Das RF-Sputtern ist eine Technik zur Abscheidung dünner Schichten, insbesondere für isolierende oder nichtleitende Materialien, unter Verwendung einer Wechselstromquelle bei Radiofrequenzen. Bei diesem Verfahren wird das elektrische Potenzial zwischen dem Zielmaterial (Kathode) und dem Substrathalter (Anode) mit einer festen Frequenz, in der Regel 13,56 MHz, gewechselt. Dieses Wechselpotential verhindert den Aufbau von Ladungen auf isolierenden Targets, die andernfalls zu Lichtbogenbildung führen und den Prozess stören könnten. Während des positiven Halbzyklus werden Elektronen vom Target angezogen, wodurch eine negative Vorspannung entsteht, während im negativen Halbzyklus durch Ionenbeschuss Targetatome und Gasionen auf das Substrat geschleudert werden, wodurch ein dünner Film entsteht. Das RF-Sputtern ist besonders effektiv für dielektrische Materialien und arbeitet im Vergleich zum DC-Sputtern mit niedrigeren Abscheideraten, wodurch es sich für kleinere Substrate und hochpräzise Anwendungen eignet.
Die wichtigsten Punkte erklärt:
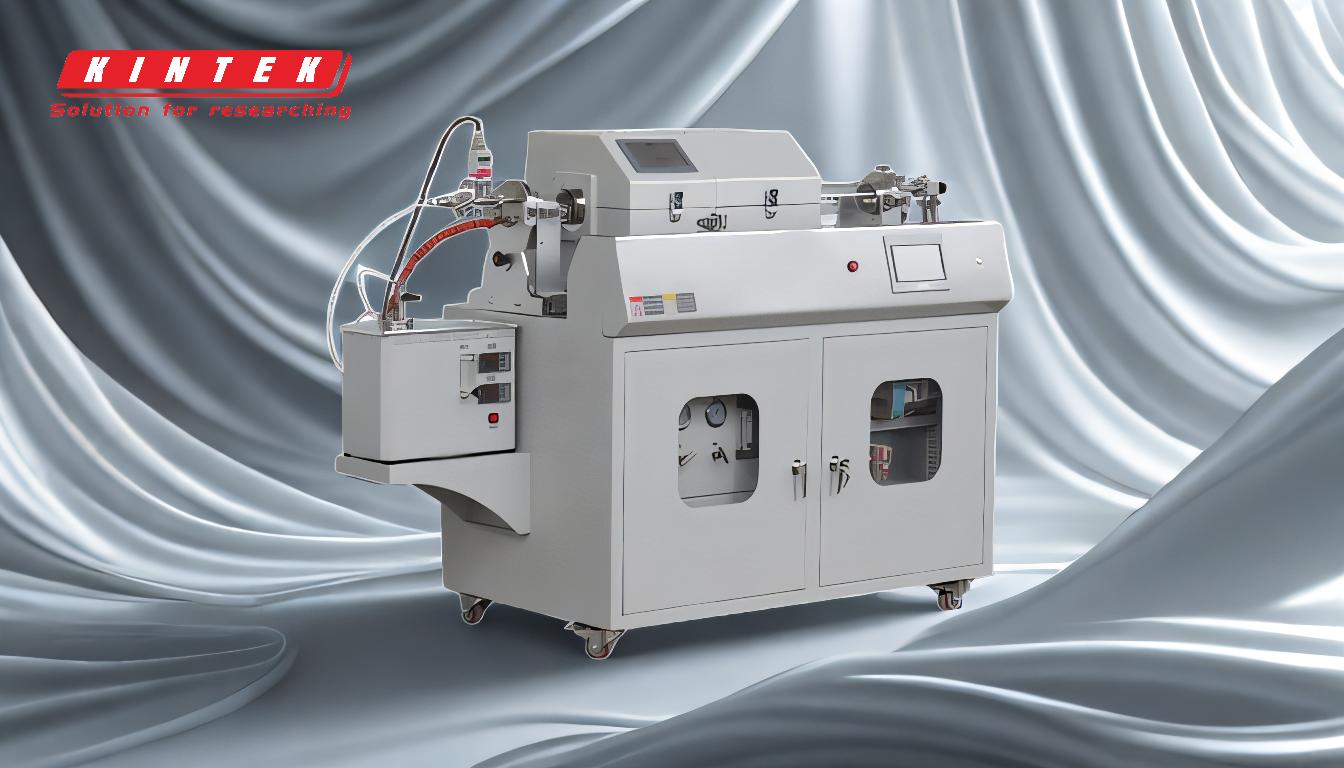
-
Grundprinzip des RF-Sputterns:
- Beim RF-Sputtern wird eine Wechselstromquelle (typischerweise mit 13,56 MHz) verwendet, um das elektrische Potenzial zwischen dem Targetmaterial und dem Substrathalter zu wechseln.
- Das wechselnde Potenzial verhindert den Aufbau von Ladungen auf isolierenden Targets, was beim Gleichstromsputtern ein häufiges Problem ist.
- Dieses Verfahren ist besonders effektiv für die Abscheidung dünner Schichten aus nichtleitenden oder dielektrischen Materialien.
-
Die Rolle des Wechselstroms (AC):
- Die Wechselstromquelle wechselt die Polarität des Targetmaterials und des Substrathalters.
- Im positiven Halbzyklus wirkt das Target als Anode, zieht Elektronen an und erzeugt eine negative Vorspannung.
- Im negativen Halbzyklus wird das Target zur Kathode und stößt Gasionen und Targetatome auf das Substrat.
-
Verhinderung des Ladungsaufbaus:
- Isolierende Materialien neigen dazu, beim DC-Sputtern Ladungen zu akkumulieren, was zu Lichtbogenbildung und Prozessinstabilität führt.
- Beim RF-Sputtern wechselt die Polarität, wodurch die Oberfläche des Targets bei jedem Zyklus effektiv von Ladungsansammlungen "gereinigt" wird.
- Dies gewährleistet einen stabilen Sputterprozess und eine hochwertige Dünnschichtabscheidung.
-
Ionisierung und Sputtering-Prozess:
- Ein inertes Gas (z. B. Argon) wird in einer Vakuumkammer durch die HF-Energie ionisiert.
- Das ionisierte Gas erzeugt ein Plasma, und hochenergetische Ionen beschießen das Zielmaterial.
- Die Zielatome werden herausgeschleudert und bilden einen feinen Sprühnebel, der das Substrat beschichtet und eine dünne Schicht bildet.
-
Abscheiderate und Substratgröße:
- Beim RF-Sputtern ist die Abscheiderate in der Regel niedriger als beim DC-Sputtern.
- Aufgrund der höheren Kosten und der für Isoliermaterialien erforderlichen Präzision ist es besser für kleinere Substrate geeignet.
-
Anwendungen des RF-Sputterns:
- Das HF-Sputtern ist in der Halbleiter- und Computerindustrie für die Abscheidung dünner Schichten aus isolierenden Materialien weit verbreitet.
- Es wird auch bei der Herstellung von optischen Beschichtungen, Solarzellen und anderen hochpräzisen Anwendungen eingesetzt.
-
RF-Magnetronzerstäubung:
- Eine Variante des HF-Sputterns, das HF-Magnetron-Sputtern, verwendet Magnete, um Elektronen in der Nähe des Zielmaterials einzufangen.
- Dies erhöht die Ionisierungseffizienz und ermöglicht schnellere Abscheidungsraten unter Beibehaltung der Vorteile des RF-Sputterns.
-
Betriebsparameter:
- Das RF-Sputtern arbeitet mit einem Kammerdruck von 0,5 bis 10 mTorr.
- Die Elektronendichte reicht von 10^9 bis 10^11 cm^-3.
- Die HF-Spitze-Spitze-Spannung liegt typischerweise bei 1000 V.
Wenn man diese Prinzipien versteht, kann man die Vielseitigkeit und Präzision des HF-Sputterns schätzen, insbesondere bei Anwendungen mit nichtleitenden Materialien und der Abscheidung hochwertiger Dünnschichten.
Zusammenfassende Tabelle:
Hauptaspekt | Einzelheiten |
---|---|
Grundprinzip | Verwendung von Wechselstrom bei 13,56 MHz, um Ladungsaufbau auf isolierenden Targets zu verhindern. |
Die Rolle von AC | Wechselt die Polarität und ermöglicht so stabiles Sputtern für dielektrische Materialien. |
Verhindert den Aufbau von Ladungen | Vermeidet Lichtbogenbildung und gewährleistet eine hochwertige Dünnschichtabscheidung. |
Ionisierungsprozess | Ionisiertes Inertgas (z. B. Argon) zur Erzeugung eines Plasmas für den Ausstoß der Zielatome. |
Abscheiderate | Niedriger als beim DC-Sputtern, ideal für kleinere Substrate und Präzisionsarbeiten. |
Anwendungen | Halbleiter, optische Beschichtungen, Solarzellen und mehr. |
Betriebsparameter | Kammerdruck: 0,5-10 mTorr; Elektronendichte: 10^9-10^11 cm^-3. |
Entdecken Sie, wie RF-Sputtering Ihre Dünnschichtprozesse verbessern kann. Kontaktieren Sie unsere Experten noch heute !