Das Sintern ist ein entscheidender Prozess in der Pulvermetallurgie und der Keramikherstellung, bei dem pulverförmige Werkstoffe durch Anwendung von Wärme und Druck in dichte, feste Körper umgewandelt werden, in der Regel unterhalb des Schmelzpunkts des Materials.Dieser Prozess umfasst mehrere Stufen, darunter die Bildung eines Grünlings, die Entfernung des Bindemittels und das eigentliche Sintern, bei dem die Partikel miteinander verschmelzen.Die Sintermaschine spielt eine wichtige Rolle bei der Steuerung von Temperatur, Atmosphäre und Druck, um sicherzustellen, dass die gewünschten Materialeigenschaften erreicht werden.Zu den Schlüsselkomponenten des Sinterprozesses gehören Rohstoffe wie eisenhaltige Pulver, Schmelzmittel und Brennstoffe, die bestimmte Kriterien für eine effektive Sinterung erfüllen müssen.
Die wichtigsten Punkte werden erklärt:
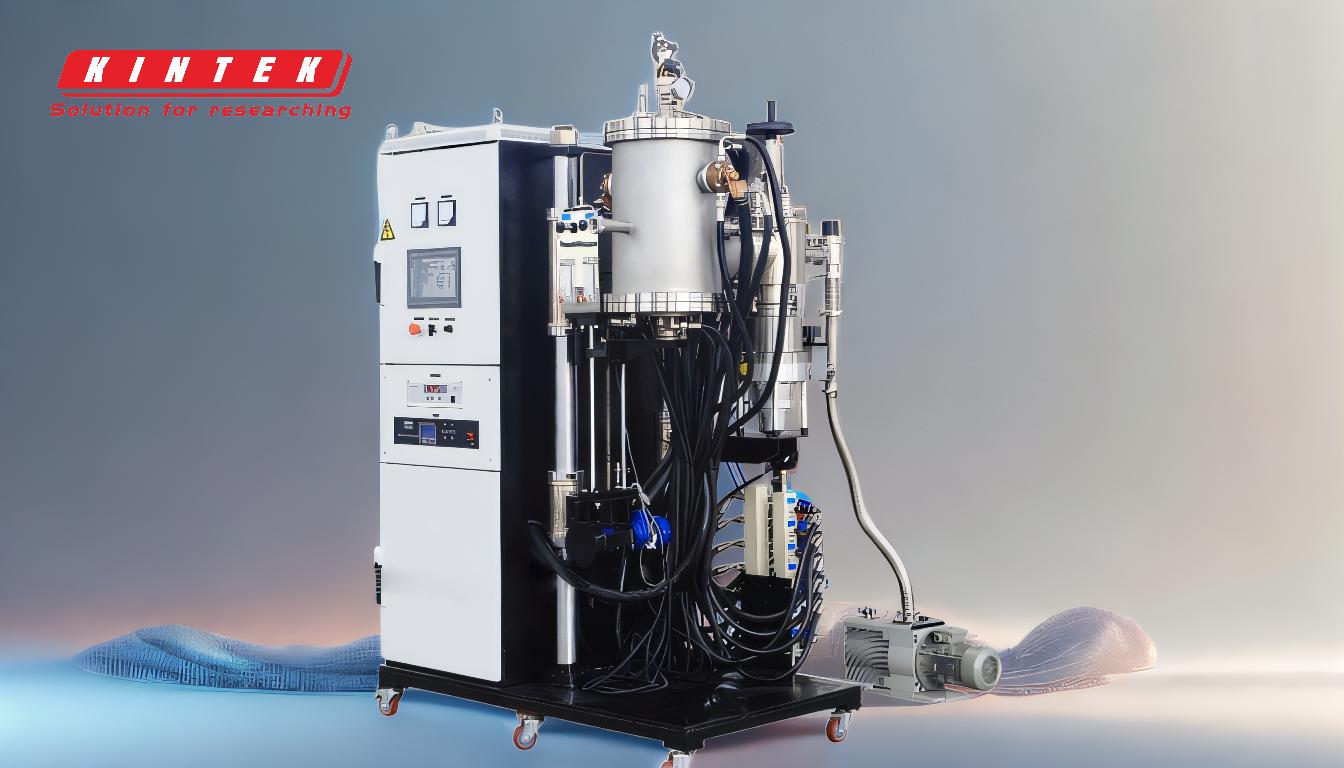
-
Definition und Zweck des Sinterns:
- Sintern ist ein Verfahren, bei dem eine feste Materialmasse durch Anwendung von Wärme oder Druck verdichtet und geformt wird, ohne dass der Schmelzpunkt des Materials erreicht wird.
- Es wird eingesetzt, um dichte, hochfeste Werkstoffe aus pulverförmigem Material zu erzeugen, wie es in der Pulvermetallurgie und der Keramikherstellung üblich ist.
-
Stadien des Sinterprozesses:
- Formung des Grünteils: Eine Mischung aus Primärpulver und einem Bindemittel (wie Wachs oder Polymer) wird in die gewünschte Form gebracht.
- Entfernung des Bindemittels: Beim Erhitzen verdampft oder verbrennt das Bindemittel.
- Sintern: Die Temperatur wird bis zu einem Punkt erhöht, an dem die Partikel an ihren Oberflächen zu verschmelzen beginnen, entweder durch teilweises Schmelzen oder durch ein zwischengeschaltetes Bindemittel.
-
Bestandteile von Sinterrohstoffen:
- Eisenhaltige Rohstoffe: Dazu gehören Erzpulver mit hohem Eisengehalt, Eisenkonzentrat und andere eisenhaltige Materialien.
- Schmelzmittel: Diese müssen einen hohen CaO-Gehalt, einen geringen Anteil an Verunreinigungen, einen spezifischen Wassergehalt und eine bestimmte Partikelgröße aufweisen.
- Brennstoff: In der Regel Kokspulver und rauchlose Kohle, die einen hohen Gehalt an festem Kohlenstoff, wenig Asche und einen geringen Schwefelgehalt aufweisen müssen.
-
Die wichtigsten Schritte des Sintervorgangs:
- Stoff: Legen des Bodens und des Mischmaterials auf die Sintermaschine.
- Zündung: Die Oberfläche des Fachs auf dem Wagen wird entzündet und auf einer angemessen hohen Temperatur gehalten.
- Sintern: Erfordert eine präzise Steuerung von Luftmenge, Vakuum, Schichtdicke, Geschwindigkeit und Endpunkt des Sinterns, um optimale Ergebnisse zu erzielen.
-
Atmosphärischer Sinterofen:
- Dieser Ofentyp steuert die Atmosphäre (z. B. Stickstoff oder Argon) zur Optimierung der Sinterumgebung.
- Er umfasst Heizvorrichtungen, Druckmechanismen, Sinterkammern und Gassteuerungssysteme.
- Die kontrollierte Atmosphäre ermöglicht die Materialwanderung, die Bewegung der Korngrenzen, die Beseitigung von Poren und die Schrumpfung, wodurch ein dichter Keramikkörper mit spezifischen Festigkeitseigenschaften entsteht.
-
Vorteile des Sinterns:
- Herstellung von Werkstoffen mit verbesserten mechanischen Eigenschaften, z. B. höherer Festigkeit und Haltbarkeit.
- Ermöglicht die Herstellung komplexer Formen und Strukturen, die mit herkömmlichen Schmelz- und Gießverfahren nur schwer zu erreichen wären.
- Geeignet für Materialien mit extrem hohen Schmelzpunkten, wie Wolfram und Molybdän.
Wenn man diese Schlüsselpunkte versteht, kann man die Komplexität und Präzision des Sinterprozesses sowie die entscheidende Rolle, die Sintermaschinen beim Erreichen der gewünschten Materialeigenschaften spielen, besser einschätzen.
Zusammenfassende Tabelle:
Aspekt | Einzelheiten |
---|---|
Definition | Verdichten von pulverförmigen Materialien unter Verwendung von Wärme/Druck unterhalb des Schmelzpunktes. |
Etappen | Grünlingsbildung, Bindemittelentfernung und Partikelschmelze. |
Wichtige Komponenten | Eisenhaltige Pulver, Schmelzmittel und Brennstoff. |
Sintervorgang | Tuch, Zündung und präzise Steuerung von Luft, Vakuum und Temperatur. |
Atmosphären-Sintern | Kontrollierte Umgebung für Materialmigration, Porenbeseitigung und Schrumpfung. |
Vorteile | Erhöhte Festigkeit, komplexe Formen und Eignung für hochschmelzende Materialien. |
Erfahren Sie, wie das Sintern Ihren Fertigungsprozess verändern kann. Kontaktieren Sie unsere Experten noch heute !