Bei der Sputterbeschichtung handelt es sich um ein spezielles Verfahren zur Abscheidung dünner Schichten, bei dem Atome aus einem festen Zielmaterial durch Beschuss mit hochenergetischen Ionen in eine Gasphase geschleudert werden.Diese ausgestoßenen Atome lagern sich dann auf einem Substrat ab und bilden eine dünne, gleichmäßige Schicht.Dieses Verfahren ist in Branchen wie der Halbleiterindustrie, der Elektronik, der Optik und dem Gesundheitswesen weit verbreitet.Die Anwendungen reichen von der Herstellung von Computerfestplatten und transparenten Elektroden für Solarzellen bis zur Beschichtung medizinischer Implantate.Das Verfahren ist äußerst vielseitig und ermöglicht eine präzise Kontrolle der Schichtdicke und -zusammensetzung, was es für die fortschrittliche Fertigung und Technologieentwicklung unverzichtbar macht.
Die wichtigsten Punkte erklärt:
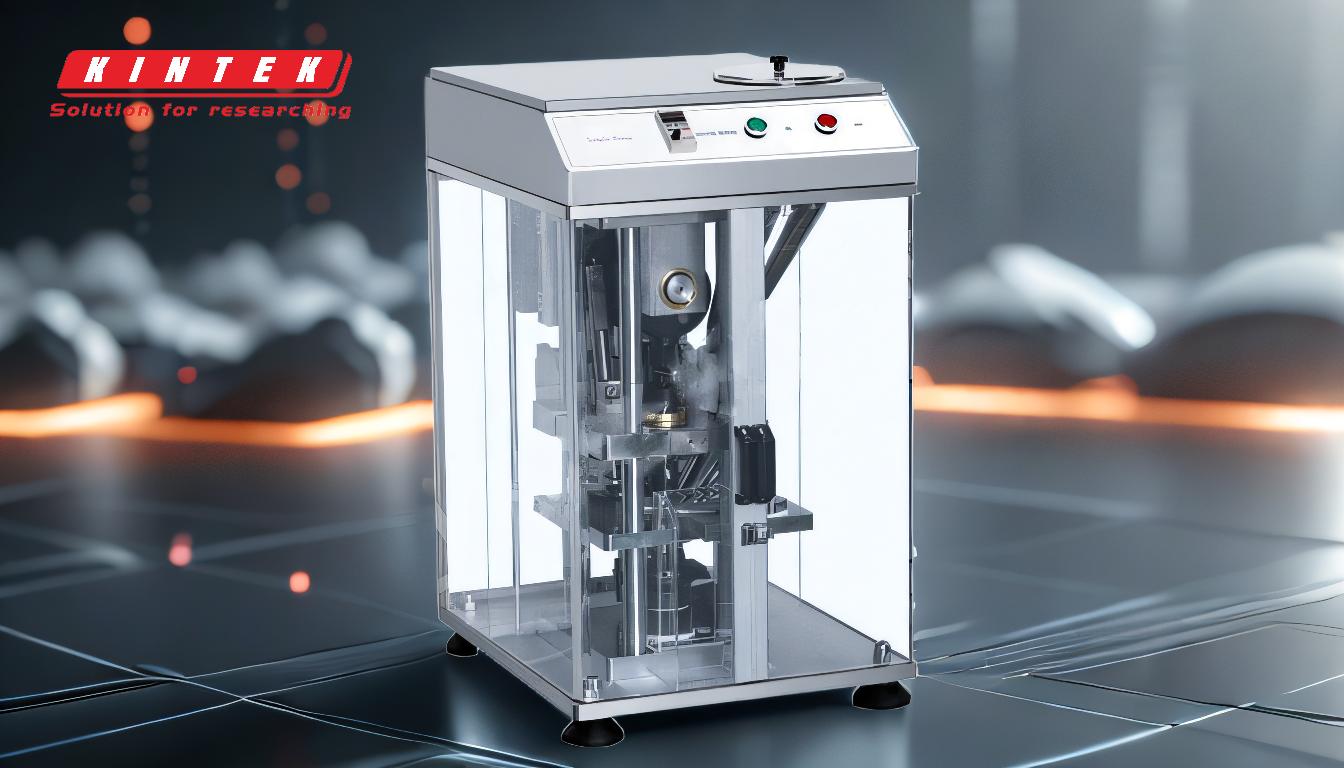
-
Definition der Sputter-Beschichtung:
- Bei der Sputterbeschichtung handelt es sich um ein PVD-Verfahren (Physical Vapor Deposition), bei dem ein festes Zielmaterial mit hochenergetischen Ionen beschossen wird, wodurch Atome herausgeschleudert werden und sich auf einem Substrat ablagern.
- Dieser Prozess findet in einer Vakuumkammer statt, die eine kontrollierte Umgebung für eine präzise Dünnfilmbildung gewährleistet.
-
Mechanismus des Sputterns:
- Inertgas-Ionen (z. B. Argon) werden auf das Zielmaterial beschleunigt.
- Bei der Kollision wird Energie übertragen, wodurch Atome aus dem Target herausgeschleudert werden.
- Diese ausgestoßenen Atome wandern durch das Vakuum und lagern sich auf dem Substrat ab und bilden einen dünnen Film.
-
Anwendungen in Halbleitern und Elektronik:
- Die Sputterbeschichtung ist in der Halbleiterindustrie von entscheidender Bedeutung für die Abscheidung dünner Schichten von Materialien wie Metallen, Oxiden und Nitriden.
- Es wird bei der Herstellung von Computerfestplatten, integrierten Schaltkreisen und TFT-LCD-Komponenten (z. B. Source-, Drain- und Gate-Elektroden) eingesetzt.
- Das Verfahren ermöglicht die Herstellung transparenter leitfähiger Schichten für Displays und Solarzellen.
-
Industrielle und kommerzielle Anwendungen:
- Architektonische und antireflektierende Glasbeschichtungen.
- Solartechnik, einschließlich Dünnschicht-Solarzellen.
- Automobil- und dekorative Beschichtungen.
- Beschichtungen für Werkzeugeinsätze für verbesserte Haltbarkeit.
- CD- und DVD-Metallbeschichtungen für die Datenspeicherung.
-
Medizinische und gesundheitliche Anwendungen:
- Sputterbeschichtungen werden bei medizinischen Implantaten zur Verbesserung der Biokompatibilität und Haltbarkeit eingesetzt.
- Ionengestützte Abscheidungsmethoden werden zur Herstellung spezieller Beschichtungen für Implantate eingesetzt, was die Nachfrage im Gesundheitssektor ankurbelt.
-
Vorteile der Sputter-Beschichtung:
- Hohe Präzision und Gleichmäßigkeit bei der Schichtabscheidung.
- Fähigkeit zur Abscheidung einer breiten Palette von Materialien, einschließlich Metallen, Legierungen und Keramiken.
- Hervorragende Haftung der Beschichtung auf dem Substrat.
- Geeignet für komplexe Geometrien und Großserienproduktion.
-
Herausforderungen und Überlegungen:
- Das Verfahren erfordert spezielle Geräte und eine Vakuumumgebung, was die Betriebskosten erhöht.
- Die beim Sputtern entstehende Wärme erfordert wirksame Kühlsysteme.
- Um gleichbleibende Ergebnisse zu erzielen, müssen Parameter wie Gasdruck, Ionenenergie und Target-Substrat-Abstand sorgfältig kontrolliert werden.
-
Zukünftige Trends:
- Wachsende Nachfrage nach Anwendungen im Bereich der erneuerbaren Energien, wie z. B. transparente Elektroden für Solarzellen.
- Expansion im Gesundheitswesen bei fortschrittlichen Beschichtungen für medizinische Implantate.
- Fortgesetzte Innovation in der Halbleiterfertigung, angetrieben durch den Bedarf an kleineren, effizienteren Geräten.
Die Sputterbeschichtung ist eine grundlegende Technologie in der modernen Fertigung und ermöglicht Fortschritte in der Elektronik, Optik, Energie und im Gesundheitswesen.Ihre Vielseitigkeit und Präzision machen sie unverzichtbar für die Herstellung von Hochleistungsmaterialien und -komponenten.
Zusammenfassende Tabelle:
Aspekt | Einzelheiten |
---|---|
Definition | Abscheidung von Dünnschichten durch hochenergetischen Ionenbeschuss in einer Vakuumkammer. |
Anwendungen | Halbleiter, Solarzellen, medizinische Implantate und dekorative Beschichtungen. |
Vorteile | Hohe Präzision, gleichmäßiges Auftragen, hervorragende Haftung und Vielseitigkeit. |
Herausforderungen | Erfordert spezielle Geräte, eine Vakuumumgebung und eine präzise Steuerung. |
Zukünftige Trends | Wachstum in den Bereichen erneuerbare Energien, Gesundheitswesen und Halbleiterinnovationen. |
Erfahren Sie, wie die Sputterbeschichtung Ihre Fertigungsprozesse verbessern kann. Kontaktieren Sie unsere Experten noch heute !