Physical Vapor Deposition (PVD) und Chemical Vapor Deposition (CVD) sind fortschrittliche Beschichtungstechnologien zur Verbesserung der Oberflächeneigenschaften von Werkstoffen, z. B. Härte, Verschleißfestigkeit und Korrosionsbeständigkeit.Beim PVD-Verfahren wird ein festes Material im Vakuum verdampft und auf ein Substrat aufgebracht, während beim CVD-Verfahren chemische Reaktionen von gasförmigen Ausgangsstoffen zur Bildung einer Beschichtung genutzt werden.Beide Verfahren haben unterschiedliche Schritte, Vorteile und Anwendungen.PVD ist schneller und arbeitet bei niedrigeren Temperaturen, so dass es sich für ein breiteres Spektrum von Materialien eignet, während CVD dichtere und gleichmäßigere Beschichtungen erzeugt, aber höhere Temperaturen und längere Bearbeitungszeiten erfordert.
Die wichtigsten Punkte erklärt:
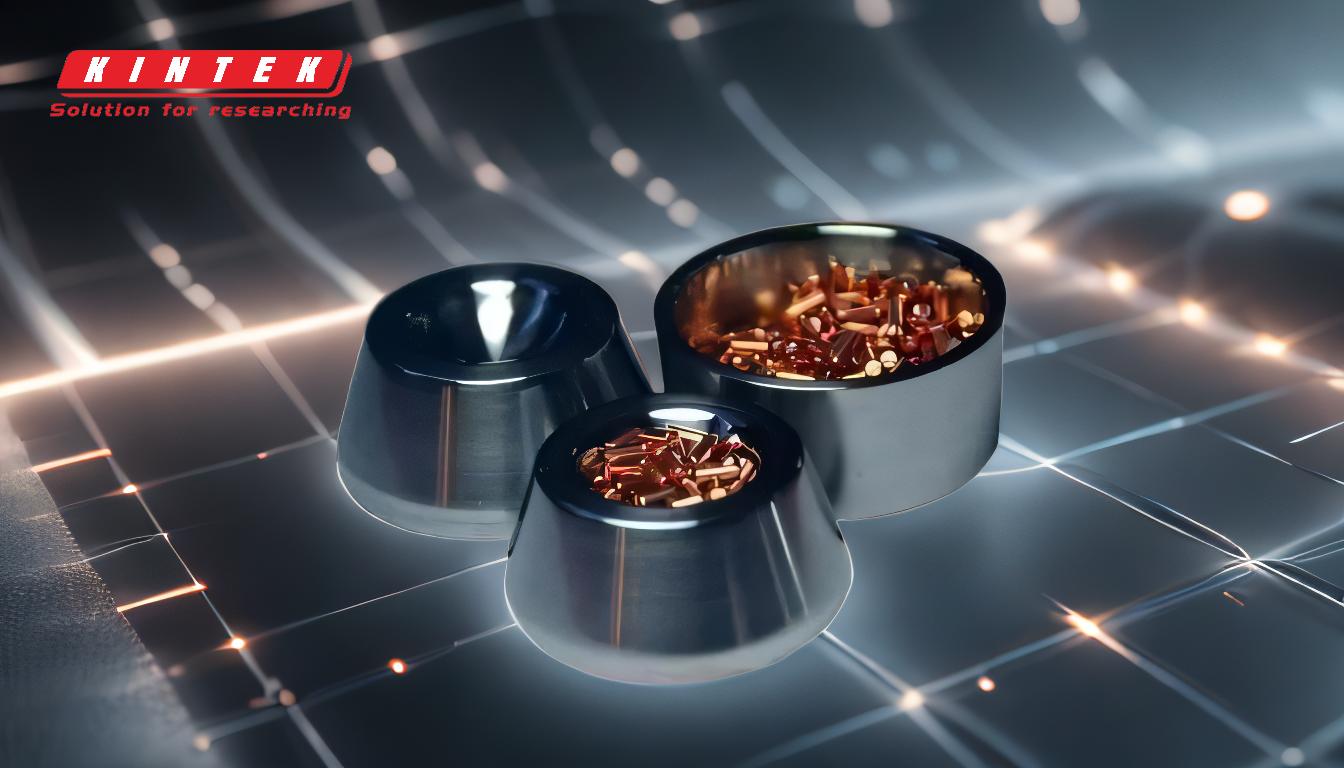
-
Überblick über PVD- und CVD-Beschichtungsprozesse:
- PVD:Bei diesem Verfahren wird ein festes Material im Vakuum verdampft und auf ein Substrat aufgebracht.Es handelt sich um ein physikalisches Verfahren, das bei niedrigeren Temperaturen (etwa 500 °C) abläuft und für Metalle, Legierungen und Keramik geeignet ist.
- CVD:Nutzt chemische Reaktionen von gasförmigen Vorläufern bei hohen Temperaturen (800-1000 °C), um eine Beschichtung aufzubringen.Es ist in der Regel auf Keramiken und Polymere beschränkt und erzeugt dickere, dichtere und gleichmäßigere Beschichtungen.
-
Schritte im PVD-Beschichtungsprozess:
- Schritt 1: Reinigung des Substrats:Der Untergrund wird gereinigt, um Verunreinigungen zu entfernen und eine bessere Haftung der Beschichtung zu gewährleisten.
- Schritt 2: Vorbehandlung:Das Substrat wird einer Vorbehandlung unterzogen, um die Haftung der Beschichtung zu verbessern, was häufig eine Oberflächenaktivierung oder ein Ätzen beinhaltet.
- Schritt 3: Beschichtung:Das Zielmaterial wird mit Techniken wie Elektronenstrahl, Ionenbeschuss oder kathodischem Lichtbogen verdampft.Das verdampfte Material wird dann zum Substrat transportiert und als Dünnschicht abgeschieden.
- Schritt 4: Qualitätskontrolle:Das beschichtete Substrat wird geprüft, um sicherzustellen, dass die Beschichtung den vorgegebenen Standards entspricht, z. B. hinsichtlich Dicke, Gleichmäßigkeit und Haftung.
- Schritt 5: Endbearbeitung:Um das Aussehen oder die Leistung der Beschichtung zu verbessern, können zusätzliche Behandlungen wie Polieren oder Glühen durchgeführt werden.
-
Schritte im CVD-Beschichtungsprozess:
- Schritt 1: Vorläufer Einführung:Gasförmige Ausgangsstoffe werden in die Reaktionskammer eingeleitet.
- Schritt 2: Chemische Reaktion:Die Vorläufer reagieren bei hohen Temperaturen (800-1000 °C) und bilden das gewünschte Beschichtungsmaterial.
- Schritt 3: Abscheidung:Die Reaktionsprodukte lagern sich auf dem Substrat ab und bilden eine dichte und gleichmäßige Beschichtung.
- Schritt 4: Nachbehandlung:Das beschichtete Substrat kann zusätzlich behandelt werden, z. B. durch Glühen oder Oberflächenveredelung, um seine Eigenschaften zu verbessern.
-
Hauptunterschiede zwischen PVD und CVD:
- Temperatur:PVD arbeitet bei niedrigeren Temperaturen (etwa 500 °C), während CVD hohe Temperaturen (800-1000 °C) erfordert.
- Dicke der Beschichtung:PVD erzeugt dünnere Schichten (3~5μm), während CVD zu dickeren Schichten führt (10~20μm).
- Dichte und Gleichmäßigkeit der Beschichtung:CVD-Beschichtungen sind im Vergleich zu PVD-Beschichtungen dichter und gleichmäßiger.
- Material-Kompatibilität:Mit PVD kann ein breiteres Spektrum von Materialien abgeschieden werden, darunter Metalle, Legierungen und Keramiken, während CVD in der Regel auf Keramiken und Polymere beschränkt ist.
- Verarbeitungszeit:PVD ist schneller und eignet sich daher für Anwendungen, die eine kurze Durchlaufzeit erfordern, während CVD aufgrund der damit verbundenen chemischen Reaktionen länger dauert.
-
Anwendungen von PVD und CVD:
- PVD:Wird häufig für Anwendungen verwendet, die eine hohe Verschleißfestigkeit erfordern, wie z. B. Schneidwerkzeuge, dekorative Beschichtungen und Komponenten für die Luft- und Raumfahrt.Es eignet sich auch für unterbrochene Schneidprozesse wie das Fräsen.
- CVD:Ideal für Anwendungen, die dicke, dichte und gleichmäßige Beschichtungen erfordern, wie z. B. die Halbleiterherstellung, verschleißfeste Beschichtungen für kontinuierliche Schneidverfahren wie Drehen und Hochtemperaturanwendungen.
-
Vorteile und Beschränkungen:
- PVD Vorteile:Schnellere Verarbeitung, niedrigere Betriebstemperaturen und Kompatibilität mit einer breiten Palette von Materialien.
- PVD-Einschränkungen:Weniger dichte und weniger gleichmäßige Beschichtungen im Vergleich zu CVD.
- CVD Vorteile:Dichtere und gleichmäßigere Schichten, geeignet für Hochtemperaturanwendungen.
- CVD Beschränkungen:Höhere Verarbeitungstemperaturen, längere Verarbeitungszeiten und eingeschränkte Materialkompatibilität.
Durch das Verständnis der detaillierten Schritte und Unterschiede zwischen PVD- und CVD-Beschichtungsprozessen können Käufer von Anlagen und Verbrauchsmaterialien fundierte Entscheidungen treffen, die auf den spezifischen Anforderungen ihrer Anwendungen basieren, wie z. B. den gewünschten Beschichtungseigenschaften, der Materialkompatibilität und den Verarbeitungseinschränkungen.
Zusammenfassende Tabelle:
Blickwinkel | PVD | CVD |
---|---|---|
Temperatur | Niedriger (um 500 °C) | Höher (800~1000 °C) |
Dicke der Beschichtung | Dünner (3~5μm) | Dicker (10~20μm) |
Dichte der Beschichtung | Weniger dicht | Dichter und gleichmäßiger |
Material-Kompatibilität | Metalle, Legierungen, Keramiken | Keramiken, Polymere |
Verarbeitungszeit | Schneller | Länger |
Anwendungen | Schneidwerkzeuge, dekorative Beschichtungen, Komponenten für die Luft- und Raumfahrt | Halbleiterfertigung, verschleißfeste Beschichtungen, Hochtemperaturanwendungen |
Benötigen Sie Hilfe bei der Auswahl des richtigen Beschichtungsverfahrens für Ihre Anwendung? Kontaktieren Sie noch heute unsere Experten !