CVD (Chemical Vapour Deposition) wird oft in mehreren Schlüsselaspekten als besser als PVD (Physical Vapour Deposition) angesehen, insbesondere für Anwendungen, die hochreine, gleichmäßige und dichte Beschichtungen über komplexe Geometrien erfordern. Während beide Techniken zur Abscheidung dünner Filme auf Substraten verwendet werden, zeichnet sich CVD durch die Herstellung von Beschichtungen mit überragender Gleichmäßigkeit, Reinheit und Vielseitigkeit aus. Es arbeitet bei höheren Temperaturen und ermöglicht so eine stärkere chemische Bindung und eine bessere Haftung. Darüber hinaus können mit CVD komplizierte Formen und Innenflächen beschichtet werden, mit denen PVD aufgrund seiner Sichtlinienbeschaffenheit zu kämpfen hat. Allerdings hängt die Wahl zwischen CVD und PVD letztlich von der konkreten Anwendung, den Materialanforderungen und den gewünschten Beschichtungseigenschaften ab.
Wichtige Punkte erklärt:
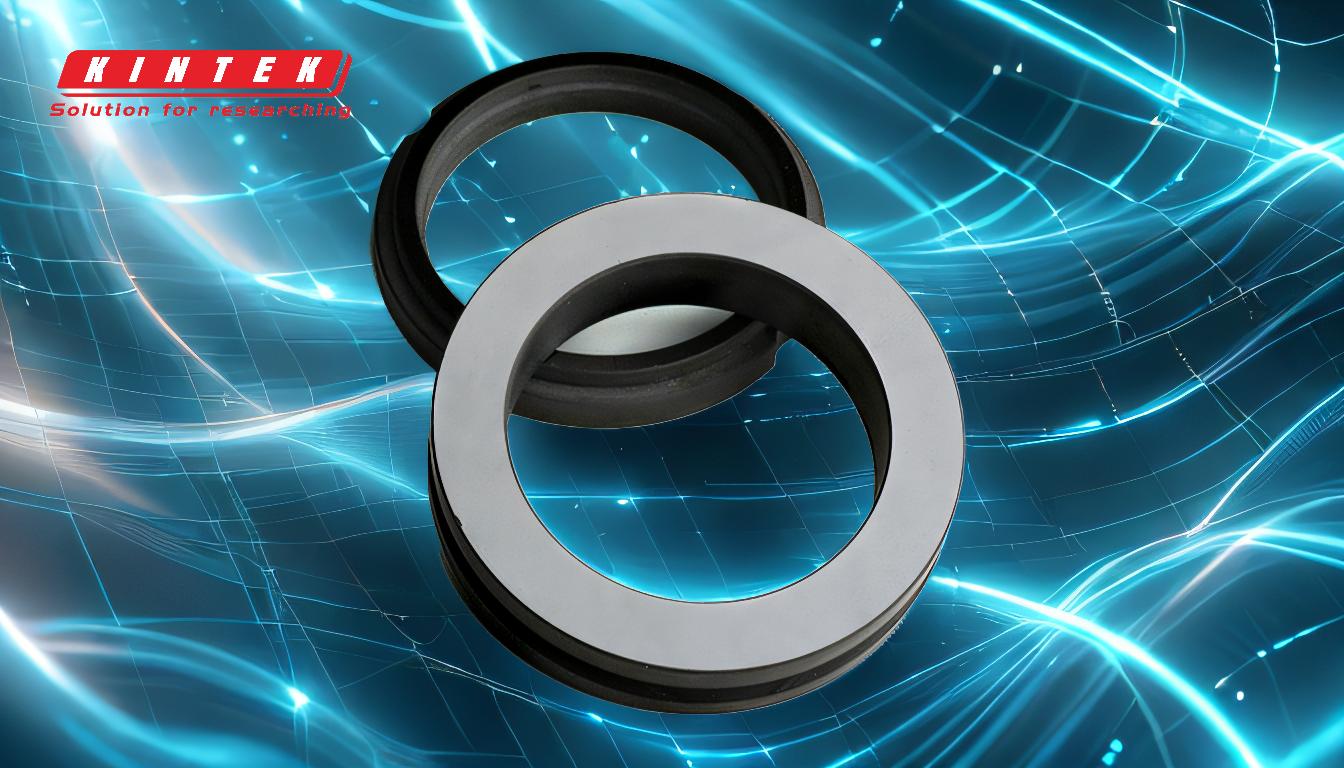
-
Gleichmäßigkeit und Abdeckung der Beschichtung:
- CVD erzeugt Beschichtungen mit gleichmäßiger Dicke, selbst auf komplexen Geometrien, wie z. B. Innenflächen oder komplizierten Formen. Dies liegt daran, dass CVD auf chemischen Reaktionen gasförmiger Vorläufer beruht, die in das Substrat eindringen und sich gleichmäßig darauf ablagern können.
- PVD hingegen ist ein Sichtlinienverfahren, das heißt, es können nur Oberflächen beschichtet werden, die direkt der Dampfquelle ausgesetzt sind. Dies schränkt seine Fähigkeit ein, komplexe Formen gleichmäßig zu beschichten.
-
Reinheit und Dichte der Beschichtung:
- CVD-Beschichtungen sind für ihre hohe Reinheit und Dichte bekannt. Die beim CVD beteiligten chemischen Reaktionen stellen sicher, dass das abgeschiedene Material frei von Verunreinigungen ist und eine dichte, fest verbundene Schicht bildet.
- PVD-Beschichtungen sind zwar glatt und langlebig, weisen jedoch in der Regel eine geringere Dichte auf und können aufgrund des physikalischen Verdampfungsprozesses Verunreinigungen enthalten.
-
Betriebstemperatur und Haftfestigkeit:
- CVD arbeitet bei höheren Temperaturen (450 °C bis 1050 °C), was eine stärkere chemische Bindung zwischen der Beschichtung und dem Substrat fördert. Dies führt zu einer besseren Haftung und Haltbarkeit.
- PVD arbeitet bei niedrigeren Temperaturen (250 °C bis 450 °C), wodurch es für temperaturempfindliche Substrate geeignet ist, aber im Vergleich zu CVD oft zu einer schwächeren Bindung führt.
-
Materialvielfalt:
- CVD kann ein breites Spektrum an Materialien abscheiden, darunter Keramik, Polymere und Verbundwerkstoffe. Es ist besonders effektiv für die Herstellung von Hochleistungsbeschichtungen wie Al2O3, das eine hervorragende Härte, Verschleißfestigkeit und chemische Stabilität bietet.
- PVD kann Metalle, Legierungen und Keramik abscheiden, ist jedoch aufgrund von Prozessbeschränkungen im Allgemeinen nur begrenzt in der Lage, bestimmte Hochleistungsbeschichtungen wie Al2O3 herzustellen.
-
Anwendungsvielfalt:
- CVD ist vielseitig und kann für Anwendungen eingesetzt werden, die hochreine Beschichtungen erfordern, wie etwa die Halbleiterfertigung, die Graphenproduktion und Kohlenstoffnanoröhren-Arrays.
- PVD wird häufiger für Anwendungen verwendet, die glatte, dünne und dauerhafte Beschichtungen erfordern, wie z. B. dekorative Oberflächen, Schneidwerkzeuge und verschleißfeste Oberflächen.
-
Kosten und Effizienz:
- Aufgrund der Möglichkeit, mehrere Teile gleichzeitig zu beschichten, und der geringeren Materialkosten ist CVD für die Großserienproduktion häufig kostengünstiger.
- PVD ist bei einschichtigen Beschichtungen schneller, bei großflächigen oder komplexen Anwendungen jedoch möglicherweise weniger effizient.
-
Spezifische Vorteile von CVD:
- CVD bietet hohe Abscheidungsraten und die Dicke der Beschichtungen kann durch Anpassung von Temperatur und Dauer präzise gesteuert werden.
- Es ist in der Lage, große Graphenschichten und Kohlenstoff-Nanoröhrchen-Arrays herzustellen, die mit PVD nur schwer zu erreichen sind.
-
Einschränkungen von PVD:
- PVD-Beschichtungen sind im Vergleich zu CVD weniger gleichmäßig und dicht und das Verfahren ist für die Beschichtung komplexer Geometrien weniger effektiv.
- Obwohl PVD sein Angebot an Beschichtungsmaterialien erweitert und die Leistung verbessert hat, fällt es ihm immer noch schwer, bei bestimmten Anwendungen mit der Vielseitigkeit und Leistung von CVD mithalten zu können.
Zusammenfassend lässt sich sagen, dass CVD bei Anwendungen, die hochreine, gleichmäßige und dichte Beschichtungen erfordern, insbesondere bei komplexen Geometrien, häufig der PVD vorgezogen wird. PVD bleibt jedoch eine gute Wahl für Anwendungen, die glatte, dünne und dauerhafte Beschichtungen auf einfacheren Formen erfordern. Die Entscheidung zwischen den beiden Techniken sollte auf den spezifischen Anforderungen der Anwendung basieren, einschließlich Materialeigenschaften, Beschichtungsleistung und Kostenüberlegungen.
Übersichtstabelle:
Aspekt | CVD | PVD |
---|---|---|
Einheitlichkeit und Abdeckung | Gleichmäßige Dicke, auch bei komplexen Formen und Innenflächen | Beschränkt auf die Sichtlinie, Probleme mit komplexen Geometrien |
Reinheit und Dichte | Hochreine, dichte Beschichtungen mit starker chemischer Bindung | Weniger dicht, kann Verunreinigungen enthalten |
Betriebstemperatur | Höhere Temperaturen (450°C–1050°C) für stärkere Haftung | Niedrigere Temperaturen (250°C–450°C), geeignet für empfindliche Untergründe |
Materialvielfalt | Große Auswahl: Keramik, Polymere, Verbundwerkstoffe (z. B. Al2O3) | Beschränkt auf Metalle, Legierungen und einige Keramiken |
Anwendungsvielfalt | Hochreine Beschichtungen für Halbleiter, Graphen, Kohlenstoffnanoröhren | Glatte, dünne Beschichtungen für dekorative Oberflächen, Schneidwerkzeuge |
Kosten und Effizienz | Kostengünstig für Großserienfertigung, geringere Materialkosten | Schneller bei einschichtigen Beschichtungen, weniger effizient bei komplexen Formen |
Sind Sie bereit, Ihren Beschichtungsprozess mit der CVD-Technologie zu verbessern? Kontaktieren Sie noch heute unsere Experten um die passende Lösung für Ihre Bedürfnisse zu finden!