Das Ziel pulverbasierter Herstellungsverfahren
Inhaltsverzeichnis
- Das Ziel pulverbasierter Herstellungsverfahren
- Der Prozess des kaltisostatischen Pressens (CIP).
- Der Prozess des Heißisostatischen Pressens (HIP).
- Die Möglichkeit der einstufigen Vorverarbeitung von Konstruktionen durch additive Fertigung mit mehreren Materialien
- Der Einsatz der selektiven Abscheidungstechnologie von Kintek beim isostatischen Pressen
- Das Potenzial eines ähnlichen Ansatzes für Teile, die mit HIP verarbeitet werden
- Fazit: Die Brücke der selektiven Pulverabscheidung zwischen neuer additiver Fertigung und traditioneller Fertigung
- Das Potenzial der selektiven Pulverabscheidung, eine Brücke zwischen neuen additiven Fertigungstechnologien und der traditionellen Herstellung hochwertiger Komponenten zu schlagen
- Durch diesen Ansatz besteht die Möglichkeit, die Besorgnis der Industrie hinsichtlich mittels additiver Fertigung hergestellter Artikel zu lindern
Das Ziel der meisten pulverbasierten Herstellungsverfahren
Das Ziel der meisten pulverbasierten Herstellungsverfahren , wie beispielsweise der Pulvermetallurgie (PM), besteht darin, dichte Teile mit weniger als 1 % Porosität herzustellen, ohne das Ausgangsmaterial zu schmelzen. Das in diesen Verfahren verwendete lose Pulver weist typischerweise eine niedrige Stapeldichte auf, wobei die theoretische Maximaldichte für zufällig gestapelte, perfekt kugelförmige Partikel nur 64 % beträgt. Durch die Verwendung geeigneter Pulverpartikelgrößenverteilungen oder verformbarer Pulver können jedoch Packungsdichten von über 90 % erreicht werden.
Die Grenzen des uniaxialen Pressens
Um bei pulverbasierten Herstellungsprozessen zufriedenstellende Ergebnisse zu erzielen, ist die Anwendung von Druck entscheidend. Üblicherweise wird uniaxiales Pressen verwendet, bei dem Druck in eine Richtung ausgeübt wird. Allerdings weist diese Methode insbesondere bei dicken Teilen Einschränkungen auf. Dies führt tendenziell zu Dichteunterschieden entlang der Pressrichtung, die sich auf die Qualität des Endteils auswirken können.
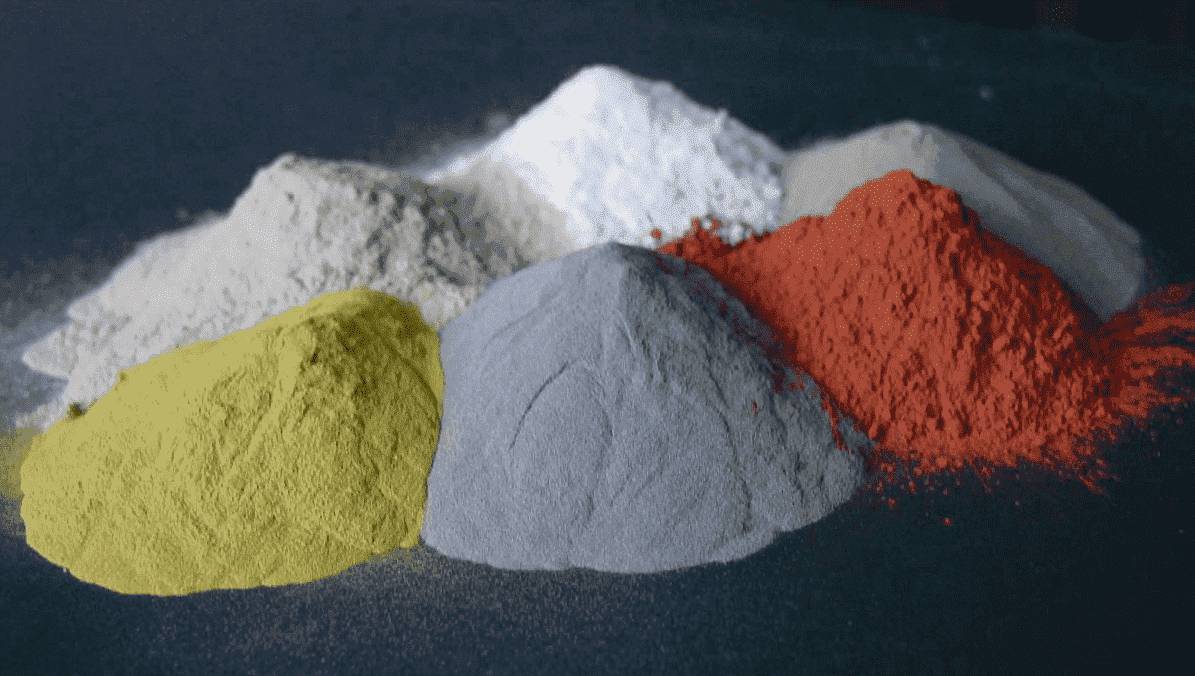
Die Lösung: isostatisches Pressen
Um die Einschränkungen des uniaxialen Pressens zu überwinden, wird bei Massenteilen häufig das isostatische Pressen eingesetzt. Isostatisches Pressen ist eine Pulververarbeitungstechnik, bei der das Teil durch Flüssigkeitsdruck verdichtet wird. Metallpulver werden in einen flexiblen Behälter gegeben, der als Form für das Teil dient. Auf die gesamte Außenfläche des Behälters wird Flüssigkeitsdruck ausgeübt, wodurch das Pulver gepresst und in die gewünschte Geometrie gebracht wird. Im Gegensatz zum einachsigen Pressen wird beim isostatischen Pressen Druck aus allen Richtungen ausgeübt, was zu einer gleichmäßigeren Dichteverteilung führt.
Alternative Prozesse
Isostatisches Pressen
Isostatisches Pressen ist ein weit verbreitetes Herstellungsverfahren auf Pulverbasis, das einen gleichmäßigen Druck ausübt, um Pulver zu verfestigen oder Defekte in Gussteilen zu heilen. Es kann für eine Reihe von Materialien verwendet werden, darunter Keramik, Metalle, Verbundwerkstoffe, Kunststoffe und Kohlenstoff. Dabei wird das Pulver in eine flexible Form gegeben, versiegelt und aus allen Richtungen mit Druck beaufschlagt. Das isostatische Pressen bietet einzigartige Vorteile für Keramik- und Feuerfestanwendungen, da es die Bildung von Produktformen mit präzisen Toleranzen ermöglicht und den Bedarf an kostspieliger Bearbeitung reduziert.
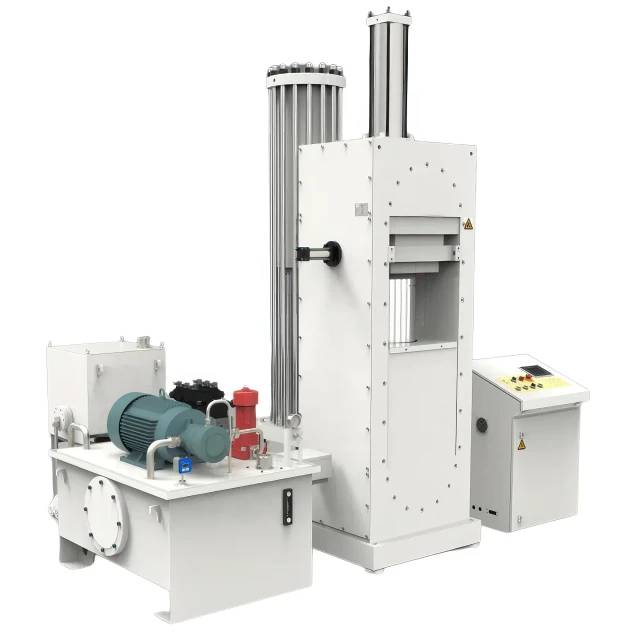
Metallpulververarbeitung
Die Pulvermetallverarbeitung ist eine weitere pulverbasierte Fertigungstechnik, die die Herstellung von Produkten mit Eigenschaften ermöglicht, die die von legierten Materialien übertreffen können. Bei diesem Verfahren werden Metall- oder Keramikpulver zusammen mit einem Bindemittel zu einer Mischung vermischt, die in gewünschte Formen gepresst werden kann. Bei größeren Teilen wird die Mischung in Formen gefüllt. Dieses Verfahren wird häufig bei der Herstellung von Produkten wie PDC-Bohrern (Polykristalliner Diamantverbundstoff) für Tiefbrunnenbohrungen verwendet, bei denen die Mischung gepresst und gebrannt wird, um endkonturnahe Produkte zu erhalten.
Fortschritte in der Pulvermetallurgie
Pulverbasierte Verfahren wie Pulververdichtung, heißisostatisches Pulverpressen (P-HIP), Metallspritzguss (MIM) und Funkenplasmasintern werden zunehmend zur Herstellung von Net-Shape- (NS) und Near-Net-Shape- (NS) und Near-Net-Shape-Verfahren eingesetzt. Formteile (NNS) aus Hochleistungslegierungen. Diese Prozesse zielen darauf ab, Teile herzustellen, die genau der erforderlichen Endgeometrie entsprechen, und Kosten, Durchlaufzeiten und Materialverschwendung zu reduzieren, indem Prozessschritte wie Bearbeitung und Endbearbeitung minimiert werden. Mit pulverbasierten Technologien können Teile mit Leistungseigenschaften hergestellt werden, die denen herkömmlicher Herstellungsverfahren wie dem Gießen entsprechen oder diese sogar übertreffen können. Dies ist auf Faktoren wie die einheitliche Mikrostruktur von Partikelmaterialien und die Fortschritte in der Pulvermetallurgie zurückzuführen, die die Herstellung einer breiten Palette von Hochleistungslegierungen im Pulverformat ermöglichen.
Zusammenfassend lässt sich sagen, dass das Ziel pulverbasierter Fertigungsverfahren darin besteht, dichte Teile mit hoher Packungsdichte und minimaler Porosität herzustellen. Isostatisches Pressen ist eine wertvolle Technik zur Überwindung der Einschränkungen des uniaxialen Pressens und sorgt für eine gleichmäßigere Dichteverteilung in dicken Teilen. Darüber hinaus haben alternative Prozesse wie die Pulvermetallverarbeitung und Fortschritte in der Pulvermetallurgie die Möglichkeiten der pulverbasierten Fertigung erweitert und ermöglichen die Herstellung komplexer Formen und Hochleistungslegierungen.
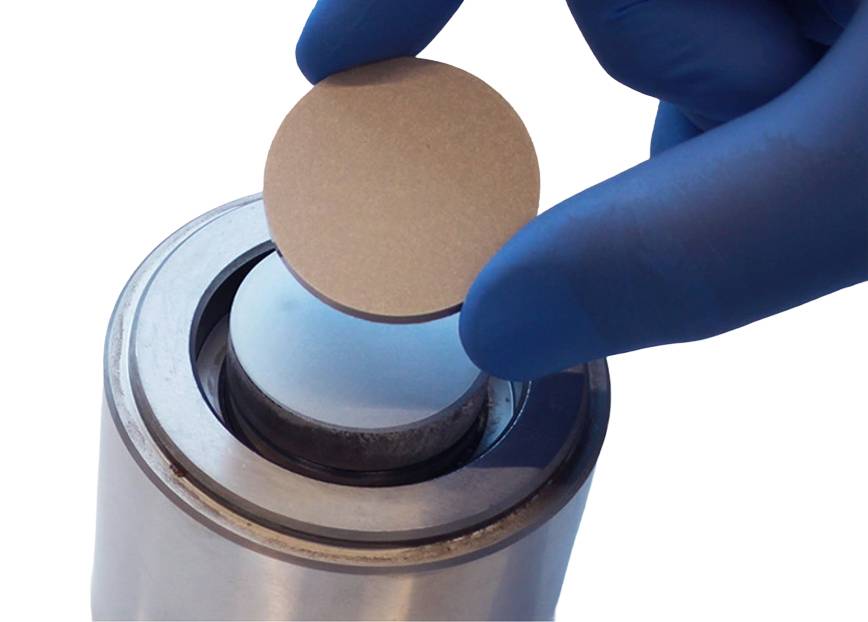
Der Prozess des kaltisostatischen Pressens (CIP).
Der Prozess von CIP
Kaltisostatisches Pressen (CIP) ist eine Materialverarbeitungsmethode, mit der Pulver zu Komponenten unterschiedlicher Größe und Form geformt und verdichtet werden. Dabei wird das Pulver oder ein Grünteil mit geringer Dichte in einen versiegelten flexiblen Behälter gegeben und in einem Druckbehälter in eine Flüssigkeit getaucht. Dabei wird ein Druck von mehreren Tausend Bar angelegt, wodurch der Grünling möglichst nahe an seine maximale Packungsdichte verdichtet wird. Diese höhere Anfangsdichte beschleunigt die Konsolidierung zur Enddichte im Wärmekreislauf.
CIP nutzt das vom französischen Wissenschaftler Blaise Pascal vorgeschlagene Prinzip, das besagt, dass eine Druckänderung in einer eingeschlossenen inkompressiblen Flüssigkeit unvermindert auf jeden Teil der Flüssigkeit und auf die Oberfläche ihres Behälters übertragen wird. Pulvermaterialien werden in einer Form mit geringem Verformungswiderstand, beispielsweise einem Gummibeutel, versiegelt, und es wird Flüssigkeitsdruck ausgeübt, um den Formkörper über seine gesamte Oberfläche gleichmäßig zu komprimieren.
Das Metallformpressen ist ein ähnliches Pressverfahren wie CIP. Bei diesem Verfahren werden Pulvermaterialien in einen von einer Metallform und einem unteren Stempel umschlossenen Raum gefüllt. Anschließend werden sie komprimiert, indem der Abstand zwischen Ober- und Unterstempel verringert wird.
Die Vorteile einer hohen Anfangsdichte bei der Beschleunigung der Konsolidierung zur Enddichte im Wärmekreislauf
Die durch den CIP-Prozess erreichte hohe Anfangsdichte bietet mehrere Vorteile bei der Konsolidierung von Pulvern. Zu diesen Vorteilen gehören:
Vorhersehbare Kompression während des nachfolgenden Sinterprozesses: Hohe Verdichtung und gleichmäßige Dichte sorgen für eine vorhersehbare Kompression während des Sinterprozesses, was zu einer konsistenten und zuverlässigen Enddichte führt.
Fähigkeit zur Bearbeitung großer, komplizierter und perfekter Formen: CIP ermöglicht die Bearbeitung großer und komplexer Formen mit hoher Präzision. Dies spart Zeit und Kosten bei Nachbehandlungsprozessen.
Erzeugung von Teilen mit großem Seitenverhältnis und gleichmäßiger Dichte: Durch CIP können Teile mit Seitenverhältnissen von mehr als 2:1 hergestellt werden, wobei im gesamten Bauteil eine gleichmäßige Dichte erhalten bleibt.
Grünfestigkeit für die Handhabung und Behandlung während des Prozesses: Der durch CIP gebildete Grünling verfügt über ausreichende Festigkeit für die Handhabung und Behandlung während des Prozesses, wodurch die Produktionskosten gesenkt werden.
Insgesamt bietet der CIP-Prozess eine effiziente und effektive Formung und Verdichtung von Pulvern, was zu hochwertigen Bauteilen mit der gewünschten Dichte führt. Seine Vielseitigkeit und die Fähigkeit, verschiedene Materialien zu verarbeiten, machen es zu einer wertvollen Methode in Branchen wie der Präzisionsfertigung, Luft- und Raumfahrt, Verteidigung und Automobilindustrie.
Einem Bericht von DataIntelo zufolge wird der globale Markt für kaltisostatische Pressgeräte (CIP) im Prognosezeitraum 2020–2026 voraussichtlich mit einer erheblichen jährlichen Wachstumsrate wachsen. Die steigende Nachfrage nach CIP-verarbeiteten Produkten in Branchen wie Präzisionsfertigung, Luft- und Raumfahrt, Verteidigung und Automobilindustrie treibt dieses Wachstum voran.
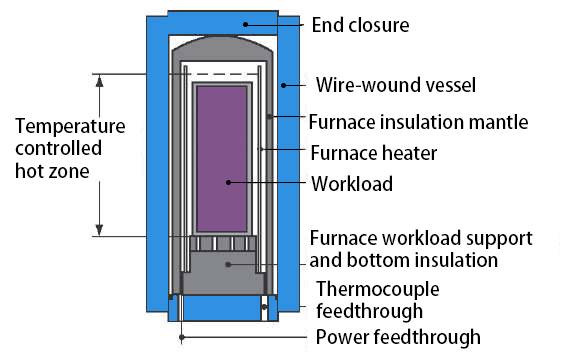
Der Prozess des Heißisostatischen Pressens (HIP).
Der Nutzen des uniaxialen druckunterstützten Sinterns im HIP
Während des Wärmezyklus kann auch Druck ausgeübt werden. Beim uniaxialen druckunterstützten Sintern können typischerweise nur plattenförmige Produkte hergestellt werden. Für komplexere Teile kommt das Heißisostatische Pressen (HIP) zum Einsatz. Da HIP in einer Gasatmosphäre durchgeführt wird, besteht die Hauptanforderung darin, dass die äußere Oberfläche der behandelten Teile zunächst gasdicht sein muss. Daher kann dieses Verfahren zur Herstellung von Bauteilen verwendet werden, indem Teilepulver in einer Weichstahlhülle vakuumversiegelt wird. Durch die gleichmäßige Druckausübung bleibt die Form erhalten, auch wenn das Teil und die Schale schrumpfen. Mit einer HIP-Strategie verarbeitete Pulver sind typischerweise nicht mit Schmelzprozessen kompatibel, da sie entweder übermäßige Temperaturen erfordern oder ungünstige Mikrostrukturen ergeben. Dennoch weist der zusätzliche Aufwand, der bei der Verarbeitung dieser Materialien betrieben wird, darauf hin, dass sie in anspruchsvollen Anwendungen eingesetzt werden, bei denen selbst ein geringer Grad an Porosität nicht akzeptabel ist.
Die Anforderungen und Ergebnisse des HIP-Prozesses
Unter Heißisostatischem Pressen (HIP) versteht man die gleichzeitige Anwendung hoher Temperatur und hohem Druck auf Metalle und andere Materialien über einen bestimmten Zeitraum, um deren mechanische Eigenschaften zu verbessern. In der HIP-Einheit ist ein Hochtemperaturofen in einem Druckbehälter eingeschlossen. Temperatur, Druck und Prozesszeit werden präzise gesteuert, um optimale Materialeigenschaften zu erreichen. Teile werden in einem Inertgas, im Allgemeinen Argon, erhitzt, das einen gleichmäßigen „isostatischen“ Druck in alle Richtungen ausübt. Dadurch wird das Material „plastisch“, sodass Hohlräume unter dem Differenzdruck kollabieren. Die Oberflächen der Hohlräume verbinden sich durch Diffusion miteinander, um die Defekte effektiv zu beseitigen und eine nahezu theoretische Dichte zu erreichen, während gleichzeitig die mechanischen Eigenschaften der Teile wie Feingussteile verbessert werden.
Die Unverträglichkeit von Pulvern, die mit einer HIP-Strategie verarbeitet werden, mit Schmelzprozessen
Heißisostatisches Pressen (HIP) ist ein Materialbehandlungsprozess, bei dem Wärme und Druck eingesetzt werden, um die physikalischen Eigenschaften eines Materials zu verbessern. Es wird typischerweise auf Metallen und Keramik durchgeführt. Wenn einer dieser Materialtypen Hitze und Druck ausgesetzt wird, verändern sich seine physikalischen Eigenschaften. HIP ist ein wirksames Verfahren zur Beseitigung von Fehlern in pulverbasierten additiv gefertigten Teilen und erzeugt 100 % dichtes Material mit verbesserten Ermüdungseigenschaften und Duktilität.
Sektoren HIP hat sich bewährt, seit es eine vergleichbare Größenordnung wie Guss- und Schmiedeteile erreicht hat und sich als wirtschaftlicher Konkurrent von Schmiede- und Gussteilen bei Anwendungen mit höheren Rohstoffkosten etabliert hat. Derzeit gibt es drei Haupt-HIP-Sektoren: Öl und Gas, Energieerzeugung und Luft- und Raumfahrt. Die Herstellung eines PM-HIP-Bauteils ist schlanker und kürzer als die üblichen konventionellen metallurgischen Prozesse. Die Kosten für HIP im Verhältnis zu den Energie- und Materialkosten sind in den letzten zwei Jahrzehnten um 65 % gesunken.
Einleitung Heißisostatisches Pressen (HIP) ist ein Verfahren zur Verdichtung von Pulvern oder Guss- und Sinterteilen in einem Ofen bei hohem Druck (100–200 MPa) und bei Temperaturen von 900 bis 1250 °C, beispielsweise für Stähle und Superlegierungen. Der Gasdruck wirkt gleichmäßig in alle Richtungen und sorgt so für isotrope Eigenschaften und eine 100-prozentige Verdichtung. Es bietet viele Vorteile und ist in vielen Anwendungen zu einer praktikablen und leistungsstarken Alternative zu herkömmlichen Verfahren wie Schmieden, Gießen und Bearbeiten geworden.
Sintern/Pulvermetallurgie: Hot Isostatic Pressing (HIP)-Technologie
Das heißisostatische Pressen hat sich im Laufe der letzten 50 Jahre vom Forschungslabor zur Serienproduktion entwickelt. Die Zukunft dieser Technologie sieht rosig aus, da die Nachfrage nach verbesserten Materialeigenschaften, der Verwendung von Pulvermaterialien und der Wunsch, endkonturnahe oder endkonturnahe Teile herzustellen, zunimmt.
Widerstandsbeheizte Ofentemperaturquelle im Inneren des Gefäßes
Das HIP-Verfahren, ursprünglich als Gasdruckbonden bekannt, wurde 1955 im Labor des Battelle Memorial Institute in Columbus, Ohio, entwickelt. Die ursprüngliche Anwendung war die Diffusionsbindungsbeschichtung von Zirkonium mit Zirkonium-Uran-Legierungen für Kernbrennstoffelemente. Etwa zur gleichen Zeit nutzte ASEA-Schweden die isostatische Druckanwendung, um die ersten synthetischen Diamanten zu verdichten. Heißisostatisches Pressen (HIP) ist ein Herstellungsverfahren, mit dem die Porosität von Metallen verringert und die Dichte vieler Keramikmaterialien erhöht wird. Dadurch werden die mechanischen Eigenschaften und die Verarbeitbarkeit des Materials verbessert.
Was ist heißisostatisches Pressen (HIP)?
Unter Heißisostatischem Pressen (HIP) oder „Hipping“ versteht man die gleichzeitige Anwendung von Hitze und hohem Druck auf Materialien. Dieses Verfahren ist ideal, um die Eigenschaften Ihres additiv gefertigten Produkts zu verbessern, indem die Porosität bis zu 100 % entfernt wird.
Dieses Verfahren wird bereits heute bei der Verbesserung additiv gefertigter Produkte eingesetzt. Nach Hipp'ing ist das Ergebnis die Beseitigung innerer Hohlräume (dh Porosität) und eine verbesserte Mikrostruktur, was zu enorm verbesserten mechanischen Eigenschaften führt. HIP kann auf eine Vielzahl von Legierungen angewendet werden, darunter Titan, Stähle, Aluminium, Kupfer und Magnesium.
Die Möglichkeit der einstufigen Vorverarbeitung von Konstruktionen durch additive Fertigung mit mehreren Materialien
Die potenziellen Vorteile der additiven Fertigung mit mehreren Materialien sowohl in CIP- als auch in HIP-Prozessen
Die additive Fertigung aus mehreren Materialien bietet eine Reihe potenzieller Vorteile sowohl bei den Prozessen „Konsolidierung durch Isostatisches Pressen“ (CIP) als auch „Hot Isostatic Pressing“ (HIP). Durch den Einsatz selektiver Pulverabscheidung kann dieser Ansatz die Lücke zwischen neuen additiven Fertigungstechnologien und traditionellen Fertigungsmethoden für High-End-Komponenten schließen. Durch die Konsolidierung von Teilen mithilfe etablierter Technologie können Bedenken hinsichtlich der Qualität und Zuverlässigkeit von AM-hergestellten Artikeln ausgeräumt werden.
Einer der Hauptvorteile der additiven Fertigung mit mehreren Materialien ist die Senkung der Herstellungskosten. Mit erhöhter Teilekomplexität, weniger Bearbeitungsschritten und kürzerer Zeit können Hersteller Kosteneinsparungen erzielen. Dies ist insbesondere bei der Herstellung von Kleinserien oder Prototypen von Vorteil, bei denen es auf Effizienz und Wirtschaftlichkeit ankommt.
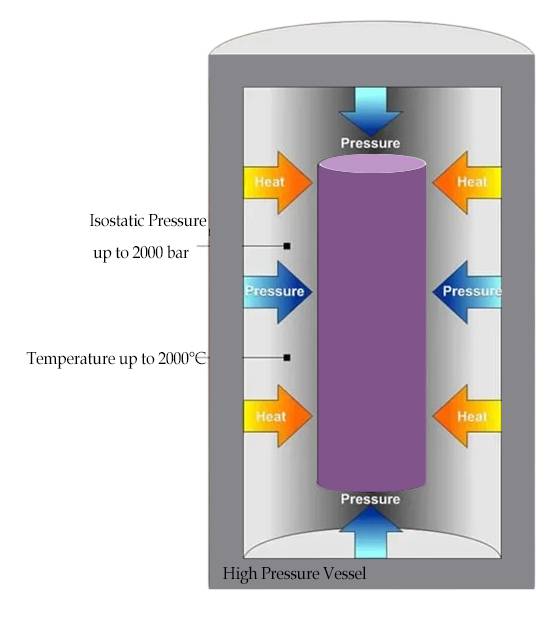
Die potenzielle Senkung der Herstellungskosten bei erhöhter Teilekomplexität, weniger Verarbeitungsschritten und weniger Zeitaufwand
Der Einsatz der additiven Fertigung mit mehreren Materialien kann zu einer Senkung der Herstellungskosten führen. Traditionelle subtraktive Fertigungsmethoden weisen geometrische Grenzen auf, die bei der additiven Fertigung nicht mehr gelten. Dadurch können komplexe Formen und Designs geschaffen werden, ohne dass die Produktionskosten wesentlich steigen. Darüber hinaus können die Kosten durch die Möglichkeit, mehrere Versionen desselben Produkts zu erstellen, ohne die Produktionskosten zu variieren, weiter gesenkt werden.
Ein weiterer wesentlicher Vorteil der Multimaterial-Additiv-Herstellung
cturing ist die drastische Reduzierung von Verarbeitungsabfällen. Durch das schrittweise Hinzufügen von Material, bis das gewünschte Objekt entsteht, entsteht im Vergleich zu herkömmlichen subtraktiven Fertigungsmethoden nur minimaler Abfall. Dies senkt nicht nur die Kosten, sondern trägt auch zu einem nachhaltigeren Herstellungsprozess bei.
Die Welt der additiven Metallfertigung erlebt einen deutlichen Anstieg des Einsatzes von Methoden wie Metal Injection Molding (MIM), Binder Jetting (BJ) und Fused Deposition Modeling (FDM). Diese Methoden bieten einzigartige Vorteile hinsichtlich Kosten, Designflexibilität und Materialeigenschaften.

Bei der additiven Fertigung von Metallen ist die thermische Entbinderung ein entscheidender Prozess nach dem Drucken. Dabei werden Bindemittel und andere Zusatzstoffe entfernt, um ein vollständig dichtes Metallteil zu erhalten. Um die gewünschten mechanischen Eigenschaften und Maßgenauigkeit zu erreichen, ist die ordnungsgemäße Entbinderung von Teilen, die durch additive Metallfertigung hergestellt werden, von entscheidender Bedeutung.
Sowohl der CIP- als auch der HIP-Prozess nutzen Multimaterial-Konstrukte. Bei CIP werden Polymerschalen mit Keramikpulvern verwendet, während bei HIP geschweißte Gehäuse aus Weichstahlblech mit hochwertigen pulvermetallurgischen Legierungen zum Einsatz kommen. Diese Methoden bieten die Möglichkeit einer einstufigen Vorverarbeitung von Konstrukten mittels additiver Fertigung aus mehreren Materialien.
Dieser Ansatz ist besonders bei der Herstellung von Kleinserien oder Prototypen von Vorteil, da er eine höhere Teilekomplexität mit weniger Bearbeitungsschritten und weniger Zeitaufwand ermöglicht. Durch die Nutzung der Vorteile der additiven Fertigung mit mehreren Materialien können Hersteller eine höhere Effizienz und Kosteneffizienz in ihren Produktionsprozessen erzielen.
Die industrielle Basis für das HIP-Verfahren wächst aufgrund der wachsenden Nachfrage nach verbesserten Materialeigenschaften und der Verwendung von Pulvermaterialien rasant. Darüber hinaus machen Fortschritte bei der HIP-Ausrüstung, kürzere Verarbeitungszeiten und verbesserte Wirtschaftlichkeit das HIP-Verfahren zu einer praktikablen Wahl für eine Vielzahl von Materialien. Dies verstärkt das Potenzial für die einstufige Vorverarbeitung von Konstrukten durch additive Fertigung mit mehreren Materialien weiter.
Zusammenfassend lässt sich sagen, dass die additive Fertigung mit mehreren Materialien erhebliche Möglichkeiten zur Effizienzsteigerung, Kostensenkung und Erzielung komplexer Designs sowohl im CIP- als auch im HIP-Prozess bietet. Durch die Nutzung der Vorteile dieser Technologie können Hersteller an der Spitze der Innovation bleiben und den Anforderungen des heutigen wettbewerbsintensiven Marktes gerecht werden.
Der Einsatz der selektiven Abscheidungstechnologie von Kintek beim isostatischen Pressen
Die gleichzeitige Abscheidung unterschiedlicher Materialien
Isostatisches Pressen ist eine Methode zum Verdichten von Pulver in einem Elastomerbehälter, der in eine Flüssigkeit unter hohem Druck getaucht ist. Traditionell wird dieses Verfahren vor allem für Keramik und Metalle eingesetzt. Jüngste Fortschritte in der selektiven Abscheidungstechnologie, wie beispielsweise der innovative Ansatz von Kintek, haben jedoch neue Möglichkeiten für das isostatische Pressen eröffnet.
Die selektive Abscheidungstechnologie von KinTek ermöglicht die gleichzeitige Abscheidung verschiedener Materialien. Dies bedeutet, dass anstelle der Verwendung eines einzigen Pulvermaterials mehrere Materialien Schicht für Schicht aufgetragen werden können. Dies eröffnet eine Reihe von Möglichkeiten zur Herstellung komplexer Teile aus mehreren Materialien mit einzigartigen Eigenschaften.
Es entsteht eine geformte, flüssigkeitsdichte Polymerhülle, die das unverdichtete Keramikpulver umgibt
Einer der Hauptvorteile der selektiven Abscheidungstechnologie von KinTek beim isostatischen Pressen ist die Möglichkeit, eine geformte, flüssigkeitsdichte Polymerhülle zu erzeugen, die das unverdichtete Keramikpulver umgibt. Diese Hülle fungiert als Barriere und verhindert, dass sich das Keramikpulver während des isostatischen Pressvorgangs verteilt.
Durch die selektive Abscheidung zur Erzeugung dieser Schale ist es möglich, auch bei Teilen mit großem Höhen-/Durchmesserverhältnis eine gleichmäßige Gründichte zu erreichen. Dies ist besonders wichtig für Anwendungen, bei denen die Maßkontrolle von entscheidender Bedeutung ist, beispielsweise in der Luft- und Raumfahrt- oder Automobilindustrie.
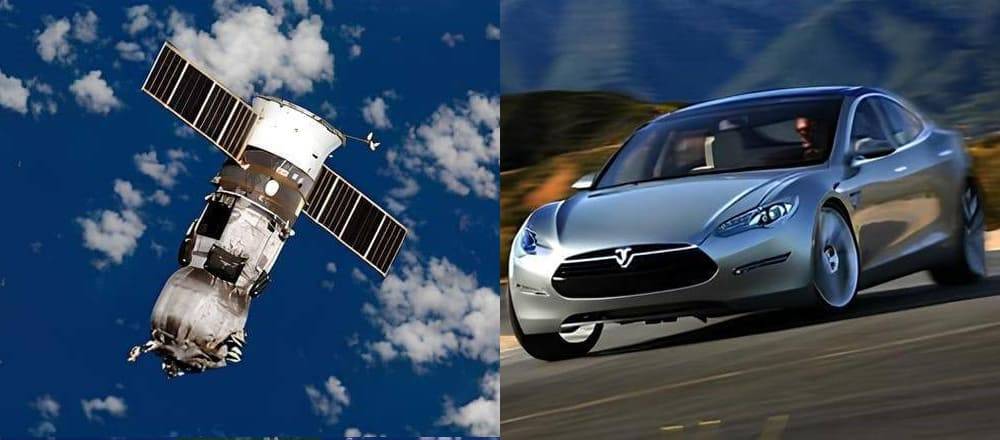
Der einfache Transport und die Platzierung des Konstrukts in einer CIP-Maschine
Ein weiterer Vorteil der selektiven Abscheidungstechnologie von ist der einfache Transport und die einfache Platzierung des Konstrukts in einer kaltisostatischen Pressmaschine (CIP). Das Konstrukt, bestehend aus der geformten Polymerhülle, die mit unverdichtetem Keramikpulver gefüllt ist, lässt sich leicht handhaben und in der CIP-Maschine positionieren.
Dieser einfache Transport und die einfache Platzierung erhöhen nicht nur die Effizienz, sondern verringern auch das Risiko einer Beschädigung des Konstrukts während des Ladevorgangs. Es ermöglicht einen effizienteren und zuverlässigeren isostatischen Pressprozess und gewährleistet konsistente Ergebnisse und qualitativ hochwertige Teile.
Zusammenfassend lässt sich sagen, dass die selektive Abscheidungstechnologie von 's spannende Möglichkeiten für das isostatische Pressen bietet. Die gleichzeitige Abscheidung verschiedener Materialien, die Schaffung einer geformten, flüssigkeitsdichten Polymerhülle und der einfache Transport und die Platzierung des Konstrukts in einer CIP-Maschine tragen alle zur Weiterentwicklung dieses Herstellungsprozesses bei. Durch Weiterentwicklung und Verfeinerung hat die Technologie von das Potenzial, die Art und Weise, wie wir komplexe Teile aus mehreren Materialien herstellen, mit verbesserter Maßkontrolle und Leistung zu revolutionieren.
Das Potenzial eines ähnlichen Ansatzes für Teile, die mit HIP verarbeitet werden
Gemeinsames Auftragen eines Weichwerkzeugstahls und einer PM-spezifischen Legierung mithilfe eines selektiven Pulverauftragssystems
Für Teile, die mit HIP bearbeitet werden müssen, könnte ein ähnlicher Ansatz verwendet werden. Ein weicher Werkzeugstahl und eine PM-spezifische Legierung könnten mithilfe eines selektiven Pulverabscheidungssystems gemeinsam abgeschieden werden, und nur die Außenseite des Werkzeugstahls müsste konsolidiert werden. Da die PM-Legierung nicht geschmolzen werden muss, ist es leicht vorstellbar, ein vorgefülltes Gehäuse mit Rohrleitungen herzustellen, das eine Schweißnahtversiegelung dieses Gehäuses unter Vakuum ermöglichen würde, genau wie bei HIP-produzierten Teilen, die aus geschweißtem Blech hergestellt werden. Der Rest der HIP-Verarbeitung kann dann dem herkömmlichen Weg folgen.
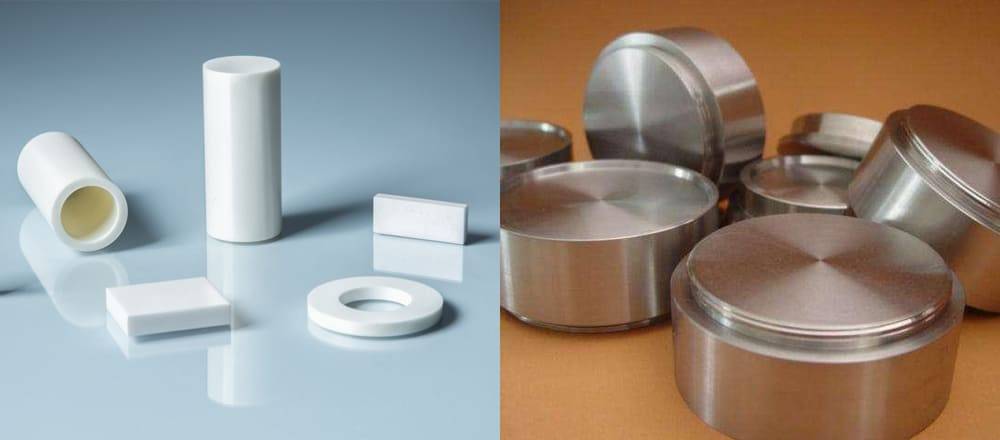
Herstellung einer vorgefüllten Hülle mit Rohrleitungen zur Schweißnahtversiegelung unter Vakuum
Ein ähnlicher Ansatz zur HIP-Verarbeitung kann für Teile verwendet werden, die eine HIP-Behandlung erfordern. Durch die gleichzeitige Abscheidung eines Weichwerkzeugstahls und einer PM-spezifischen Legierung mithilfe eines selektiven Pulverabscheidungssystems ist es möglich, ein vorgefülltes Gehäuse mit Rohrleitungen für die Schweißnahtabdichtung unter Vakuum herzustellen. Dies ermöglicht die Konsolidierung der Außenseite des Werkzeugstahls und bewahrt gleichzeitig die Integrität der PM-Legierung. Die weitere HIP-Verarbeitung kann dann wie gewohnt erfolgen.
Der traditionelle Weg der restlichen HIP-Verarbeitung
Nach der gemeinsamen Abscheidung eines Weichwerkzeugstahls und einer PM-spezifischen Legierung mithilfe eines selektiven Pulverabscheidungssystems und der Konsolidierung der Außenseite des Werkzeugstahls kann der Rest der HIP-Verarbeitung dem traditionellen Weg folgen. Dazu gehört der Einsatz fortschrittlicher Kühltechnologie, um die Verarbeitungsökonomie zu steigern und die Endmaterialeigenschaften zu verbessern. Durch die Möglichkeit, mit Argongas und internen Kühlsystemen schneller abzukühlen, können HIP-Zyklen erheblich verkürzt werden, was zu Kosteneinsparungen und einer verbesserten Teilequalität führt.
Der Einsatz von HIP hat sich in verschiedenen Branchen als äußerst vorteilhaft erwiesen. HIP kann zur Herstellung einer breiten Palette von Komponenten verwendet werden, einschließlich großer und massiver endkonturnaher Metallkomponenten wie Öl- und Gasteile und endkonturnahe Laufräder. Es eignet sich auch für die Herstellung kleiner PM-HSS-Schneidwerkzeuge und winziger Teile wie Zahnspangen. Das Verfahren hat sich im Laufe der Jahre zu einer leistungsstarken, qualitativ hochwertigen und kostengünstigen Methode zur Herstellung von Metall- und Keramikbauteilen entwickelt.
HIPing bietet zahlreiche Vorteile, darunter verbesserte mechanische Eigenschaften, weniger Ausschuss, minimierte Bearbeitung und die Möglichkeit, alte Teile zu erneuern. Es kann auf eine Vielzahl von Materialien angewendet werden, darunter Aluminium, Stahl, Edelstahl, Superlegierungen, Titan und Keramik. Mit der Weiterentwicklung der HIP-Ausrüstung und der Verarbeitungszeiten wird das HIP-Verfahren für eine Vielzahl von Materialien und Anwendungen immer beliebter.
Zusammenfassend lässt sich sagen, dass ein ähnlicher Ansatz zur HIP-Verarbeitung auf Teile angewendet werden kann, die eine HIP-Behandlung erfordern. Durch die gleichzeitige Abscheidung eines Weichwerkzeugstahls und einer PM-spezifischen Legierung mithilfe eines selektiven Pulverabscheidungssystems ist es möglich, vorgefüllte Gehäuse mit Rohrleitungen für die Schweißnahtabdichtung unter Vakuum herzustellen. Dieser Ansatz bietet zahlreiche Vorteile, darunter eine verbesserte Teilequalität, kürzere Bearbeitungszeit und Kosteneinsparungen. Mit den kontinuierlichen Fortschritten in der HIP-Technologie wächst das Potenzial für den Einsatz dieses Ansatzes in verschiedenen Branchen immer weiter.
Fazit: Die Brücke der selektiven Pulverabscheidung zwischen neuer additiver Fertigung und traditioneller Fertigung
Das Potenzial der selektiven Pulverabscheidung, eine Brücke zwischen neuen additiven Fertigungstechnologien und der traditionellen Herstellung hochwertiger Komponenten zu schlagen
Die selektive Pulverabscheidung hat das Potenzial, die Lücke zwischen der neuen additiven Fertigungstechnologie (AM) und der traditionellen Herstellung hochwertiger Komponenten zu schließen. Dieser Ansatz nutzt die wohlverstandenen Druckbehandlungs- und Temperaturwechselprozesse, die bereits in der Industrie verfügbar sind. Durch die Verwendung dieser etablierten Methoden zur Konsolidierung von mittels AM hergestellten Teilen kann dies dazu beitragen, die Bedenken der Industrie hinsichtlich der mit dieser neuen Technologie hergestellten Artikel zu lindern.
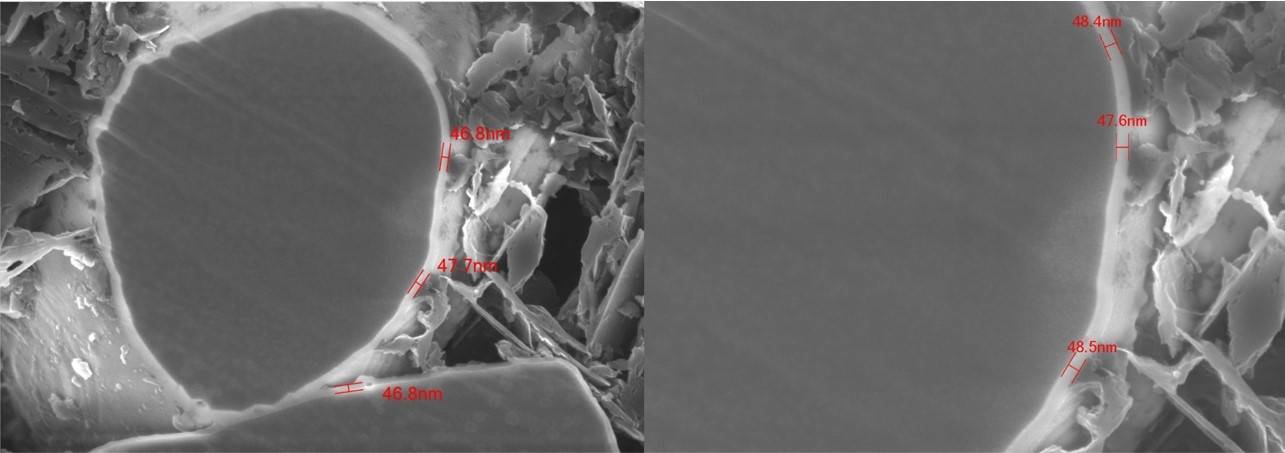
Durch diesen Ansatz besteht die Möglichkeit, die Besorgnis der Industrie hinsichtlich mittels additiver Fertigung hergestellter Artikel zu lindern
Eines der Hauptanliegen der Branche bei der additiven Fertigung ist die Qualität und Zuverlässigkeit der Endprodukte. Traditionelle Herstellungsmethoden wurden über Jahrzehnte verfeinert und es besteht ein gewisses Maß an Vertrauen in die durch diese Prozesse hergestellten Komponenten.
Durch die selektive Pulverabscheidung können die durch AM erzeugten Teile mit der neuen Technologie geformt, aber mit den seit langem etablierten Methoden konsolidiert werden. Dies kann dazu beitragen, die Ängste vor dem Einsatz von AM für High-End-Komponenten etwas zu lindern.
Zusammenfassend lässt sich sagen, dass die selektive Pulverabscheidung eine vielversprechende Lösung darstellt, um die Lücke zwischen neuer additiver Fertigungstechnologie und traditioneller Fertigung zu schließen. Durch die Nutzung der etablierten Prozesse und Techniken der traditionellen Fertigung kann es dazu beitragen, Vertrauen in die durch additive Fertigung hergestellten Komponenten aufzubauen.
Kontaktieren Sie uns für eine kostenlose Beratung
Die Produkte und Dienstleistungen von KINTEK LAB SOLUTION werden von Kunden auf der ganzen Welt anerkannt. Unsere Mitarbeiter helfen Ihnen gerne bei allen Fragen weiter. Kontaktieren Sie uns für eine kostenlose Beratung und sprechen Sie mit einem Produktspezialisten, um die am besten geeignete Lösung für Ihre Anwendungsanforderungen zu finden!