Sputtern ist eine Schlüsseltechnik der physikalischen Gasphasenabscheidung (PVD), mit der dünne Schichten auf Substrate aufgebracht werden.Dabei wird ein Plasma erzeugt, in der Regel mit Argongas, das energiereiche Ionen und Elektronen enthält.Diese Ionen beschießen ein Zielmaterial und stoßen Atome von dessen Oberfläche ab.Die herausgeschleuderten Atome wandern dann durch das Plasma und lagern sich auf einem Substrat ab, wobei sie eine dünne, gleichmäßige Schicht bilden.Dieses Verfahren ist in Branchen wie der Halbleiter-, Optik- und Beschichtungsindustrie weit verbreitet, da es selbst bei relativ niedrigen Temperaturen hochwertige, dichte Schichten mit hervorragender Haftung und geringer Eigenspannung erzeugen kann.
Die wichtigsten Punkte erklärt:
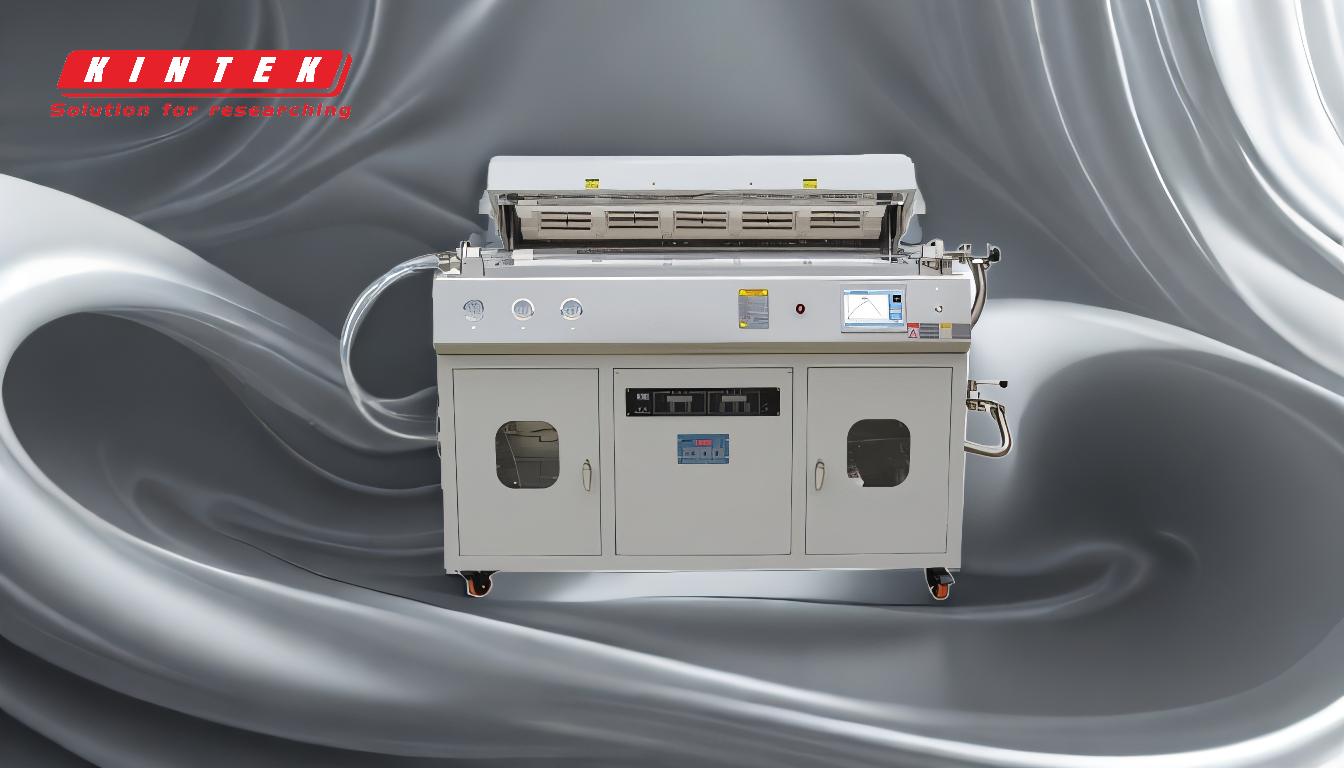
-
Definition des Sputterns:
- Beim Sputtern handelt es sich um ein Verfahren der physikalischen Gasphasenabscheidung (PVD), bei dem Atome aus der Oberfläche eines Materials (dem Target) herausgeschleudert werden, wenn dieses von hochenergetischen Teilchen, in der Regel Argon-Ionen, getroffen wird.
- Dieser Prozess findet in einer Vakuumkammer statt, in die ein kontrolliertes Gas (normalerweise Argon) eingeleitet und ionisiert wird, um ein Plasma zu erzeugen.
-
Die Rolle des Plasmas:
- Das Plasma ist eine Schlüsselkomponente des Sputterns.Es wird durch die elektrische Erregung einer Kathode in der Vakuumkammer erzeugt, wodurch ein sich selbst erhaltendes Plasma entsteht.
- Das Plasma enthält Argon-Ionen und Elektronen, die aufgrund des elektrischen Feldes auf das Zielmaterial beschleunigt werden.
-
Ionenbeschuss und Ausstoß von Atomen:
- Die Argon-Ionen im Plasma stoßen mit dem Targetmaterial zusammen und übertragen ihre Energie auf die Atome der Targetoberfläche.
- Wenn die Energieübertragung ausreicht, werden die Atome von der Oberfläche des Targets abgestoßen (gesputtert).Dieser Vorgang wird als physikalisches Sputtern bezeichnet.
-
Ablagerung von gesputterten Atomen:
- Die ausgestoßenen Atome wandern durch das Plasma und lagern sich auf einem in der Kammer befindlichen Substrat ab.
- Die Atome bilden eine dünne, gleichmäßige Schicht auf dem Substrat und erzeugen einen hochwertigen Dünnfilm.
-
Vorteile des Sputterns:
- Hochwertige Filme:Das Sputtern erzeugt dichte, gleichmäßige Schichten mit hervorragender Haftung auf dem Substrat.
- Niedrige Eigenspannung:Mit dem Verfahren können geringe Eigenspannungen in den abgeschiedenen Schichten erzielt werden, was für viele Anwendungen entscheidend ist.
- Vielseitigkeit:Sputtern kann bei einer Vielzahl von Materialien eingesetzt werden, darunter Metalle, Legierungen und Keramiken.
- Niedertemperatur-Beschichtung:Die Schichten können bei Temperaturen unter 150 °C abgeschieden werden, wodurch sie sich für temperaturempfindliche Substrate eignen.
-
Anwendungen des Sputterns:
- Halbleiter:Für die Abscheidung dünner Schichten in integrierten Schaltkreisen und anderen elektronischen Komponenten.
- Optik:Wird bei der Herstellung von Antireflexionsbeschichtungen, Spiegeln und optischen Filtern verwendet.
- Beschichtungen:Wird für verschleißfeste, dekorative und schützende Beschichtungen auf verschiedenen Materialien verwendet.
- Magnetische Lagerung:Wird bei der Herstellung von magnetischen Dünnschichten für Datenspeichergeräte verwendet.
-
Prozesskontrolle und Parameter:
- Gasdruck:Der Druck des Argongases in der Kammer beeinflusst die Sputterrate und die Schichtqualität.
- Stromzufuhr:Die an die Kathode angelegte Leistung beeinflusst die Energie der Ionen und die Geschwindigkeit der Zerstäubung.
- Target-Material:Die Wahl des Zielmaterials bestimmt die Zusammensetzung der abgeschiedenen Schicht.
- Temperatur des Substrats:Während das Sputtern bei niedrigen Temperaturen durchgeführt werden kann, kann die Steuerung der Substrattemperatur die Schichteigenschaften beeinflussen.
-
Vergleich mit anderen PVD-Techniken:
- Das Sputtern wird oft mit dem Verdampfen, einer anderen PVD-Technik, verglichen.Während beim Verdampfen das Zielmaterial erhitzt wird, um einen Dampf zu erzeugen, beruht das Sputtern auf dem Beschuss mit Ionen.
- Beim Sputtern werden in der Regel Schichten mit besserer Haftung und Gleichmäßigkeit als beim Verdampfen erzeugt, weshalb es für viele Anwendungen die bevorzugte Methode ist.
Wenn die Käufer von Anlagen und Verbrauchsmaterialien diese wichtigen Punkte kennen, können sie fundierte Entscheidungen über den Einsatz des Sputterns in ihren Verfahren treffen und so eine optimale Leistung und Kosteneffizienz gewährleisten.
Zusammenfassende Tabelle:
Hauptaspekt | Einzelheiten |
---|---|
Definition | Sputtern ist ein PVD-Verfahren, bei dem Atome durch Ionenbeschuss aus einem Zielmaterial herausgeschleudert werden. |
Die Rolle des Plasmas | Das mit Argongas erzeugte Plasma enthält Ionen, die das Ziel beschießen. |
Vorteile | Hochwertige Schichten, geringe Eigenspannung, Vielseitigkeit, Abscheidung bei niedrigen Temperaturen. |
Anwendungen | Halbleiter, Optik, Beschichtungen, Magnetspeicher. |
Prozess-Parameter | Gasdruck, Stromzufuhr, Zielmaterial, Substrattemperatur. |
Vergleich zur Verdampfung | Sputtern bietet eine bessere Haftung und Gleichmäßigkeit als Verdampfen. |
Entdecken Sie, wie das Sputtern Ihre Dünnschichtprozesse verbessern kann. Kontaktieren Sie unsere Experten noch heute !