Die am besten geeignete Temperatur für das Brennen von Zement in einem Drehrohrofen liegt normalerweise zwischen 1400°C bis 1500°C .Dieser Temperaturbereich gewährleistet die ordnungsgemäße Bildung von Klinker, dem Zwischenprodukt bei der Zementherstellung.Unterhalb dieses Bereichs können die für die Klinkerbildung erforderlichen chemischen Reaktionen unvollständig sein, während Temperaturen oberhalb dieses Bereichs zu übermäßigem Energieverbrauch und möglichen Schäden an der Ofenauskleidung führen können.Bei dem Verfahren werden die Rohmaterialien (Kalkstein, Ton und andere Zusatzstoffe) auf diesen Temperaturbereich erhitzt, um die chemischen Reaktionen zur Herstellung von Zementklinker zu erleichtern.
Die wichtigsten Punkte erklärt:
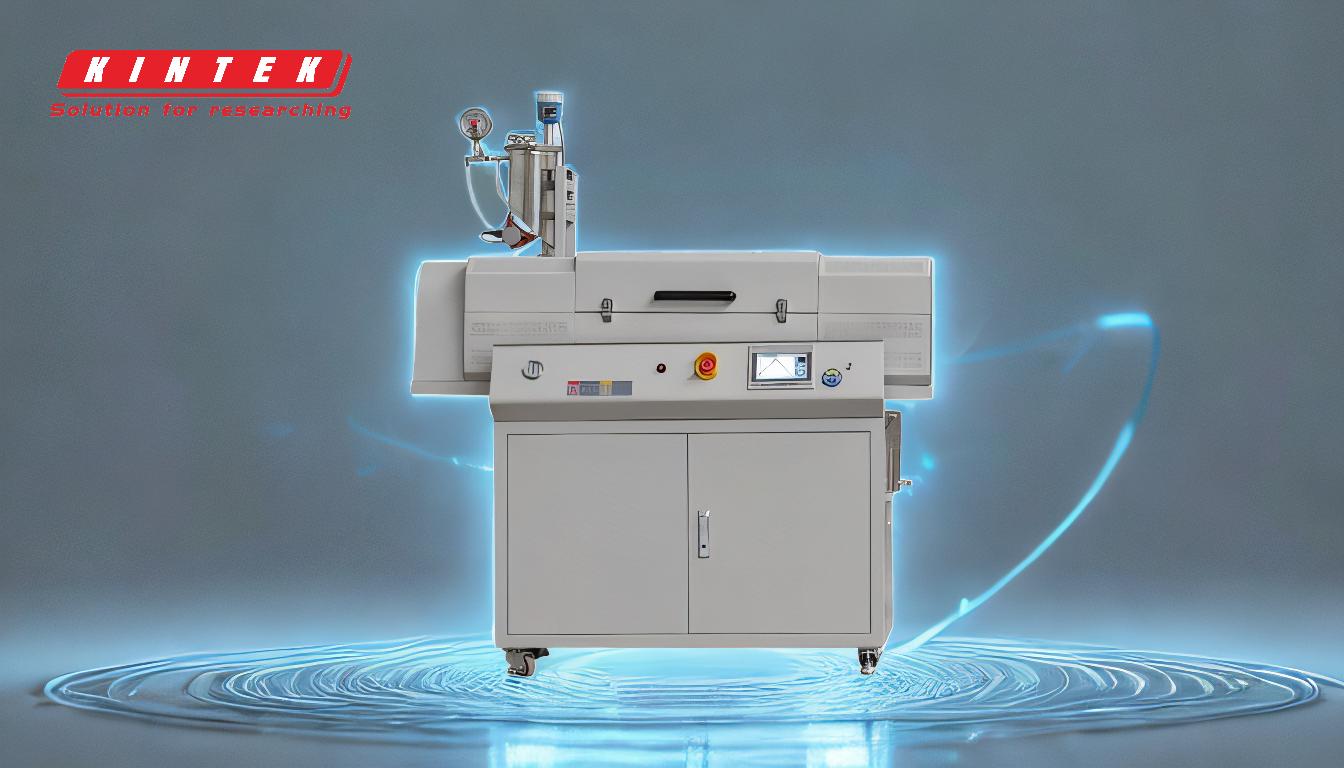
-
Optimaler Temperaturbereich für die Zementverbrennung:
- Der ideale Temperaturbereich für das Brennen von Zement in einem Drehrohrofen ist 1400°C bis 1500°C .Dieser Bereich ist entscheidend für die Bildung von Klinker, dem Hauptbestandteil von Zement.
- Bei dieser Temperatur durchlaufen die Rohmaterialien eine Reihe chemischer Reaktionen, darunter die Kalzinierung (Zersetzung von Kalkstein in Kalk) und die Sinterung (Bildung von Klinkerverbindungen wie Alit und Belit).
-
Warum 1400°C bis 1500°C geeignet sind:
- Chemische Reaktionen:Bei Temperaturen unter 1400°C können die für die Klinkerbildung erforderlichen chemischen Reaktionen nicht vollständig ablaufen, was zu minderwertigem Klinker führt.Bei Temperaturen über 1500°C können die Reaktionen zu intensiv werden, was zu einer Überverbrennung und Energieineffizienz führt.
- Energie-Effizienz:Wenn die Temperatur innerhalb dieses Bereichs gehalten wird, ist eine effiziente Energienutzung gewährleistet.Überhöhte Temperaturen führen zu einem höheren Brennstoffverbrauch und höheren Betriebskosten.
- Schutz der Ofenauskleidung:Bei längerer Einwirkung von Temperaturen über 1500°C kann die feuerfeste Auskleidung des Ofens beschädigt werden, was seine Lebensdauer verkürzt und die Wartungskosten erhöht.
-
Vergleich mit anderen Ofentypen:
- Indirekte Drehrohröfen:Diese Öfen arbeiten in der Regel mit niedrigeren Temperaturen (1200-1300°C für das Ofenrohr und weniger als 1150°C für das Material).Sie sind für die Zementherstellung nicht geeignet, da sie die für die Klinkerbildung erforderlichen Temperaturen nicht erreichen können.
- Elektrische Drehrohröfen:Mit einer maximalen Arbeitstemperatur von 1100°C sind elektrische Drehrohröfen für die Zementherstellung ebenfalls ungeeignet, da sie die erforderlichen Klinkerbildungstemperaturen nicht erreichen können.
-
Faktoren, die die Auswahl der Temperatur beeinflussen:
- Zusammensetzung des Rohmaterials:Die chemische Zusammensetzung des Rohmaterials kann die erforderliche Brenntemperatur beeinflussen.Beispielsweise können Rohstoffe mit einem höheren Siliziumdioxidgehalt etwas höhere Temperaturen erfordern.
- Konstruktion des Ofens:Die Konstruktion des Drehrohrofens, einschließlich seiner Länge, seines Durchmessers und seiner feuerfesten Auskleidung, kann die Temperaturverteilung und die Effizienz der Wärmeübertragung beeinflussen.
- Brennstoffart:Die Art des verwendeten Brennstoffs (z. B. Kohle, Erdgas oder alternative Brennstoffe) kann die Verbrennungstemperatur und damit die Gesamttemperatur des Ofens beeinflussen.
-
Praktische Überlegungen:
- Temperaturkontrolle:Um optimale Verbrennungsbedingungen aufrechtzuerhalten, ist eine präzise Temperaturregelung unerlässlich.Dies wird in der Regel durch fortschrittliche Kontrollsysteme erreicht, die die Brennstoff- und Luftzufuhr überwachen und anpassen.
- Kühlungsprozess:Nachdem der Klinker geformt ist, muss er schnell abgekühlt werden, um seine Qualität zu erhalten.Dies geschieht in der Regel in einem an den Ofen angeschlossenen Kühler, in dem der Klinker von etwa 1400 °C auf unter 200 °C abgekühlt wird.
-
Einfluss der Temperatur auf die Zementqualität:
- Klinker Qualität:Die Temperatur wirkt sich direkt auf die Qualität des Klinkers aus, was wiederum die Festigkeit und Haltbarkeit des Zementendprodukts beeinflusst.
- Verbrauch von Energie:Der Betrieb innerhalb des optimalen Temperaturbereichs minimiert den Energieverbrauch und macht das Verfahren kostengünstiger und umweltfreundlicher.
- Umweltaspekte:Die Aufrechterhaltung der richtigen Temperatur trägt dazu bei, den Ausstoß von Schadstoffen wie Stickoxiden (NOx) und Schwefeldioxid (SO2) zu verringern, die bei der Verbrennung bei hohen Temperaturen als Nebenprodukte entstehen.
Zusammenfassend lässt sich sagen, dass die am besten geeignete Temperatur für das Brennen von Zement in einem Drehrohrofen zwischen 1400°C und 1500°C liegt.Dieser Bereich gewährleistet eine effiziente Klinkerbildung, Energieeffizienz und den Schutz der Ofenauskleidung und trägt gleichzeitig zur Herstellung von Qualitätszement bei.
Zusammenfassende Tabelle:
Aspekt | Einzelheiten |
---|---|
Optimale Temperatur | 1400°C bis 1500°C |
Zweck | Gewährleistet eine ordnungsgemäße Klinkerbildung und Energieeffizienz |
Chemische Reaktionen | Kalzinierung und Sinterung erfolgen in diesem Bereich |
Energie-Effizienz | Minimiert den Brennstoffverbrauch und die Betriebskosten |
Schutz der Ofenauskleidung | Verhindert Schäden an der feuerfesten Auskleidung |
Zementqualität | Hochwertiger Klinker führt zu haltbarem und festem Zement |
Auswirkungen auf die Umwelt | Reduziert den Ausstoß von NOx und SO2 |
Benötigen Sie fachkundige Beratung zur Optimierung Ihres Drehrohrofens für die Zementherstellung? Kontaktieren Sie uns noch heute um mehr zu erfahren!