Das Sputtern ist ein weit verbreitetes Verfahren zur Abscheidung von Dünnschichten, bei dem Atome aus einem festen Zielmaterial herausgeschleudert und auf einem Substrat abgeschieden werden, um eine dünne, gleichmäßige Schicht zu bilden.Das Verfahren findet in einer Vakuumkammer statt, in der ein Inertgas, in der Regel Argon, ionisiert wird, um ein Plasma zu erzeugen.Positiv geladene Ionen aus dem Plasma werden auf ein negativ geladenes Ziel beschleunigt, wodurch Atome aus der Oberfläche des Ziels herausgeschleudert werden.Diese ausgestoßenen Atome wandern dann durch das Vakuum und lagern sich auf dem Substrat ab und bilden einen dünnen Film.Das Verfahren ist sehr gut steuerbar und ermöglicht die Herstellung von Beschichtungen mit hervorragender Haftung, Gleichmäßigkeit und Reinheit, wodurch es sich für Anwendungen in der Elektronik, Optik und für industrielle Beschichtungen eignet.
Die wichtigsten Punkte erklärt:
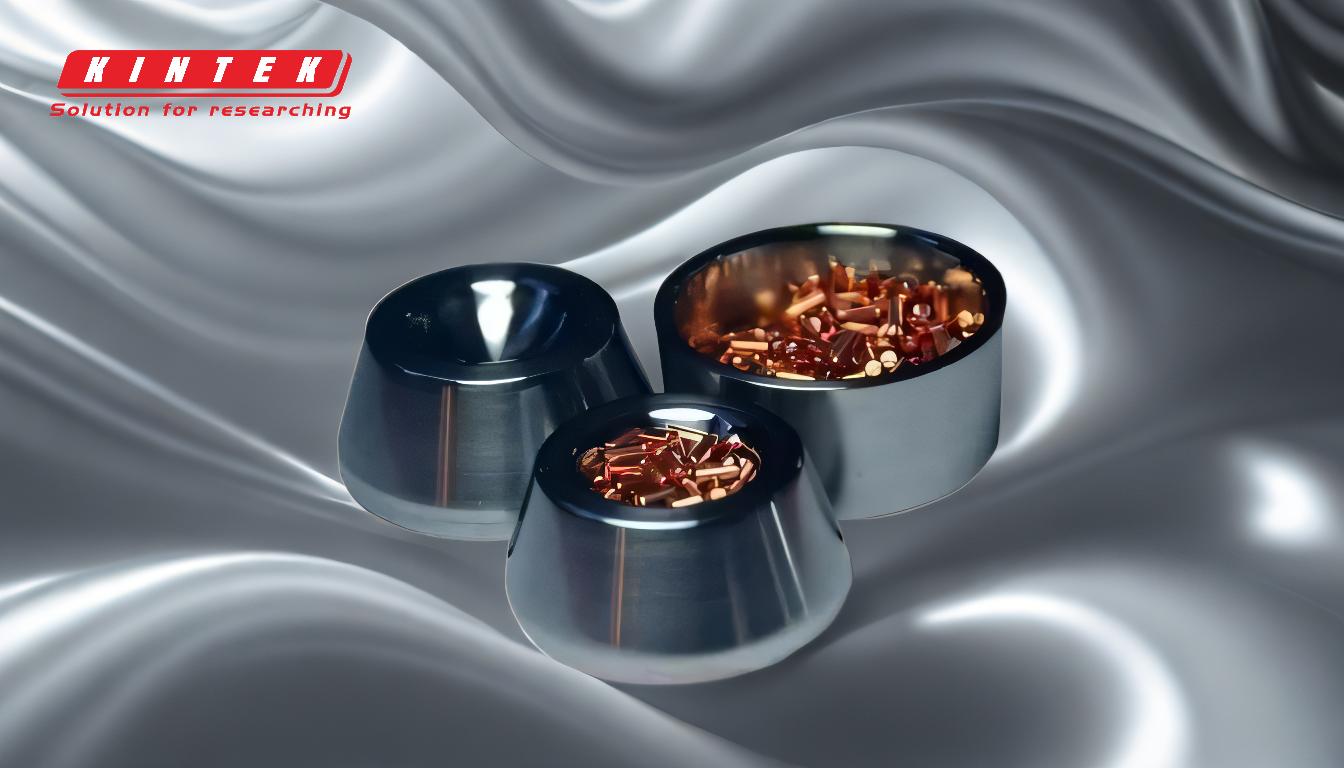
-
Aufbau der Vakuumkammer:
- Der Sputterprozess beginnt mit der Erzeugung eines Vakuums in der Reaktionskammer.Der Druck wird auf etwa 1 Pa (0,0000145 psi) reduziert, um Feuchtigkeit und Verunreinigungen zu beseitigen, die den Abscheidungsprozess stören könnten.
- Eine Vakuumumgebung sorgt dafür, dass sich die gesputterten Atome frei bewegen können, ohne mit Luftmolekülen zusammenzustoßen, die die Gleichmäßigkeit der Dünnschicht stören könnten.
-
Einführung von Inertgas:
- Ein Inertgas, in der Regel Argon, wird in die Kammer eingeleitet, um eine Niederdruckatmosphäre zu schaffen.Argon wird bevorzugt, weil es chemisch inert ist und nicht mit dem Targetmaterial oder dem Substrat reagiert.
- Der Gasdruck wird sorgfältig kontrolliert, um den Ionisierungsprozess zu optimieren und eine effiziente Zerstäubung zu gewährleisten.
-
Plasma-Erzeugung:
- Eine Hochspannung (3-5 kV) wird angelegt, um das Argongas zu ionisieren, wodurch ein Plasma aus positiv geladenen Argon-Ionen (Ar+) und freien Elektronen entsteht.
- Das Plasma wird mit Hilfe eines Magnetfelds eingegrenzt und gelenkt, wodurch die Ionisierungseffizienz erhöht und die Ionen auf das Zielmaterial gerichtet werden.
-
Bombardierung des Zielmaterials:
- Das Targetmaterial, das als Kathode dient, ist negativ geladen.Dadurch werden die positiv geladenen Argon-Ionen angezogen, die auf das Target beschleunigt werden und mit dessen Oberfläche kollidieren.
- Durch die Energie dieser Zusammenstöße werden Atome aus dem Targetmaterial herausgeschleudert, was als Sputtern bezeichnet wird.
-
Transport der gesputterten Atome:
- Die herausgeschleuderten Atome wandern durch die Vakuumkammer und lagern sich auf dem Substrat ab.Die Niederdruckumgebung sorgt dafür, dass sich die Atome in einer geraden Linie bewegen, was zu einer gleichmäßigen und gut haftenden Dünnschicht führt.
- Das Substrat wird in der Regel gegenüber dem Target positioniert, um die Effizienz der Abscheidung zu maximieren.
-
Filmbildung:
- Wenn die gesputterten Atome das Substrat erreichen, kondensieren sie und bilden einen dünnen Film.Die Dicke und die Eigenschaften des Films lassen sich durch die Einstellung von Parametern wie Sputterzeit, Leistung und Gasdruck steuern.
- Die resultierende Schicht ist sehr gleichmäßig, hat eine ausgezeichnete Haftung und Reinheit und eignet sich daher für eine Vielzahl von Anwendungen.
-
Temperaturkontrolle:
- Die Kammer kann auf Temperaturen von 150°C bis 750°C (302°F bis 1382°F) erhitzt werden, je nach der aufzutragenden Beschichtung.Die Erwärmung kann die Haftung und die Kristallinität des Films verbessern.
- Die Temperaturkontrolle ist entscheidend für das Erreichen der gewünschten Filmeigenschaften und die Gewährleistung der Kompatibilität mit dem Substratmaterial.
-
Anwendungen und Variationen:
- Sputtern wird in verschiedenen Industriezweigen eingesetzt, u. a. in der Elektronik (z. B. bei der Halbleiterherstellung), in der Optik (z. B. bei Antireflexbeschichtungen) und bei industriellen Beschichtungen (z. B. bei verschleißfesten Oberflächen).
- Variationen des Sputterverfahrens, wie Magnetronsputtern und reaktives Sputtern, werden eingesetzt, um bestimmte Schichteigenschaften zu erzielen oder komplexe Materialien abzuscheiden.
Durch die Einhaltung dieser Schritte ermöglicht das Sputterverfahren die präzise Abscheidung dünner Schichten mit maßgeschneiderten Eigenschaften, was es zu einer vielseitigen und unverzichtbaren Technik in der modernen Fertigung und Materialwissenschaft macht.
Zusammenfassende Tabelle:
Wichtigster Schritt | Beschreibung |
---|---|
Aufbau einer Vakuumkammer | Druckreduzierung auf ~1 Pa für eine saubere, kollisionsfreie Umgebung. |
Einführung von Inertgas | Argongas, das zur Schaffung einer Niederdruckatmosphäre für die Ionisierung eingeführt wird. |
Plasmaerzeugung | Durch Hochspannung wird Argon ionisiert und ein Plasma zum Sputtern erzeugt. |
Target-Beschuss | Positiv geladene Argon-Ionen stoßen mit dem Target zusammen und schleudern Atome aus. |
Atomtransport | Ausgeschleuderte Atome wandern durch das Vakuum und lagern sich auf dem Substrat ab. |
Filmbildung | Die Atome kondensieren zu einem dünnen, gleichmäßigen Film mit hervorragender Haftung und Reinheit. |
Temperaturkontrolle | Beheizte Kammer (150°C-750°C) zur Optimierung von Filmhaftung und Kristallinität. |
Anwendungen | Einsatz in der Elektronik, Optik und bei industriellen Beschichtungen für maßgeschneiderte Dünnschichten. |
Entdecken Sie, wie das Sputtering-Verfahren Ihre Produktion verbessern kann. Kontaktieren Sie uns noch heute um mehr zu erfahren!