Sowohl die Elektronenstrahlverdampfung als auch die thermische Verdampfung sind Verfahren zur physikalischen Gasphasenabscheidung (PVD), mit denen dünne Schichten auf Substrate aufgebracht werden.Der Hauptunterschied liegt in der Methode zum Erhitzen des Ausgangsmaterials.Bei der thermischen Verdampfung wird ein Tiegel mit Hilfe von elektrischem Strom erhitzt, wodurch das Material schmilzt und verdampft, was es für Materialien mit niedrigerem Schmelzpunkt geeignet macht.Im Gegensatz dazu wird bei der Elektronenstrahlverdampfung ein hochenergetischer Elektronenstrahl verwendet, um das Ausgangsmaterial direkt zu erhitzen, wodurch Materialien mit hohem Schmelzpunkt wie Oxide verarbeitet werden können.Die Elektronenstrahlverdampfung bietet dichtere Beschichtungen, ein geringeres Risiko von Verunreinigungen und höhere Abscheidungsraten als die thermische Verdampfung.Die Wahl zwischen den beiden Verfahren hängt von den Materialeigenschaften und den gewünschten Schichteigenschaften ab.
Die wichtigsten Punkte werden erklärt:
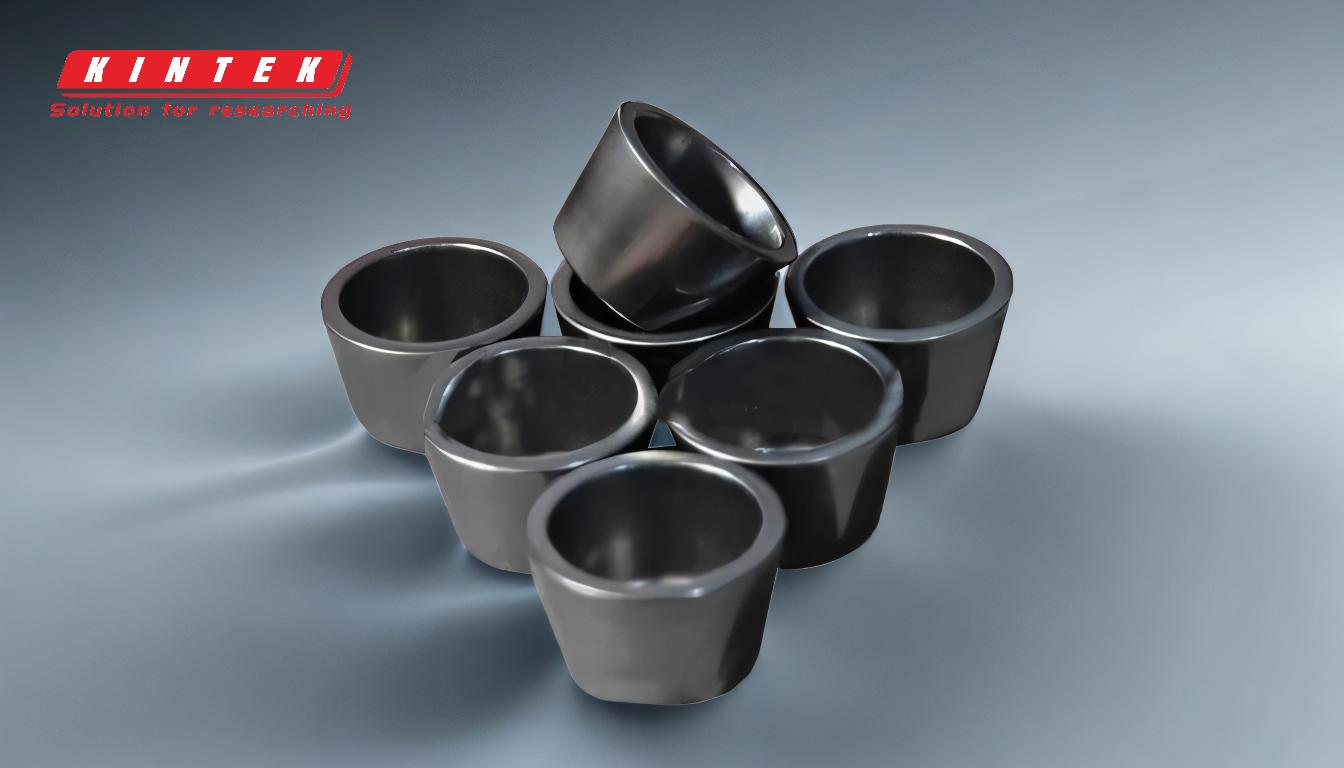
-
Mechanismus der Heizung:
- Thermische Verdampfung:Mit Hilfe von elektrischem Strom wird ein Schmelztiegel erhitzt, der wiederum das Ausgangsmaterial erhitzt und verdampft.Diese Methode ist indirekt und beruht auf Wärmeleitung.
- E-Strahl-Verdampfung:Nutzt einen hochenergetischen Elektronenstrahl zur direkten Erhitzung des Ausgangsmaterials.Der Elektronenstrahl überträgt kinetische Energie auf das Material und bringt es zum Verdampfen.Diese Methode ist direkter und effizienter für Materialien mit hohem Schmelzpunkt.
-
Eignung für Materialien:
- Thermische Verdampfung:Am besten geeignet für Materialien mit niedrigeren Schmelztemperaturen.Ideal für Metalle und Legierungen, die sich durch Widerstandserhitzung leicht schmelzen und verdampfen lassen.
- E-Strahl-Verdampfung:Geeignet für die Bearbeitung von Materialien mit hohem Schmelzpunkt, wie Oxide und hochschmelzende Metalle.Der hochenergetische Elektronenstrahl kann die notwendige Energie liefern, um diese Materialien zu verdampfen, ohne dass ein Tiegel erforderlich ist, um sie vorher zu schmelzen.
-
Eigenschaften des Films:
- Thermische Verdampfung:Erzeugt dünne Schichten, die aufgrund des indirekten Erhitzungsverfahrens und der möglichen Verunreinigung durch den Tiegel eine geringere Dichte und einen höheren Verunreinigungsgrad aufweisen können.
- E-Strahl-Verdampfung:Führt zu dichteren und reineren dünnen Schichten.Durch die direkte Erwärmung wird das Risiko einer Verunreinigung verringert, und der höhere Energieeintrag führt zu einer besseren Schichtqualität und -haftung.
-
Abscheiderate:
- Thermische Verdampfung:Die Abscheidungsrate ist im Allgemeinen niedriger als bei der Elektronenstrahlverdampfung.Die Rate wird durch die Effizienz der Wärmeübertragung vom Tiegel auf das Ausgangsmaterial begrenzt.
- E-Strahl-Verdampfung:Bietet eine höhere Abscheidungsrate aufgrund der direkten und effizienten Übertragung der Energie vom Elektronenstrahl auf das Ausgangsmaterial.Dies macht es geeigneter für Anwendungen, die eine schnelle Filmbildung erfordern.
-
Anwendungen:
- Thermische Verdampfung:Wird häufig bei Anwendungen eingesetzt, bei denen Materialien mit niedrigerem Schmelzpunkt ausreichen, wie z. B. bei der Abscheidung von Aluminium- oder Goldschichten in der Mikroelektronik und Optik.
- E-Strahl-Verdampfung:Bevorzugt für Hochleistungsanwendungen, die Materialien mit hohem Schmelzpunkt erfordern, z. B. für die Abscheidung dielektrischer Schichten, optischer Beschichtungen und Schutzschichten in der Luft- und Raumfahrt und der Halbleiterindustrie.
-
Anlagenkomplexität und Kosten:
- Thermische Verdampfung:Im Allgemeinen einfachere und kostengünstigere Geräte.Die Anlage besteht aus einem Widerstandsheizelement und einem Tiegel und ist daher einfacher zu warten und zu betreiben.
- E-Strahl-Verdampfung:Komplexer und kostspieliger, da ein Elektronenstrahlgenerator und entsprechende Kühlsysteme erforderlich sind.Die Vorteile in Bezug auf die Filmqualität und die Vielseitigkeit der Materialien rechtfertigen jedoch häufig die höheren Kosten.
-
Betriebliche Erwägungen:
- Thermische Verdampfung:Einfacher zu bedienen und zu warten, mit weniger beweglichen Teilen und einfacheren Steuersystemen.Es eignet sich für kleine und weniger anspruchsvolle Anwendungen.
- E-Strahl-Verdampfung:Erfordert aufgrund der Komplexität des Elektronenstrahlsystems eine genauere Kontrolle und Wartung.Es ist besser geeignet für Anwendungen mit hoher Präzision und hohem Durchsatz.
Zusammenfassend lässt sich sagen, dass sowohl die Elektronenstrahlverdampfung als auch die thermische Verdampfung wirksame PVD-Verfahren sind, die sich jedoch in Bezug auf ihre Heizmechanismen, die Materialeignung, die Schichteigenschaften und die Betriebskomplexität erheblich unterscheiden.Die Wahl zwischen den beiden Verfahren hängt von den spezifischen Anforderungen der Anwendung ab, einschließlich der Art des aufzubringenden Materials, der gewünschten Schichteigenschaften und der Budgetbeschränkungen.
Zusammenfassende Tabelle:
Aspekt | Thermische Verdampfung | E-Strahl-Verdampfung |
---|---|---|
Mechanismus der Erwärmung | Elektrischer Strom erhitzt einen Tiegel, wodurch das Material indirekt verdampft wird. | Ein hochenergetischer Elektronenstrahl erhitzt das Ausgangsmaterial direkt. |
Material-Eignung | Am besten für Materialien mit niedrigem Schmelzpunkt (z. B. Metalle, Legierungen). | Ideal für Werkstoffe mit hohem Schmelzpunkt (z. B. Oxide, hochschmelzende Metalle). |
Merkmale des Films | Geringere Dichte, höhere Verunreinigungsrisiken durch indirekte Erhitzung. | Dichtere, reinere Schichten mit besserer Haftung und Qualität. |
Abscheiderate | Geringere Rate aufgrund von indirekter Wärmeübertragung. | Höhere Rate durch direkte Energieübertragung. |
Anwendungen | Mikroelektronik, Optik (z. B. Aluminium, Goldschichten). | Luft- und Raumfahrt, Halbleiter, optische Beschichtungen (z. B. dielektrische Schichten). |
Kosten der Ausrüstung | Einfachere, weniger teure Einrichtung. | Komplexer und kostspieliger durch Elektronenstrahlsysteme. |
Einfacher Betrieb | Einfacher zu bedienen und zu warten, geeignet für Anwendungen in kleinem Maßstab. | Erfordert präzise Steuerung, besser für Anwendungen mit hoher Präzision und hohem Durchsatz. |
Benötigen Sie Hilfe bei der Auswahl des richtigen PVD-Verfahrens für Ihre Anwendung? Kontaktieren Sie noch heute unsere Experten für eine persönliche Beratung!