Die physikalische Gasphasenabscheidung (PVD) ist eine weit verbreitete Technik zur Abscheidung dünner Schichten, deren Dicke in der Regel von atomaren Schichten (weniger als 10 Å) bis zu mehreren Mikrometern (µm) reicht. Welche Schichtdicke erreicht wird, hängt von der Anwendung ab, ob es sich um dekorative Zwecke, funktionelle Beschichtungen oder fortgeschrittene technologische Anwendungen handelt. Für dekorative Beschichtungen sind dünnere Schichten (etwa 0,2 µm) üblich, während funktionelle Beschichtungen, wie sie in der Elektronik oder bei verschleißfesten Anwendungen eingesetzt werden, dickere Schichten (bis zu 5 µm oder mehr) erfordern können. Die Vielseitigkeit des PVD-Verfahrens ermöglicht eine präzise Steuerung der Schichtdicke, so dass es sich für eine Vielzahl von Branchen und Anwendungen eignet.
Die wichtigsten Punkte werden erklärt:
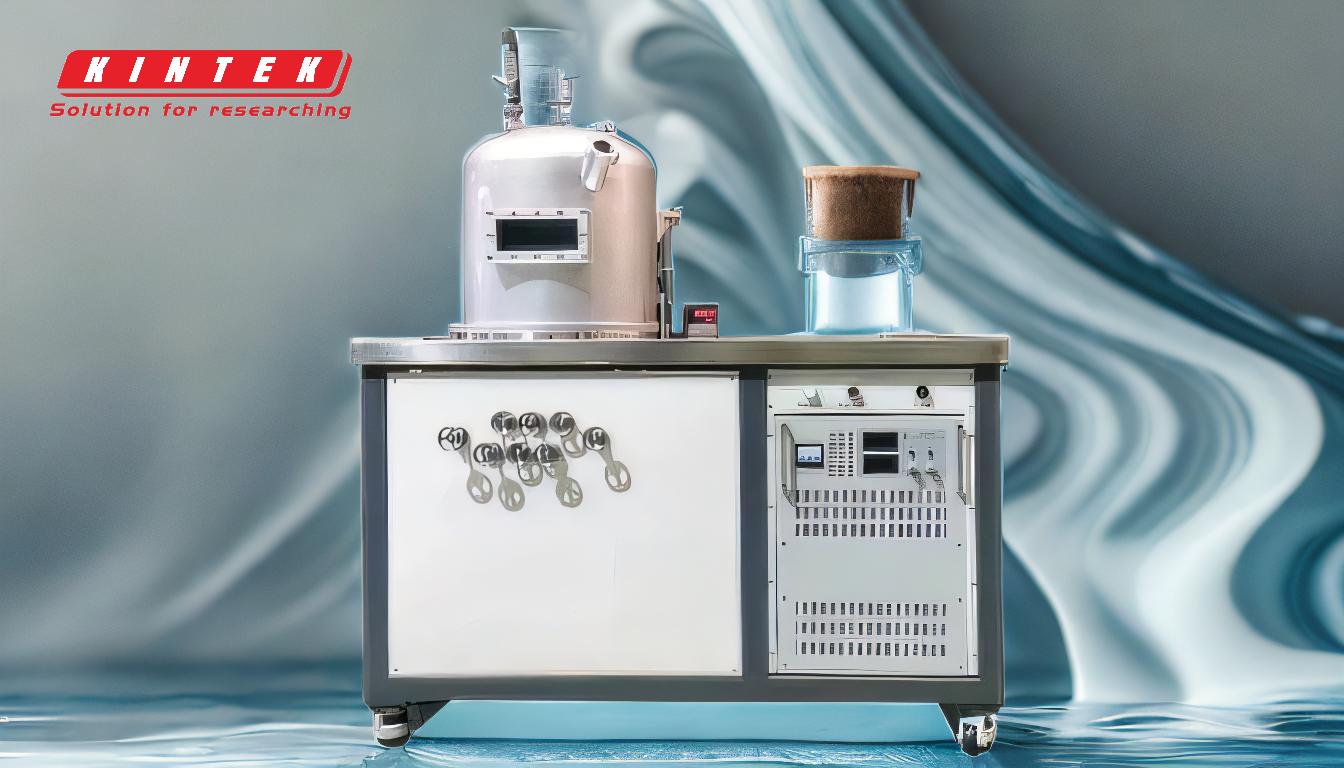
-
Bereich der Dünnschichtdicken bei PVD:
- Atomare Schichten bis zu Mikrometern: Mit PVD können Schichten im Bereich von Atomlagen (weniger als 10 Å oder 0,1 nm) bis zu mehreren Mikrometern (µm) abgeschieden werden. Dank dieses breiten Spektrums kann PVD sowohl bei Anwendungen eingesetzt werden, die ultradünne Schichten erfordern (z. B. Halbleiter), als auch bei dickeren Schichten (z. B. verschleißfeste Schichten).
- Typischer Bereich: Der gängigste Dickenbereich für PVD-Schichten liegt zwischen 0,2 µm und 5 µm. Dieser Bereich ist sowohl für dekorative als auch für funktionelle Anwendungen geeignet.
-
Dekorative vs. funktionale Beschichtungen:
- Dekorative Beschichtungen: Diese sind in der Regel dünner, etwa 0,2 µm. Dekorative Beschichtungen werden häufig in Branchen wie der Schmuck-, Uhren- und Unterhaltungselektronikindustrie verwendet, wo die Ästhetik eine wichtige Rolle spielt. Die geringe Dicke sorgt für ein hochwertiges Finish, ohne dass die Oberfläche wesentlich größer wird.
- Funktionelle Beschichtungen: Diese Beschichtungen sind im Allgemeinen dicker und reichen von 1 µm bis 5 µm oder mehr. Funktionelle Beschichtungen werden für Anwendungen verwendet, bei denen Haltbarkeit, Verschleißfestigkeit oder bestimmte elektrische Eigenschaften erforderlich sind. Beispiele sind Schutzschichten auf Werkzeugen, medizinischen Geräten und elektronischen Bauteilen.
-
Anwendungen, die die Dicke beeinflussen:
- Halbleiter und Elektronik: In diesen Bereichen werden häufig ultradünne Schichten (einige Nanometer) benötigt. PVD ist in der Lage, Schichten in dieser Größenordnung abzuscheiden und eignet sich daher ideal für die Herstellung dünner Schichten in Transistoren, Sensoren und anderen mikroelektronischen Geräten.
- Verschleißbeständige Beschichtungen: Bei Anwendungen wie Schneidwerkzeugen oder Motorkomponenten sind dickere Schichten (mehrere Mikrometer) erforderlich, um einen angemessenen Schutz gegen Verschleiß und Korrosion zu gewährleisten. Mit PVD können diese Schichtdicken bei gleichzeitig hoher Haftung und Gleichmäßigkeit erreicht werden.
-
Faktoren, die die Dicke bei PVD beeinflussen:
- Ablagerungszeit: Je länger der Abscheidungsprozess dauert, desto dicker ist die Schicht. PVD ermöglicht eine präzise Steuerung der Abscheidungszeit und damit die Herstellung von Schichten mit bestimmten Dicken.
- Materialeigenschaften: Verschiedene Materialien haben unterschiedliche Ablagerungsraten. Beispielsweise können sich Metalle schneller ablagern als Keramiken, was sich auf die Enddicke auswirkt.
- Substrate und Prozessparameter: Die Art des Substrats, die Temperatur, der Druck und andere Prozessparameter können die Dicke und Qualität der abgeschiedenen Schicht beeinflussen.
-
Vergleich mit anderen Ablagerungsmethoden:
- Chemische Gasphasenabscheidung (CVD): Wie PVD kann auch CVD Schichten von einigen Nanometern bis zu mehreren Mikrometern abscheiden. CVD erfordert jedoch häufig höhere Temperaturen und ist nicht für alle Substrate geeignet.
- Andere Dünnschichttechniken: Mit Techniken wie Sputtern oder Verdampfen (beides PVD-Methoden) lassen sich ähnliche Schichtdicken erreichen, doch wird PVD häufig bevorzugt, weil sich damit hochwertige Schichten bei niedrigeren Temperaturen abscheiden lassen.
-
Praktische Überlegungen für Einkäufer von Geräten und Verbrauchsmaterial:
- Anwendungsspezifische Anforderungen: Bei der Auswahl von PVD-Anlagen oder -Verbrauchsmaterialien ist es entscheidend, die gewünschte Schichtdicke und die Anwendung zu berücksichtigen. Sollen beispielsweise ultradünne Schichten für die Elektronik hergestellt werden, sind Anlagen mit präziser Steuerung der Abscheidungsraten und -dicken unerlässlich.
- Kompatibilität der Materialien: Vergewissern Sie sich, dass das PVD-System mit den Materialien, die Sie abscheiden wollen, kompatibel ist. Einige Werkstoffe können besondere Prozessbedingungen erfordern, um die gewünschte Dicke und Qualität zu erreichen.
- Kosten und Effizienz: Dickere Schichten können längere Beschichtungszeiten und mehr Material erfordern, was die Kosten erhöht. Ein Gleichgewicht zwischen den Anforderungen an die Schichtdicke und der Kosteneffizienz ist sowohl für die Klein- als auch für die Großserienproduktion wichtig.
Zusammenfassend lässt sich sagen, dass PVD ein vielseitiges Spektrum an Dünnschichtdicken bietet, von Atomschichten bis hin zu mehreren Mikrometern, und damit für eine Vielzahl von Anwendungen geeignet ist. Die Kenntnis der spezifischen Anforderungen Ihrer Anwendung - ob dekorativ oder funktional - hilft bei der Auswahl der richtigen PVD-Anlage und der Erreichung der gewünschten Schichtdicke.
Zusammenfassende Tabelle:
Aspekt | Einzelheiten |
---|---|
Dickenbereich | Atomare Schichten (<10 Å) bis zu mehreren Mikrometern (µm) |
Dekorative Beschichtungen | ~0,2 µm, verwendet in Schmuck, Uhren und Unterhaltungselektronik |
Funktionelle Beschichtungen | 1 µm bis 5 µm+, für Verschleißfestigkeit, Elektronik und medizinische Geräte |
Wichtige Anwendungen | Halbleiter (ultradünn), verschleißfeste Beschichtungen (dicker) |
Faktoren, die die Dicke beeinflussen | Abscheidungszeit, Materialeigenschaften, Substrat und Prozessparameter |
Vergleich mit CVD | PVD bietet niedrigere Temperaturen und bessere Substratkompatibilität |
Sind Sie bereit, Ihre Dünnschichtanwendungen zu optimieren? Kontaktieren Sie uns heute um die perfekte PVD-Lösung zu finden!