Tiegel sind wichtige Werkzeuge, die in verschiedenen Industriezweigen und Labors zum Schmelzen, Erhitzen oder Verändern von Materialien bei hohen Temperaturen verwendet werden.Welches Material für einen Tiegel verwendet wird, hängt von der vorgesehenen Anwendung, der Temperatur, der er standhalten muss, und der Art des zu verarbeitenden Materials ab.Zu den gängigen Materialien gehören Quarzglas, Siliziumkarbid, Bornitrid, Platin, Zirkonium und Ton.Jedes Material hat einzigartige Eigenschaften, die es für bestimmte Verwendungszwecke geeignet machen, z. B. Temperaturwechselbeständigkeit, Haltbarkeit, Wärmedämmung oder Inertheit zur Vermeidung von Verunreinigungen.
Die wichtigsten Punkte erklärt:
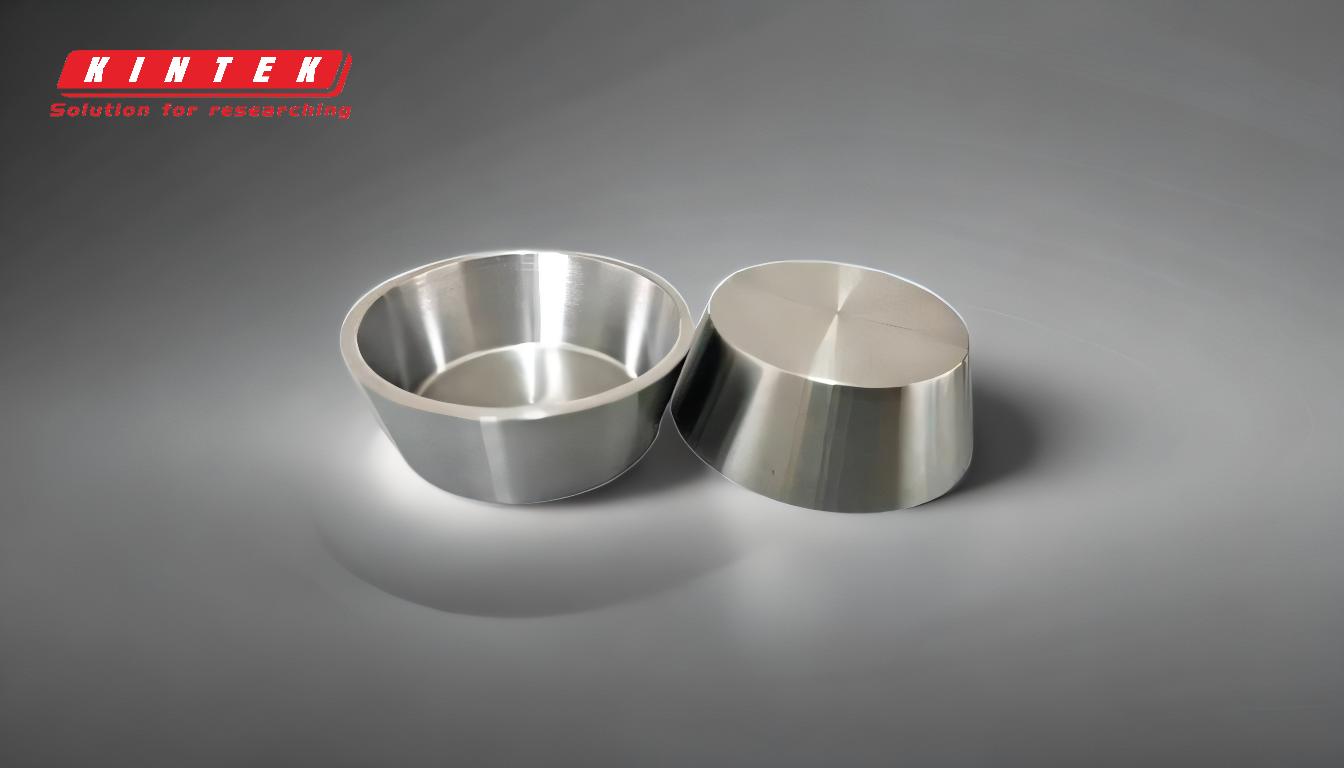
-
Geschmolzener Quarz:
- Eigenschaften:Quarzglas ist hochgradig temperaturwechselbeständig, d. h. es kann rasche Temperaturschwankungen aushalten, ohne zu brechen oder zu splittern.Darüber hinaus weist es eine ausgezeichnete chemische Reinheit und Transparenz gegenüber ultraviolettem Licht auf.
- Anwendungen:Ideal für das Schmelzen von Metallen und andere Hochtemperaturprozesse, bei denen thermische Stabilität entscheidend ist.Es wird häufig in Labors und in der Industrie für Verfahren wie Metallguss oder Glasherstellung verwendet.
-
Siliziumkarbid:
- Eigenschaften:Siliziumkarbid ist extrem langlebig, hat eine hohe Wärmeleitfähigkeit und ist verschleiß- und korrosionsbeständig.Es kann sehr hohen Temperaturen und rauen chemischen Umgebungen widerstehen.
- Anwendungen:Wird häufig in der Halbleiterproduktion verwendet, wo Haltbarkeit und Wärmemanagement entscheidend sind.Es wird auch in Gießereien zum Schmelzen von Metallen und in industriellen Hochtemperaturanwendungen eingesetzt.
-
Bornitrid:
- Eigenschaften:Bornitrid ist ein hervorragender Wärmeisolator mit hoher thermischer Stabilität und geringer Wärmeausdehnung.Außerdem ist es chemisch inert und hat gute Schmiereigenschaften.
- Anwendungen:Wird häufig in Hochtemperatur-Vakuumöfen und anderen Umgebungen verwendet, in denen thermische Isolierung und chemische Inertheit erforderlich sind.Es wird auch bei der Herstellung von Hochleistungskeramik und Verbundwerkstoffen verwendet.
-
Platin und Zirkonium:
- Eigenschaften:Platin und Zirkonium sind inerte Materialien, die chemischen Reaktionen widerstehen und sich daher ideal für den Einsatz in der analytischen Chemie eignen.Sie können hohen Temperaturen standhalten und sind korrosionsbeständig.
- Anwendungen:Wird in der Regel in Labortiegeln für die Probenvorbereitung und die analytische Chemie verwendet, wo Verunreinigungen auf ein Minimum reduziert werden müssen.Diese Materialien gewährleisten die Genauigkeit und Zuverlässigkeit von chemischen Analysen.
-
Lehm:
- Eigenschaften:Lehm ist ein traditionelles Material, das preiswert und leicht verfügbar ist.Er hat eine gute Wärmebeständigkeit und lässt sich leicht formen.
- Anwendungen:Historische Verwendung für die Herstellung von Schmelztiegeln, insbesondere in der frühen Metallurgie und Töpferei.Auch wenn sie heute weniger verbreitet sind, werden Tontiegel immer noch in einigen traditionellen oder kostengünstigen Anwendungen eingesetzt.
-
Kriterien für die Auswahl:
- Temperaturbeständigkeit:Das Material muss den für die Anwendung erforderlichen spezifischen Temperaturen standhalten.
- Chemische Verträglichkeit:Das Tiegelmaterial darf nicht mit den zu verarbeitenden Stoffen reagieren.
- Beständigkeit gegen thermische Schocks:Wichtig für Anwendungen mit schnellen Temperaturschwankungen.
- Dauerhaftigkeit und Langlebigkeit:Das Material sollte haltbar genug sein, um wiederholtem Gebrauch standzuhalten, ohne sich zu verschlechtern.
- Kosten und Verfügbarkeit:Das Material sollte kostengünstig und für den vorgesehenen Verwendungszweck leicht verfügbar sein.
Wenn ein Käufer diese wichtigen Punkte kennt, kann er eine fundierte Entscheidung darüber treffen, welches Tiegelmaterial für seine spezifischen Bedürfnisse am besten geeignet ist, sei es für den Einsatz im Labor, in der Industrie oder in der traditionellen Anwendung.
Zusammenfassende Tabelle:
Werkstoff | Wichtige Eigenschaften | Gemeinsame Anwendungen |
---|---|---|
Geschmolzener Quarz | Temperaturwechselbeständigkeit, chemische Reinheit | Metallguss, Glasherstellung |
Siliziumkarbid | Hohe Haltbarkeit, Wärmeleitfähigkeit | Halbleiterproduktion, Gießereien |
Bornitrid | Thermische Isolierung, chemische Inertheit | Hochtemperatur-Vakuumöfen, Keramiken |
Platin/Zirkonium | Inert, korrosionsbeständig | Analytische Chemie, Probenvorbereitung |
Lehm | Kostengünstig, thermische Beständigkeit | Traditionelle Metallurgie, Töpferei |
Brauchen Sie Hilfe bei der Auswahl des richtigen Tiegelmaterials? Kontaktieren Sie unsere Experten noch heute für eine persönliche Beratung!