Die Beschichtung mit diamantähnlichem Kohlenstoff (DLC) wird mit fortschrittlichen Abscheidetechniken aufgebracht, die eine starke, dauerhafte und leistungsstarke Beschichtung gewährleisten.Zu den gebräuchlichsten Verfahren gehören die physikalische Gasphasenabscheidung (PVD) und die chemische Gasphasenabscheidung (CVD), wobei es auch Varianten wie die Hochfrequenz-Plasma-unterstützte CVD (RF PECVD) und die Heißdraht-CVD gibt.Bei diesen Verfahren wird in einer Vakuumkammer eine kontrollierte Umgebung geschaffen, in der die Kohlenstoffatome aktiviert und auf dem Substrat abgeschieden werden.Die Wahl des Verfahrens hängt vom Substratmaterial, den gewünschten Schichteigenschaften und den Anwendungsanforderungen ab.DLC-Beschichtungen sind in der Regel dünn (0,5 bis 2,5 Mikrometer) und bieten eine hervorragende Verschleißfestigkeit, geringe Reibung und eine längere Lebensdauer.
Die wichtigsten Punkte erklärt:
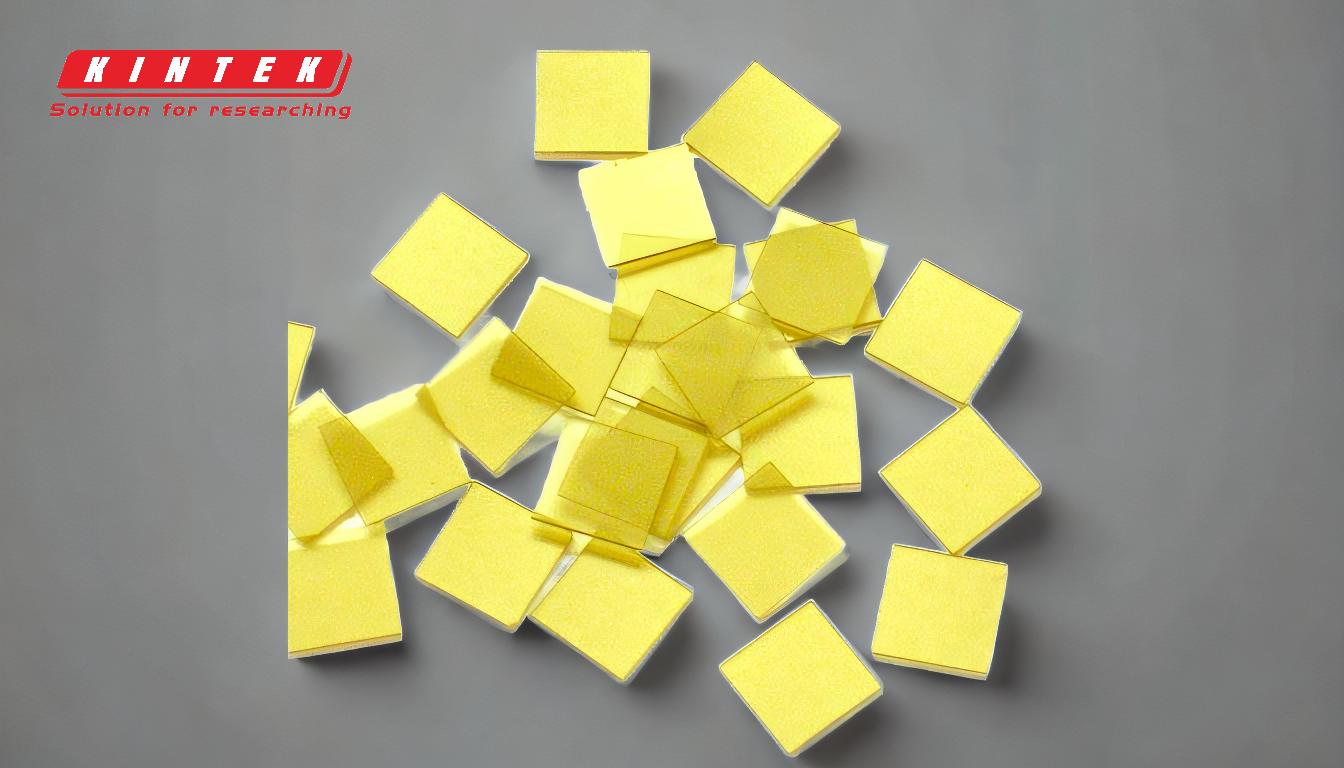
-
Überblick über die Anwendung von DLC-Beschichtungen
- DLC-Beschichtungen werden mit Hilfe fortschrittlicher Abscheidetechniken aufgebracht, um eine dünne, dauerhafte Schicht aus Kohlenstoff mit einem hohen Anteil an sp3-Bindungen zu erzeugen.
- Der Beschichtungsprozess wird auf das Substratmaterial und die vorgesehene Anwendung zugeschnitten, um eine optimale Leistung zu gewährleisten.
-
Gängige Beschichtungsmethoden
-
Physikalische Gasphasenabscheidung (PVD):
- Bei diesem Verfahren wird ein Ausgangsmaterial verdampft und auf dem Substrat kondensiert.
- Geeignet für das Aufbringen von DLC-Beschichtungen auf Hartmetallwerkzeuge mit einer typischen Dicke von 0,5 bis 2,5 Mikrometern.
- Zu den Vorteilen gehören die präzise Kontrolle der Schichtdicke und der Gleichmäßigkeit.
-
Chemische Gasphasenabscheidung (CVD):
- Bei diesem Verfahren werden Kohlenstoffatome aus einer Gasphase (z. B. Wasserstoff und Methan) auf das Substrat aufgebracht.
- Zu den gängigen Verfahren gehören Heißdraht-CVD, Hochfrequenz-Plasma-CVD (RF PECVD) und Mikrowellen-Plasma-CVD (MPCVD).
- Erfordert hohe Temperaturen (über 750 °C), um die Gasmoleküle zu aktivieren und einen Diamantfilm zu bilden.
-
Physikalische Gasphasenabscheidung (PVD):
-
Schritt-für-Schritt-Verfahren für die CVD-Beschichtung
-
Vorbereitung:
- Das Substrat (z. B. Hartmetallwerkzeuge) wird gereinigt und vorbereitet, um eine gute Haftung der Beschichtung zu gewährleisten.
-
Einlegen in die Kammer:
- Die vorbereiteten Werkzeuge werden in eine Vakuumkammer mit Wasserstoff und Methangas gelegt.
-
Aktivierung der Gasmoleküle:
- Wolframdrähte, die auf über 2.300 °C erhitzt werden, liefern die Energie zum Aufbrechen der Gasmoleküle und erhitzen die Werkzeuge auf über 750 °C.
-
Abscheidung von Kohlenstoffatomen:
- Aktivierte Kohlenstoffatome rekombinieren auf der Werkzeugoberfläche und bilden einen reinen Diamantfilm.
-
Abkühlung und Entnahme:
- Nach der Abscheidung werden die Werkzeuge abgekühlt und aus der Kammer entnommen, damit sie wieder verwendet werden können.
-
Vorbereitung:
-
Vorteile der verschiedenen Verfahren
-
PVD:
- Niedrigere Verarbeitungstemperaturen, daher geeignet für temperaturempfindliche Substrate.
- Hohe Präzision und Gleichmäßigkeit der Schichtdicke.
-
CVD:
- Erzeugt hochwertige, reine Diamantschichten mit hervorragender Haftung.
- Ideal für Hochtemperaturanwendungen und Substrate, die extremen Bedingungen standhalten können.
-
PVD:
-
Anwendungen von DLC-Beschichtungen
-
Schneidwerkzeuge:
- Erhöht die Verschleißfestigkeit und verlängert die Lebensdauer der Werkzeuge.
-
Automobilkomponenten:
- Verringert die Reibung und verbessert die Kraftstoffeffizienz in Motorenteilen.
-
Medizinische Geräte:
- Bietet Biokompatibilität und Verschleißfestigkeit für chirurgische Instrumente.
-
Elektronik:
- Verbessert die Haltbarkeit und Leistung von Komponenten wie Festplatten und Sensoren.
-
Schneidwerkzeuge:
-
Überlegungen für Einkäufer von Geräten und Verbrauchsmaterialien
-
Kompatibilität des Substrats:
- Stellen Sie sicher, dass die gewählte Methode mit dem Substratmaterial kompatibel ist (z. B. Hartmetall, Stahl oder Keramik).
-
Beschichtungsdicke und Gleichmäßigkeit:
- Beurteilen Sie die erforderliche Dicke und Gleichmäßigkeit für die jeweilige Anwendung.
-
Kosten und Skalierbarkeit:
- Berücksichtigen Sie die Kosteneffizienz und Skalierbarkeit der gewählten Methode für die Produktion in großem Maßstab.
-
Umwelt- und Sicherheitsfaktoren:
- Bewerten Sie die Umweltauswirkungen und Sicherheitsanforderungen des Beschichtungsprozesses.
-
Kompatibilität des Substrats:
Durch die Kenntnis dieser Schlüsselpunkte können Käufer von Anlagen und Verbrauchsmaterialien fundierte Entscheidungen über die beste DLC-Beschichtungsmethode für ihre spezifischen Anforderungen treffen und so optimale Leistung und Kosteneffizienz gewährleisten.
Zusammenfassende Tabelle:
Aspekt | Einzelheiten |
---|---|
Gängige Methoden | PVD, CVD (RF-PECVD, Heißfilament-CVD) |
Dicke der Beschichtung | 0,5 bis 2,5 Mikrometer |
Wichtigste Vorteile | Verschleißfestigkeit, geringe Reibung, Langlebigkeit |
Anwendungen | Schneidwerkzeuge, Automobilteile, medizinische Geräte, Elektronik |
Kompatibilität der Substrate | Hartmetall, Stahl, Keramiken |
Temperaturbereich | PVD:Niedrigere Temperaturen; CVD:Über 750°C |
Umwelt-Faktoren | Vakuumkammer, kontrollierte Gasumgebung |
Entdecken Sie die ideale DLC-Beschichtungslösung für Ihren Bedarf. Kontaktieren Sie unsere Experten noch heute !