Die chemische Abscheidung aus der Gasphase (CVD) und die physikalische Abscheidung aus der Gasphase (PVD) sind zwei unterschiedliche Verfahren zur Abscheidung dünner Schichten, die in verschiedenen Branchen weit verbreitet sind.Beide Methoden zielen darauf ab, dünne Schichten auf Substraten abzuscheiden, unterscheiden sich aber erheblich in ihren Verfahren, Betriebsbedingungen und Ergebnissen.CVD beruht auf chemischen Reaktionen mit gasförmigen Ausgangsstoffen, erfordert in der Regel hohe Temperaturen und kann korrosive Nebenprodukte erzeugen.Im Gegensatz dazu beinhaltet PVD die physikalische Verdampfung fester oder flüssiger Materialien, arbeitet bei niedrigeren Temperaturen und vermeidet korrosive Nebenprodukte.Die Entscheidung zwischen CVD und PVD hängt von Faktoren wie den gewünschten Schichteigenschaften, dem Substratmaterial und den Anwendungsanforderungen ab.
Die wichtigsten Punkte werden erklärt:
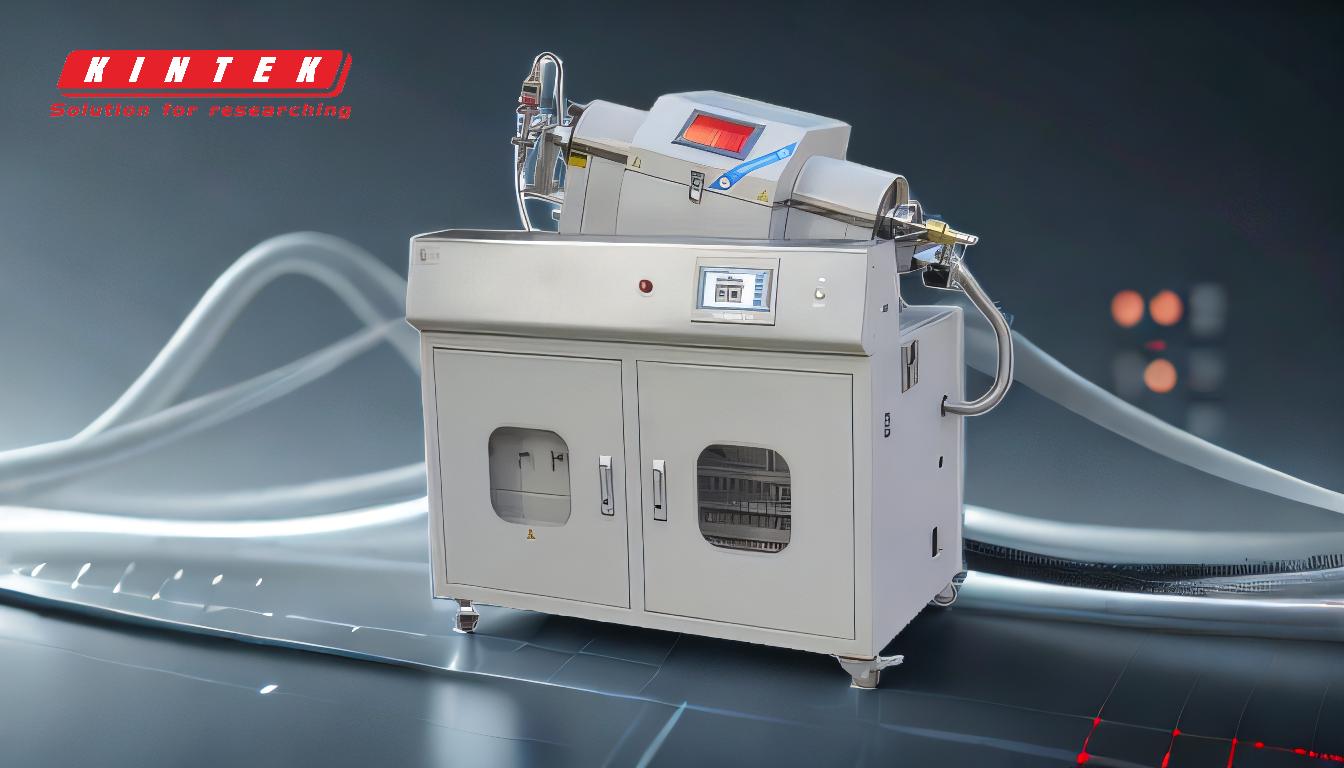
-
Mechanismus des Prozesses:
- CVD:Es handelt sich um chemische Reaktionen von gasförmigen Vorläufern auf einer erhitzten Substratoberfläche.Die gasförmigen Moleküle adsorbieren auf dem Substrat, reagieren und bilden einen festen Film.Dieses Verfahren ist multidirektional, d. h. es kann komplexe Geometrien gleichmäßig beschichten.
- PVD:Es handelt sich um die physikalische Verdampfung eines festen oder flüssigen Materials, das dann als Dampf zum Substrat transportiert wird, wo es kondensiert und einen dünnen Film bildet.PVD ist ein Sichtlinienverfahren, das heißt, es eignet sich eher für flache oder einfache Geometrien.
-
Temperatur-Anforderungen:
- CVD:Wird in der Regel bei hohen Temperaturen zwischen 500°C und 1100°C betrieben.Diese Hochtemperaturumgebung begünstigt chemische Reaktionen, kann aber die Arten von Substraten einschränken, die verwendet werden können.
- PVD:Arbeitet bei niedrigeren Temperaturen als CVD und ist daher für temperaturempfindliche Substrate geeignet.Einige PVD-Verfahren, wie z. B. Elektronenstrahl-PVD (EBPVD), können jedoch hohe Abscheideraten bei relativ niedrigen Temperaturen erzielen.
-
Nebenprodukte und Verunreinigungen:
- CVD:Es entstehen häufig korrosive gasförmige Nebenprodukte, die den Prozess erschweren und zusätzliche Sicherheitsmaßnahmen erfordern können.Die hohen Temperaturen können auch zu Verunreinigungen in der abgeschiedenen Schicht führen.
- PVD:Es entstehen keine korrosiven Nebenprodukte, was es zu einem saubereren Verfahren macht.Allerdings sind die Abscheideraten im Allgemeinen niedriger als bei der CVD.
-
Abscheideraten:
- CVD:Bietet im Allgemeinen höhere Abscheidungsraten und eignet sich daher für Anwendungen, die dicke Schichten oder einen hohen Durchsatz erfordern.
- PVD:In der Regel geringere Abscheideraten, obwohl fortgeschrittene Verfahren wie EBPVD Raten von 0,1 bis 100 μm/min erreichen können.
-
Effizienz der Materialausnutzung:
- CVD:Effiziente Materialausnutzung, da mit gasförmigen Vorprodukten komplexe Geometrien gleichmäßig beschichtet werden können.
- PVD:Ebenfalls effizient, insbesondere bei Verfahren wie EBPVD, die eine sehr hohe Materialausnutzung bieten.
-
Anwendungen:
- CVD:Wird häufig in der Halbleiterherstellung verwendet, wo hochwertige, gleichmäßige Schichten erforderlich sind.Es wird auch für die Beschichtung von Werkzeugen, optischen Komponenten und verschleißfesten Oberflächen verwendet.
- PVD:Weit verbreitet für dekorative Beschichtungen, Korrosionsschutzschichten und verschleißfeste Folien.Es wird auch bei der Herstellung von Solarzellen und medizinischen Geräten verwendet.
-
Ausrüstung und Betriebskomplexität:
- CVD:Erfordert eine spezielle Ausrüstung zur Handhabung hoher Temperaturen und korrosiver Gase.Das Verfahren erfordert außerdem geschultes Personal und eine genaue Kontrolle der Reaktionsbedingungen.
- PVD:Erfordert Vakuumbedingungen und in einigen Fällen Kühlsysteme für die Wärmeableitung.Die Anlagen sind im Allgemeinen weniger komplex als CVD-Systeme, erfordern aber dennoch eine fachkundige Bedienung.
Zusammenfassend lässt sich sagen, dass die Entscheidung zwischen CVD und PVD von den spezifischen Anforderungen der Anwendung abhängt, einschließlich der gewünschten Schichteigenschaften, des Substratmaterials und der betrieblichen Zwänge.CVD wird für Anwendungen mit hohen Temperaturen und hohen Abscheidungsraten bevorzugt, während PVD für sauberere Prozesse mit niedrigeren Temperaturen und komplexen Geometrien vorzuziehen ist.
Zusammenfassende Tabelle:
Blickwinkel | CVD | PVD |
---|---|---|
Mechanismus des Verfahrens | Chemische Reaktionen von gasförmigen Vorläufern auf einer erhitzten Substratoberfläche | Physikalische Verdampfung von festen/flüssigen Materialien, die auf dem Substrat kondensieren |
Temperatur | Hoch (500°C-1100°C) | Niedriger, geeignet für temperaturempfindliche Substrate |
Nebenprodukte | Ätzende gasförmige Nebenprodukte | Keine korrosiven Nebenprodukte |
Ablagerungsraten | Hoch | Geringer (0,1-100 μm/min bei fortgeschrittenen Verfahren wie EBPVD) |
Material-Effizienz | Hohe, gleichmäßige Beschichtung auf komplexen Geometrien | Hoch, insbesondere mit EBPVD |
Anwendungen | Halbleiter, Werkzeuge, optische Komponenten, verschleißfeste Oberflächen | Dekorative Beschichtungen, Korrosionsschutzschichten, Solarpaneele, medizinische Geräte |
Komplexität der Ausrüstung | Hoch, erfordert den Umgang mit korrosiven Gasen und hohen Temperaturen | Niedriger, erfordert Vakuumbedingungen und Kühlsysteme |
Benötigen Sie Hilfe bei der Entscheidung zwischen CVD und PVD für Ihre Anwendung? Kontaktieren Sie noch heute unsere Experten für eine maßgeschneiderte Beratung!