Reaktives Sputtern ist ein spezielles Verfahren zur Abscheidung von Dünnschichten, das zur Herstellung von Verbundschichten mit präzisen chemischen Zusammensetzungen und Eigenschaften eingesetzt wird.Dabei wird ein reaktives Gas, z. B. Sauerstoff oder Stickstoff, in eine Sputterkammer eingeleitet, wo es mit dem vom Plasma ausgestoßenen Zielmaterial reagiert.Dieses Verfahren ermöglicht die Bildung von Verbindungen wie Oxiden, Nitriden oder Karbiden direkt auf dem Substrat.Der Hauptzweck des reaktiven Sputterns besteht darin, qualitativ hochwertige, gleichmäßige dünne Schichten mit kontrollierter Stöchiometrie und verbesserten Eigenschaften wie Härte, Korrosionsbeständigkeit oder optischen Merkmalen in einer schnelleren Geschwindigkeit als bei herkömmlichen Sputterverfahren herzustellen.Dies macht es ideal für Anwendungen in der Halbleiterherstellung, für optische Beschichtungen und schützende Barriereschichten.
Die wichtigsten Punkte erklärt:
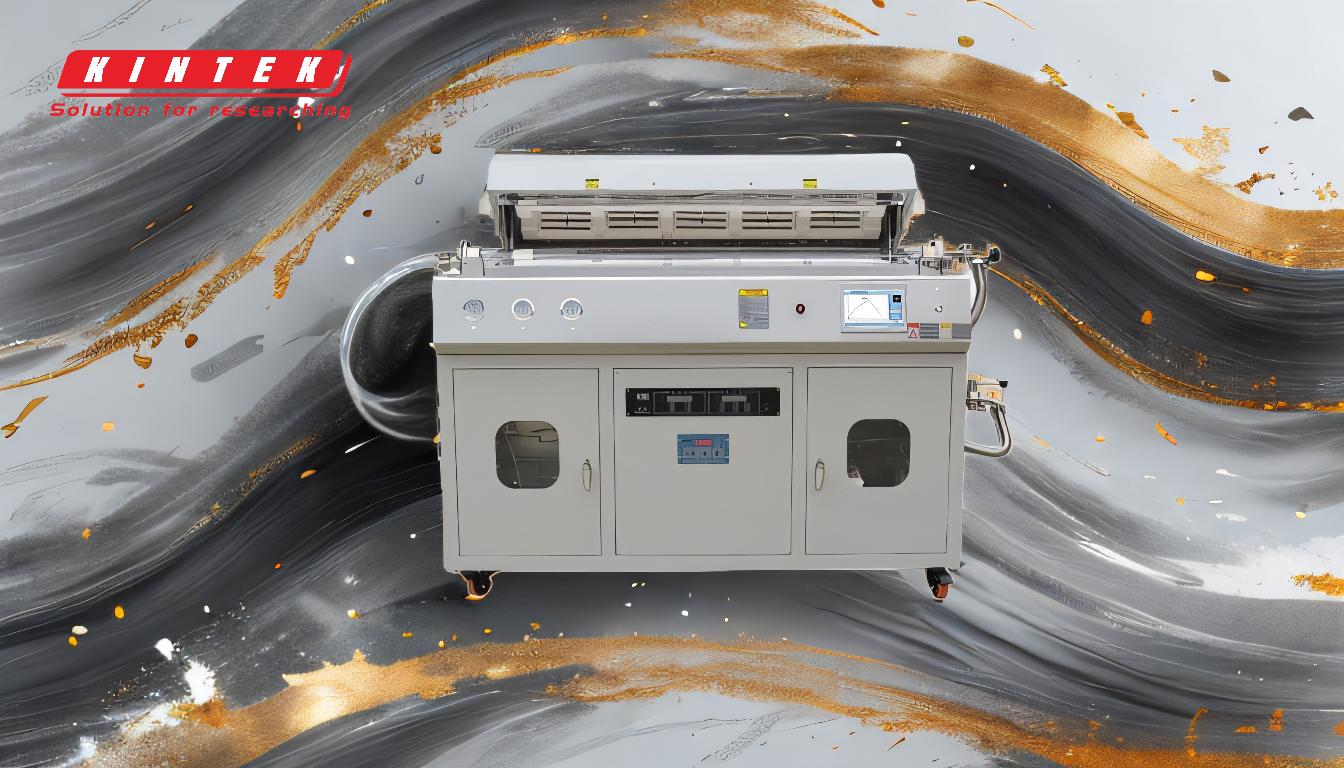
-
Bildung von Verbundfilmen:
- Beim reaktiven Sputtern werden dünne Schichten aus Verbindungen wie Oxiden, Nitriden oder Karbiden erzeugt, indem reaktive Gase wie Sauerstoff oder Stickstoff in die Sputterkammer eingeleitet werden.
- Beispiel:Aluminium (Al) reagiert mit Sauerstoff (O₂) zu Aluminiumoxid (Al₂O₃), das als dünner Film auf dem Substrat abgeschieden wird.
- Mit diesem Verfahren lassen sich die Zusammensetzung und die Eigenschaften des Films genau steuern, was für Anwendungen wie Sperrschichten oder optische Beschichtungen von entscheidender Bedeutung ist.
-
Verbesserte Abscheiderate:
- Durch reaktives Sputtern wird die Abscheidungsgeschwindigkeit von Verbundschichten im Vergleich zu herkömmlichen Sputterverfahren erheblich gesteigert.
- Indem chemische Reaktionen während des Abscheidungsprozesses erzwungen werden, verbinden sich die Materialien effizienter, was zu einer schnelleren Filmbildung führt.
- Dies ist besonders vorteilhaft für industrielle Anwendungen, bei denen ein hoher Durchsatz erforderlich ist.
-
Präzision in Filmzusammensetzung und Struktur:
- Die Einführung reaktiver Gase ermöglicht die Herstellung von Schichten mit genau regulierter Stöchiometrie und Struktur.
- Dies ist wesentlich für Anwendungen in der physikalischen Gasphasenabscheidung (PVD), wo bestimmte Materialeigenschaften wie Härte, Korrosionsbeständigkeit oder optische Transparenz erforderlich sind.
- Beispiel:Titannitridschichten (TiN), die für ihre Härte und Verschleißfestigkeit bekannt sind, werden in der Regel durch reaktives Sputtern hergestellt.
-
Vielseitigkeit bei der Materialauswahl:
- Das reaktive Sputtern kann mit einer breiten Palette von Targetmaterialien und reaktiven Gasen eingesetzt werden und ermöglicht die Abscheidung verschiedener Verbundschichten.
- Zu den gängigen Reaktivgasen gehören Sauerstoff (für Oxide), Stickstoff (für Nitride) und Acetylen (für Karbide).
- Dank dieser Vielseitigkeit eignet sich das Verfahren für verschiedene Branchen, darunter Elektronik, Optik und Beschichtungen.
-
Anwendungen in fortgeschrittenen Technologien:
- Das reaktive Sputtern wird in der Halbleiterherstellung häufig zur Herstellung von Sperrschichten wie Titannitrid (TiN) verwendet, die die Diffusion zwischen den Schichten verhindern.
- Es wird auch bei optischen Beschichtungen eingesetzt, um Schichten mit bestimmten Brechungsindizes oder Antireflexionseigenschaften herzustellen.
- Außerdem werden Schutzschichten aufgebracht, die die Haltbarkeit und Leistung von Werkzeugen und Bauteilen verbessern.
-
Vergleich zum traditionellen Sputtern:
- Im Gegensatz zum herkömmlichen Sputtern, bei dem hauptsächlich reine Metalle oder Legierungen abgeschieden werden, ermöglicht das reaktive Sputtern die direkte Abscheidung von Verbundschichten.
- Das herkömmliche Sputtern ist für Verbundschichten langsamer, da es zusätzliche Schritte erfordert, um die gewünschte chemische Zusammensetzung zu erreichen.
- Das reaktive Sputtern vereinfacht den Prozess, indem die chemische Reaktion in den Abscheidungsschritt integriert wird.
-
Optimierung der Prozessparameter:
- Der Erfolg des reaktiven Sputterns hängt von der sorgfältigen Kontrolle von Parametern wie Gasdurchsatz, Druck und Leistungsaufnahme ab.
- Eine ordnungsgemäße Optimierung gewährleistet eine gleichmäßige Schichtabscheidung und verhindert Probleme wie die Targetvergiftung, bei der das reaktive Gas eine Verbindungsschicht auf der Targetoberfläche bildet, die die Sputtereffizienz verringert.
Durch die Nutzung dieser Schlüsselaspekte bietet das reaktive Sputtern eine hocheffiziente und vielseitige Methode zur Herstellung fortschrittlicher Dünnschichten mit maßgeschneiderten Eigenschaften, was sie für die moderne Fertigung und Technologieentwicklung unverzichtbar macht.
Zusammenfassende Tabelle:
Hauptaspekt | Einzelheiten |
---|---|
Bildung von Verbundschichten | Erzeugt Oxide, Nitride oder Karbide unter Verwendung reaktiver Gase wie O₂ oder N₂. |
Verbesserte Abscheidungsrate | Schnellere Filmbildung im Vergleich zu herkömmlichen Sputtering-Verfahren. |
Präzision in der Zusammensetzung | Ermöglicht kontrollierte Stöchiometrie und maßgeschneiderte Materialeigenschaften. |
Vielseitigkeit | Arbeitet mit verschiedenen Zielmaterialien und Gasen für unterschiedliche Anwendungen. |
Anwendungen | Verwendung in Halbleitern, optischen Beschichtungen und schützenden Barriereschichten. |
Vergleich zu herkömmlichen Verfahren | Direkte Ablagerung von Verbundfolien, wodurch der Prozess vereinfacht wird. |
Optimierung | Erfordert die Steuerung von Gasfluss, Druck und Leistung für eine gleichmäßige Abscheidung. |
Sind Sie daran interessiert, reaktives Sputtern für Ihre Projekte zu nutzen? Kontaktieren Sie noch heute unsere Experten um mehr zu erfahren!