Die Sputterdeposition ist eine weit verbreitete Technik zur Abscheidung dünner Schichten auf Substraten. Dabei werden mit Hilfe von hochenergetischen Ionen Atome aus einem Zielmaterial herausgelöst, die dann auf einem Substrat kondensieren.Dieses Verfahren findet in einer Hochvakuumumgebung statt, um die Reinheit zu gewährleisten, und zeichnet sich durch seine Flexibilität, Zuverlässigkeit und die Fähigkeit aus, eine breite Palette von Materialien abzuscheiden, einschließlich leitender und dielektrischer Schichten.Die Sputterdeposition hat sich seit ihrer Entdeckung im 19. Jahrhundert erheblich weiterentwickelt, wobei Fortschritte in der Vakuumtechnologie und die Einführung des Hochfrequenzsputterns (HF) moderne Anwendungen ermöglichen.Das Verfahren beinhaltet einen Impulsaustausch zwischen energiereichen Ionen und Zielatomen, häufig unter Verwendung von Inertgasen wie Argon, und kann durch reaktive Abscheidung verbessert werden, um hochwertige Oxid- oder Nitridschichten zu erzeugen.
Die wichtigsten Punkte werden erklärt:
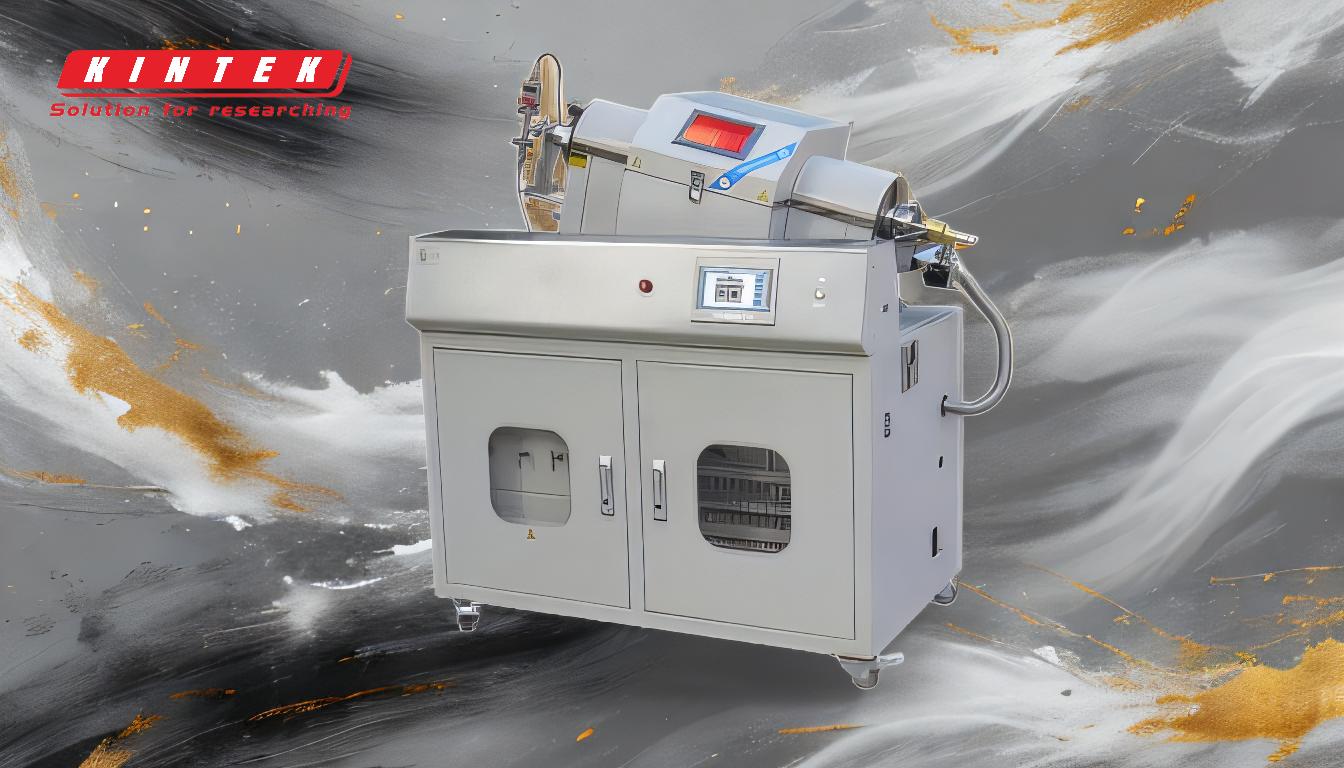
-
Grundlegender Mechanismus der Sputterabscheidung:
- Bei der Sputterbeschichtung wird ein Zielmaterial mit hochenergetischen Ionen beschossen, die in der Regel aus einem Inertgas wie Argon stammen.Diese Ionen lösen durch Impulsübertragung Atome aus dem Target, ein Prozess, der als Sputtern bekannt ist.
- Die herausgeschleuderten Atome wandern durch die Vakuumkammer und lagern sich auf einem Substrat ab, wobei sie einen dünnen Film bilden.Diese Methode gewährleistet eine gleichmäßige Beschichtung und eine starke Haftung des Films auf dem Substrat.
-
Historische Entwicklung und moderne Anwendungen:
- Das Phänomen des Sputterns wurde erstmals Mitte des 19. Jahrhunderts von Grove bei Experimenten mit Gleichstrom-Glimmentladungen beobachtet.In den 1930er Jahren fand es bereits kommerzielle Anwendung.
- Obwohl die thermische Verdampfung in den 1950er Jahren populärer wurde, gewann die Sputterdeposition in den späten 1950er und 1960er Jahren wieder an Bedeutung, was auf die Fortschritte in der Vakuumtechnologie und die Einführung des HF-Sputterns zurückzuführen ist, das die Abscheidung von dielektrischen Materialien ermöglichte.
-
Schlüsselkomponenten und Prozessbedingungen:
- Die Sputterbeschichtung erfordert eine Hochvakuumumgebung, um die Verunreinigung zu minimieren und die Reinheit der abgeschiedenen Schicht zu gewährleisten.
- Das Verfahren umfasst ein Target (Ausgangsmaterial), ein Substrat (auf dem die Schicht abgeschieden wird) und einen Plasma- oder Ionenstrahl zur Anregung der Edelgas-Ionen.Das Target kann aus verschiedenen Materialien bestehen, darunter Metalle, Legierungen und Keramiken.
-
Arten von Sputtering-Techniken:
- DC-Sputtern:Wird hauptsächlich für leitfähige Materialien verwendet, wobei ein Gleichstrom zur Erzeugung des Plasmas eingesetzt wird.
- RF-Sputtern:Geeignet für isolierende Materialien, da das Plasma mit Hilfe von Hochfrequenz erzeugt wird, wodurch eine Ladungsbildung auf dem Target vermieden wird.
- Reaktives Sputtern:Dabei werden reaktive Gase (z. B. Sauerstoff oder Stickstoff) in die Kammer eingeleitet, um Verbundschichten wie Oxide oder Nitride zu bilden.
-
Vorteile der Sputterdeposition:
- Flexibilität:Kann eine breite Palette von Materialien abscheiden, darunter Metalle, Legierungen und dielektrische Materialien.
- Gleichmäßigkeit:Ermöglicht eine gleichmäßige Beschichtung über komplexe Geometrien und große Flächen.
- Haftvermögen:Gewährleistet eine starke Bindung zwischen Folie und Substrat.
- Reinheit:Hochvakuumbedingungen minimieren die Verunreinigung, was zu qualitativ hochwertigen Schichten führt.
-
Reaktive Abscheidung und Materialsynthese:
- Beim reaktiven Sputtern wird ein Metalltarget mit reaktiven Gasen kombiniert, um Verbundschichten, wie Oxide oder Nitride, zu erzeugen.Mit dieser Methode lassen sich oft bessere Schichteigenschaften erzielen als mit vorgefertigten Materialien.
- Das Verfahren ermöglicht die Synthese neuer Materialkombinationen und maßgeschneiderter Schichteigenschaften, was es für fortschrittliche Anwendungen in der Elektronik, Optik und Beschichtung wertvoll macht.
-
Anwendungen der Sputterabscheidung:
- Halbleiterherstellung:Für die Abscheidung von leitenden und isolierenden Schichten in integrierten Schaltkreisen.
- Optische Beschichtungen:Wird bei der Herstellung von Antireflexions- und Reflexionsschichten für Linsen und Spiegel verwendet.
- Solarzellen:Abscheidung von Dünnschichten für photovoltaische Anwendungen.
- Dekorative und schützende Beschichtungen:Wird in der Automobilindustrie, der Luft- und Raumfahrt und bei Konsumgütern für ästhetische und funktionale Zwecke verwendet.
Die Sputterdeposition ist ein vielseitiges und zuverlässiges Verfahren für die Abscheidung dünner Schichten, das eine präzise Kontrolle der Schichteigenschaften und Kompatibilität mit einer Vielzahl von Materialien bietet.Die Fähigkeit, qualitativ hochwertige, gleichmäßige Schichten zu erzeugen, macht dieses Verfahren in Branchen von der Elektronik bis hin zu erneuerbaren Energien unverzichtbar.
Zusammenfassende Tabelle:
Aspekt | Einzelheiten |
---|---|
Mechanismus | Hochenergetische Ionen lösen Atome aus einem Target, die sich auf einem Substrat ablagern. |
Umgebung | Hochvakuum zur Gewährleistung der Reinheit und Minimierung der Kontamination. |
Wichtige Komponenten | Zielmaterial, Substrat, Plasma/Ionenstrahl und Inertgas (z. B. Argon). |
Techniken | DC-Zerstäubung, RF-Zerstäubung, reaktive Zerstäubung. |
Vorteile | Flexibilität, Einheitlichkeit, starke Haftung und hohe Reinheit. |
Anwendungen | Halbleiter, optische Beschichtungen, Solarzellen und Schutzschichten. |
Entdecken Sie, wie die Sputterdeposition Ihre Projekte verbessern kann. Kontaktieren Sie unsere Experten noch heute !