Das herkömmliche Sintern und das selektive Lasersintern (SLS) sind beides Verfahren zur Herstellung fester Gegenstände aus pulverförmigen Materialien. Sie unterscheiden sich jedoch erheblich in ihren Methoden, Anwendungen und ihrer Eignung für verschiedene Produktionsanforderungen.Beim traditionellen Sintern, das häufig in der Pulvermetallurgie eingesetzt wird, wird pulverförmiges Material in einer Form verdichtet und dann bis knapp unter den Schmelzpunkt erhitzt, um die Partikel zu verschmelzen.Diese Methode ist hochpräzise, kostengünstig für die Massenproduktion und erfordert Formen.Im Gegensatz dazu ist das selektive Lasersintern ein Verfahren der additiven Fertigung (3D-Druck), bei dem ein Laser verwendet wird, um pulverförmiges Material selektiv Schicht für Schicht zu verschmelzen, wobei eine CAD-Datei als Vorlage dient.SLS erfordert keine Formen, bietet eine größere Designflexibilität und eignet sich besser für die Herstellung von Prototypen und Kleinserien, ist jedoch im Allgemeinen weniger genau und teurer als das traditionelle Sintern.
Die wichtigsten Punkte werden erklärt:
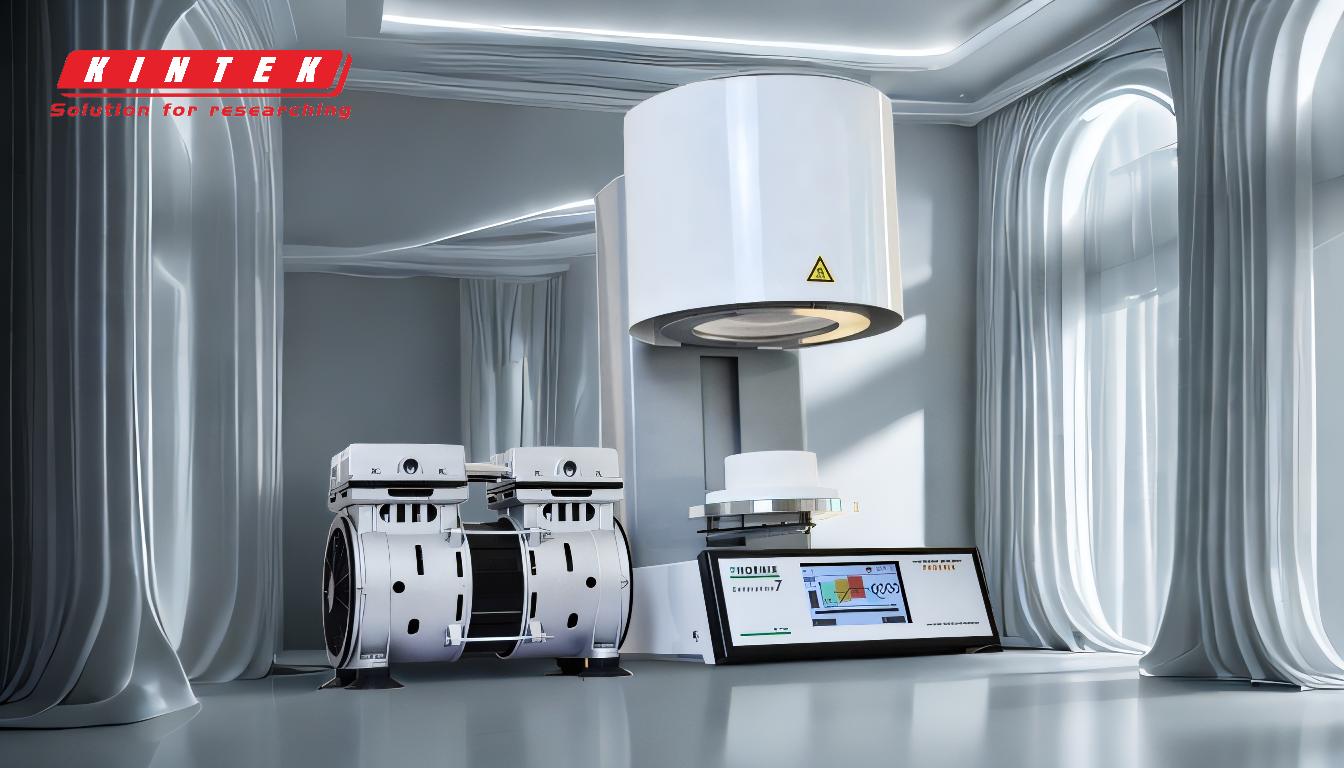
-
Prozess-Methodik:
- Traditionelle Sinterung:Bei diesem Verfahren wird pulverförmiges Material in einer Form verdichtet und anschließend erhitzt, um die Partikel zu verschmelzen.Die Form bestimmt die Gestalt des Endprodukts.
- Selektives Laser-Sintern (SLS):Verwendet einen Laser, um pulverförmiges Material Schicht für Schicht selektiv zu verschmelzen, wobei eine CAD-Datei als Leitfaden dient.Für dieses Verfahren ist keine Form erforderlich, so dass auch komplexere Geometrien möglich sind.
-
Anforderung an die Form:
- Traditionelle Sinterung:Erfordert eine Form, um das Objekt zu formen, was die Designflexibilität einschränken und die Kosten für komplexe Formen erhöhen kann.
- Selektives Laser-Sintern:Es wird keine Form benötigt, was die Herstellung komplizierter und komplexer Designs ohne zusätzliche Werkzeugkosten ermöglicht.
-
Eignung für die Produktion:
- Traditionelle Sinterung:Aufgrund ihrer Genauigkeit und Kosteneffizienz ist sie besser für die kostengünstige Massenproduktion geeignet.Es ist ideal für die Herstellung großer Mengen identischer Teile.
- Selektives Laser-Sintern:Besser geeignet für die Herstellung von Prototypen und Kleinserien.Aufgrund höherer Kosten und langsamerer Produktionsraten wird es in der Regel nicht für die Massenproduktion verwendet.
-
Genauigkeit und Kosten:
- Traditionelle Sinterung:Im Allgemeinen genauer und billiger für die Massenproduktion.Die Verwendung von Gussformen gewährleistet gleichbleibende und präzise Teile.
- Selektives Laser-Sintern:Weniger genau und teurer im Vergleich zum traditionellen Sintern.Da es keine Formen gibt und das Verfahren Schicht für Schicht erfolgt, kann es zu leichten Abweichungen kommen.
-
Flexibilität bei der Gestaltung:
- Traditionelle Sinterung:Begrenzt durch die Notwendigkeit von Gussformen, die die Komplexität der Designs einschränken können.
- Selektives Laser-Sintern:Bietet eine größere Designflexibilität und ermöglicht die Herstellung komplexer und komplizierter Geometrien, die mit herkömmlichen Sinterverfahren nur schwer oder gar nicht zu realisieren wären.
-
Anwendungen:
- Traditionelle Sinterung:Wird häufig in Branchen eingesetzt, in denen hohe Stückzahlen produziert werden müssen, z. B. in der Automobil- und Luftfahrtindustrie.
- Selektives Laser-Sintern:Wird häufig in Branchen eingesetzt, die schnelles Prototyping, kundenspezifische Teile und Kleinserienfertigung erfordern, z. B. medizinische Geräte und Konsumgüter.
Zusammenfassend lässt sich sagen, dass sowohl das herkömmliche Sintern als auch das selektive Lasersintern zur Herstellung fester Objekte aus pulverförmigen Werkstoffen verwendet werden, sich aber in ihren Methoden, Formanforderungen, Produktionseignung, Genauigkeit, Kosten, Designflexibilität und Anwendungen unterscheiden.Das traditionelle Sintern ist kostengünstiger und genauer für die Massenproduktion, während das selektive Lasersintern eine größere Designflexibilität bietet und besser für die Herstellung von Prototypen und Kleinserien geeignet ist.
Zusammenfassende Tabelle:
Blickwinkel | Traditionelles Sintern | Selektives Laser-Sintern (SLS) |
---|---|---|
Methodik des Verfahrens | Verdichtung des Pulvers in einer Form, dann Erhitzen zum Schmelzen | Verwendet einen Laser, um das Pulver Schicht für Schicht zu schmelzen (keine Form) |
Erforderliche Form | Erfordert Gussformen | Keine Gussformen erforderlich |
Eignung für die Produktion | Ideal für die Massenproduktion | Am besten geeignet für die Herstellung von Prototypen und Kleinserien |
Genauigkeit | Höhere Genauigkeit bei Massenproduktion | Weniger genau aufgrund des Schicht-für-Schicht-Verfahrens |
Kosten | Kostengünstig für Großserienproduktion | Teurer, geeignet für Kleinserien |
Flexibilität bei der Gestaltung | Begrenzt durch die Anforderungen an die Form | Hohe Flexibilität, unterstützt komplexe Geometrien |
Anwendungen | Automobilindustrie, Luft- und Raumfahrt (großvolumige Teile) | Medizinische Geräte, Konsumgüter (Prototyping) |
Sind Sie noch unsicher, welches Sinterverfahren für Ihr Projekt am besten geeignet ist? Kontaktieren Sie noch heute unsere Experten für eine persönliche Beratung!