Zwei-Platten-Werkzeuge sind aufgrund ihrer Einfachheit und Kosteneffizienz beim Spritzgießen weit verbreitet.Sie sind jedoch mit gewissen Nachteilen verbunden, insbesondere bei Mehrfachkavitätenkonstruktionen.Eine der größten Herausforderungen besteht darin, den Fluss des geschmolzenen Kunststoffs über mehrere Kavitäten auszugleichen, was zu ungleichmäßiger Füllung und Defekten im Endprodukt führen kann.Darüber hinaus kann die Ausrichtung der Trennebene mit dem Anschnitt in einer Zweiplattenform den Konstruktions- und Herstellungsprozess erschweren.Diese Einschränkungen können sich auf die Effizienz, die Qualität und die Kosten der Produktion auswirken, so dass es wichtig ist, ihre Eignung für bestimmte Anwendungen sorgfältig zu prüfen.
Die wichtigsten Punkte erklärt:
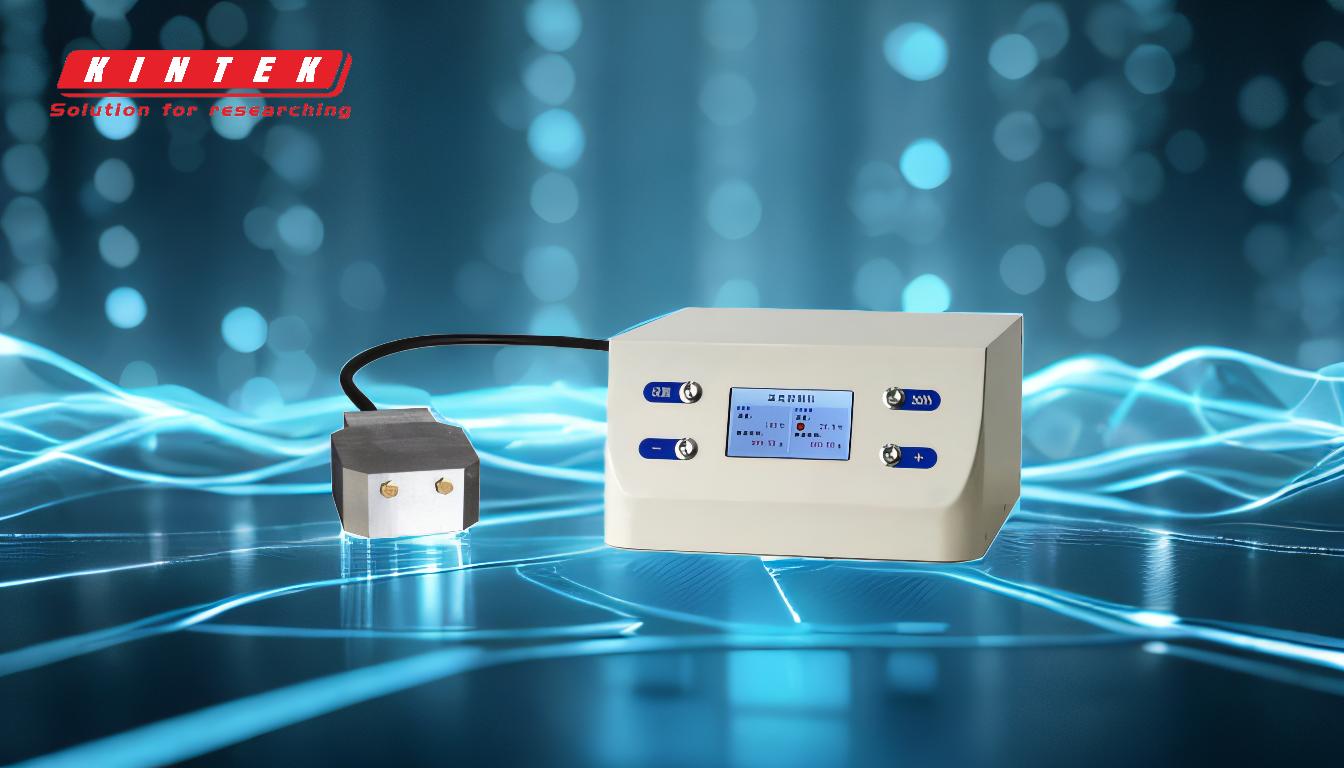
-
Herausforderungen beim Balancieren von geschmolzenem Kunststofffluss:
- Bei Zwei-Platten-Werkzeugen mit mehreren Kavitäten ist es schwierig, eine gleichmäßige Verteilung des geschmolzenen Kunststoffs in jeder Kavität sicherzustellen.
- Ein ungleichmäßiger Fluss kann zu Defekten wie kurzen Schüssen, Verzug oder uneinheitlichen Teileabmessungen führen.
- Dieses Problem verschärft sich bei komplexen Konstruktionen, bei denen sich die Kavitäten in unterschiedlichen Abständen vom Anschnitt befinden.
-
Ausrichtung der Trennebene zum Anschnitt:
- Die Trennebene in einer Zweiplattenform muss mit dem Anschnitt fluchten, was die Flexibilität der Konstruktion einschränkt.
- Diese Ausrichtung kann die Formkonstruktion erschweren, insbesondere bei komplizierten Teilen oder Mehrfachkavitäten.
- Sie kann auch das Risiko von Gratbildung oder anderen Defekten an der Trennfuge erhöhen.
-
Eingeschränkte Design-Flexibilität:
- Zwei-Platten-Werkzeuge sind im Vergleich zu Drei-Platten-Werkzeugen oder Heißkanalsystemen weniger vielseitig.
- Sie sind nicht ideal für Teile, die komplexe Anschnitte erfordern, oder für Teile mit besonderen ästhetischen Anforderungen.
- Die Einfachheit von Zwei-Platten-Werkzeugen geht oft auf Kosten von reduzierten Anpassungsmöglichkeiten.
-
Höheres Risiko von Defekten:
- Aufgrund der Herausforderungen beim Fließgleichgewicht und der Anschnittausrichtung sind Zwei-Platten-Werkzeuge anfälliger für Fehler.
- Zu den häufigsten Problemen gehören Schweißnähte, Lufteinschlüsse und eine uneinheitliche Teilequalität.
- Diese Mängel können die Ausschussrate und die Produktionskosten erhöhen.
-
Längere Zykluszeiten:
- Die Einschränkungen von Zwei-Platten-Werkzeugen können zu längeren Kühl- und Zykluszeiten führen.
- Dies gilt insbesondere für Mehrkavitätenwerkzeuge, bei denen eine ungleichmäßige Kühlung auftreten kann.
- Längere Zykluszeiten verringern die Gesamteffizienz der Produktion und erhöhen die Betriebskosten.
-
Höhere Wartungsanforderungen:
- Die Komplexität des Ausgleichs des Durchflusses und der Ausrichtung der Anschnitte kann zu einem erhöhten Verschleiß der Form führen.
- Um eine gleichbleibende Leistung zu gewährleisten, ist eine regelmäßige Wartung erforderlich, was die Gesamtbetriebskosten erhöht.
-
Nicht für alle Anwendungen geeignet:
- Zwei-Platten-Werkzeuge eignen sich am besten für einfache Teile mit unkomplizierten Anschnittanforderungen.
- Für komplexe Teile oder hochpräzise Anwendungen können alternative Werkzeugkonstruktionen (z. B. Drei-Platten-Werkzeuge oder Heißkanalsysteme) besser geeignet sein.
Wenn Hersteller diese Nachteile kennen, können sie fundierte Entscheidungen darüber treffen, ob ein Zwei-Platten-Werkzeug die richtige Wahl für ihre spezifischen Produktionsanforderungen ist.Sie bieten zwar Einfachheit und Kosteneinsparungen, aber ihre Grenzen müssen sorgfältig gegen die Anforderungen des Projekts abgewogen werden.
Zusammenfassende Tabelle:
Benachteiligung | Auswirkungen |
---|---|
Flow Balancing Herausforderungen | Ungleichmäßige Füllung, Defekte wie kurze Schüsse, Verzug oder inkonsistente Abmessungen. |
Trennebenen-Ausrichtung | Eingeschränkte Designflexibilität, erhöhtes Risiko der Gratbildung. |
Eingeschränkte Design-Flexibilität | Weniger flexibel für komplexe Teile oder besondere ästhetische Anforderungen. |
Höheres Risiko von Defekten | Schweißnähte, Lufteinschlüsse und uneinheitliche Teilequalität erhöhen die Ausschussrate. |
Längere Zykluszeiten | Ungleichmäßige Kühlung führt zu einer geringeren Produktionseffizienz. |
Höherer Wartungsbedarf | Erhöhter Verschleiß, der regelmäßige Wartung erfordert. |
Nicht für alle Anwendungen geeignet | Am besten für einfache Teile geeignet; für komplexe Konstruktionen sind möglicherweise andere Formen erforderlich. |
Benötigen Sie Hilfe bei der Auswahl der richtigen Form für Ihr Projekt? Kontaktieren Sie noch heute unsere Experten für maßgeschneiderte Lösungen!