Die Sintertemperatur von Zirkonoxidkeramik liegt in der Regel zwischen 1400°C und 1600°C, wobei der optimale Bereich bei 1500°C bis 1550°C liegt. Dieser Temperaturbereich gewährleistet, dass das Material die gewünschte Härte, Dichte und Festigkeit erreicht. Höhere Temperaturen können zu übermäßigem Kornwachstum führen und die Festigkeit verringern, während niedrigere Temperaturen das Material möglicherweise nicht vollständig verdichten. Die Umwandlung von der monoklinen in die polytetragonale Struktur findet bei etwa 1100°C bis 1200°C statt, aber für die vollständige Sinterung sind höhere Temperaturen erforderlich, um die theoretisch maximale Dichte zu erreichen. Insbesondere zahnmedizinisches Zirkoniumdioxid wird häufig bei etwa 1550 °C gesintert, um ideale physikalische, mechanische und ästhetische Eigenschaften zu erreichen.
Die wichtigsten Punkte werden erklärt:
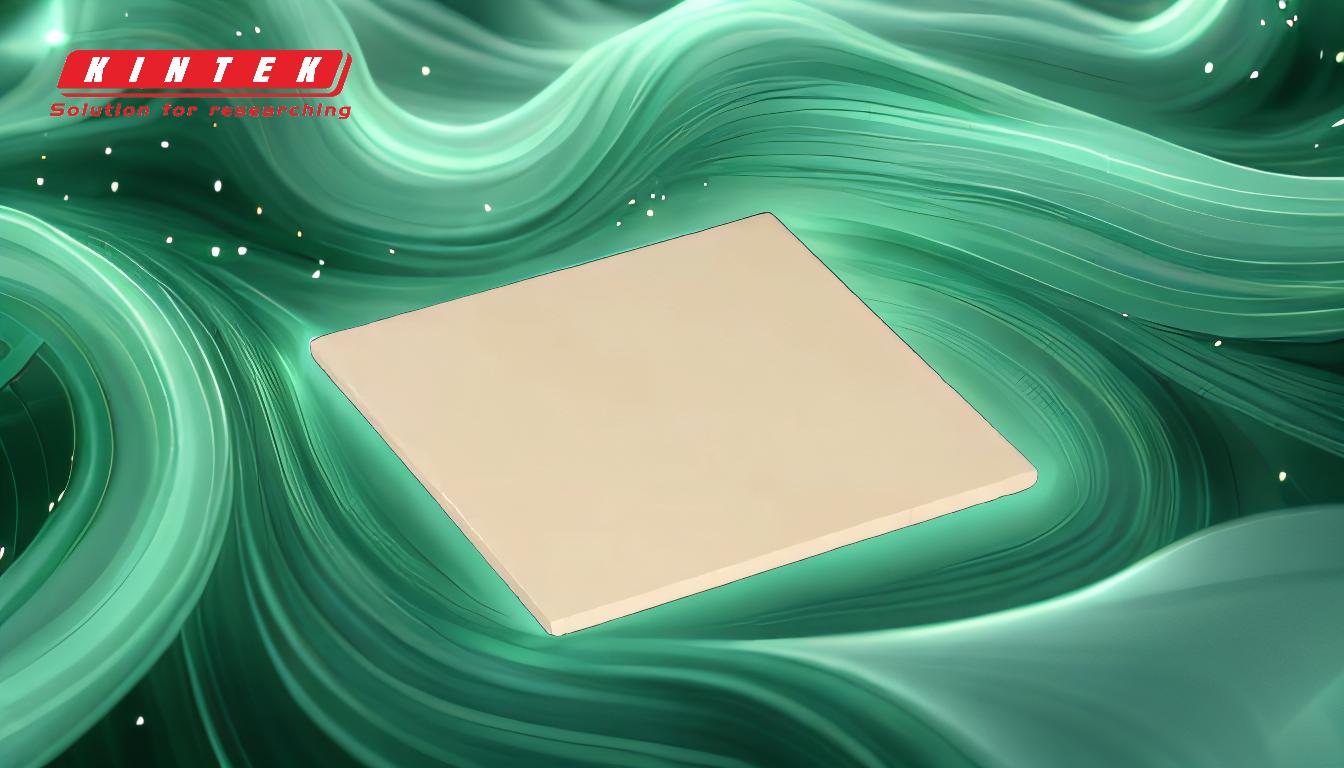
-
Sintertemperaturbereich:
- Zirkoniumdioxid-Keramik wird bei hohen Temperaturen gesintert, die zwischen 1400°C und 1600°C .
- Dieser Bereich ist notwendig, um die gewünschte Härte, Dichte und Festigkeit des Endprodukts zu erreichen.
-
Optimale Sintertemperatur:
- Die optimale Sintertemperatur für die meisten Zirkoniumdioxid-Materialien ist 1500°C bis 1550°C .
- In diesem Temperaturbereich erreicht Zirkoniumdioxid nahezu die theoretische maximale Dichte (nahezu 99 %) und optimale mechanische Eigenschaften.
-
Umwandlungstemperatur:
- Die Umwandlung von der monoklinen in die polytetragonale Struktur erfolgt bei 1100°C bis 1200°C .
- Diese Umwandlung allein reicht jedoch für eine vollständige Verdichtung nicht aus, die höhere Sintertemperaturen erfordert.
-
Einfluss der Temperatur auf die Festigkeit:
- Brennen von Zirkoniumdioxid bei 1500°C bis 1550°C erzeugt maximale Stärke (etwa 1280 MPa ).
-
Abweichend von diesem Bereich durch
±150°C
kann die Festigkeit erheblich verringern:
- Unter 1600°C fällt die Stärke auf etwa 980 MPa .
- Unter 1700°C sinkt die Stärke weiter auf etwa 600 MPa .
-
Wachstum und Dichte der Körner:
- Höhere Sintertemperaturen (über 1550°C) können dazu führen, dass übermäßiges Kornwachstum was sich negativ auf die Festigkeit auswirkt.
- Niedrigere Temperaturen (unter 1500°C) können dazu führen, dass unvollständige Verdichtung dadurch werden die mechanischen Eigenschaften des Materials beeinträchtigt.
-
Zahnärztliches Sintern von Zirkoniumdioxid:
- Zahnärztliches Zirkoniumdioxid wird in der Regel gesintert bei 1550°C um das ideale Gleichgewicht zu erreichen zwischen physikalische, mechanische und ästhetische Eigenschaften .
- Dental-Sinteröfen sind für den Betrieb innerhalb der 1400°C bis 1600°C bereich, um optimale Ergebnisse zu gewährleisten.
-
Wärmeanstiegsrate:
- Die empfohlene wärmeanstiegsrate während des Sinterns ist 4°C bis 10°C pro Minute .
- Eine kontrollierte Aufheizrate ist entscheidend, um thermische Spannungen zu vermeiden und eine gleichmäßige Verdichtung zu gewährleisten.
-
Hersteller-Empfehlungen:
- Einige Hersteller empfehlen unter Umständen etwas niedrigere oder höhere Sintertemperaturen je nach dem spezifischen Zirkoniumdioxid-Material und seiner vorgesehenen Anwendung.
- Um die gewünschten Eigenschaften zu erzielen, müssen die Richtlinien des Herstellers unbedingt beachtet werden.
-
Die Bedeutung der Temperaturgenauigkeit:
- Die genauigkeit des Sinterofens ist von entscheidender Bedeutung, da selbst kleine Abweichungen vom optimalen Temperaturbereich die Leistung des Materials erheblich beeinträchtigen können.
- Die Öfen sollten kalibriert und gewartet werden, um eine gleichmäßige und präzise Temperaturregelung zu gewährleisten.
Durch das Verständnis dieser Schlüsselpunkte können Käufer und Anwender von Zirkoniumdioxid-Keramik fundierte Entscheidungen über die Sinterparameter treffen, um die gewünschten Materialeigenschaften für ihre spezifischen Anwendungen zu erzielen.
Zusammenfassende Tabelle:
Wichtige Parameter | Einzelheiten |
---|---|
Sintertemperaturbereich | 1400°C bis 1600°C |
Optimale Temperatur | 1500°C bis 1550°C (nahe dem theoretischen Maximum an Dichte und Festigkeit) |
Umwandlungstemperatur | 1100°C bis 1200°C (monoklin bis polytetragonal) |
Maximale Stärke | ~1280 MPa bei 1500°C-1550°C |
Risiko des Getreidewachstums | Über 1550°C (übermäßiges Kornwachstum verringert die Festigkeit) |
Sintern von Zirkoniumdioxid | ~1550°C für ideale physikalische, mechanische und ästhetische Eigenschaften |
Wärmeanstiegsrate | 4°C bis 10°C pro Minute (entscheidend für eine gleichmäßige Verdichtung) |
Benötigen Sie Hilfe beim Erreichen der perfekten Sintertemperatur für Ihre Zirkoniumdioxid-Keramik? Kontaktieren Sie unsere Experten noch heute für maßgeschneiderte Lösungen!