Die für die Herstellung von Biokohle benötigte Zeit hängt von mehreren Faktoren ab, unter anderem von der Art des Pyrolyseverfahrens (langsam oder schnell), dem verwendeten Ausgangsmaterial, der Erhitzungsrate, der Spitzentemperatur und der Verweilzeit.Die langsame Pyrolyse, die üblicherweise für die Herstellung von Biokohle verwendet wird, dauert aufgrund der niedrigen Erhitzungsraten und der längeren Verweilzeiten in der Regel mehrere Stunden.Auch die Prozessbedingungen, wie Temperatur und Feuchtigkeitsgehalt des Ausgangsmaterials, spielen eine wichtige Rolle bei der Bestimmung der Dauer.So können höhere Temperaturen und ein geringerer Feuchtigkeitsgehalt die benötigte Zeit verkürzen, während bestimmte Eigenschaften des Ausgangsmaterials Anpassungen des Prozesses erfordern können.Insgesamt ist die Herstellung von Biokohle ein flexibles Verfahren, das auf die jeweiligen Anforderungen zugeschnitten werden kann, aber je nach gewünschter Produktqualität und -ausbeute dauert es im Allgemeinen zwischen einigen Stunden und mehreren Stunden.
Die wichtigsten Punkte erklärt:
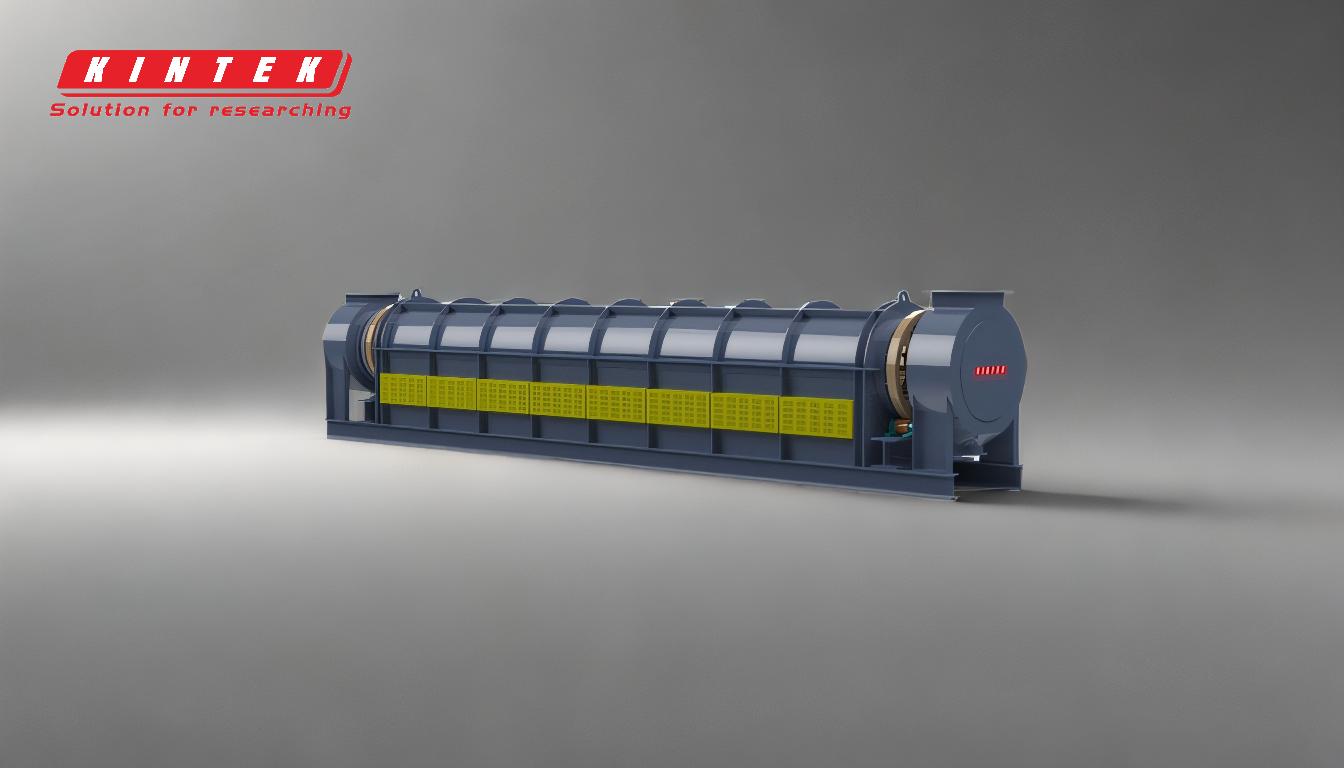
-
Art und Dauer der Pyrolyse:
- Die langsame Pyrolyse ist die gängigste Methode zur Herstellung von Biokohle und zeichnet sich durch niedrige Heizraten und lange Verweilzeiten aus.Dieser Prozess dauert in der Regel mehrere Stunden.
- Die Schnellpyrolyse hingegen ist für die Herstellung von flüssigem Bioöl konzipiert und arbeitet mit sehr viel kürzeren Verweilzeiten (Sekunden bis Minuten), so dass sie für die Herstellung von Biokohle nicht geeignet ist.
-
Heizrate und Temperatur:
- Die Erhitzungsgeschwindigkeit hat einen erheblichen Einfluss auf die Dauer der Biokohleproduktion.Bei der langsamen Pyrolyse werden Erhitzungsraten von 5-30 °C pro Minute verwendet, wodurch sich die Prozessdauer verlängert.
- Höhere Spitzentemperaturen (z.B. 400-700°C) können den Pyrolyseprozess beschleunigen, müssen aber sorgfältig kontrolliert werden, um eine Verschlechterung der Biokohlequalität zu vermeiden.
-
Verweilzeit:
- Die Verweilzeit gibt an, wie lange die Biomasse den Pyrolysebedingungen ausgesetzt ist.Bei der langsamen Pyrolyse kann die Verweilzeit zwischen 30 Minuten und mehreren Stunden liegen, je nach Ausgangsmaterial und gewünschten Biokohleeigenschaften.
- Längere Verweilzeiten werden häufig verwendet, um eine vollständige Verkohlung zu gewährleisten und die Stabilität der Biokohle zu verbessern.
-
Merkmale des Ausgangsmaterials:
- Die Art des Biomasse-Rohstoffs (z. B. Holz, landwirtschaftliche Abfälle oder Gülle) beeinflusst die Dauer der Pyrolyse.Einsatzstoffe mit einem höheren Ligningehalt, wie z. B. Holz, erfordern in der Regel längere Verarbeitungszeiten.
- Der Feuchtigkeitsgehalt des Ausgangsmaterials spielt ebenfalls eine Rolle; trockenere Ausgangsmaterialien pyrolysieren schneller, was die Gesamtproduktionszeit verkürzt.
-
Prozessbedingungen:
- Die höchste Behandlungstemperatur (HTT) und die Verweilzeit sind kritische Variablen, die sowohl den Ertrag als auch die Eigenschaften von Biokohle beeinflussen.Eine höhere HTT kann die Produktionszeit verkürzen, kann aber die Eigenschaften der Biokohle verändern.
- Druck und Gasumgebung (z. B. inert oder reaktiv) können sich ebenfalls auf den Pyrolyseprozess auswirken, obwohl diese Faktoren weniger bedeutend sind als Temperatur und Verweilzeit.
-
Optimierung für Ausbeute und Qualität:
- Um die Ausbeute an Biokohle zu maximieren, wird eine langsame Pyrolyse bei niedrigeren Temperaturen (300-500 °C) und langsameren Erhitzungsraten durchgeführt.Dieser Ansatz gewährleistet einen höheren Kohlenstoffgehalt im Endprodukt, verlängert aber die Produktionszeit.
- Die Anpassung der Prozessbedingungen, wie z. B. die Reduzierung des Feuchtigkeitsgehalts oder die Optimierung der HTT, kann dazu beitragen, die Produktionszeit mit den gewünschten Biokohleeigenschaften in Einklang zu bringen.
-
Variabilität der Produktionszeit:
- Die große Bandbreite an Rohstoffen und Prozessbedingungen bedeutet, dass die Produktionszeiten für Biokohle erheblich variieren können.So kann die Herstellung von Biokohle aus Holzspänen 2 bis 4 Stunden dauern, während landwirtschaftliche Rückstände aufgrund ihrer geringeren Dichte und ihres geringeren Feuchtigkeitsgehalts weniger Zeit benötigen.
Durch das Verständnis und die Kontrolle dieser Faktoren können die Hersteller den Prozess der Biokohleherstellung optimieren, um das gewünschte Gleichgewicht zwischen Produktionszeit, Ertrag und Produktqualität zu erreichen.
Zusammenfassende Tabelle:
Faktor | Einfluss auf die Produktionszeit |
---|---|
Pyrolyse-Typ | Langsame Pyrolyse: mehrere Stunden; schnelle Pyrolyse: Sekunden bis Minuten (nicht ideal für Biokohle). |
Erhitzungsrate | Langsame Raten (5-30°C/min) verlängern die Zeit; höhere Raten verkürzen die Zeit, können aber die Qualität beeinträchtigen. |
Verweilzeit | Längere Zeiten (30 Minuten bis mehrere Stunden) gewährleisten eine vollständige Karbonisierung und Stabilität. |
Merkmale des Ausgangsmaterials | Ein hoher Ligningehalt (z. B. Holz) erfordert eine längere Verarbeitung; trockenere Rohstoffe verkürzen die Zeit. |
Prozessbedingungen | Höhere Temperaturen verkürzen die Zeit; Feuchtigkeitsgehalt und HTT-Anpassungen optimieren die Produktion. |
Ausbeute vs. Qualität | Niedrigere Temperaturen (300-500°C) maximieren die Ausbeute, erhöhen aber den Zeitaufwand; Gleichgewicht mit gewünschten Eigenschaften. |
Sind Sie bereit, Ihr Biokohle-Produktionsverfahren zu optimieren? Kontaktieren Sie noch heute unsere Experten für maßgeschneiderte Lösungen!