Die Sintertemperatur von Zirkoniumdioxid hat erhebliche Auswirkungen auf seine Mikrostruktur und seine Eigenschaften.Die optimale Sintertemperatur liegt bei etwa 1500 °C und maximiert die Festigkeit und Stabilität.Abweichungen von 150℃ über oder unter dieser Temperatur können zu Kornwachstum, verminderter Festigkeit und anderen nachteiligen Auswirkungen wie Rissbildung, unkontrollierter Umwandlung und verminderter Transluzenz führen.Die Einhaltung des vom Hersteller empfohlenen Sinterplans ist entscheidend für das Erreichen der gewünschten physikalischen, mechanischen und ästhetischen Eigenschaften von Zirkoniumdioxid.
Die wichtigsten Punkte werden erklärt:
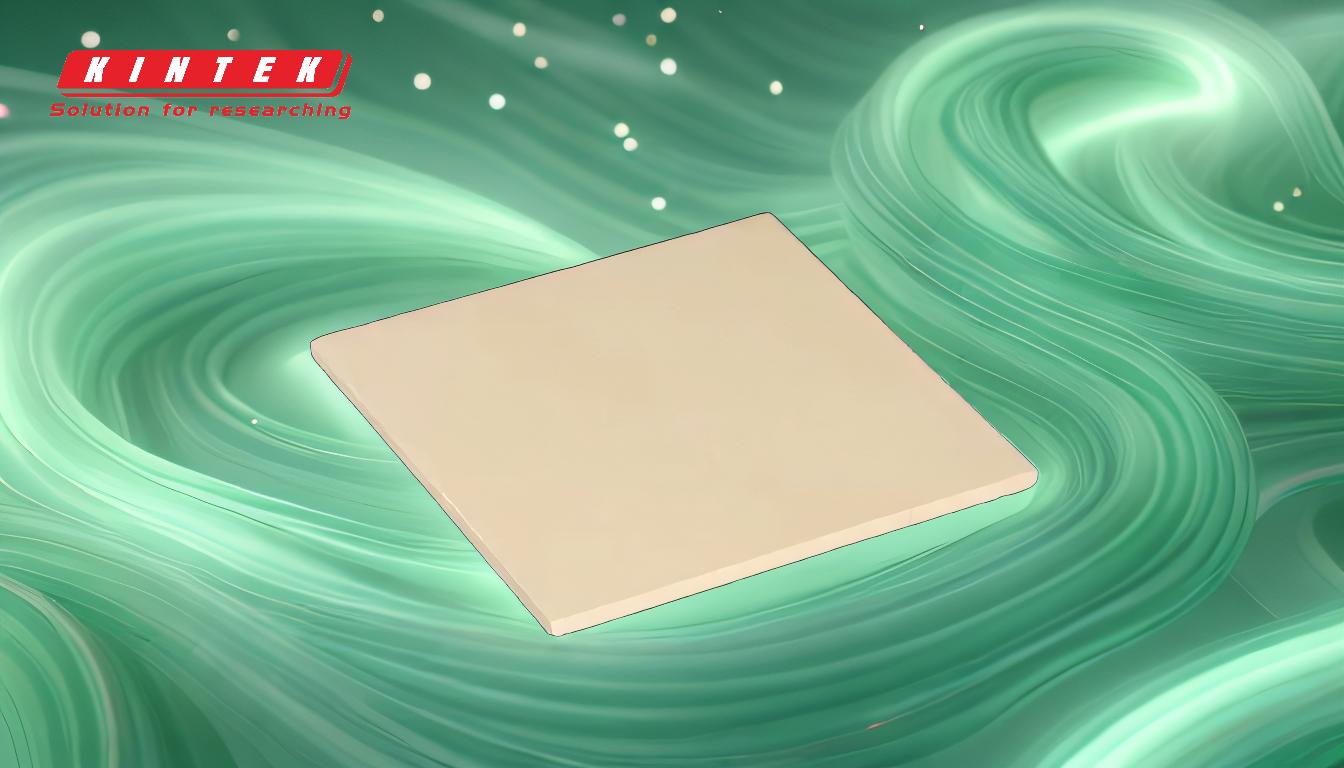
-
Optimale Sintertemperatur:
- 1500℃:Jüngste Studien zeigen, dass das Sintern von Zirkoniumdioxid bei etwa 1500℃ seine Festigkeit maximiert.Diese Temperatur wird als optimal angesehen, um ein Gleichgewicht zwischen mechanischen Eigenschaften und Stabilität zu erreichen.
- Abweichung Effekte:Eine Abweichung von nur 150℃ über oder unter dieser Temperatur kann die Festigkeit von Zirkoniumdioxid erheblich verringern.Diese Verringerung ist in erster Linie auf das Kornwachstum zurückzuführen, das sich negativ auf die strukturelle Integrität des Materials auswirkt.
-
Mikrostrukturelle Veränderungen:
- Korngröße und Porengröße:Der Sinterprozess wirkt sich direkt auf die Korngröße und die Porengröße im Zirkoniumdioxid-Mikrogefüge aus.Optimale Sinterbedingungen führen zu einer feinen und gleichmäßigen Kornstruktur, die die Festigkeit und Haltbarkeit des Materials erhöht.
- Form und Verteilung der Korngrenzen:Eine ordnungsgemäße Sinterung beeinflusst auch die Form und Verteilung der Korngrenzen.Gut definierte Korngrenzen tragen zur allgemeinen Stabilität und mechanischen Leistungsfähigkeit von Zirkoniumdioxid bei.
-
Nachteilige Auswirkungen von hohen Temperaturen:
- Verminderte Stabilität:Das Sintern bei zu hohen Temperaturen kann die Stabilität von Zirkoniumdioxid beeinträchtigen und es anfälliger für unkontrollierte Phasenumwandlungen machen.
- Unkontrollierte Umwandlung:Hohe Temperaturen können unkontrollierte Umwandlungen im Zirkoniumdioxidgefüge hervorrufen, die zu Defekten und Leistungseinbußen führen.
- Rissbildung:Zu hohe Sintertemperaturen erhöhen das Risiko der Rissbildung, was die Integrität und Langlebigkeit des Materials stark beeinträchtigen kann.
- Reduzierte Transluzenz:Hohe Sintertemperaturen können auch die Transluzenz von Zirkoniumdioxid vermindern, was seine ästhetischen Eigenschaften beeinträchtigt.Dies ist besonders wichtig bei Anwendungen, bei denen das Aussehen ein entscheidender Faktor ist.
-
Bedeutung der Herstellerempfehlungen:
- Zeitplan für den Abschuss:Die Einhaltung des vom Hersteller empfohlenen Brennplans ist für das Erreichen der idealen physikalischen, mechanischen und ästhetischen Eigenschaften von Zirkoniumdioxid unerlässlich.Dieser Zeitplan soll den Sinterungsprozess optimieren und eine gleichbleibende Qualität gewährleisten.
- Konsistenz und Qualität:Die Einhaltung der empfohlenen Sinterparameter trägt dazu bei, die Eigenschaften des Materials konstant zu halten und qualitativ hochwertige Ergebnisse zu erzielen.Abweichungen von diesen Richtlinien können zu suboptimalen Ergebnissen und möglichen Fehlern in der Anwendung führen.
Zusammenfassend lässt sich sagen, dass die Sintertemperatur von Zirkoniumdioxid ein entscheidender Faktor ist, der das Mikrogefüge und die Eigenschaften des Materials beeinflusst.Eine optimale Sinterung bei etwa 1500℃ gewährleistet maximale Festigkeit und Stabilität, während Abweichungen zu nachteiligen Auswirkungen wie Kornwachstum, Rissbildung und verminderter Transluzenz führen können.Die Einhaltung des vom Hersteller empfohlenen Sinterzeitplans ist für die Erzielung der gewünschten Leistung und Ästhetik von Zirkoniumdioxidprodukten unerlässlich.
Zusammenfassende Tabelle:
Hauptaspekt | Einzelheiten |
---|---|
Optimale Sintertemperatur | 1500℃ maximiert die Festigkeit und Stabilität. |
Abweichung Effekte | ±150℃ kann zu Kornwachstum, verminderter Festigkeit, Rissbildung und schlechter Ästhetik führen. |
Mikrostrukturelle Veränderungen | Feines Korngefüge, gleichmäßige Poren und gut definierte Korngrenzen. |
Nachteilige Auswirkungen von hohen Temperaturen | Unkontrollierte Umwandlungen, Rissbildung und verminderte Lichtdurchlässigkeit. |
Empfehlungen des Herstellers | Befolgen Sie die empfohlenen Brenntermine, um eine gleichbleibende Qualität und Leistung zu gewährleisten. |
Stellen Sie sicher, dass Ihr Zirkoniumdioxid eine optimale Festigkeit und Ästhetik erreicht. Kontaktieren Sie noch heute unsere Experten für Beratung!