Thermisches Cracken ist ein Verfahren, das in der Erdölindustrie eingesetzt wird, um große Kohlenwasserstoffmoleküle durch Wärmezufuhr in kleinere, besser nutzbare Moleküle aufzuspalten.Der Temperaturbereich für thermisches Cracken liegt normalerweise zwischen 450°C bis 750°C (842°F bis 1382°F) je nach dem spezifischen Verfahren und dem verwendeten Ausgangsmaterial.Bei diesen hohen Temperaturen brechen die chemischen Bindungen in den Kohlenwasserstoffen auf, was zur Bildung kleinerer Moleküle wie Olefine, Paraffine und andere leichtere Kohlenwasserstoffe führt.Die genaue Temperatur hängt von Faktoren wie der Art des Ausgangsmaterials, den gewünschten Produkten und dem spezifischen thermischen Crackverfahren (z. B. Steamcracking, Visbreaking oder Verkokung) ab.
Die wichtigsten Punkte erklärt:
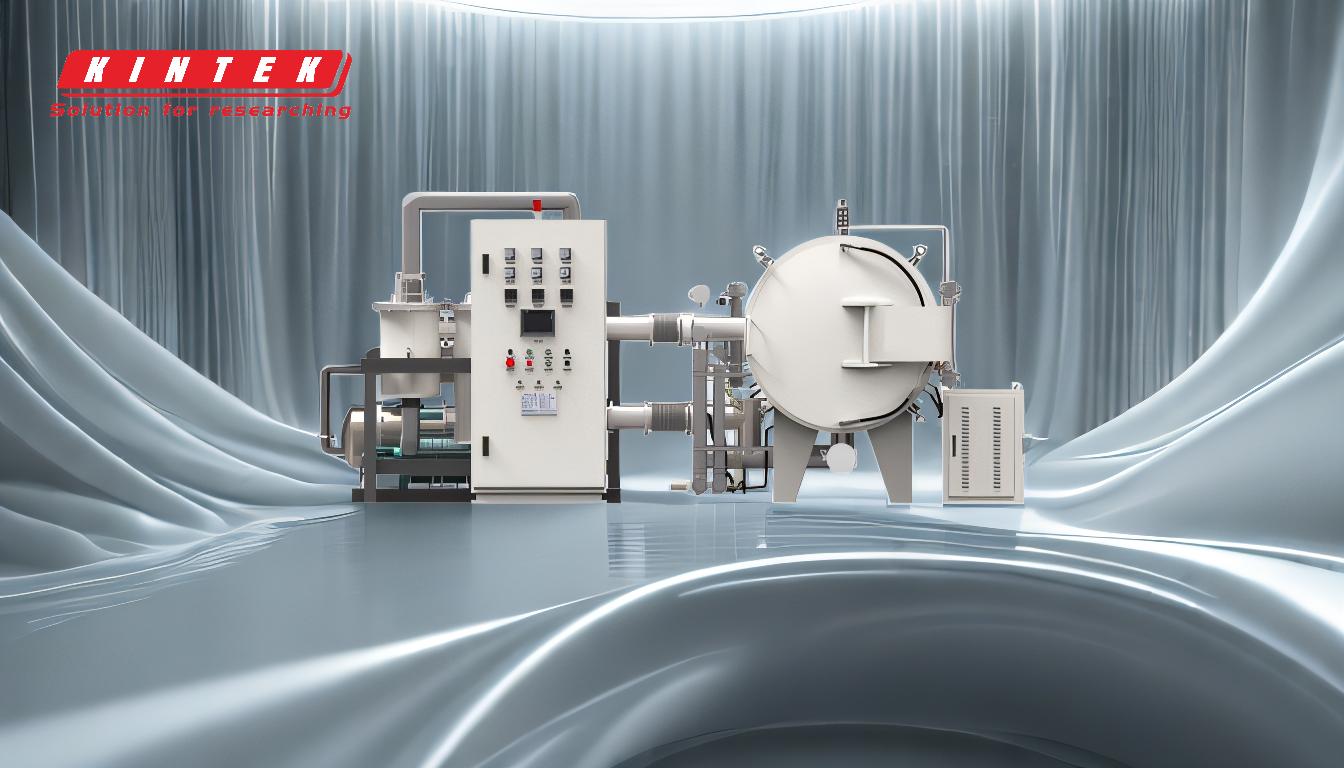
-
Definition des thermischen Crackens
- Thermisches Cracken ist ein chemischer Prozess, bei dem große Kohlenwasserstoffmoleküle durch Wärmezufuhr in kleinere Moleküle zerlegt werden.
- Es wird in der Erdölindustrie häufig eingesetzt, um leichtere, wertvollere Produkte wie Benzin, Diesel und petrochemische Rohstoffe herzustellen.
-
Temperaturbereich für thermisches Cracken
- Der typische Temperaturbereich für die thermische Rissbildung ist 450°C bis 750°C (842°F bis 1382°F) .
- Dieser Bereich stellt sicher, dass die chemischen Bindungen in den Kohlenwasserstoffmolekülen wirksam aufgebrochen werden, ohne dass es zu übermäßigem Abbau oder unerwünschten Nebenreaktionen kommt.
-
Faktoren, die die Temperatur beeinflussen
- Art des Ausgangsmaterials:Schwerere Einsatzstoffe (z. B. Rohölrückstände) erfordern höhere Temperaturen als leichtere Einsatzstoffe (z. B. Naphtha).
- Gewünschte Produkte:Die Temperatur wird auf der Grundlage der Zielprodukte angepasst.Für die Herstellung von Ethylen und Propylen (die in der Petrochemie verwendet werden) sind zum Beispiel oft höhere Temperaturen erforderlich.
- Prozess-Typ:Verschiedene thermische Crackverfahren (z. B. Steamcracking, Visbreaking, Coking) arbeiten in unterschiedlichen Temperaturbereichen.
-
Arten von thermischen Crackverfahren
-
Dampfkracken:
- Wird hauptsächlich zur Herstellung von Olefinen (z. B. Ethylen, Propylen) verwendet.
- Arbeitet bei Temperaturen von 750°C bis 900°C (1382°F bis 1652°F) .
- Dem Einsatzmaterial wird Dampf zugesetzt, um die Koksbildung zu verringern und die Ausbeute zu verbessern.
-
Visbreaking:
- Ein mildes thermisches Crackverfahren, das zur Verringerung der Viskosität von schweren Rückständen eingesetzt wird.
- Wird bei niedrigeren Temperaturen durchgeführt, typischerweise 450°C bis 500°C (842°F bis 932°F) .
-
Verkokung:
- Ein starkes thermisches Krackverfahren, mit dem schwere Rückstände in leichtere Fraktionen und festen Koks zerlegt werden.
- Arbeitet bei Temperaturen von 450°C bis 550°C (842°F bis 1022°F) .
-
Dampfkracken:
-
Die Bedeutung der Temperaturkontrolle
- Optimale Ausbeute:Die Aufrechterhaltung der richtigen Temperatur gewährleistet eine maximale Ausbeute der gewünschten Produkte.
- Minimierung von Nebenreaktionen:Zu hohe Temperaturen können zu unerwünschten Nebenreaktionen führen, wie z. B. zur Bildung von Koks oder Gas.
- Energie-Effizienz:Eine ordnungsgemäße Temperaturregelung senkt den Energieverbrauch und die Betriebskosten.
-
Anwendungen des thermischen Crackens
- Erdölraffination:Umwandlung schwerer Rohölfraktionen in leichtere, wertvollere Produkte.
- Petrochemische Produktion:Zur Herstellung von Rohstoffen für Kunststoffe, synthetischen Kautschuk und andere Chemikalien.
- Energieproduktion:Verbesserung der Qualität der Brennstoffe und Verringerung des Abfalls.
-
Herausforderungen und Überlegungen
- Koks-Bildung:Hohe Temperaturen können zu Koksablagerungen führen, die die Anlagen verstopfen und die Effizienz verringern können.
- Auswahl des Materials:Die Geräte müssen so konstruiert sein, dass sie hohen Temperaturen und korrosiven Umgebungen standhalten.
- Auswirkungen auf die Umwelt:Beim thermischen Cracken entstehen Treibhausgase und andere Schadstoffe, die wirksame Vermeidungsstrategien erfordern.
Durch das Verständnis der Temperaturanforderungen und der Faktoren, die das thermische Cracken beeinflussen, können die Einkäufer von Anlagen und Verbrauchsmaterialien fundierte Entscheidungen über die Materialien, Technologien und Prozesse treffen, die zur Optimierung des Betriebs und zur Erzielung der gewünschten Ergebnisse erforderlich sind.
Zusammenfassende Tabelle:
Aspekt | Einzelheiten |
---|---|
Temperaturbereich | 450°C bis 750°C (842°F bis 1382°F) |
Wichtige Faktoren | Art des Rohstoffs, gewünschte Produkte, Verfahrenstyp |
Prozess-Typen | Dampfkracken, Visbreaking, Verkokung |
Anwendungen | Erdölraffination, petrochemische Produktion, Energieerzeugung |
Herausforderungen | Koksbildung, Materialauswahl, Umweltauswirkungen |
Benötigen Sie auf Ihre Bedürfnisse zugeschnittene Lösungen für das thermische Cracken? Kontaktieren Sie noch heute unsere Experten für Beratung!