Stickstoff wird aufgrund seiner inerten Eigenschaften, seiner Kosteneffizienz und seiner Fähigkeit, die Materialeigenschaften zu verbessern, beim Sintern verwendet.Er wirkt als Schutzatmosphäre und verhindert Oxidation und Verunreinigung während des Sinterprozesses.Stickstoff ist besonders vorteilhaft beim Sintern von nichtrostenden Stählen, wo er als Mischkristallverfestigungsmittel wirken kann.Seine Verwendung erfordert jedoch eine sorgfältige Kontrolle der Abkühlungsraten, um die Ausscheidung von Chromnitrid zu vermeiden, das die Korrosionsbeständigkeit beeinträchtigen kann.Stickstoffhaltige Atmosphären sind auch wirksam bei der Regulierung von Prozessfaktoren wie Entkohlung und Desoxidation und gewährleisten hochwertige Sinterprodukte.Insgesamt ist Stickstoff eine vielseitige und wirtschaftliche Wahl für Sinteranwendungen, vorausgesetzt, die Prozessparameter werden gut verwaltet.
Die wichtigsten Punkte erklärt:
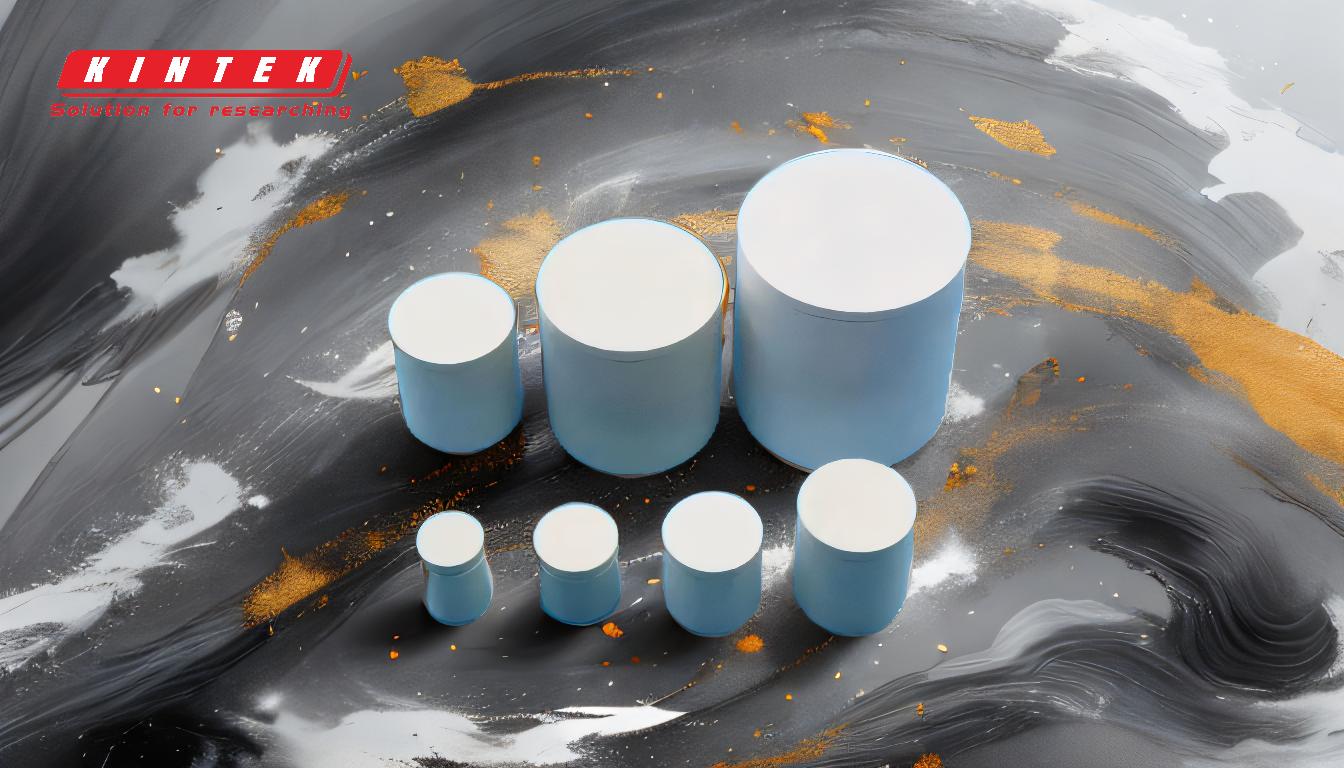
-
Inerte/Schutzatmosphäre:
- Stickstoff ist ein inertes Gas, das heißt, es reagiert nicht ohne weiteres mit anderen Stoffen.Diese Eigenschaft macht es ideal für die Schaffung einer Schutzatmosphäre während des Sinterns, die Oxidation und Verunreinigung der zu sinternden Metallpulver verhindert.
- Der Einsatz von Stickstoff trägt dazu bei, die Integrität und Qualität des gesinterten Produkts zu erhalten, indem er es vor reaktiven Gasen wie Sauerstoff abschirmt, die sonst das Material zersetzen könnten.
-
Kosten-Nutzen-Verhältnis:
- Stickstoff ist im Vergleich zu anderen Inertgasen wie Argon relativ kostengünstig.Seine Kosteneffizienz macht ihn zu einer bevorzugten Wahl für viele industrielle Sinterprozesse.
- Die Möglichkeit, Stickstoff vor Ort zu erzeugen, senkt die Kosten weiter und macht es zu einer wirtschaftlichen Option für Großbetriebe.
-
Mischkristallhärtung in austenitischen rostfreien Stählen:
- Stickstoff ist in der Stahlmatrix löslich, insbesondere in austenitischen nichtrostenden Stählen.Diese Löslichkeit ermöglicht es dem Stickstoff, als Mischkristallverfestiger zu wirken und die mechanischen Eigenschaften des Stahls zu verbessern.
- Das Vorhandensein von Stickstoff in der Stahlmatrix kann die Härte, die Festigkeit und die Verschleißfestigkeit verbessern, was für bestimmte Anwendungen von Vorteil ist.
-
Risiko der Ausscheidung von Chromnitrid:
- Bei hohen Temperaturen kann Stickstoff in nichtrostenden Stählen Nitride, insbesondere Chromnitride, bilden.Diese Ausscheidungen können die Korrosionsbeständigkeit des Werkstoffs negativ beeinflussen.
- Um dieses Risiko zu mindern, werden während des Sinterprozesses häufig hohe Abkühlungsraten eingesetzt, um die Bildung von Chromnitriden zu minimieren.
-
Regulierung von Prozessfaktoren:
- Stickstoffbasierte Atmosphären können zur Regulierung kritischer Prozessfaktoren wie Entkohlung und Desoxidation eingesetzt werden.Diese Faktoren sind entscheidend für die Aufrechterhaltung des gewünschten Kohlenstoffgehalts und die Gewährleistung, dass das Metall frei von Oxiden ist.
- Durch die Kontrolle dieser Faktoren trägt Stickstoff zur Herstellung hochwertiger Sinterprodukte mit gleichbleibenden Eigenschaften bei.
-
Vielseitigkeit in der Anwendung:
- Stickstoff wird in vielen Bereichen eingesetzt, z. B. bei der Wärmebehandlung von Metallen, in der Pulvermetallurgie, bei magnetischen Materialien und bei der Halbleiterherstellung.Seine Vielseitigkeit macht ihn zu einer wertvollen Ressource in vielen industriellen Prozessen.
- Neben dem Sintern wird Stickstoff als Schutzgas beim Glühen, bei der Behandlung von Nitriden und beim Spülen von Öfen verwendet, was seine breite Anwendbarkeit noch unterstreicht.
-
Verwendung in stickstoffbasierten Gemischen:
- Gemische auf Stickstoffbasis sind besonders nützlich, wenn hohe Abkühlungsraten erreicht werden können und die Gefahr der Ausscheidung von Chromnitrid minimal ist.Diese Mischungen sind eine wirksame und wirtschaftliche Lösung für das Sintern einer Vielzahl von Materialien.
- Die Wahl der Stickstoffmischungen hängt von den spezifischen Anforderungen des Sinterprozesses und den verwendeten Materialien ab.
Zusammenfassend lässt sich sagen, dass Stickstoff aufgrund seiner Inertheit, seiner Kosteneffizienz und seiner Fähigkeit, die Materialeigenschaften zu verbessern, eine entscheidende Komponente beim Sintern ist.Seine Verwendung erfordert jedoch ein sorgfältiges Management der Prozessparameter, insbesondere der Abkühlungsraten, um nachteilige Auswirkungen wie die Ausscheidung von Chromnitrid zu vermeiden.Wenn diese Faktoren bekannt sind und kontrolliert werden, kann Stickstoff effektiv zur Herstellung hochwertiger Sinterprodukte in verschiedenen Industriezweigen eingesetzt werden.
Zusammenfassende Tabelle:
Hauptaspekt | Beschreibung |
---|---|
Inerte/Schutzatmosphäre | Verhindert Oxidation und Verunreinigung während des Sinterns. |
Kosten-Wirksamkeit | Kostengünstig im Vergleich zu anderen Inertgasen; kann vor Ort erzeugt werden. |
Mischkristallhärtung | Verbessert die Härte, Festigkeit und Verschleißfestigkeit von nichtrostenden Stählen. |
Risiko von Chromnitrid | Erfordert eine kontrollierte Abkühlung, um die Korrosionsbeständigkeit nicht zu beeinträchtigen. |
Regulierung von Prozessfaktoren | Steuert die Entkohlung und Desoxidation für hochwertige Sinterprodukte. |
Vielseitigkeit | Einsatz in der Wärmebehandlung, Pulvermetallurgie, bei magnetischen Materialien und mehr. |
Stickstoff-basierte Mischungen | Wirksam beim Sintern mit hohen Abkühlungsraten und minimalem Chromnitridrisiko. |
Möchten Sie Ihren Sinterprozess mit Stickstoff optimieren? Kontaktieren Sie noch heute unsere Experten für maßgeschneiderte Lösungen!