Die Sintertemperatur spielt eine entscheidende Rolle bei der Bestimmung der endgültigen Eigenschaften von Keramiken, einschließlich Festigkeit, Härte, chemischer Stabilität und Gefüge. Um optimale Ergebnisse zu erzielen, ist eine präzise Steuerung der Sintertemperatur unerlässlich, da Abweichungen zu Problemen wie übermäßigem Kornwachstum, geringerer Festigkeit oder beeinträchtigter Maßgenauigkeit führen können. Zirkoniumdioxidkeramiken weisen beispielsweise eine maximale Festigkeit auf, wenn sie bei etwa 1500 °C gesintert werden, wobei selbst kleine Abweichungen (z. B. ±150 °C) die Leistung erheblich beeinträchtigen. Der Sinterprozess beinhaltet Diffusionsmechanismen, die stark temperaturabhängig sind. Daher ist eine konsequente Temperaturkontrolle während der Aufheiz-, Halte- und Abkühlungsphasen von entscheidender Bedeutung für die Herstellung hochwertiger Keramiken mit gleichmäßigem Gefüge und gewünschten mechanischen Eigenschaften.
Die wichtigsten Punkte werden erklärt:
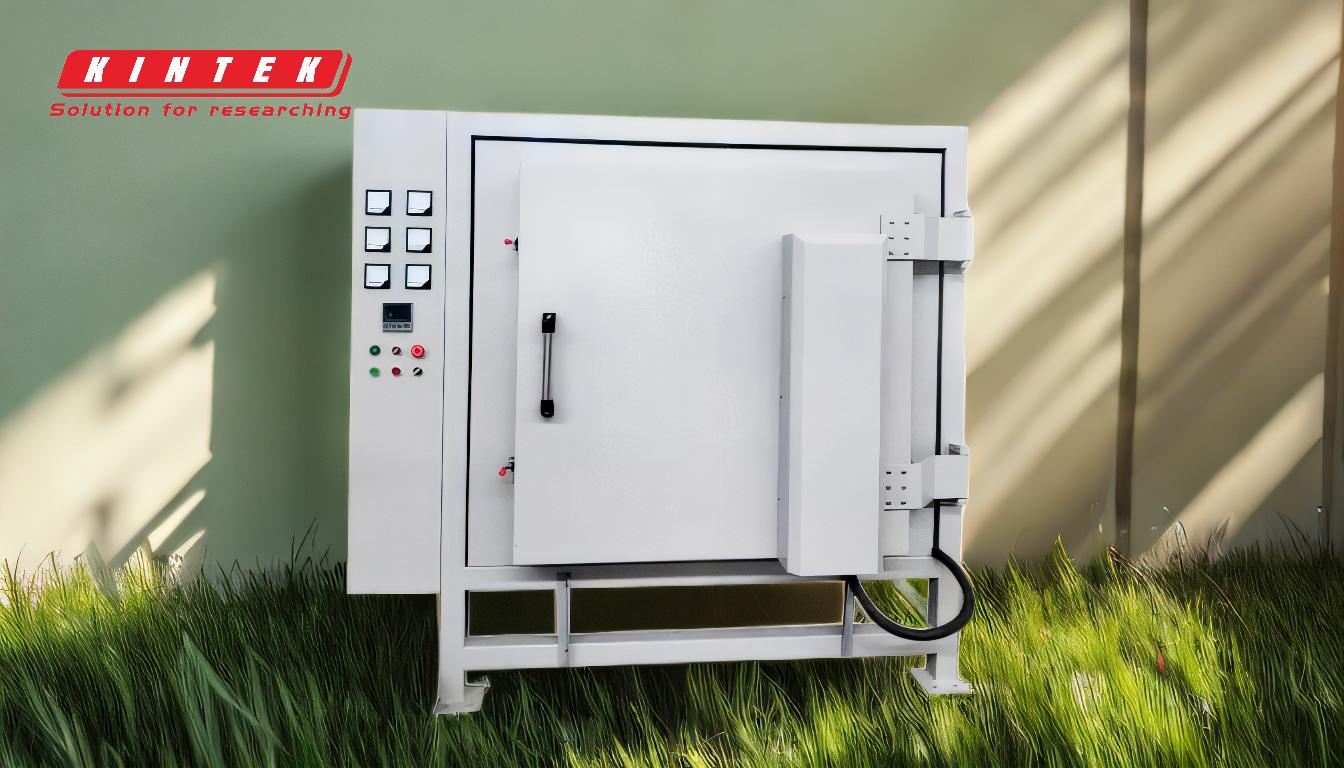
-
Die Bedeutung der Sintertemperatur
- Beim Sintern wird keramisches Pulver durch Diffusion und Stoffübertragung in ein dichtes, polykristallines Material umgewandelt.
- Die Temperatur hat einen direkten Einfluss auf die Korngrenzendiffusion und die Massendiffusion, die für das Erreichen einer Verdichtung und eines gleichmäßigen Gefüges entscheidend sind.
- Die richtige Sintertemperatur gewährleistet die Festigkeit, Härte, chemische Stabilität und Maßhaltigkeit der Keramik.
-
Optimale Sintertemperatur für Zirkoniumdioxid
- Studien zeigen, dass das Sintern von Zirkoniumdioxid bei ca. 1500°C seine Festigkeit maximiert.
- Abweichungen von ±150°C von dieser Temperatur können zu Kornwachstum führen und die Festigkeit des Materials verringern.
- Höhere Temperaturen (z. B. über 1500 °C) führen zu erheblichen Festigkeitseinbußen aufgrund einer übermäßigen Kornvergröberung.
-
Einfluss der Temperatur auf das Gefüge
- Die Sintertemperatur steuert die Korngröße und -verteilung, die für die mechanischen Eigenschaften entscheidend sind.
- Zu hohe Temperaturen können ein schnelles Kornwachstum verursachen, was zu einem ungleichmäßigen Gefüge und geringerer Zähigkeit führt.
- Durch eine präzise Temperatursteuerung (z. B. nicht über 1450 °C bei Hartmetallen) bleiben kleine Korngrößen erhalten, was die Härte und Verschleißfestigkeit erhöht.
-
Temperaturkontrolle während der Sinterphasen
- Die Anstiegsgeschwindigkeit von 900 °C auf die Höchsttemperatur, die Temperaturkonstanz während der Haltephase und die Abkühlgeschwindigkeit zurück auf 900 °C sind entscheidend für optimale Ergebnisse.
- Eine uneinheitliche Temperaturkontrolle während dieser Phasen kann zu Defekten wie Verformung, Rissbildung oder ungleichmäßiger Verdichtung führen.
-
Anwendungen in der Dentalkeramik
- Bei Zahnkronen, Verblendungen und Implantaten aus Zirkoniumdioxid wirkt sich die Sintertemperatur direkt auf Farbe, Größe und Festigkeit aus.
- Die richtige Temperaturkontrolle gewährleistet, dass die feinen Details und die Verarbeitung erhalten bleiben und die ästhetische und funktionale Qualität des Endprodukts gewahrt wird.
-
Wirtschaftliche und produktionstechnische Vorteile
- Das Sintern ermöglicht die Herstellung komplexer Formen und Geometrien, die mit herkömmlichen Fertigungsmethoden nur schwer zu erreichen sind.
- Sie ermöglicht eine kostengünstigere Werkzeugherstellung und eine schnelle Massenproduktion bei gleichbleibender Präzision und Wiederholbarkeit.
- Die Kombination mehrerer Materialien durch Sintern kann Eigenschaften wie Zähigkeit und Abriebfestigkeit verbessern.
-
Herausforderungen und Überlegungen
- Um eine präzise Temperaturkontrolle zu erreichen, sind moderne Geräte und Überwachungssysteme erforderlich.
- Auch die Sinterumgebung (z. B. Atmosphäre, Druck) und die Materialzusammensetzung (z. B. Partikelgröße, Verteilung) beeinflussen das Ergebnis.
- Temperaturschwankungen können die Leistung der Keramik beeinträchtigen, weshalb eine Prozessoptimierung unerlässlich ist.
Zusammenfassend lässt sich sagen, dass die Sintertemperatur ein entscheidender Faktor bei der Keramikherstellung ist, da sie das Mikrogefüge, die mechanischen Eigenschaften und die Qualität des Endprodukts beeinflusst. Eine präzise Steuerung der Temperatur während aller Phasen des Sinterns ist unerlässlich, um die gewünschten Eigenschaften zu erzielen und eine gleichbleibende Qualität bei modernen Keramikanwendungen zu gewährleisten.
Zusammenfassende Tabelle:
Hauptaspekt | Einzelheiten |
---|---|
Die Bedeutung der Sintertemperatur | Beeinflusst die Korngrenzendiffusion, die Verdichtung und das Gefüge. |
Optimale Sinterung für Zirkoniumdioxid | ~1500°C maximiert die Festigkeit; Abweichungen von ±150°C verringern die Leistung. |
Auswirkungen auf die Mikrostruktur | Kontrolliert die Korngröße; zu hohe Temperaturen verursachen ungleichmäßige Strukturen. |
Phasen der Temperaturkontrolle | Die Rampenrate, die Haltephase und die Abkühlungsrate sind entscheidend für konsistente Ergebnisse. |
Anwendungen in der Dentalkeramik | Beeinflusst Farbe, Größe und Festigkeit von Zahnkronen und Implantaten. |
Wirtschaftlicher Nutzen | Ermöglicht komplexe Formen, kostengünstigere Werkzeuge und eine schnelle Massenproduktion. |
Herausforderungen | Dies erfordert eine fortschrittliche Ausrüstung und eine genaue Überwachung, um Fehler zu vermeiden. |
Erzielen Sie optimale Keramikeigenschaften durch präzise Steuerung der Sintertemperatur kontaktieren Sie unsere Experten noch heute !