Sputtern ist ein wichtiger Prozess bei der Abscheidung von Dünnschichten, insbesondere in Branchen, die präzise, gleichmäßige und hochwertige Beschichtungen benötigen. Dabei wird ein Zielmaterial mit hochenergetischen Ionen beschossen, wodurch Atome ausgestoßen werden und sich auf einem Substrat ablagern. Diese Methode ist in Anwendungen wie der Halbleiterherstellung, der Optik und der Rasterelektronenmikroskopie (SEM) weit verbreitet. Das Sputtern gewährleistet eine gleichmäßige Schichtdicke, eine starke Bindung auf atomarer Ebene und die Möglichkeit, komplexe Geometrien zu beschichten. Es wird auch für seine Fähigkeit geschätzt, eine breite Palette von Materialien, einschließlich Metallen, Keramiken und Kunststoffen, bei niedrigeren Temperaturen abzuscheiden, was es für temperaturempfindliche Substrate geeignet macht.
Die wichtigsten Punkte erklärt:
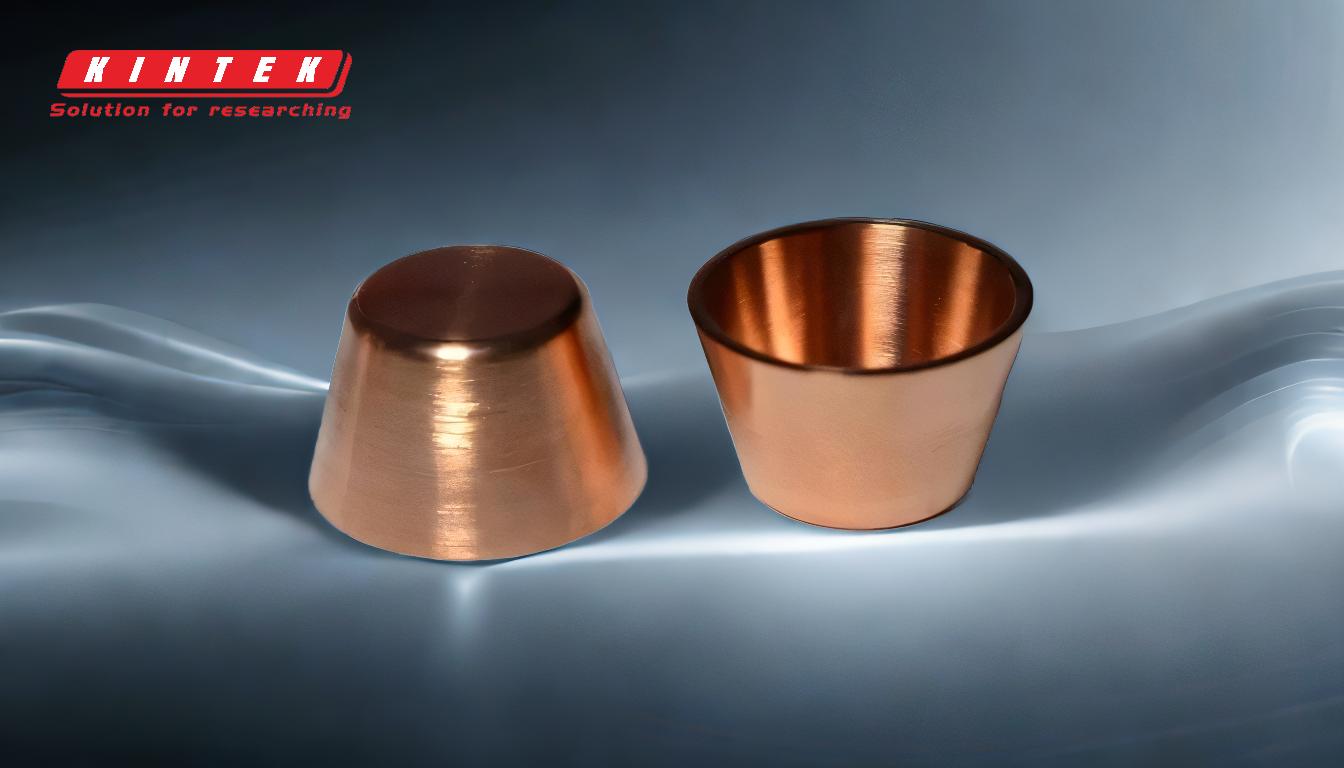
-
Uniform Thin-Film Deposition:
- Das Sputtern ermöglicht die Herstellung dünner, gleichmäßiger Schichten, die für Anwendungen wie Halbleiterbauelemente und optische Beschichtungen unerlässlich sind. Das Verfahren gewährleistet eine gleichmäßige Schichtdicke auf dem gesamten Substrat, selbst auf komplexen, dreidimensionalen Oberflächen.
- Der Impulsübertragungsmechanismus sorgt dafür, dass die ausgestoßenen Zielatome gleichmäßig verteilt werden, so dass eine dichte und gleichmäßige Schicht entsteht.
-
Starke Bindung auf atomarer Ebene:
- Die hochenergetischen Ionen, die beim Sputtern verwendet werden, erzeugen starke Bindungen auf atomarer Ebene zwischen dem abgeschiedenen Material und dem Substrat. Dies führt zu dauerhaften Beschichtungen mit hervorragender Haftung, was für Anwendungen, die eine langfristige Zuverlässigkeit erfordern, wie z. B. Schutzbeschichtungen in der Luft- und Raumfahrt oder in medizinischen Geräten, entscheidend ist.
-
Vielseitigkeit bei der Materialabscheidung:
- Durch Sputtern kann eine Vielzahl von Materialien abgeschieden werden, darunter Metalle, Keramiken und Kunststoffe. Dank dieser Vielseitigkeit eignet sich das Verfahren für verschiedene Branchen, von der Elektronik bis zu dekorativen Beschichtungen.
- Das Verfahren kann durch die Auswahl geeigneter Zielmaterialien und Abscheidungsparameter auf bestimmte Materialeigenschaften wie Leitfähigkeit, Reflektivität oder Härte zugeschnitten werden.
-
Präzise Kontrolle über die Schichtdicke:
- Das Sputtern ermöglicht eine präzise Steuerung der Schichtdicke durch Anpassung der Abscheidungszeit und anderer Prozessparameter. Dieses Maß an Kontrolle ist für Anwendungen wie die Mikroelektronik von entscheidender Bedeutung, bei denen selbst Abweichungen im Nanometerbereich die Leistung beeinträchtigen können.
-
Niedrigere Abscheidetemperaturen:
- Im Gegensatz zu einigen anderen Abscheidungsmethoden kann das Sputtern bei relativ niedrigen Temperaturen durchgeführt werden. Dies macht es ideal für die Beschichtung temperaturempfindlicher Substrate wie Polymere oder biologische Proben, ohne diese zu beschädigen.
-
Beschichtung komplexer Geometrien:
- Das Sputtern eignet sich hervorragend für die Beschichtung komplexer, dreidimensionaler Oberflächen, wie sie beispielsweise bei REM-Proben oder komplizierten mechanischen Bauteilen zu finden sind. Das Verfahren gewährleistet eine gleichmäßige Beschichtung auch in schwer zugänglichen Bereichen.
-
Reduktion von Eigenspannungen:
- Durch das Sputtern wird die abgeschiedene Schicht verdichtet, wodurch Eigenspannungen verringert und die mechanischen Eigenschaften der Beschichtung verbessert werden. Dies ist besonders wichtig für Anwendungen, die eine hohe Haltbarkeit und Beständigkeit gegen Rissbildung oder Delamination erfordern.
-
Einsatz in der Rasterelektronenmikroskopie (SEM):
- In der Rasterelektronenmikroskopie werden nichtleitende Proben durch Sputtern mit einer dünnen leitfähigen Schicht, z. B. Gold oder Platin, beschichtet. Dadurch wird die Leitfähigkeit der Probe erhöht, was eine klarere Abbildung und Analyse ermöglicht.
-
Impuls-Transfer-Mechanismus:
- Der Sputterprozess beruht auf dem Impulstransfer, bei dem hochenergetische Ionen mit dem Zielmaterial zusammenstoßen und Atome ausstoßen, die sich dann auf dem Substrat ablagern. Dieser Mechanismus gewährleistet eine effiziente und kontrollierte Materialabscheidung.
-
Vakuumumgebung und Inertgas:
- Das Sputtern erfolgt in einer Vakuumkammer mit einem Inertgas, z. B. Argon. Die Vakuumumgebung minimiert die Verunreinigung, während das Inertgas ionisiert wird, um das für den Prozess erforderliche Plasma zu erzeugen.
Zusammenfassend lässt sich sagen, dass das Sputtern erforderlich ist, weil es eine unvergleichliche Präzision, Gleichmäßigkeit und Vielseitigkeit bei der Abscheidung von Dünnschichten bietet. Die Fähigkeit, starke, dauerhafte Beschichtungen auf komplexen Oberflächen bei niedrigeren Temperaturen zu erzeugen, macht es in Branchen von der Elektronik bis zur Mikroskopie unverzichtbar. Durch die Ausnutzung des Impulsübertragungsmechanismus und den Betrieb in einer kontrollierten Vakuumumgebung gewährleistet das Sputtern qualitativ hochwertige Ergebnisse, die den strengen Anforderungen der modernen Technologie entsprechen.
Zusammenfassende Tabelle:
Die wichtigsten Vorteile des Sputterns | Anwendungen |
---|---|
Gleichmäßige Abscheidung von Dünnschichten | Halbleiterherstellung, Optik |
Starke Bindung auf atomarer Ebene | Luft- und Raumfahrt, medizinische Geräte |
Vielseitigkeit bei der Materialabscheidung | Elektronik, dekorative Beschichtungen |
Präzise Kontrolle über die Schichtdicke | Mikroelektronik |
Niedrigere Abscheidetemperaturen | Temperaturempfindliche Substrate |
Möglichkeit zur Beschichtung komplexer Geometrien | SEM-Proben, komplizierte Komponenten |
Verringerung von Eigenspannungen | Anwendungen mit hoher Dauerhaftigkeit |
Einsatz im SEM für leitfähige Beschichtungen | Rasterelektronenmikroskopie |
Mechanismus der Impulsübertragung | Effiziente und kontrollierte Materialabscheidung |
Vakuumumgebung und Inertgas | Minimale Verunreinigung, kontrolliertes Plasma |
Möchten Sie wissen, wie das Sputtern Ihren Dünnschichtabscheidungsprozess verbessern kann? Kontaktieren Sie noch heute unsere Experten für maßgeschneiderte Lösungen!