Pyrolyseanlagen spielen eine entscheidende Rolle bei der Umwandlung von Abfallstoffen wie Kunststoff, Gummi und Biomasse in wertvolle Produkte wie Heizöl, Biokohle und Gase.Die Typen von Pyrolysereaktoren unterscheiden sich in ihrer Konstruktion, ihren Heizmethoden und ihrer Betriebseffizienz.Zu den gängigen Typen gehören Flachkopf-, Kegelkopf- und Ellipsoidkopfkonstruktionen sowie Drehrohrofenreaktoren, Wirbelschichtreaktoren und spezialisierte Systeme wie sprudelnde Wirbelschichten, zirkulierende Wirbelschichten, transportierte Betten und ablative Pyrolyseure.Jeder Reaktortyp ist auf bestimmte Anwendungen zugeschnitten, z. B. Schnellpyrolyse für die Bioölproduktion oder langsame Pyrolyse für Biokohle.Wichtige Konstruktionsmerkmale wie Wärmeübertragungseffizienz, Isolierung und Sicherheitsmechanismen gewährleisten optimale Leistung und Umweltverträglichkeit.
Die wichtigsten Punkte werden erklärt:
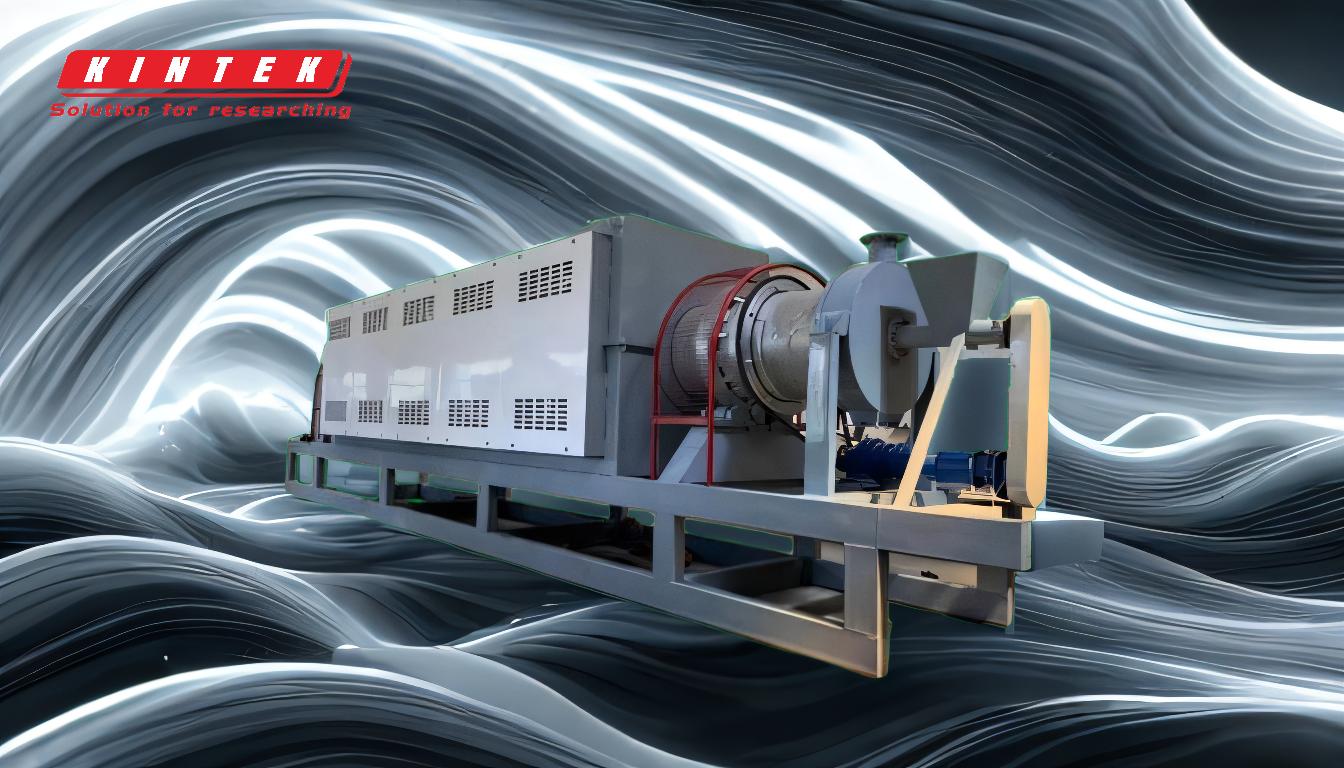
-
Typen von Pyrolysereaktoren basierend auf der Kopfkonstruktion:
- Flachkopf-Design:Diese Konstruktion ist einfach und kostengünstig und wird häufig für Pyrolyseprozesse im kleinen Maßstab verwendet.Sie eignet sich für Anwendungen, bei denen eine gleichmäßige Erwärmung keine kritische Anforderung darstellt.
- Konisches Kopfdesign:Diese Konstruktion verbessert die Wärmeverteilung und den Materialfluss und ist daher ideal für mittlere Betriebe.Die konische Form trägt zu einer besseren Durchmischung bei und reduziert tote Zonen.
- Ellipsoidkopf-Design:Diese Konstruktion bietet eine überragende Wärmeübertragung und strukturelle Festigkeit und eignet sich daher für groß angelegte industrielle Anwendungen.Sie gewährleistet eine gleichmäßige Erwärmung und minimiert Spannungskonzentrationen.
-
Typen von Pyrolysereaktoren auf Basis der Technologie:
- Drehrohrofen-Reaktoren:In diesen Reaktoren werden die Materialien durch indirekte Erhitzung zersetzt, was das Kontaminationsrisiko verringert.Sie sind vielseitig einsetzbar und können eine große Bandbreite an Rohstoffen verarbeiten, darunter Kunststoffe, Gummi und Biomasse.Die Drehbewegung gewährleistet eine gleichmäßige Erhitzung und eine effiziente Pyrolyse.
- Wirbelschichtreaktoren:In diesen Reaktoren werden die Materialien in einem Gas oder einer Flüssigkeit suspendiert, was eine gleichmäßige Erwärmung und eine schnellere Verarbeitung ermöglicht.Sie sind hocheffizient und eignen sich für die Schnellpyrolyse, bei der Bioöl als Hauptprodukt entsteht.Die Wirbelschichtkonstruktion gewährleistet eine hervorragende Wärmeübertragung und Verweilzeitkontrolle.
- Sprudelnde Wirbelschicht-Pyrolyseure:Sie sind eine Unterart der Wirbelschichtreaktoren und zeichnen sich durch ihre Fähigkeit aus, feine Partikel zu verarbeiten und hochwertiges Bioöl zu produzieren.Sie werden häufig bei der Pyrolyse von Biomasse eingesetzt.
- Zirkulierende Wirbelbetten:Diese Reaktoren recyceln das Bettmaterial, verbessern die Wärmeübertragung und verlängern die Verweilzeit des Einsatzmaterials.Sie sind ideal für kontinuierliche Pyrolyseprozesse.
- Transportierte Betten:Diese Reaktoren verwenden ein Trägergas, um das Ausgangsmaterial durch den Reaktor zu transportieren, was eine schnelle Erhitzung und effiziente Pyrolyse gewährleistet.Sie eignen sich für den Einsatz in großem Maßstab.
- Ablative Pyrolyseure:In diesen Reaktoren wird das Ausgangsmaterial mit mechanischer Kraft gegen eine heiße Oberfläche gepresst, was eine schnelle Wärmeübertragung und Pyrolyse ermöglicht.Sie sind hocheffizient, erfordern aber eine genaue Kontrolle der Betriebsbedingungen.
-
Konstruktionsmerkmale des Pyrolyse-Reaktors:
- Material und Isolierung:Hochwertiger Kesselstahl (Q345R) wird für eine effiziente Wärmeübertragung und Langlebigkeit verwendet.Der Reaktorkörper und die Tür sind mit 16 mm dickem Stahl und 80 mm dicker feuerfester Aluminiumsilikat-Faserwatte isoliert, was einen minimalen Wärmeverlust gewährleistet.
- Schweißen und Sicherheit:Eine spezielle Schweißtechnik gewährleistet vollständige und saubere Schweißnähte und vermeidet Fehler.Um Sicherheit und strukturelle Integrität zu gewährleisten, werden Ultraschallprüfungen zur Fehlererkennung durchgeführt.
- Rollen- und Motordesign:Hochtemperaturbeständige Rollen und Invertermotoren mit Frequenzumrichtern ermöglichen eine einstellbare Geschwindigkeit und eine verbesserte Effizienz.Große Zahnkranzstrukturen erhöhen die Stabilität und Präzision.
- Dynamische Gleichgewichtstests:Diese Tests gewährleisten die Langlebigkeit und Stabilität des Reduzierers und reduzieren Vibrationen und Verschleiß während des Betriebs.
-
Anwendungen von Pyrolyse-Reaktoren:
- Schnelle Pyrolyse:Erzeugt Bioöl durch schnelles Erhitzen von Biomasse auf hohe Temperaturen (400-700°C).Dieses Verfahren ist ideal für die Erzeugung von Flüssigbrennstoffen und Chemikalien.
- Langsame Pyrolyse:Herstellung von Biokohle durch Erhitzen von Biomasse bei niedrigeren Temperaturen (300-400°C).Dieses Verfahren eignet sich zur Bodenverbesserung und Kohlenstoffbindung.
- Torrefizierung:Erhitzt Biomasse bei mittleren Temperaturen (250-350°C), um ein festes Produkt mit verbesserten Brennstoffeigenschaften, wie höherer Energiedichte und geringerem Feuchtigkeitsgehalt, zu erzeugen.
-
Vorteile für die Umwelt:
- Pyrolysereaktoren wurden entwickelt, um das Recycling und die Wiederverwendung von Abfallstoffen zu maximieren und so zu einer umweltfreundlichen und schadstofffreien Welt beizutragen.Sie wandeln Kunststoff-, Gummi-, Reifen- und Schlammabfälle in einer sauerstofffreien Hochtemperaturumgebung in Heizöl um und tragen so dazu bei, die Umweltverschmutzung zu beseitigen und den Deponiemüll zu reduzieren.
Durch das Verständnis der verschiedenen Arten von Pyrolysereaktoren und ihren einzigartigen Merkmalen können die Käufer die am besten geeignete Anlage für ihre spezifischen Anwendungen auswählen und so eine optimale Leistung und Umweltverträglichkeit sicherstellen.
Zusammenfassende Tabelle:
Typ des Reaktors | Wesentliche Merkmale | Anwendungen |
---|---|---|
Flachkopf-Design | Einfach, kostengünstig, gleichmäßige Erwärmung nicht kritisch | Pyrolyseprozesse im kleinen Maßstab |
Konisches Kopfdesign | Verbesserte Wärmeverteilung, bessere Durchmischung, geringere Totzonen | Mittelgroße Betriebe |
Ellipsoidkopf-Design | Hervorragende Wärmeübertragung, strukturelle Stärke, gleichmäßige Erwärmung | Großtechnische Anwendungen |
Drehrohrofen-Reaktoren | Indirekte Beheizung, vielseitige, gleichmäßige Beheizung | Breites Spektrum an Einsatzstoffen (Kunststoffe, Gummi, Biomasse) |
Wirbelschichtreaktoren | Gleichmäßige Erwärmung, schnellere Verarbeitung, hervorragende Wärmeübertragung | Schnelle Pyrolyse für die Bioölproduktion |
Ablative Pyrolyseure | Schnelle Wärmeübertragung, mechanische Kraft für die Pyrolyse | Hocheffiziente Pyrolyse mit präziser Steuerung |
Sind Sie bereit, die richtige Pyrolyseanlage für Ihre Bedürfnisse auszuwählen? Kontaktieren Sie uns noch heute für fachkundige Beratung!