Die Sputterbeschichtung ist eine vielseitige und weit verbreitete Technik in verschiedenen Industriezweigen und wissenschaftlichen Anwendungen.Dabei werden dünne Materialschichten mit Hilfe eines Sputterverfahrens auf ein Substrat aufgebracht.Diese Technik ist unerlässlich für die Herstellung leitfähiger Beschichtungen, die Vorbereitung von Proben für die Mikroskopie und die Herstellung dünner Schichten für fortschrittliche Technologien.Die Sputterbeschichtung ist besonders wertvoll in Bereichen wie der Herstellung von Solarzellen, der Mikroelektronik und der Materialwissenschaft, wo präzise und gleichmäßige Beschichtungen von entscheidender Bedeutung sind.Das Verfahren beruht auf der Erzeugung eines Plasmas, das die Atome des Zielmaterials ausstößt, die sich dann mit dem Substrat verbinden und eine dünne, gleichmäßige Schicht bilden.Diese Methode gewährleistet eine starke Bindung auf atomarer Ebene und qualitativ hochwertige Ergebnisse.
Die wichtigsten Punkte erklärt:
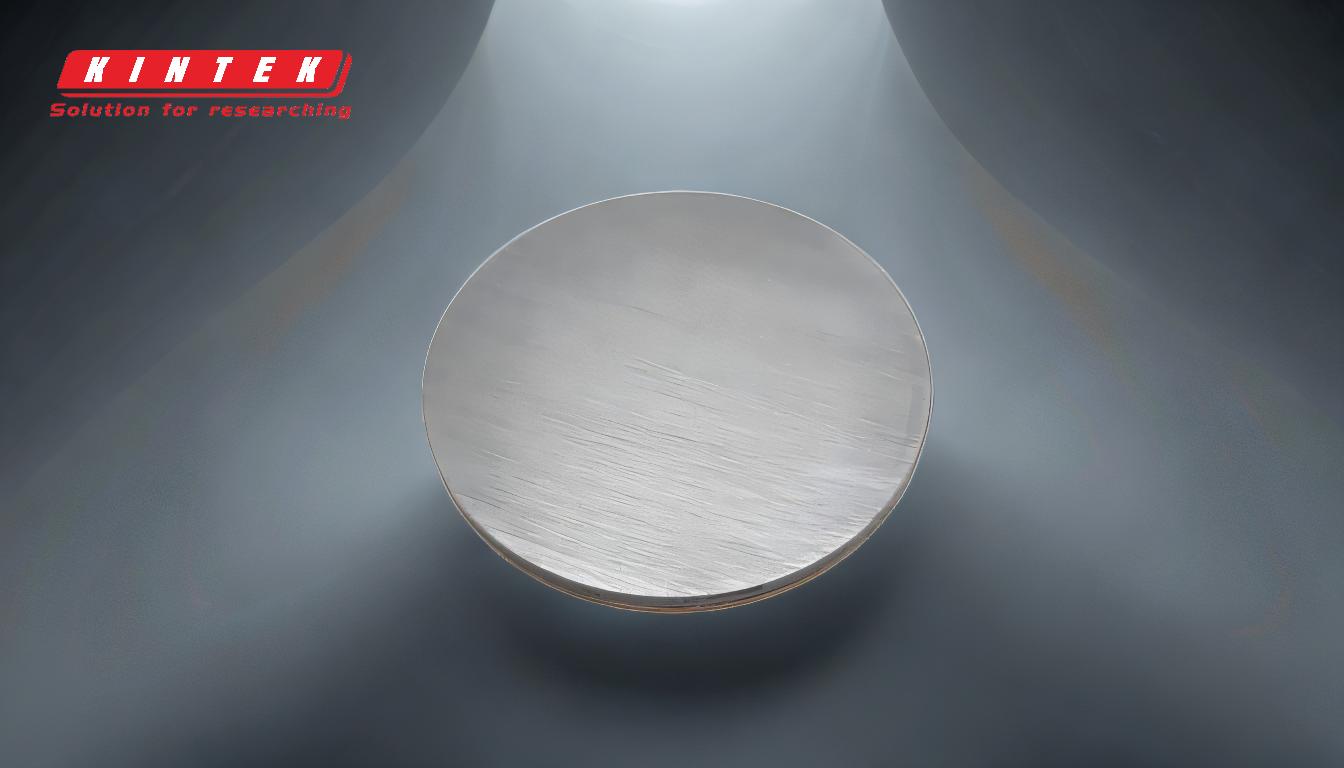
-
Was ist Sputter-Beschichtung?
- Bei der Sputterbeschichtung handelt es sich um ein Verfahren zur physikalischen Gasphasenabscheidung (PVD), mit dem dünne Materialschichten auf ein Substrat aufgebracht werden.
- Dabei wird durch elektrische Aufladung einer Sputterkathode ein Plasma erzeugt, das Atome aus einem Zielmaterial ausstößt.
- Diese ausgestoßenen Atome werden auf das Substrat gerichtet, wo sie durch Impulsübertragung eine dünne, gleichmäßige Beschichtung bilden.
-
Wie funktioniert die Sputter-Beschichtung?
- An das Zielmaterial wird eine Hochspannung angelegt, wodurch ein Plasma aus Gasatomen, freien Elektronen und positiv geladenen Ionen entsteht.
- Magnetfelder konzentrieren das Plasma, und energiereiche Ionen beschießen das Target, wodurch Atome abgesputtert werden.
- Die gesputterten Atome wandern durch die Vakuumkammer und lagern sich auf dem Substrat ab und bilden einen dünnen Film.
- Zu den wichtigsten Komponenten gehören die Vakuumkammer, das Targetmaterial, die Kühlsysteme und die Magnetfelder, die eine stabile und gleichmäßige Erosion gewährleisten.
-
Anwendungen der Sputter-Beschichtung:
- Elektronenmikroskopie: Sputter-Coater sind in Labors für Rasterelektronenmikroskopie (SEM) für die Vorbereitung nicht leitender Proben unerlässlich.Eine dünne leitfähige Beschichtung (z. B. Gold oder Platin) wird auf die Probe aufgetragen, um Aufladung zu verhindern und die Bildqualität zu verbessern.
- Solarpaneele: Mit Hilfe der Sputterbeschichtung werden dünne Schichten aus Materialien wie Indium-Zinn-Oxid (ITO) auf Solarpaneele aufgebracht, um deren Effizienz und Leitfähigkeit zu verbessern.
- Mikroelektronik: In der Halbleiterindustrie wird es häufig zur Herstellung dünner Schichten für integrierte Schaltkreise, Sensoren und andere elektronische Komponenten verwendet.
- Architektonisches Glas: Die Sputterbeschichtung wird eingesetzt, um reflektierende oder niedrig emittierende Schichten auf Glas aufzutragen und so die Energieeffizienz und Ästhetik zu verbessern.
- Luft- und Raumfahrt und Automobilindustrie: Durch Sputtern hergestellte Dünnschichten werden in diesen Branchen für Schutzbeschichtungen, Sensoren und moderne Materialien verwendet.
- Flachbildschirme: Die Sputter-Beschichtung ist entscheidend für die Abscheidung leitender und optischer Schichten in Displays, wie LCDs und OLEDs.
-
Vorteile der Sputter-Beschichtung:
- Gleichmäßigkeit: Das Verfahren erzeugt sehr gleichmäßige dünne Schichten, selbst bei komplexen Geometrien.
- Vielseitigkeit: Es kann eine breite Palette von Materialien ablagern, darunter Metalle, Legierungen und Keramiken.
- Starke Adhäsion: Der Impulsübertragungsprozess gewährleistet eine starke Bindung auf atomarer Ebene zwischen der Beschichtung und dem Substrat.
- Hohe Reinheit: Die Sputterbeschichtung erfolgt im Vakuum, wodurch Verunreinigungen minimiert werden und hochreine Schichten entstehen.
- Skalierbarkeit: Er ist sowohl für kleine Laboranwendungen als auch für die industrielle Großproduktion geeignet.
-
Hauptkomponenten eines Sputter Coaters:
- Vakuumkammer: Bietet eine kontrollierte Umgebung, um die Kontamination zu minimieren und gleichbleibende Ergebnisse zu gewährleisten.
- Zielmaterial: Das abzuscheidende Material, das an die Kathode geklebt oder geklemmt wird.
- Kühlungssysteme: Bewältigung der während des Sputterprozesses erzeugten Wärme, um die Stabilität zu erhalten und Schäden zu vermeiden.
- Magnetische Felder: Erhöhen die Plasmakonzentration und gewährleisten eine gleichmäßige Erosion des Zielmaterials.
-
Herausforderungen und Überlegungen:
- Wärmemanagement: Das Sputtering-Verfahren erzeugt erhebliche Wärme, die effektive Kühlsysteme erfordert.
- Kosten: Anlagen und Materialien für die Sputterbeschichtung können teuer sein, insbesondere bei hochreinen oder speziellen Anwendungen.
- Kompliziertheit: Das Verfahren erfordert eine präzise Steuerung von Parametern wie Spannung, Druck und Temperatur, um die gewünschten Ergebnisse zu erzielen.
Zusammenfassend lässt sich sagen, dass die Sputter-Beschichtung eine wichtige Technologie mit vielfältigen Anwendungen in verschiedenen Branchen ist.Ihre Fähigkeit, hochwertige, gleichmäßige dünne Schichten zu erzeugen, macht sie für Fortschritte in der Elektronik, Energie und Materialwissenschaft unverzichtbar.Das Verständnis ihrer Prinzipien, Vorteile und Herausforderungen ist entscheidend für die Nutzung ihres vollen Potenzials in verschiedenen Anwendungen.
Zusammenfassende Tabelle:
Aspekt | Einzelheiten |
---|---|
Verfahren | Physikalische Gasphasenabscheidung (PVD) unter Verwendung eines Plasmas zum Ausstoßen von Atomen des Zielmaterials. |
Anwendungen | Elektronenmikroskopie, Sonnenkollektoren, Mikroelektronik, Architekturglas. |
Vorteile | Gleichmäßigkeit, Vielseitigkeit, starke Haftung, hohe Reinheit, Skalierbarkeit. |
Wichtige Komponenten | Vakuumkammer, Targetmaterial, Kühlsysteme, Magnetfelder. |
Herausforderungen | Wärmemanagement, Kosten, Komplexität. |
Entdecken Sie, wie die Sputterbeschichtung Ihre Projekte verbessern kann. Kontaktieren Sie noch heute unsere Experten für maßgeschneiderte Lösungen!