Das selektive Lasersintern (SLS) ist ein komplexer additiver Fertigungsprozess, der von zahlreichen Faktoren beeinflusst wird, die die Qualität, Effizienz und Eigenschaften des Endprodukts bestimmen.Zu den wichtigsten Faktoren gehören Temperatur, Heizrate, Druck, Partikelgröße und Materialzusammensetzung.Die Temperatur bestimmt die Sinterkinetik und die Materialeigenschaften, während die Erhitzungsgeschwindigkeit die Verdichtung und das Gefüge beeinflusst.Der Druck unterstützt die Umlagerung der Partikel und die Verringerung der Porosität.Partikelgröße und -zusammensetzung spielen eine entscheidende Rolle für das Sinterverhalten, wobei kleinere Partikel und homogene Zusammensetzungen zu einer besseren Verdichtung und besseren mechanischen Eigenschaften führen.Das Verständnis dieser Faktoren ist entscheidend für die Optimierung des SLS-Prozesses und die Herstellung hochwertiger Teile.
Die wichtigsten Punkte erklärt:
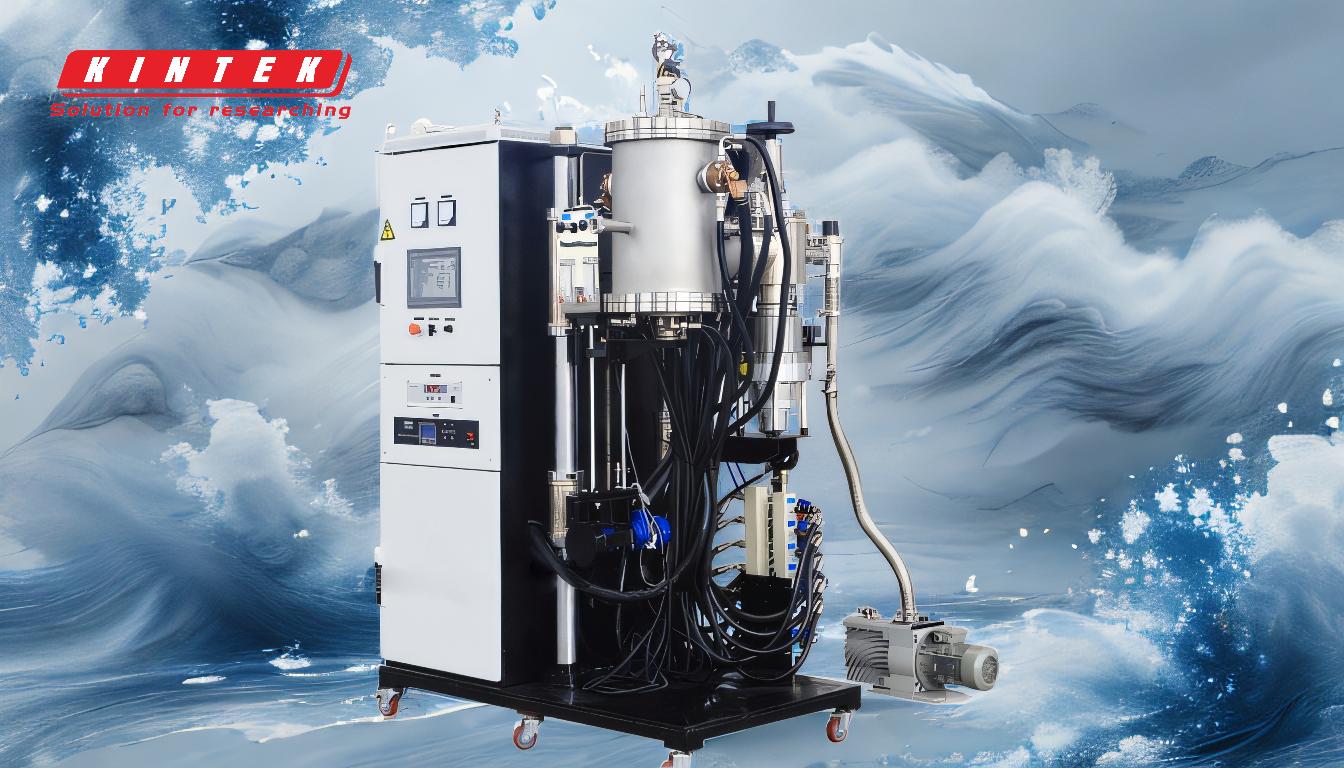
-
Temperatur:
- Rolle:Die Temperatur ist ein kritischer Faktor beim SLS, da sie die Sinterkinetik und die endgültigen Materialeigenschaften direkt beeinflusst.Sie bestimmt die Geschwindigkeit, mit der sich die Partikel verbinden, und den Grad der Verdichtung.
- Aufprall:Höhere Temperaturen beschleunigen im Allgemeinen die Sinterung, müssen aber sorgfältig kontrolliert werden, um Defekte wie Verzug oder übermäßiges Kornwachstum zu vermeiden.Die optimale Temperatur gewährleistet eine ordnungsgemäße Bindung, ohne die Integrität des Teils zu beeinträchtigen.
-
Aufheizrate:
- Rolle:Die Heizrate bestimmt, wie schnell das Material die Sintertemperatur erreicht und beeinflusst den Verdichtungsprozess.
- Aufprall:Eine kontrollierte Aufheizgeschwindigkeit gewährleistet eine gleichmäßige Verdichtung und minimiert thermische Gradienten, die zu inneren Spannungen und Verformungen der Teile führen können.Eine schnelle Erwärmung kann zu einer unvollständigen Sinterung führen, während eine langsame Erwärmung zu einem übermäßigen Energieverbrauch führen kann.
-
Druck:
- Rolle:Druck, auch wenn er bei SLS nicht immer angewendet wird, kann die Umlagerung von Partikeln fördern und die Porosität verringern.
- Aufprall:Durch den angewandten Druck wird ein besserer Partikelkontakt und eine bessere Verdichtung erreicht, was zu besseren mechanischen Eigenschaften führt.Übermäßiger Druck kann jedoch zu einer Verformung oder Beschädigung des Teils führen.
-
Partikelgröße:
- Rolle:Die Partikelgröße wirkt sich erheblich auf das Sinterverhalten aus, da kleinere Partikel eine höhere Oberflächenenergie und eine größere Antriebskraft für die Sinterung haben.
- Aufprall:Kleinere Partikel fördern eine schnellere und gleichmäßigere Verdichtung, was zu Teilen mit höherer Dichte und besseren mechanischen Eigenschaften führt.Größere Partikel können zu einer unvollständigen Sinterung und erhöhter Porosität führen.
-
Material-Zusammensetzung:
- Rolle:Die Zusammensetzung des Materials bestimmt sein Sinterverhalten, einschließlich Schmelzpunkt, Wärmeleitfähigkeit und Bindungseigenschaften.
- Schlagzähigkeit:Homogene Zusammensetzungen mit gleichmäßiger Partikelverteilung gewährleisten eine gleichmäßige Sinterung und eine bessere Teilequalität.Inhomogene Zusammensetzungen können zu ungleichmäßiger Verdichtung und Defekten führen.
-
Laserleistung und Scan-Geschwindigkeit:
- Rolle:Laserleistung und Scangeschwindigkeit sind kritische Parameter beim SLS, die den Energieeintrag und die Wechselwirkungszeit mit dem Material steuern.
- Aufprall:Höhere Laserleistung und langsamere Scangeschwindigkeiten erhöhen den Energieeintrag, was eine bessere Sinterung begünstigt, aber das Risiko einer Überhitzung birgt.Eine geringere Leistung und schnellere Geschwindigkeiten können zu einer unzureichenden Sinterung führen.Die Ausgewogenheit dieser Parameter ist entscheidend für eine optimale Teilequalität.
-
Schichtdicke:
- Rolle:Die Schichtdicke beeinflusst die Auflösung und die Oberflächengüte des fertigen Teils.
- Aufschlag:Dünnere Schichten bieten eine höhere Auflösung und glattere Oberflächen, verlängern aber die Bauzeit.Dickere Schichten verkürzen die Bauzeit, können aber die Genauigkeit der Teile und die Oberflächenqualität beeinträchtigen.
-
Atmosphäre:
- Rolle:Die Sinterumgebung, in der Regel eine inerte Atmosphäre, verhindert Oxidation und Verunreinigung.
- Aufprall:Eine kontrollierte Atmosphäre gewährleistet gleichbleibende Materialeigenschaften und verhindert Defekte durch Oxidation oder Verunreinigung.Eine unzureichende Kontrolle der Atmosphäre kann zu einer Verschlechterung der Teile führen.
-
Nachbearbeitungen:
- Rolle:Nachbearbeitungsschritte wie Wärmebehandlung oder Oberflächenveredelung können die Eigenschaften der Teile verbessern.
- Aufprall:Eine ordnungsgemäße Nachbearbeitung verbessert die mechanischen Eigenschaften, die Maßhaltigkeit und die Oberflächengüte.Eine Vernachlässigung der Nachbearbeitung kann zu einer suboptimalen Teileleistung führen.
Durch sorgfältige Kontrolle und Optimierung dieser Faktoren können Hersteller qualitativ hochwertige SLS-Teile mit den gewünschten Eigenschaften herstellen und sicherstellen, dass das Verfahren effizient und kostengünstig ist.
Zusammenfassende Tabelle:
Faktor | Rolle | Auswirkung |
---|---|---|
Temperatur | Beeinflusst die Sinterkinetik und die Materialeigenschaften. | Höhere Temperaturen beschleunigen die Sinterung, bergen aber das Risiko von Defekten; optimale Temperaturen gewährleisten die Bindung. |
Aufheizrate | Beeinflusst die Verdichtung und das Mikrogefüge. | Kontrolliertes Erhitzen gewährleistet eine gleichmäßige Verdichtung; schnelles Erhitzen kann Probleme verursachen. |
Druck | Verbessert die Umlagerung von Partikeln und verringert die Porosität. | Verbessert die Verdichtung, aber übermäßiger Druck kann die Teile verformen. |
Partikelgröße | Kleinere Partikel haben eine höhere Oberflächenenergie für die Sinterung. | Kleinere Partikel führen zu einer besseren Verdichtung und besseren mechanischen Eigenschaften. |
Materialzusammensetzung | Bestimmt das Sinterverhalten und die Bindungseigenschaften. | Homogene Zusammensetzungen gewährleisten gleichbleibende Sinter- und Teilequalität. |
Laserleistung & Scan-Geschwindigkeit | Steuert den Energieeintrag und die Wechselwirkungszeit. | Die Ausgewogenheit dieser Parameter ist entscheidend für eine optimale Sinterung. |
Schichtdicke | Beeinflusst Auflösung und Oberflächengüte. | Dünnere Schichten verbessern die Auflösung, verlängern aber die Bauzeit. |
Atmosphäre | Verhindert Oxidation und Verunreinigung. | Die kontrollierte Atmosphäre gewährleistet gleichbleibende Materialeigenschaften. |
Nachbearbeitung | Verbessert die mechanischen Eigenschaften, die Genauigkeit und die Oberflächengüte. | Eine ordnungsgemäße Nachbearbeitung verbessert die Leistung der Teile. |
Sind Sie bereit, Ihr SLS-Verfahren zu optimieren? Kontaktieren Sie noch heute unsere Experten für maßgeschneiderte Lösungen!