Chemische Gasphasenabscheidung (CVD) und physikalische Gasphasenabscheidung (PVD) sind zwei weit verbreitete Techniken zum Aufbringen von Werkzeugbeschichtungen, die jeweils unterschiedliche Prozesse, Vorteile und Einschränkungen aufweisen. CVD umfasst chemische Reaktionen bei relativ niedrigen Temperaturen und erzeugt dichte, gleichmäßige Beschichtungen, die für komplexe Geometrien geeignet sind. PVD hingegen arbeitet im Vakuum bei hohen Temperaturen und nutzt physikalische Prozesse, um eine breitere Palette von Materialien abzuscheiden, darunter Metalle, Legierungen und Keramik. Während PVD-Beschichtungen weniger dicht sind und sich schneller auftragen lassen, sind CVD-Beschichtungen dichter, gleichmäßiger und besser für komplizierte Formen geeignet. Beide Methoden erfordern hochentwickelte Geräte und Reinraumeinrichtungen, ihre Anwendungen unterscheiden sich jedoch je nach den gewünschten Beschichtungseigenschaften und Werkzeuganforderungen.
Wichtige Punkte erklärt:
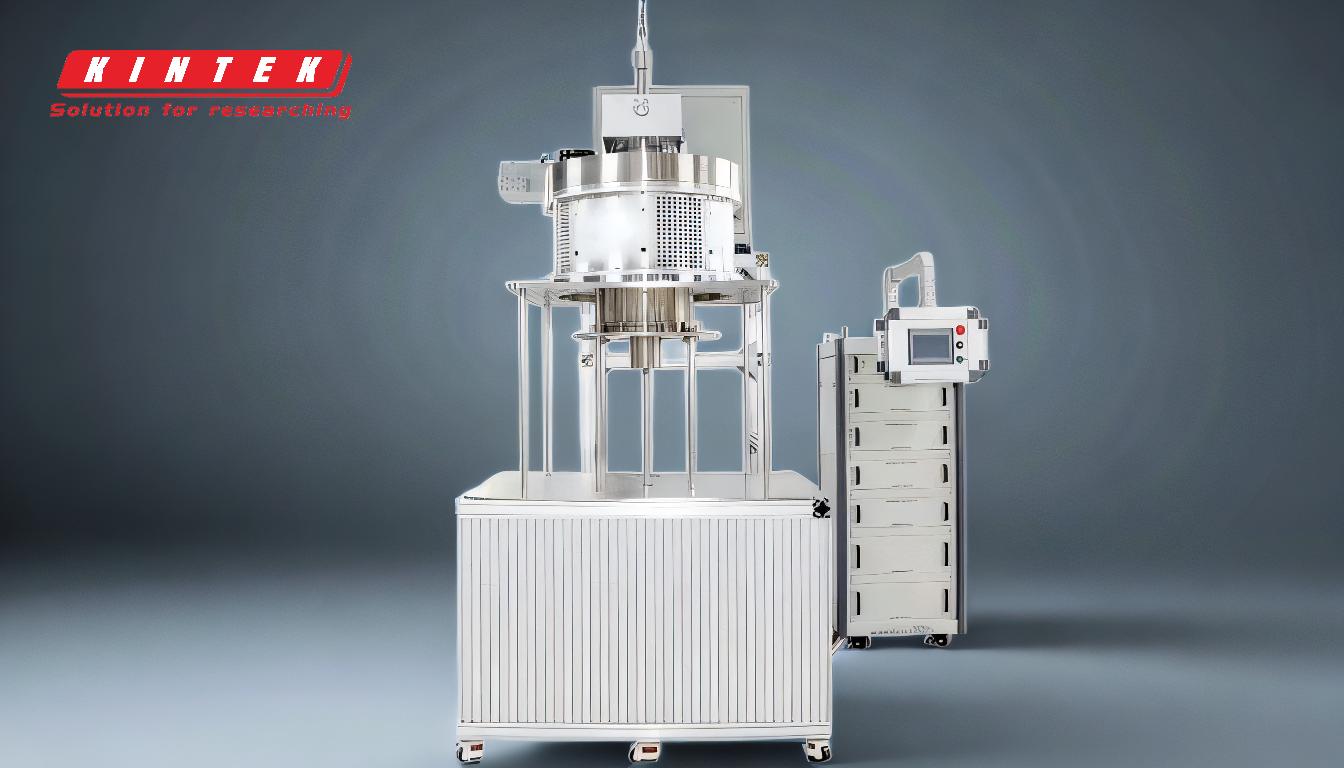
-
Materialbereich und Anwendbarkeit:
- PVD: Kann eine Vielzahl von Materialien abscheiden, darunter Metalle, Legierungen und Keramik. Aufgrund dieser Vielseitigkeit eignet es sich für Anwendungen, die unterschiedliche Materialeigenschaften erfordern.
- CVD: Hauptsächlich auf Keramik und Polymere beschränkt. Seine chemische Beschaffenheit schränkt die Auswahl an Materialien ein, ermöglicht jedoch hochreine Filme und komplexe Materialsynthesen.
-
Prozessbedingungen:
- PVD: Wird im Vakuum bei hohen Temperaturen durchgeführt und beinhaltet physikalische Prozesse wie Verdampfen oder Sputtern. Dies erfordert spezielle Ausrüstung, Vakuumbedingungen und erfahrene Bediener.
- CVD: Arbeitet im Vergleich zu PVD bei niedrigeren Temperaturen und beruht auf chemischen Reaktionen zur Abscheidung von Beschichtungen. Es sind keine Ultrahochvakuumbedingungen erforderlich, was es in manchen Fällen wirtschaftlicher macht.
-
Beschichtungseigenschaften:
- PVD: Erzeugt weniger dichte und weniger gleichmäßige Beschichtungen, lässt sich aber schneller auftragen. Der Sichtlinienaufprallprozess schränkt seine Fähigkeit ein, komplexe Geometrien gleichmäßig zu beschichten.
- CVD: Erzeugt dichtere, gleichmäßigere Beschichtungen mit ausgezeichneter Streukraft, sodass Löcher, tiefe Vertiefungen und komplizierte Formen effektiv beschichtet werden können.
-
Abscheidungsraten und -dicke:
- PVD: Hat im Allgemeinen niedrigere Abscheidungsraten, aber Techniken wie Elektronenstrahl-PVD (EBPVD) können hohe Raten (0,1 bis 100 μm/min) bei hoher Materialausnutzungseffizienz erzielen.
- CVD: Bietet höhere Abscheidungsraten und kann im Vergleich zu herkömmlichen Methoden dickere Beschichtungen erzeugen, die von Nanometern bis zu weniger als 20 Mikrometern reichen.
-
Temperatur- und Umgebungsaspekte:
- PVD: Erfordert hohe Temperaturen und Vakuumbedingungen, was die Verwendung für wärmeempfindliche Substrate einschränken kann. Außerdem sind Kühlsysteme zur Wärmeableitung erforderlich.
- CVD: Arbeitet bei niedrigeren Temperaturen (500–1100 °C) und erzeugt keine korrosiven Nebenprodukte, wodurch es umweltfreundlicher und für eine breitere Palette von Substraten geeignet ist.
-
Anwendungseignung:
- PVD: Ideal für Anwendungen, die schnelle Beschichtungsprozesse und eine große Auswahl an Materialien erfordern, wie z. B. verschleißfeste und korrosionsbeständige Beschichtungen.
- CVD: Besser geeignet für Anwendungen, die hochreine, gleichmäßige Beschichtungen auf komplexen Formen erfordern, wie z. B. Halbleiterbauelemente und moderne Werkzeuge.
-
Wirtschaftliche und betriebliche Faktoren:
- PVD: Erfordert erhebliche Investitionen in Vakuumsysteme und qualifizierte Arbeitskräfte, aber die schnellere Anwendungszeit kann die Kosten bei der Massenproduktion ausgleichen.
- CVD: Oft wirtschaftlicher aufgrund höherer Abscheidungsraten und der Möglichkeit, komplexe Geometrien ohne Ultrahochvakuum-Anforderungen zu beschichten.
Zusammenfassend lässt sich sagen, dass die Wahl zwischen CVD und PVD für die Werkzeugbeschichtung von den spezifischen Anforderungen der Anwendung abhängt, einschließlich Materialeigenschaften, Gleichmäßigkeit der Beschichtung, Abscheidungsraten und geometrischer Komplexität. Beide Methoden haben ihre einzigartigen Vorteile und Einschränkungen, sodass sie im Bereich der Oberflächentechnik eher komplementäre als konkurrierende Technologien darstellen.
Übersichtstabelle:
Aspekt | CVD | PVD |
---|---|---|
Materialbereich | Hauptsächlich Keramik und Polymere | Metalle, Legierungen und Keramik |
Prozessbedingungen | Niedrigere Temperaturen, chemische Reaktionen, kein Ultrahochvakuum erforderlich | Hohe Temperaturen, Vakuum, physikalische Prozesse wie Verdampfen/Sputtern |
Beschichtungseigenschaften | Dichter, gleichmäßiger, hervorragend für komplexe Formen | Weniger dichte, schnellere Anwendung, begrenzt durch Auftreffen auf Sichtlinie |
Ablagerungsraten | Höhere Raten, dickere Beschichtungen (Nanometer bis <20 Mikrometer) | Niedrigere Raten, aber EBPVD kann hohe Raten erreichen (0,1 bis 100 μm/min) |
Temperatur und Umgebung | Niedrigere Temperaturen (500°–1100°C), umweltfreundlich | Hohe Temperaturen, Vakuum, erfordern Kühlsysteme |
Anwendungseignung | Hochreine, gleichmäßige Beschichtungen für komplexe Formen (z. B. Halbleiter) | Schnelle Beschichtung, vielfältige Materialien (z. B. verschleißfest, korrosionsbeständig) |
Wirtschaftsfaktoren | Wirtschaftlich bei komplexen Geometrien, höhere Abschmelzleistung | Hohe Anfangsinvestition, aber schnellere Anwendung gleicht die Kosten aus |
Benötigen Sie Hilfe bei der Auswahl zwischen CVD und PVD für Ihre Werkzeugbeschichtungsanforderungen? Kontaktieren Sie noch heute unsere Experten für maßgeschneiderte Lösungen!