Die PVD-Beschichtung (Physical Vapor Deposition) ist eine hochmoderne und dauerhafte Oberflächenveredelungstechnik, die die Härte, Verschleißfestigkeit und Lebensdauer von Werkstoffen deutlich erhöht.Sie ist besonders für ihre Fähigkeit bekannt, dünne, harte Beschichtungen mit einer Dicke von 0,5 bis 5 Mikrometern zu erzeugen, die auf Metalle wie Edelstahl aufgetragen werden.PVD-Beschichtungen sind viermal härter als Chrom, was sie außergewöhnlich kratz-, korrosions- und oxidationsbeständig macht.Dies macht sie ideal für Anwendungen in rauen Umgebungen, wie z. B. Automobilteile, Industriewerkzeuge und Küstenprojekte.Darüber hinaus sind PVD-Beschichtungen umweltfreundlich, arbeiten bei niedrigeren Temperaturen und eignen sich für Präzisionswerkzeuge und komplexe Bauteile, was sowohl praktische als auch ethische Vorteile gegenüber herkömmlichen Beschichtungsmethoden wie dem Verchromen bietet.
Die wichtigsten Punkte erklärt:
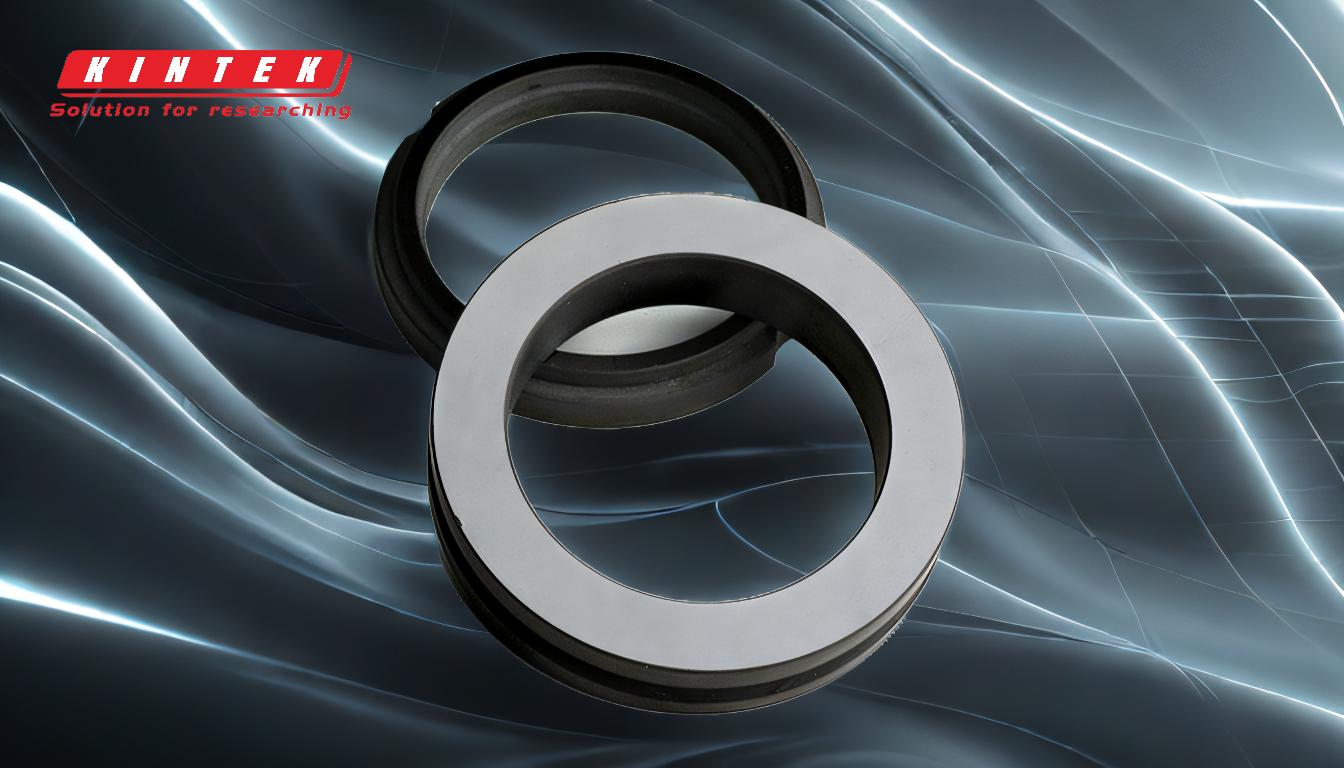
-
Härte von PVD-Beschichtungen:
- PVD-Beschichtungen sind viermal härter als Chrom und damit äußerst kratz- und verschleißfest.Diese Härte wird durch die Veränderung der Metalloberfläche auf molekularer Ebene während des Beschichtungsprozesses erreicht.
- Die Härte von PVD-Beschichtungen macht sie ideal für Anwendungen, die eine lange Lebensdauer erfordern, wie z. B. Schneidwerkzeuge, Automobilkomponenten und Industriemaschinen.
-
Dicke und Dauerhaftigkeit:
- PVD-Beschichtungen sind extrem dünn, in der Regel zwischen 0,5 und 5 Mikrometer.Trotz ihrer geringen Dicke bieten sie eine außergewöhnliche Haltbarkeit und Langlebigkeit.
- Die dünne Beschichtung bewahrt die Schärfe von Werkzeugen, wie z. B. Klingen, und reduziert die Schnittkraft und die Hitze während des Gebrauchs.
-
Widerstandsfähigkeit gegen Korrosion und Oxidation:
- PVD-Beschichtungen sind äußerst korrosions- und oxidationsbeständig und eignen sich daher für den Einsatz in rauen Umgebungen, z. B. in Küstenregionen oder in der Industrie.
- Diese Beständigkeit verlängert die Lebensdauer der beschichteten Produkte und verringert die Notwendigkeit eines häufigen Austauschs oder einer Wartung.
-
Ökologische und praktische Vorteile:
- Die PVD-Beschichtung ist eine umweltfreundliche Alternative zu herkömmlichen Verfahren wie dem Verchromen, bei dem giftige Nebenprodukte entstehen.
- Das Verfahren arbeitet mit niedrigeren Temperaturen (ca. 500 °C), wodurch das Risiko einer thermischen Beschädigung des Substrats verringert und die Materialverformung minimiert wird.
-
Vielseitigkeit der Anwendungen:
- PVD-Beschichtungen eignen sich für eine Vielzahl von Anwendungen, darunter Schneidwerkzeuge aus Schnellarbeitsstahl (HSS) und Hartmetall, Kunststoffspritzgussteile, Feinschneidwerkzeuge und optische Beschichtungen.
- Das Verfahren eignet sich sowohl für die Großserien- als auch für die Kleinserienfertigung und ist damit vielseitig in verschiedenen Branchen einsetzbar.
-
Vorteile gegenüber herkömmlichen Beschichtungen:
- PVD-Beschichtungen bieten im Vergleich zu herkömmlichen Beschichtungen wie Verchromung eine höhere Härte, Verschleißfestigkeit und Haltbarkeit.
- Die Druckspannung, die sich beim Abkühlen bildet, verhindert Rissbildung und Ausdehnung, wodurch PVD-Beschichtungen ideal für unterbrochene Schneidprozesse wie das Fräsen sind.
-
Betriebliche Effizienz:
- PVD-Beschichtungsanlagen sind computergesteuert und ermöglichen einen präzisen und gleichmäßigen Auftrag der Beschichtungen.Dies senkt die Produktionskosten und die Durchlaufzeit.
- Die hohe Abscheidegeschwindigkeit und die niedrige Abscheidetemperatur von PVD-Anlagen machen sie effizient und geeignet für die Beschichtung komplexer und präziser Werkzeuge.
Zusammenfassend lässt sich sagen, dass die PVD-Beschichtung eine hocheffektive und vielseitige Technik der Oberflächenveredelung ist, die eine überragende Härte, Haltbarkeit und Beständigkeit gegen Korrosion und Oxidation bietet.Ihre Vorteile für die Umwelt und ihre Fähigkeit, die Lebensdauer und Leistung von Produkten zu erhöhen, machen sie zu einer bevorzugten Wahl für eine breite Palette industrieller und gewerblicher Anwendungen.
Zusammenfassende Tabelle:
Aspekt | Einzelheiten |
---|---|
Härte | 4x härter als Chrom, ideal für dauerhafte Anwendungen. |
Schichtdicke | 0,5 bis 5 Mikrometer, dünn und dennoch sehr haltbar. |
Korrosionsbeständigkeit | Ausgezeichnete Korrosions- und Oxidationsbeständigkeit, geeignet für raue Umgebungen. |
Umweltverträglichkeit | Umweltfreundlich, arbeitet bei niedrigeren Temperaturen (≈500 °C). |
Anwendungen | Schneidwerkzeuge, Automobilteile, Industriemaschinen und vieles mehr. |
Verbessern Sie Ihre Produkte mit der überragenden Haltbarkeit von PVD-Beschichtungen. Kontaktieren Sie uns noch heute um mehr zu erfahren!