PVD (Physical Vapour Deposition) und CVD (Chemical Vapour Deposition) sind zwei bekannte Dünnschichtabscheidungstechniken, die zur Beschichtung von Substraten mit Materialien verwendet werden. Obwohl beide Methoden darauf abzielen, die Oberflächeneigenschaften zu verbessern, unterscheiden sie sich erheblich in ihren Prozessen, Betriebsbedingungen und resultierenden Beschichtungen. PVD umfasst die physikalische Verdampfung von Materialien, typischerweise im Vakuum, und deren Abscheidung auf einem Substrat ohne chemische Reaktionen. Im Gegensatz dazu beruht CVD auf chemischen Reaktionen zwischen gasförmigen Vorläufern und dem Substrat, um eine feste Beschichtung zu bilden. Die Wahl zwischen PVD und CVD hängt von Faktoren wie den gewünschten Beschichtungseigenschaften, dem Substratmaterial und den Anwendungsanforderungen ab. PVD wird oft aufgrund seiner niedrigeren Betriebstemperaturen, Umweltfreundlichkeit und überlegenen Verschleißfestigkeit bevorzugt, während CVD sich durch die Herstellung dichter, gleichmäßiger Beschichtungen bei höheren Temperaturen auszeichnet.
Wichtige Punkte erklärt:
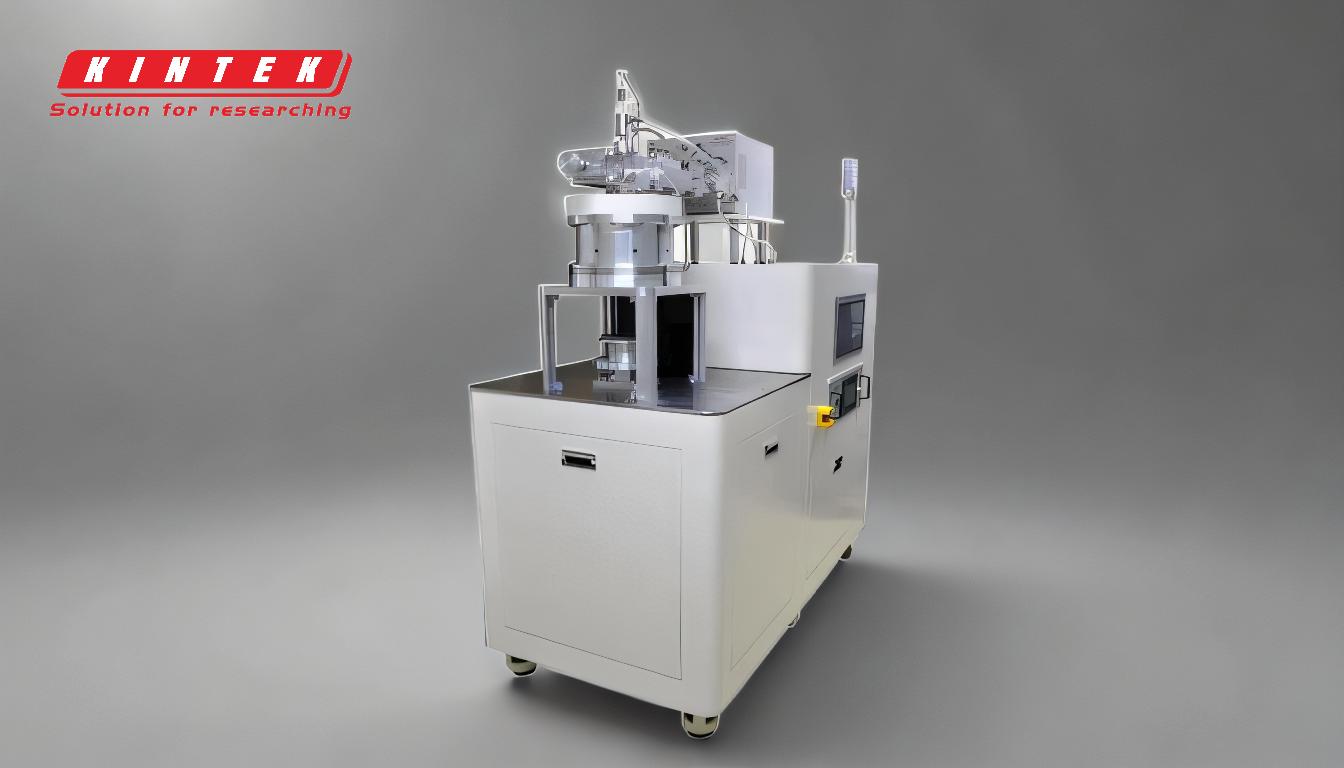
-
Ablagerungsmechanismus:
- PVD: Umfasst physikalische Prozesse wie Sputtern oder Verdampfen, um Material von einer festen Quelle auf das Substrat zu übertragen. Der Prozess ist ein Sichtlinienverfahren, das heißt, das Material wird ohne chemische Wechselwirkung direkt auf dem Substrat abgeschieden.
- CVD: Basiert auf chemischen Reaktionen zwischen gasförmigen Vorläufern und der Substratoberfläche. Die Reaktion erzeugt eine feste Beschichtung und die Abscheidung erfolgt multidirektional, was eine bessere Abdeckung komplexer Geometrien ermöglicht.
-
Betriebstemperaturen:
- PVD: Funktioniert bei relativ niedrigeren Temperaturen, typischerweise zwischen 250 °C und 450 °C. Dadurch ist es für temperaturempfindliche Untergründe geeignet.
- CVD: Erfordert höhere Temperaturen im Bereich von 450 °C bis 1050 °C, was die Verwendung bei bestimmten Materialien einschränken kann, aber zu dichteren und gleichmäßigeren Beschichtungen führt.
-
Beschichtungsmaterialien:
- PVD: Kann ein breites Spektrum an Materialien abscheiden, darunter Metalle, Legierungen und Keramik. Es ist vielseitig einsetzbar und eignet sich für Anwendungen, die harte, verschleißfeste Beschichtungen erfordern.
- CVD: Wird hauptsächlich zum Abscheiden von Keramik und Polymeren verwendet. Es ist ideal für Anwendungen, die hochreine, dichte Beschichtungen erfordern.
-
Beschichtungseigenschaften:
- PVD: Erzeugt Beschichtungen mit hoher Härte, ausgezeichneter Verschleißfestigkeit und geringer Reibung. Die Beschichtungen sind im Vergleich zu CVD weniger dicht und weniger gleichmäßig, lassen sich aber schneller auftragen.
- CVD: Ergibt dichtere, gleichmäßigere Beschichtungen mit hervorragender Haftung. Allerdings ist der Prozess langsamer und es kann zu Zugspannungen kommen, die zu feinen Rissen führen.
-
Anwendungen:
- PVD: Wird häufig in Branchen verwendet, die verschleißfeste Beschichtungen erfordern, wie z. B. Schneidwerkzeuge, Automobilkomponenten und dekorative Oberflächen. Durch den Betrieb bei niedrigeren Temperaturen eignet es sich für temperaturempfindliche Substrate.
- CVD: Weit verbreitet in der Halbleiterfertigung, optischen Beschichtungen und Anwendungen, die hochreine, dichte Filme erfordern. Seine Fähigkeit, komplexe Geometrien zu beschichten, macht es ideal für komplizierte Komponenten.
-
Umwelt- und Wirtschaftsaspekte:
- PVD: Umweltfreundlich, da keine gefährlichen Nebenprodukte entstehen. Aufgrund der Notwendigkeit von Vakuumgeräten und energieintensiven Prozessen ist es jedoch im Allgemeinen teurer.
- CVD: Abhängig von den verwendeten Vorläufern können gefährliche Nebenprodukte entstehen. Während es für die Produktion im großen Maßstab kostengünstig ist, können die hohen Betriebstemperaturen und die Anforderungen an die Handhabung von Chemikalien die betriebliche Komplexität erhöhen.
Zusammenfassend hängt die Wahl zwischen PVD und CVD von den spezifischen Anforderungen der Anwendung ab, einschließlich der gewünschten Beschichtungseigenschaften, des Substratmaterials und der betrieblichen Einschränkungen. PVD wird oft wegen seiner Vielseitigkeit, niedrigeren Temperaturen und überlegenen Verschleißfestigkeit bevorzugt, während CVD wegen seiner Fähigkeit, dichte, gleichmäßige Beschichtungen auf komplexen Geometrien zu erzeugen, bevorzugt wird.
Übersichtstabelle:
Aspekt | PVD | CVD |
---|---|---|
Ablagerungsmechanismus | Physikalische Prozesse (Sputtern/Verdampfen), Sichtlinienabscheidung. | Chemische Reaktionen zwischen gasförmigen Vorläufern und Substrat, multidirektional. |
Betriebstemperaturen | 250°C bis 450°C, geeignet für temperaturempfindliche Untergründe. | 450 °C bis 1050 °C, ideal für dichte, gleichmäßige Beschichtungen. |
Beschichtungsmaterialien | Metalle, Legierungen, Keramik. | Keramik, Polymere. |
Beschichtungseigenschaften | Hohe Härte, Verschleißfestigkeit, geringe Reibung, weniger dicht. | Dichter, gleichmäßiger, bessere Haftung, langsamerer Prozess. |
Anwendungen | Schneidwerkzeuge, Automobilkomponenten, dekorative Oberflächen. | Halbleiter, optische Beschichtungen, komplexe Komponenten. |
Umweltauswirkungen | Umweltfreundlich, keine gefährlichen Nebenprodukte. | Kann gefährliche Nebenprodukte produzieren, höhere betriebliche Komplexität. |
Benötigen Sie Hilfe bei der Auswahl zwischen PVD und CVD für Ihr Projekt? Kontaktieren Sie noch heute unsere Experten für persönliche Beratung!