CVD (Chemical Vapour Deposition) und PVD (Physical Vapour Deposition) sind zwei weit verbreitete Beschichtungstechniken für Einsätze mit jeweils unterschiedlichen Prozessen, Eigenschaften und Anwendungen. CVD umfasst chemische Reaktionen bei hohen Temperaturen und erzeugt dichte, gleichmäßige Beschichtungen, die für Hochtemperatur- und verschleißfeste Anwendungen geeignet sind. PVD hingegen nutzt physikalische Prozesse im Vakuum bei niedrigeren Temperaturen, was zu dünneren, weniger dichten Beschichtungen mit ausgezeichneter Haftung und Oberflächenbeschaffenheit führt. Die Wahl zwischen CVD und PVD hängt von Faktoren wie Materialkompatibilität, Anwendungsanforderungen und Betriebsbedingungen ab.
Wichtige Punkte erklärt:
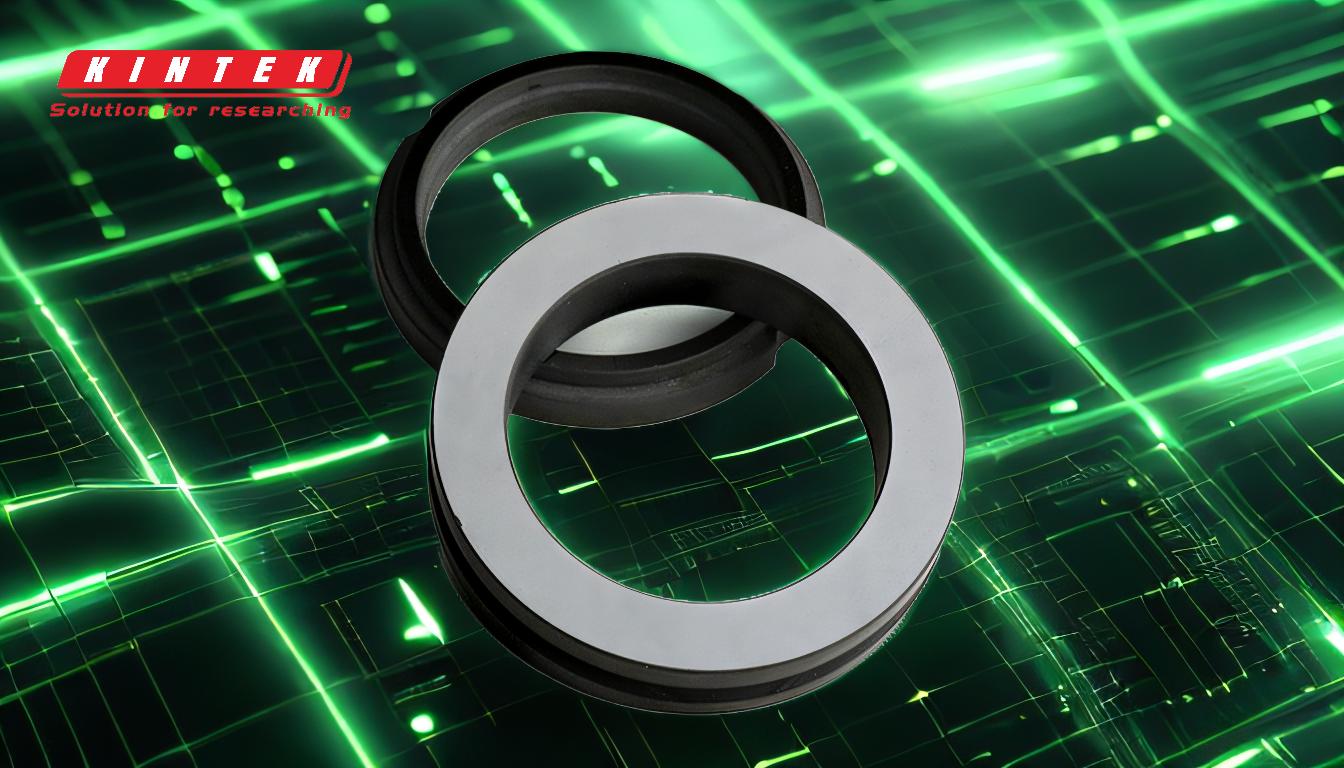
-
Ablagerungsmechanismus:
- CVD: Verwendet chemische Reaktionen zwischen gasförmigen Vorläufern und dem Substrat, um eine feste Beschichtung zu bilden. Der Prozess ist multidirektional und ermöglicht eine gleichmäßige Abdeckung auch komplexer Geometrien.
- PVD: Verlässt sich auf physikalische Prozesse wie Sputtern oder Verdampfen, um Material auf dem Substrat abzuscheiden. Es handelt sich um einen Sichtlinienprozess, das heißt, es werden nur Oberflächen beschichtet, die direkt der Quelle ausgesetzt sind.
-
Betriebstemperaturen:
- CVD: Arbeitet bei hohen Temperaturen (450°C bis 1050°C), was zu Zugspannungen und feinen Rissen in der Beschichtung führen kann. Dadurch ist es für Hochtemperaturanwendungen geeignet.
- PVD: Funktioniert bei niedrigeren Temperaturen (250 °C bis 450 °C), reduziert die thermische Belastung und macht es für temperaturempfindliche Substrate geeignet.
-
Beschichtungsmaterialien:
- CVD: Aufgrund der chemischen Natur des Prozesses normalerweise auf Keramik und Polymere beschränkt.
- PVD: Kann ein breiteres Spektrum an Materialien, einschließlich Metallen, Legierungen und Keramiken, auftragen und bietet so eine größere Vielseitigkeit.
-
Beschichtungseigenschaften:
- CVD: Erzeugt dichtere und gleichmäßigere Beschichtungen, ideal für Anwendungen, die eine hohe Verschleißfestigkeit und thermische Stabilität erfordern.
- PVD: Ergibt weniger dichte und weniger gleichmäßige Beschichtungen, bietet jedoch eine bessere Haftung und Oberflächenbeschaffenheit und eignet sich daher für Präzisionsanwendungen.
-
Auftragsgeschwindigkeit und -stärke:
- CVD: Das Auftragen dauert aufgrund des chemischen Reaktionsprozesses länger, kann jedoch zu dickeren Beschichtungen führen (10–20 μm).
- PVD: Lässt sich schneller auftragen, führt jedoch typischerweise zu dünneren Beschichtungen (3–5 μm), die für viele Präzisionsanwendungen ausreichend sind.
-
Stress und Rissbildung:
- CVD: Hohe Verarbeitungstemperaturen können zu Zugspannungen und feinen Rissen führen, die die Haltbarkeit der Beschichtung beeinträchtigen können.
- PVD: Bildet beim Abkühlen eine Druckspannung, wodurch die Wahrscheinlichkeit von Rissen verringert und die Haltbarkeit der Beschichtung verbessert wird.
-
Anwendungen:
- CVD: Wird häufig in Hochtemperatur- und verschleißfesten Anwendungen verwendet, z. B. bei Schneidwerkzeugen und Komponenten für die Luft- und Raumfahrt.
- PVD: Bevorzugt für Anwendungen, die eine hervorragende Oberflächenbeschaffenheit und Haftung erfordern, wie z. B. medizinische Geräte und Präzisionsbearbeitungswerkzeuge.
Das Verständnis dieser Unterschiede hilft bei der Auswahl der geeigneten Beschichtungsmethode basierend auf den spezifischen Anforderungen der Anwendung.
Übersichtstabelle:
Aspekt | CVD | PVD |
---|---|---|
Ablagerungsmechanismus | Chemische Reaktionen, multidirektionale Abdeckung | Physikalische Prozesse, Sichtlinienabdeckung |
Betriebstemperatur | Hoch (450 °C bis 1050 °C), geeignet für Hochtemperaturanwendungen | Niedriger (250 °C bis 450 °C), ideal für temperaturempfindliche Untergründe |
Beschichtungsmaterialien | Beschränkt auf Keramik und Polymere | Breites Sortiment, einschließlich Metalle, Legierungen und Keramik |
Beschichtungseigenschaften | Dicht, gleichmäßig, hohe Verschleißfestigkeit, thermische Stabilität | Dünner, weniger dicht, bessere Haftung, hervorragende Oberflächenbeschaffenheit |
Anwendungsgeschwindigkeit | Langsamere, dickere Beschichtungen (10–20 μm) | Schnellere, dünnere Beschichtungen (3–5 μm) |
Stress und Rissbildung | Zugbeanspruchung, feine Risse möglich | Druckspannung, reduzierte Rissbildung |
Anwendungen | Hochtemperaturbeständig, verschleißfest (z. B. Schneidwerkzeuge, Luft- und Raumfahrt) | Präzisionsanwendungen (z. B. medizinische Geräte, Bearbeitungswerkzeuge) |
Sie sind sich immer noch nicht sicher, welche Beschichtung für Ihre Einsätze die richtige ist? Kontaktieren Sie noch heute unsere Experten für persönliche Beratung!