PVD- (Physical Vapor Deposition) und DLC- (Diamond-Like Carbon) Fässer unterscheiden sich in erster Linie durch die Beschichtungsmaterialien, die Anwendungsprozesse und die daraus resultierenden Eigenschaften.PVD-Beschichtungen werden im Vakuum bei hohen Temperaturen aufgebracht, wobei physikalische Verfahren zur Abscheidung einer breiten Palette von Materialien, einschließlich Metallen, Legierungen und Keramiken, zum Einsatz kommen.Diese Beschichtungen sind bekannt für ihre hohe Reinheit, Gleichmäßigkeit und hervorragende Haftung, wodurch sie härter und korrosionsbeständiger sind als galvanische Beschichtungen.DLC-Beschichtungen hingegen sind eine spezielle Art von PVD-Beschichtungen, die Kohlenstoff enthalten, um eine diamantähnliche Struktur zu erzeugen, die außergewöhnliche Härte, geringe Reibung und Verschleißfestigkeit bietet.Während PVD-Beschichtungen vielseitig und langlebig sind, bieten DLC-Beschichtungen aufgrund ihrer einzigartigen kohlenstoffbasierten Struktur eine überlegene Leistung bei Anwendungen mit hoher Beanspruchung und Reibung.
Die wichtigsten Punkte werden erklärt:
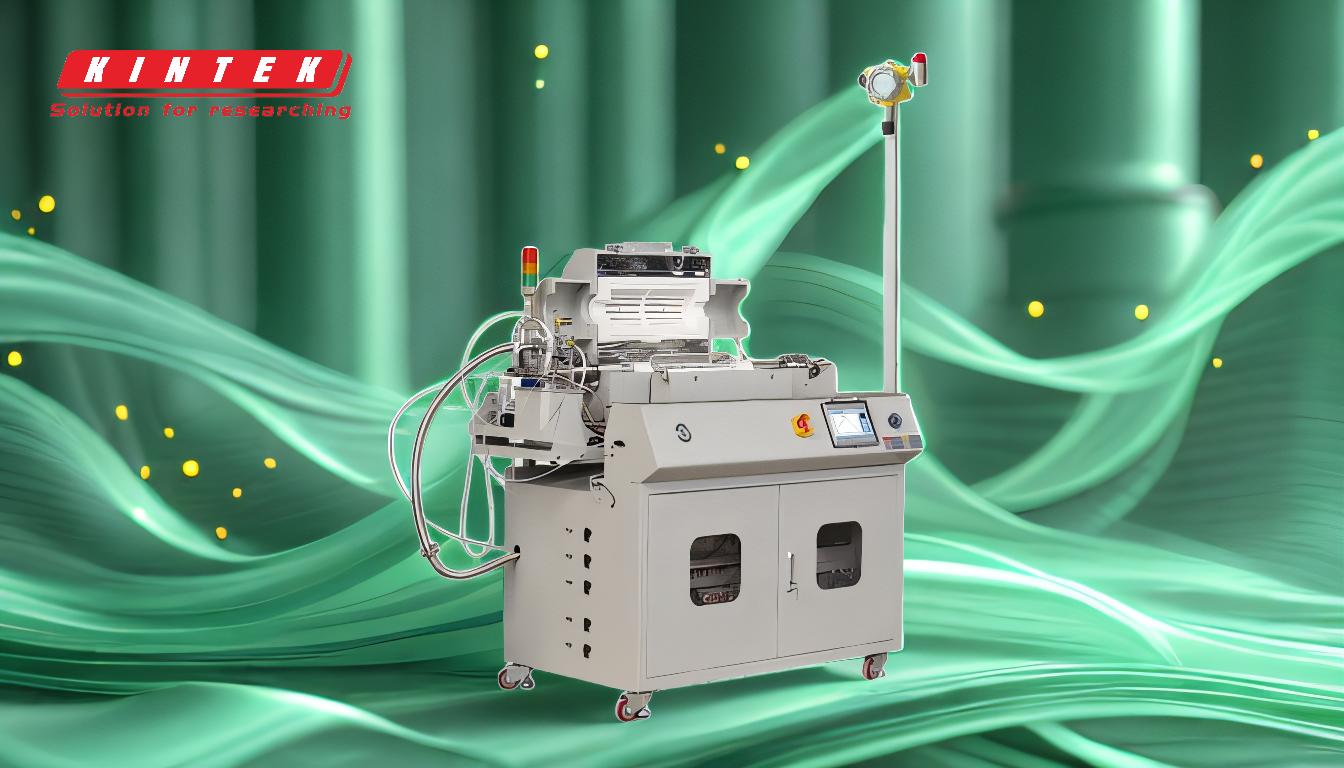
-
Beschichtungsmaterialien und Zusammensetzung:
- PVD-Beschichtungen: Mit PVD kann eine breite Palette von Materialien abgeschieden werden, darunter Metalle, Legierungen und Keramik.Diese Vielseitigkeit ermöglicht maßgeschneiderte Beschichtungen, die bestimmte Leistungsanforderungen erfüllen, wie z. B. Härte, Korrosionsbeständigkeit und thermische Stabilität.
- DLC-Beschichtungen: DLC ist eine spezielle Form der PVD-Beschichtung, bei der Kohlenstoff zu einer diamantähnlichen Struktur verarbeitet wird.Das Ergebnis ist eine Beschichtung, die die Härte von Diamant mit der Flexibilität von Kohlenstoff kombiniert und eine außergewöhnliche Verschleißfestigkeit und geringe Reibung bietet.
-
Anwendungsprozess:
- PVD-Verfahren: PVD-Beschichtungen werden in einem Vakuum bei hohen Temperaturen durch physikalische Verfahren wie Sputtern oder Verdampfen aufgebracht.Das Ergebnis ist eine dichte, gleichmäßige Beschichtung mit hervorragender Haftung auf dem Substrat.
- DLC-Verfahren: DLC-Beschichtungen werden ebenfalls mit PVD-Techniken aufgebracht, wobei jedoch Kohlenstoffatome in die Beschichtungsstruktur eingebaut werden.Dieser Prozess kann angepasst werden, um die Härte, den Reibungskoeffizienten und andere Eigenschaften der DLC-Beschichtung zu verändern.
-
Eigenschaften der Beschichtung:
- PVD-Eigenschaften: PVD-Beschichtungen zeichnen sich durch hohe Reinheit, Gleichmäßigkeit und hervorragende Haftung aus.Sie sind härter und korrosionsbeständiger als galvanische Beschichtungen und zeichnen sich durch hohe Temperatur- und Schlagfestigkeit, hervorragende Abriebfestigkeit und Haltbarkeit aus.
- DLC-Eigenschaften: DLC-Beschichtungen bieten eine außergewöhnliche Härte (ähnlich der von Diamant), geringe Reibung und ausgezeichnete Verschleißfestigkeit.Sie eignen sich besonders für Anwendungen, die eine hohe Leistung unter extremen Bedingungen erfordern, z. B. in Umgebungen mit hoher Belastung und hoher Reibung.
-
Leistung in Anwendungen:
- PVD-Anwendungen: PVD-Beschichtungen sind in verschiedenen Branchen weit verbreitet, z. B. in der Automobil-, Luft- und Raumfahrtindustrie sowie im Werkzeugbau, wo Haltbarkeit und Korrosionsbeständigkeit entscheidend sind.Sie eignen sich aufgrund ihrer Druckspannungseigenschaften für Anwendungen mit unterbrochenem Schnitt, wie z. B. Fräsen.
- DLC-Anwendungen: DLC-Beschichtungen sind ideal für Anwendungen, bei denen geringe Reibung und hohe Verschleißfestigkeit erforderlich sind, wie z. B. bei Automobilkomponenten (z. B. Kolbenringe, Nockenwellen) und Schneidwerkzeugen.Dank ihrer einzigartigen Struktur auf Kohlenstoffbasis sind sie besonders wirksam bei der Verringerung von Reibung und Verschleiß unter hohen Belastungen.
-
Kosten und Komplexität:
- PVD-Kosten: PVD-Beschichtungen sind in der Regel teurer als herkömmliche Beschichtungen wie die Galvanotechnik, was auf den komplexen Prozess der Vakuumabscheidung und die verwendeten hochwertigen Materialien zurückzuführen ist.
- DLC-Kosten: DLC-Beschichtungen können aufgrund des speziellen Kohlenstoffabscheidungsverfahrens und der fortschrittlichen Eigenschaften, die sie bieten, teurer sein als herkömmliche PVD-Beschichtungen.Die langfristigen Vorteile in Bezug auf Leistung und Haltbarkeit rechtfertigen jedoch häufig die höheren Anschaffungskosten.
-
Oberflächengüte und Ästhetik:
- PVD-Beschichtung: PVD-Beschichtungen haben einen glatten, metallischen Glanz, der die Oberfläche des Werkzeugs gut reflektiert.Sie erfordern kein zusätzliches Polieren für ein gutes Finish und sind daher ästhetisch ansprechend für sichtbare Komponenten.
- DLC-Finish: DLC-Beschichtungen haben aufgrund des Kohlenstoffgehalts in der Regel eine dunklere, matte Oberfläche.Sie reflektieren zwar nicht so stark wie PVD-Beschichtungen, bieten aber ein glattes, modernes Aussehen, das bei Hochleistungsanwendungen oft erwünscht ist.
Zusammenfassend lässt sich sagen, dass sowohl PVD- als auch DLC-Beschichtungen zwar erhebliche Vorteile gegenüber herkömmlichen Beschichtungen bieten, sich aber aufgrund ihrer einzigartigen Eigenschaften für unterschiedliche Anwendungen eignen.PVD-Beschichtungen sind vielseitig und haltbar und eignen sich daher für eine breite Palette industrieller Anwendungen.DLC-Beschichtungen mit ihrer außergewöhnlichen Härte und geringen Reibung sind ideal für stark beanspruchte Umgebungen mit hoher Reibung, in denen Leistung und Langlebigkeit entscheidend sind.
Zusammenfassende Tabelle:
Blickwinkel | PVD-Beschichtungen | DLC-Beschichtungen |
---|---|---|
Beschichtungsmaterialien | Metalle, Legierungen, Keramiken | Kohlenstoffbasierte, diamantähnliche Struktur |
Anwendungsprozess | Vakuumabscheidung bei hohen Temperaturen (Sputtern/Verdampfen) | PVD mit Kohlenstoffeinlagerung für maßgeschneiderte Eigenschaften |
Eigenschaften | Hohe Reinheit, Gleichmäßigkeit, Haftung, Härte, Korrosionsbeständigkeit | Außergewöhnliche Härte, geringe Reibung, Verschleißfestigkeit |
Anwendungen | Automobilindustrie, Luft- und Raumfahrt, Werkzeugbau (unterbrochenes Schneiden, Fräsen) | Hochbelastete Umgebungen mit hoher Reibung (Kolbenringe, Nockenwellen, Schneidwerkzeuge) |
Kosten | Höher als bei der Galvanotechnik aufgrund des komplexen Prozesses | Höher als Standard-PVD aufgrund der speziellen Kohlenstoffabscheidung |
Oberflächenbeschaffenheit | Glatt, metallisch glänzend | Dunkleres, mattes Finish |
Benötigen Sie Hilfe bei der Auswahl der richtigen Beschichtung für Ihre Anwendung? Kontaktieren Sie noch heute unsere Experten für eine persönliche Beratung!