Sputtern ist eine vielseitige Technik der physikalischen Gasphasenabscheidung (PVD), mit der dünne Materialschichten auf Substrate aufgebracht werden.Dabei werden Atome aus einem festen Zielmaterial durch den Beschuss mit energiereichen Ionen ausgestoßen, in der Regel in einer Vakuumumgebung.Das Verfahren kann je nach Art der Ionenerzeugung, der Art der Stromversorgung und der spezifischen Anwendungen in verschiedene Typen eingeteilt werden.Zu diesen Typen gehören DC-Diodensputtern, RF-Sputtern, Magnetronsputtern, Ionenstrahlsputtern, reaktives Sputtern und andere.Jeder Typ hat einzigartige Eigenschaften, Vor- und Nachteile und eignet sich daher für unterschiedliche Anwendungen in Branchen wie Halbleiter, Optik und Beschichtungen.
Die wichtigsten Punkte erklärt:
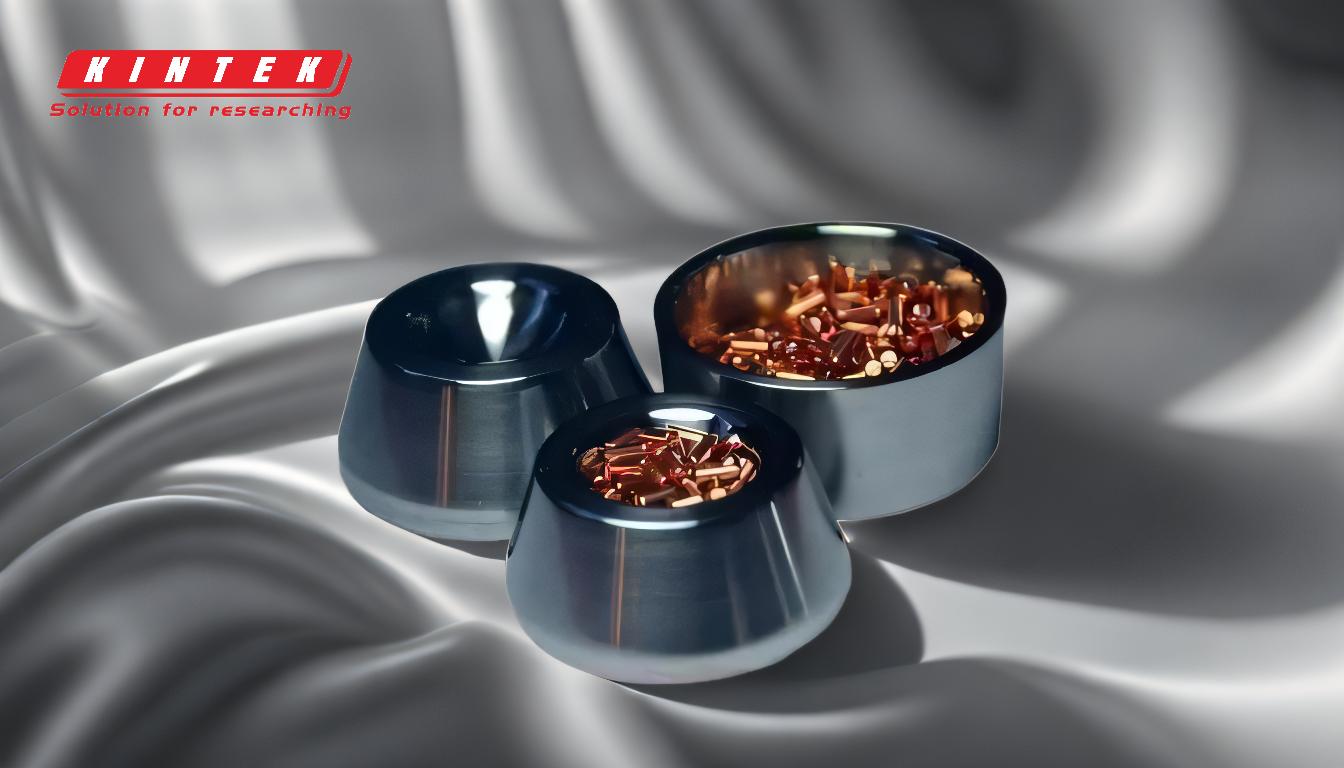
-
DC-Dioden-Sputtern
- Das Gleichstromdiodensputtern ist eine der einfachsten und ältesten Formen des Sputterns.
- Dabei wird eine Gleichspannung (normalerweise 500-1000 V) verwendet, um ein Argon-Niederdruckplasma zwischen dem Target (Kathode) und dem Substrat (Anode) zu zünden.
- Positive Argon-Ionen beschießen das Target und schleudern Atome aus, die dann auf das Substrat wandern und zu einem dünnen Film kondensieren.
- Vorteile:Einfacher Aufbau, kostengünstig und für leitfähige Materialien geeignet.
- Benachteiligungen:Begrenzt auf leitfähige Targets, geringere Abscheidungsraten und mögliche Erwärmung des Substrats.
-
RF-Sputtern
- Beim RF-Sputtern wird ein hochfrequentes Wechselfeld (typischerweise 13,56 MHz) anstelle eines elektrischen Gleichfelds verwendet.
- Diese Methode ermöglicht das Sputtern von isolierenden Materialien (z. B. Keramik und Halbleiter), da sie die Ansammlung von Ladungen auf dem Target verhindert.
- Vorteile:Abscheidung von Isoliermaterialien, geringere Erwärmung des Substrats und höhere Sputterraten bei niedrigerem Druck.
- Nachteile:Komplexere Ausrüstung und höhere Kosten im Vergleich zum DC-Sputtern.
-
Magnetron-Zerstäubung
- Beim Magnetronsputtern werden Magnetfelder eingesetzt, um die Ionisierung des Sputtergases zu verbessern und die Abscheidungsrate zu erhöhen.
-
Zu den Typen gehören:
- DC-Magnetron-Sputtern:Verwendet eine Gleichstromversorgung und ist für leitende Materialien geeignet.
- Gepulste DC-Doppelmagnetronzerstäubung:Wechselt die Polarität des Targets, um Lichtbogenbildung zu verhindern, ideal für reaktives Sputtern.
- Rotierender Magnet oder rotierendes Target DC-Magnetron-Sputtering:Verbessert die Zielnutzung und die Gleichmäßigkeit der Ablagerung.
- Vorteile:Hohe Abscheideraten, bessere Materialausnutzung und bessere Schichtgleichmäßigkeit.
- Nachteile:Erfordert eine präzise Steuerung der Magnetfelder und kann teurer sein.
-
Ionenstrahl-Sputtern (IBS)
- Beim Ionenstrahlsputtern wird ein fokussierter Ionenstrahl verwendet, um Material vom Target abzusputtern.
- Das Verfahren ist hochgradig richtungsabhängig und ermöglicht eine präzise Kontrolle der Schichtdicke und -zusammensetzung.
- Vorteile:Hohe Präzision, ausgezeichnete Filmqualität und minimale Beschädigung des Substrats.
- Benachteiligungen:Geringere Abscheideraten und höhere Anlagenkosten.
-
Reaktives Sputtern
- Beim reaktiven Sputtern wird ein reaktives Gas (z. B. Sauerstoff oder Stickstoff) in die Sputterkammer eingeleitet, um Verbundschichten (z. B. Oxide oder Nitride) auf dem Substrat zu bilden.
- Wird häufig in Verbindung mit DC- oder RF-Sputtern verwendet.
- Vorteile:Ermöglicht die Abscheidung von Verbundwerkstoffen mit maßgeschneiderten Eigenschaften.
- Benachteiligungen:Erfordert eine präzise Steuerung des Gasdurchsatzes und kann zu einer Vergiftung des Targets führen.
-
Mittelfrequenzsputtern (MF) und gepulstes DC-Sputtern
- Das MF-Sputtern arbeitet mit Frequenzen zwischen 10 und 100 kHz, während beim gepulsten DC-Sputtern die Polarität des Targets wechselt, um Lichtbögen zu vermeiden.
- Diese Verfahren eignen sich besonders für das reaktive Sputtern und die Abscheidung von Isolierstoffen.
- Vorteile:Geringere Lichtbogenbildung, verbesserte Filmqualität und Kompatibilität mit isolierenden Targets.
- Nachteile:Komplexere Stromversorgungen und höhere Kosten.
-
Hochleistungs-Impuls-Magnetron-Sputtern (HiPIMS)
- HiPIMS verwendet kurze Hochleistungspulse, um eine hohe Ionisierung des gesputterten Materials zu erreichen.
- Das Ergebnis sind dichte, hochwertige Schichten mit hervorragender Haftung.
- Vorteile:Hervorragende Filmqualität, hohe Ionisierungsraten und verbesserte Haftung.
- Benachteiligungen:Geringere Abscheidungsraten und höhere Anlagenkomplexität.
-
Planare Dioden-RF-Sputterung
- Eine Variante des HF-Sputterns, bei der das Target und das Substrat in einer planaren Konfiguration angeordnet sind.
- Vorteile:Gleichmäßige Ablagerung und Verträglichkeit mit isolierenden Materialien.
- Nachteile:Begrenzt auf kleine Anwendungen und geringere Abscheidungsraten im Vergleich zum Magnetronsputtern.
-
Gasfluss-Sputtern
- Beim Gasfluss-Sputtern wird ein strömendes Gas verwendet, um das gesputterte Material auf das Substrat zu transportieren.
- Vorteile:Geeignet für die Abscheidung von Materialien mit niedrigem Schmelzpunkt und zur Erzielung gleichmäßiger Beschichtungen auf komplexen Geometrien.
- Benachteiligungen:Erfordert eine präzise Steuerung des Gasflusses und kann bei hochschmelzenden Materialien weniger effizient sein.
-
Ionenunterstütztes Sputtern
- Kombiniert Sputtern mit Ionenbeschuss des Substrats zur Verbesserung der Schichtdichte und Haftung.
- Vorteile:Bessere Filmeigenschaften und bessere Haftung.
- Nachteile:Erhöhte Komplexität und höhere Kosten.
Zusammenfassend kann man die Sputtertechniken grob nach der Stromversorgung (DC, RF, MF, gepulster DC, HiPIMS), der Methode der Ionenerzeugung (Magnetron, Ionenstrahl) und dem Vorhandensein reaktiver Gase (reaktives Sputtern) einteilen.Jede Art hat spezifische Anwendungen und Nachteile, so dass es wichtig ist, die richtige Sputtermethode auf der Grundlage der gewünschten Schichteigenschaften, des Zielmaterials und der Substratanforderungen zu wählen.
Zusammenfassende Tabelle:
Art der Zerstäubung | Wesentliche Merkmale | Vorteile | Nachteile |
---|---|---|---|
DC-Dioden-Sputtern | Einfacher Aufbau, verwendet Gleichspannung (500-1000 V) | Kostengünstig, geeignet für leitfähige Materialien | Begrenzt auf leitfähige Targets, geringere Abscheidungsraten, Substraterwärmung |
RF-Sputtern | Hochfrequentes Wechselfeld (13,56 MHz) | Ablagerung von Isoliermaterial, geringere Erwärmung, höhere Raten bei niedrigem Druck | Komplexe Ausrüstung, höhere Kosten |
Magnetron-Sputtering | Magnetfelder verbessern Ionisierung und Abscheidungsraten | Hohe Abscheidungsraten, bessere Schichtgleichmäßigkeit | Erfordert präzise Magnetfeldsteuerung, höhere Kosten |
Ionenstrahl-Sputtern (IBS) | Fokussierter Ionenstrahl für präzise Kontrolle | Hohe Präzision, hervorragende Schichtqualität, minimale Substratbeschädigung | Niedrigere Abscheideraten, höhere Anlagenkosten |
Reaktives Sputtern | Einleiten reaktiver Gase (z. B. Sauerstoff, Stickstoff) | Abscheidung von Verbundwerkstoffen mit maßgeschneiderten Eigenschaften | Erfordert präzise Gassteuerung, anfällig für Zielvergiftung |
HiPIMS | Kurze Hochleistungspulse für hohe Ionisierung | Hervorragende Schichtqualität, hohe Haftfestigkeit, dichte Schichten | Geringere Abscheideraten, komplexe Anlagen |
Benötigen Sie Hilfe bei der Auswahl der richtigen Sputtertechnik für Ihre Anwendung? Kontaktieren Sie noch heute unsere Experten !