Das Sputtern ist zwar eine weit verbreitete Technik für die Abscheidung dünner Schichten, hat jedoch einige bemerkenswerte Nachteile, die sich auf ihre Effizienz, Kosten und Eignung für bestimmte Anwendungen auswirken können.Zu diesen Nachteilen gehören hohe Investitionskosten, niedrige Abscheidungsraten für einige Materialien, mögliche Verunreinigungen der Schichten und Schwierigkeiten bei der Kontrolle der Schichtdicke und -gleichmäßigkeit.Außerdem erfordert das Sputtern häufig komplexe Anlagen und Kühlsysteme, was die Betriebskosten erhöhen und die Produktionsraten verringern kann.Das Verfahren ist auch weniger kompatibel mit bestimmten Materialien, insbesondere mit organischen Feststoffen, die sich unter Ionenbeschuss zersetzen können.Außerdem können durch das Sputtern Verunreinigungen in das Substrat eingebracht werden, und der diffuse Transportmechanismus erschwert die Integration mit Lift-off-Verfahren zur Strukturierung der Schichten.
Die wichtigsten Punkte erklärt:
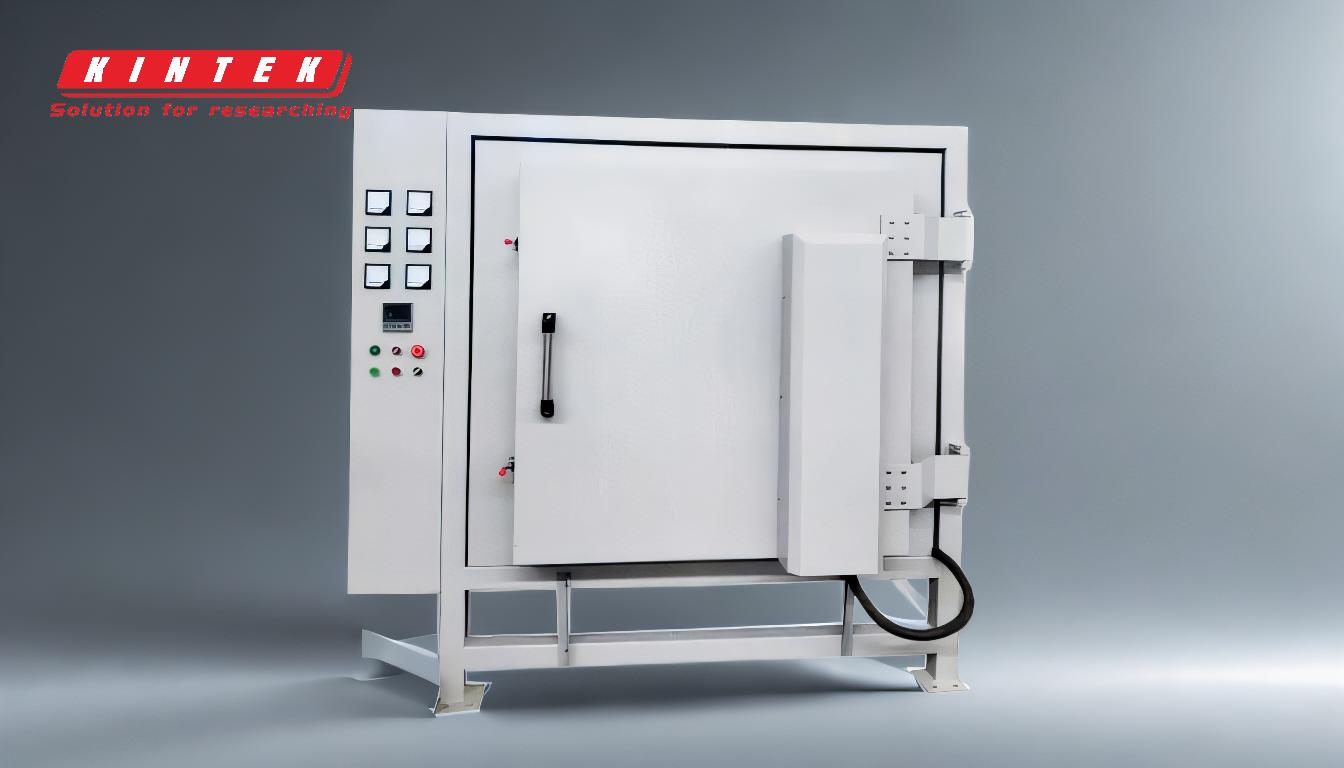
-
Hohe Kapitalkosten:
- Sputtering-Anlagen sind oft teuer und erfordern erhebliche Vorabinvestitionen.Dazu gehören die Kosten für Hochdruckgeräte, Kühlsysteme und andere spezielle Komponenten.
- Die Notwendigkeit eines Kühlsystems erhöht nicht nur die anfänglichen Kapitalkosten, sondern auch die laufenden Energiekosten, was die Gesamtwirtschaftlichkeit des Prozesses verringert.
-
Niedrige Abscheideraten:
- Beim Sputtern sind die Abscheideraten im Allgemeinen niedriger als bei anderen Techniken wie der thermischen Verdampfung.Dies gilt insbesondere für bestimmte Materialien wie SiO2, die die Produktionsraten verlangsamen können.
- Die niedrigen Sputterraten können in Fertigungsumgebungen mit hohem Durchsatz, in denen die Geschwindigkeit entscheidend ist, eine erhebliche Einschränkung darstellen.
-
Filmkontamination:
- Einer der größten Nachteile des Sputterns ist das Risiko der Filmverunreinigung.Verunreinigungen aus dem Targetmaterial oder der Sputterumgebung können in die Schicht eingebracht werden und deren Qualität beeinträchtigen.
- Gasförmige Verunreinigungen im Plasma können aktiviert und in die wachsende Schicht eingebaut werden, wodurch sich das Risiko einer Verunreinigung weiter erhöht.
- Bei der reaktiven Sputterabscheidung ist eine sorgfältige Kontrolle der Gaszusammensetzung erforderlich, um eine Vergiftung des Targets zu verhindern, die ebenfalls zu Verunreinigungen führen kann.
-
Schwierige Kontrolle von Schichtdicke und Gleichmäßigkeit:
- Das Erreichen einer gleichmäßigen Schichtdicke kann beim Sputtern aufgrund der ungleichmäßigen Verteilung des Abscheidungsflusses eine Herausforderung sein.Dies macht häufig den Einsatz beweglicher Vorrichtungen erforderlich, um eine gleichmäßige Beschichtung zu gewährleisten.
- Aufgrund des diffusen Transports der gesputterten Atome ist es schwierig, eine vollständige Abschattung zu erreichen, was die Integration mit Lift-off-Verfahren zur Strukturierung von Schichten erschwert.
-
Beschränkungen des Materials:
- Einige Materialien, insbesondere organische Feststoffe, sind anfällig für eine Zersetzung unter dem Ionenbeschuss, der mit dem Sputterverfahren einhergeht.Dies schränkt die Palette der Materialien ein, die mit dieser Technik effektiv beschichtet werden können.
- Die Auswahl der Beschichtungsmaterialien wird auch durch ihre Schmelztemperatur eingeschränkt, da Materialien mit sehr hohen Schmelzpunkten möglicherweise nicht für das Sputtern geeignet sind.
-
Verunreinigung Einführung:
- Beim Sputtern herrscht im Vergleich zum Aufdampfen ein geringeres Vakuum, wodurch die Wahrscheinlichkeit steigt, dass Verunreinigungen in das Substrat gelangen.Dies kann die Reinheit und Leistung der abgeschiedenen Schichten beeinträchtigen.
-
Komplexe Ausrüstung und Wartung:
- Das Sputtering-Verfahren erfordert komplexe Anlagen, darunter Hochdruckgeräte und Kühlsysteme, deren Wartung und Betrieb schwierig sein kann.
- Die Notwendigkeit der Wartung durch den Anwender und die Begrenzung der Prozessparameter können den Einsatz des Sputterns in industriellen Anwendungen weiter erschweren.
-
Hoher Temperaturanstieg des Substrats:
- Der Sputterprozess kann zu einem erheblichen Anstieg der Substrattemperatur führen, was bei temperaturempfindlichen Materialien oder Anwendungen unerwünscht sein kann.
- Dieser Temperaturanstieg kann auch dazu führen, dass das Substrat anfälliger für Verunreinigungen durch Fremdgase wird.
Zusammenfassend lässt sich sagen, dass das Sputtern zwar eine vielseitige und weit verbreitete Abscheidungstechnik ist, aber mehrere Nachteile aufweist, die ihre Wirksamkeit bei bestimmten Anwendungen einschränken können.Dazu gehören hohe Kosten, niedrige Abscheideraten, Verunreinigungsrisiken, Schwierigkeiten bei der Kontrolle der Schichteigenschaften, Materialbeschränkungen und komplexe Geräteanforderungen.Die Kenntnis dieser Nachteile ist entscheidend für die Auswahl der geeigneten Abscheidungsmethode für bestimmte Anwendungen und für die Optimierung des Sputterprozesses, um seine Einschränkungen zu verringern.
Zusammenfassende Tabelle:
Benachteiligung | Beschreibung |
---|---|
Hohe Kapitalkosten | Teure Geräte und Kühlsysteme erhöhen die Anschaffungs- und laufenden Kosten. |
Niedrige Abscheideraten | Langsame Raten für Materialien wie SiO2 begrenzen die Produktion mit hohem Durchsatz. |
Filmverschmutzung | Verunreinigungen von Targets oder Plasma können die Filmqualität beeinträchtigen. |
Kontrolle der Schichtdicke | Ungleichmäßiger Abscheidungsfluss erschwert das Erreichen gleichmäßiger Schichten. |
Einschränkungen bei den Materialien | Organische Feststoffe zersetzen sich unter Ionenbeschuss; hochschmelzende Materialien sind weniger geeignet. |
Einführung von Verunreinigungen | Ein geringerer Vakuumbereich erhöht das Risiko von Verunreinigungen in Substraten. |
Komplexe Ausrüstung | Hochdruckgeräte und Kühlsysteme erfordern einen hohen Wartungsaufwand. |
Temperaturanstieg des Substrats | Temperaturempfindliche Materialien können durch die beim Sputtern entstehende Hitze beschädigt werden. |
Benötigen Sie Hilfe bei der Auswahl des richtigen Verfahrens zur Dünnschichtabscheidung? Kontaktieren Sie noch heute unsere Experten für maßgeschneiderte Lösungen!