CVD-Beschichtungen (Chemical Vapor Deposition) sind vielseitige und leistungsstarke Dünnschichten, die in einer Vielzahl von Branchen und Anwendungen eingesetzt werden.Sie werden u. a. wegen ihrer Verschleißfestigkeit, Korrosionsbeständigkeit, ihres Hochtemperaturschutzes und ihres Erosionsschutzes geschätzt.Diese Beschichtungen können auf verschiedene Basismaterialien aufgebracht werden, darunter Keramik, Glas, Metalle und Metalllegierungen, und sind in der Lage, komplizierte und präzise Oberflächen zu beschichten.CVD-Beschichtungen sind aufgrund ihrer Langlebigkeit, Haftung und Fähigkeit, extremen Bedingungen standzuhalten, besonders nützlich in anspruchsvollen Umgebungen, z. B. bei biomedizinischen Implantaten, Leiterplatten, Werkzeugmaschinen und Komponenten für analytische Fließwege.Die bei der CVD verwendeten Vorläufergase können so angepasst werden, dass sie bestimmte Eigenschaften wie Schmierfähigkeit, chemische Inertheit oder hohe Reinheit aufweisen, wodurch sie für spezielle Anwendungen geeignet sind.
Die wichtigsten Punkte erklärt:
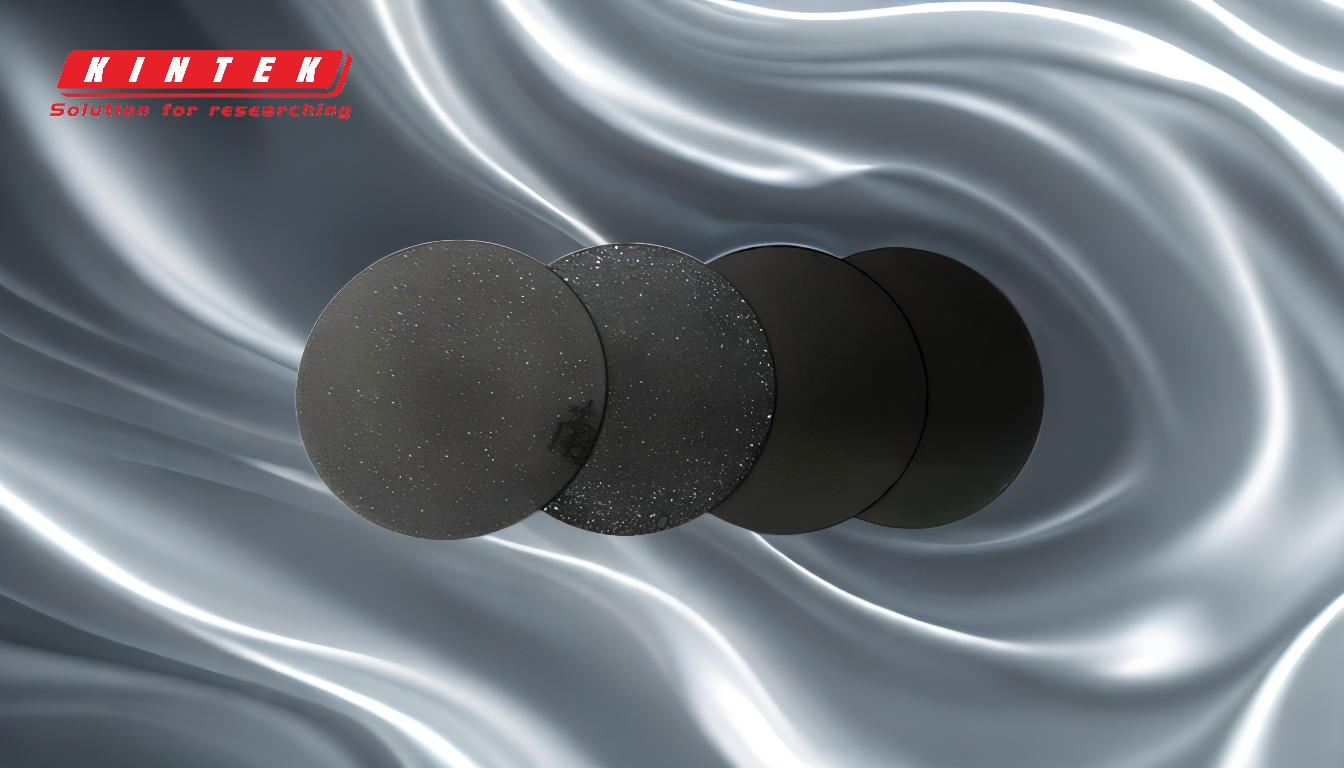
-
Vielseitigkeit der Anwendungen
- CVD-Beschichtungen werden in einer Vielzahl von Branchen eingesetzt, darunter in der Biomedizin, der Elektronik, der Fertigung und der Instrumentierung.
-
Zu den üblichen Anwendungen gehören:
- Implantate für biomedizinische Geräte (z. B. korrosionsbeständige Beschichtungen für chirurgische Werkzeuge oder Implantate).
- Leiterplatten (z. B. dielektrische Schichten wie Siliziumdioxid oder Siliziumnitrid zur Isolierung).
- Werkzeugmaschinen und Verschleißteile (z. B. verschleißfeste Beschichtungen zur Verlängerung der Werkzeuglebensdauer).
- Komponenten für analytische Fließwege (z. B. Beschichtungen für chemische Inertheit in Laborgeräten).
-
Hohe Leistung und Langlebigkeit
-
CVD-Beschichtungen sind dafür bekannt, dass sie extremen Bedingungen standhalten, z. B:
- Hohe und niedrige Temperaturen sowie schnelle Temperaturschwankungen.
- Stark beanspruchte Umgebungen, in denen die Beschichtung auch dann haften bleibt, wenn sich das Substrat biegt oder krümmt.
- Diese Eigenschaften machen sie ideal für Anwendungen, die langfristige Haltbarkeit und Zuverlässigkeit erfordern.
-
CVD-Beschichtungen sind dafür bekannt, dass sie extremen Bedingungen standhalten, z. B:
-
Breite Palette an Basismaterialien
-
CVD-Beschichtungen können auf verschiedene Substrate aufgebracht werden, darunter:
- Keramiken (z. B. für Hochtemperaturanwendungen).
- Glas (z. B. für optische oder schützende Beschichtungen).
- Metalle und Metalllegierungen (z. B. für Verschleiß- oder Korrosionsbeständigkeit).
- Diese Vielseitigkeit ermöglicht den Einsatz von CVD-Beschichtungen in verschiedenen Branchen und Anwendungen.
-
CVD-Beschichtungen können auf verschiedene Substrate aufgebracht werden, darunter:
-
Präzision und komplizierte Oberflächenbeschichtung
-
CVD-Beschichtungen können komplexe Geometrien beschichten, darunter:
- Innenflächen und Dichtungsbereiche.
- Komplizierte oder präzisionsgefertigte Komponenten.
- Diese Fähigkeit ist von entscheidender Bedeutung für Anwendungen, bei denen eine gleichmäßige Schichtdicke und -abdeckung unerlässlich sind.
-
CVD-Beschichtungen können komplexe Geometrien beschichten, darunter:
-
Maßgeschneiderte Eigenschaften durch Optimierung der Vorläufergase
-
Die bei der CVD verwendeten Vorstufengase können optimiert werden, um bestimmte Eigenschaften zu erzielen, z. B:
- Verschleißfestigkeit (z. B. für Werkzeugmaschinen).
- Schmierfähigkeit (z. B. zur Verringerung der Reibung in beweglichen Teilen).
- Korrosionsbeständigkeit (z. B. für biomedizinische Implantate oder Schiffsausrüstung).
- Chemische Inertheit (z. B. für analytische Instrumente).
- Hohe Reinheit (z. B. für die Halbleiterherstellung).
- Diese Anpassung macht CVD-Beschichtungen äußerst anpassungsfähig an spezielle Anforderungen.
-
Die bei der CVD verwendeten Vorstufengase können optimiert werden, um bestimmte Eigenschaften zu erzielen, z. B:
-
Glatte Oberfläche und Dünnschichtabscheidung
-
CVD-Beschichtungen werden für die Abscheidung dünner Schichten mit glatter Oberfläche verwendet, was für Anwendungen wie die folgenden entscheidend ist:
- Halbleiter (z. B. Silizium- oder Kohlenstoffschichten).
- Dielektrische Schichten (z. B. Siliziumdioxid oder Siliziumnitrid zur Isolierung).
- Die glatte Oberfläche gewährleistet eine optimale Leistung bei elektronischen und optischen Anwendungen.
-
CVD-Beschichtungen werden für die Abscheidung dünner Schichten mit glatter Oberfläche verwendet, was für Anwendungen wie die folgenden entscheidend ist:
-
Widerstandsfähigkeit gegen Umwelteinflüsse
-
CVD-Beschichtungen bieten Schutz gegen:
- Korrosion (z. B. in rauen chemischen Umgebungen).
- Erosion (z. B. bei Anwendungen mit hohen Strömungsgeschwindigkeiten).
- Verschmutzung (z. B. bei Anwendungen in der Schifffahrt oder Biomedizin).
- Dadurch eignen sie sich für den Einsatz in schwierigen Umgebungen, in denen andere Beschichtungen versagen könnten.
-
CVD-Beschichtungen bieten Schutz gegen:
-
Starke Verbindung zwischen Beschichtung und Substrat
-
Die Haftung von CVD-Beschichtungen auf Substraten ist außergewöhnlich stark und gewährleistet:
- Langfristige Haltbarkeit in stark beanspruchten Umgebungen.
- Beständigkeit gegen Delaminierung oder Abblättern, auch bei mechanischer Belastung oder Temperaturschwankungen.
- Diese Verbindung ist entscheidend für Anwendungen, bei denen die Beschichtung unter extremen Bedingungen intakt bleiben muss.
-
Die Haftung von CVD-Beschichtungen auf Substraten ist außergewöhnlich stark und gewährleistet:
Zusammenfassend lässt sich sagen, dass CVD-Beschichtungen eine wichtige Technologie für die Herstellung leistungsstarker, haltbarer und maßgeschneiderter dünner Schichten in einer Vielzahl von Branchen sind.Ihre Fähigkeit, verschiedene Materialien zu beschichten, extremen Bedingungen standzuhalten und spezifische funktionale Eigenschaften zu bieten, macht sie für Anwendungen von biomedizinischen Implantaten bis hin zur Halbleiterherstellung unverzichtbar.Die Flexibilität des CVD-Verfahrens in Verbindung mit seiner Fähigkeit, glatte, haftende Beschichtungen zu erzeugen, sorgt für seine anhaltende Bedeutung in der modernen Materialwissenschaft und -technik.
Zusammenfassende Tabelle:
Die wichtigsten Vorteile von CVD-Beschichtungen | Anwendungen |
---|---|
Verschleißfestigkeit | Werkzeugmaschinen, Verschleißteile |
Korrosionsbeständigkeit | Biomedizinische Implantate, Schiffsausrüstung |
Schutz vor hohen Temperaturen | Keramiken, Glas, Metalle |
Erosionsbeständigkeit | Analytische Fließwegkomponenten |
Maßgeschneiderte Eigenschaften (z. B. Schmierfähigkeit, chemische Inertheit) | Halbleiterherstellung, Laborausrüstung |
Glattes Oberflächenfinish | Optische und elektronische Anwendungen |
Starke Verbindung zwischen Beschichtung und Substrat | Stark beanspruchte Umgebungen |
Erschließen Sie das Potenzial von CVD-Beschichtungen für Ihre Branche. Kontaktieren Sie unsere Experten noch heute !