Stickstoff wird häufig im Glühprozess verwendet, da er eine inerte Atmosphäre schafft, die Oxidation und Entkohlung von Materialien verhindert.Dies ist besonders wichtig bei der Wärmebehandlung von Metallen, der Pulvermetallurgie und anderen industriellen Verfahren, bei denen die Unversehrtheit und Qualität des Materials entscheidend ist.Stickstoffglühen ist für eine Vielzahl von Werkstoffen von Vorteil, darunter Eisen- und Nichteisenmetalle, und wird in Verfahren wie Blankglühen, Neutralhärten und Sintern eingesetzt.Seine inerte Beschaffenheit stellt sicher, dass das Material nicht mit Sauerstoff reagiert, der andernfalls die Eigenschaften des Materials beeinträchtigen könnte.Außerdem ist Stickstoff kostengünstig und leicht verfügbar, was ihn zu einer praktischen Wahl für industrielle Anwendungen macht.
Die wichtigsten Punkte erklärt:
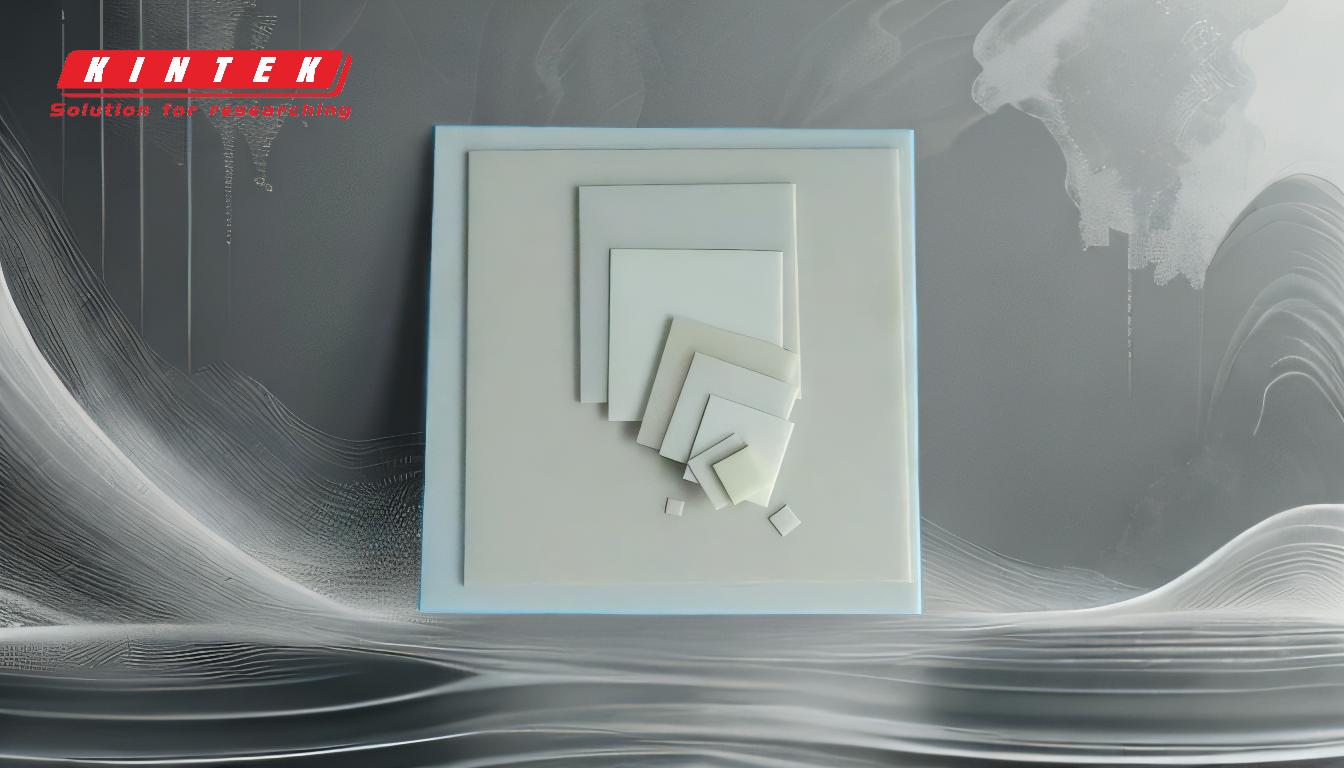
-
Verhinderung von Oxidation:
- Während des Glühens werden die Materialien auf hohe Temperaturen erhitzt, was sie anfällig für Oxidation macht, wenn sie Sauerstoff ausgesetzt sind.Oxidation kann zur Bildung von Oxiden auf der Oberfläche des Materials führen und seine Qualität und Leistung beeinträchtigen.
- Da Stickstoff ein inertes Gas ist, reagiert er nicht mit dem Material und verhindert so die Oxidation.Dies ist besonders wichtig für Metalle wie Stahl, Kupfer und Aluminium, bei denen die Unversehrtheit der Oberfläche entscheidend ist.
-
Schaffung einer inerten Atmosphäre:
- Stickstoff wird verwendet, um im Glühofen eine inerte Atmosphäre zu schaffen.Diese inerte Umgebung stellt sicher, dass während der Erwärmungs- und Abkühlungsphasen keine unerwünschten chemischen Reaktionen auftreten.
- Eine inerte Atmosphäre ist für Verfahren wie das Blankglühen unerlässlich, bei denen es darum geht, den Oberflächenglanz des Materials zu erhalten und Verfärbungen zu vermeiden.
-
Entkohlung Prävention:
- Entkohlung ist ein Prozess, bei dem Kohlenstoff von der Oberfläche von Stahl oder anderen kohlenstoffhaltigen Materialien verloren geht, was zu einer Verringerung der Härte und Festigkeit führt.
- Stickstoff trägt dazu bei, die Entkohlung zu verhindern, indem er eine neutrale Umgebung aufrechterhält, die das Entweichen von Kohlenstoff aus dem Material verhindert.Dies ist entscheidend für die Aufrechterhaltung der mechanischen Eigenschaften des Werkstoffs.
-
Vielseitigkeit in der Anwendung:
- Das Stickstoffglühen wird in einer Vielzahl von Anwendungen eingesetzt, darunter die Wärmebehandlung von Werkzeugen, Schrauben, Federn, Lagern und Nichteisenmetallen wie Kupfer und Aluminium.
- Es wird auch bei speziellen Verfahren wie Nitrieren, Carbonitrieren und Sintern eingesetzt, bei denen die Aufrechterhaltung einer kontrollierten Atmosphäre für die Erzielung der gewünschten Materialeigenschaften unerlässlich ist.
-
Kosteneffizienz und Verfügbarkeit:
- Stickstoff ist relativ preiswert und leicht verfügbar, was ihn zu einer praktischen Wahl für industrielle Anwendungen macht.Sein weitverbreiteter Einsatz in verschiedenen Industriezweigen ist auch auf seine Sicherheit und einfache Handhabung im Vergleich zu anderen Gasen wie Wasserstoff zurückzuführen.
- Die Kosteneffizienz von Stickstoff macht ihn zu einer bevorzugten Option für groß angelegte industrielle Prozesse, bei denen die benötigte Gasmenge erheblich ist.
-
Vergleich mit Wasserstoff:
- Wasserstoff hat zwar einen höheren Wärmeübergangskoeffizienten und kann den Glühprozess effizienter machen, ist aber reaktiver und birgt Sicherheitsrisiken, z. B. Entflammbarkeit.
- Stickstoff hingegen ist sicherer in der Handhabung und bietet eine stabilere Umgebung für das Glühen, insbesondere bei Prozessen, bei denen die Gefahr der Oxidation groß ist.
-
Verwendung in spezialisierten Prozessen:
- Stickstoff wird auch in speziellen Wärmebehandlungsverfahren wie dem Blankhärten und Plasmaschneiden eingesetzt, bei denen die Aufrechterhaltung einer nicht reaktiven Atmosphäre entscheidend ist.
- Bei diesen Verfahren sorgt Stickstoff dafür, dass die Oberfläche des Materials frei von Oxiden und anderen Verunreinigungen bleibt, was zu einer besseren Oberflächenqualität führt.
Zusammenfassend lässt sich sagen, dass Stickstoff im Glühprozess vor allem dazu dient, Oxidation und Entkohlung zu verhindern, eine inerte Atmosphäre zu schaffen und die Integrität des Materials zu erhalten.Seine Vielseitigkeit, Kosteneffizienz und Sicherheit machen es zu einer idealen Wahl für eine Vielzahl von industriellen Anwendungen.
Zusammenfassende Tabelle:
Hauptnutzen | Beschreibung |
---|---|
Verhindert Oxidation | Stickstoff schafft eine inerte Atmosphäre, die eine Materialzersetzung verhindert. |
Verhindert die Entkohlung | Erhält den Kohlenstoffgehalt und damit die Härte und Festigkeit der Materialien. |
Vielseitige Anwendungen | Verwendung beim Blankglühen, Sintern und bei der Wärmebehandlung von Metallen. |
Kostengünstig und sicher | Erschwinglich, leicht verfügbar und sicherer als reaktive Gase wie Wasserstoff. |
Spezialisierte Prozesse | Ideal zum Blankhärten, Plasmaschneiden und zur Erhaltung der Oberflächenintegrität. |
Erfahren Sie, wie Stickstoffglühen Ihre industriellen Prozesse verbessern kann. Kontaktieren Sie unsere Experten noch heute !