Der Druck des Sputtergases wirkt sich sowohl auf die Schichtqualität als auch auf die Sputterrate beim Sputterverfahren erheblich aus.Höhere Gasdrücke bewirken, dass die gesputterten Ionen mit den Gasatomen kollidieren, was zu einer diffusiven Bewegung führt, die vor der Abscheidung zu einem Random Walk führt.Dadurch verringert sich die Energie der Ionen, was zu niedrigeren Sputterraten führt, aber möglicherweise die Gleichmäßigkeit und Deckung der Schicht verbessert.Umgekehrt ermöglichen niedrigere Gasdrücke ballistische Stöße mit hoher Energie, was die Sputterrate erhöht, aber möglicherweise die Gleichmäßigkeit der Schichten beeinträchtigt.Die Wahl des Gasdrucks ist daher ein kritischer Parameter, der auf der Grundlage der gewünschten Schichteigenschaften und der Abscheidungseffizienz optimiert werden muss.
Die wichtigsten Punkte werden erklärt:
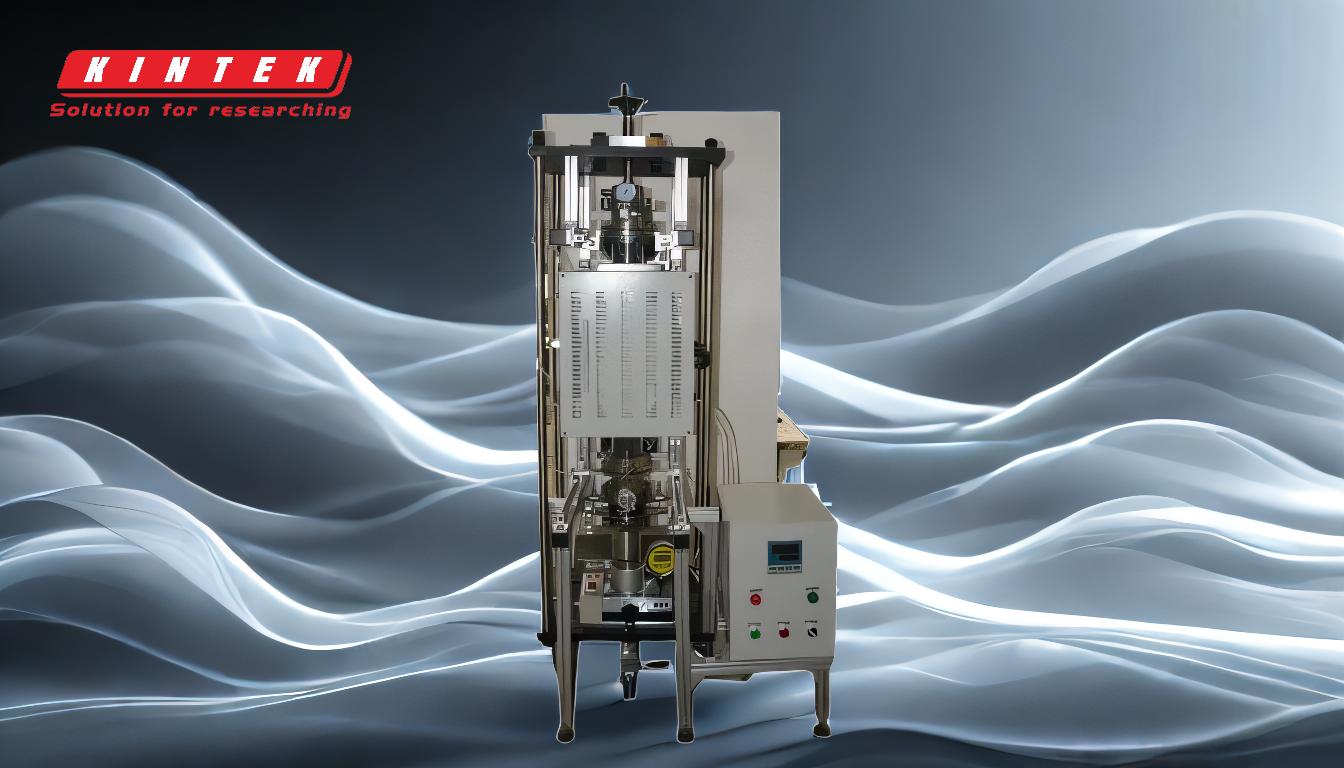
-
Auswirkung des Gasdrucks auf die Sputteringrate:
- Höherer Gasdruck:Bei höherem Druck stoßen die gesputterten Ionen häufiger mit Gasatomen zusammen, die als Moderatoren wirken.Dadurch verlieren die Ionen an Energie und bewegen sich diffus, was zu einer langsameren Sputterrate führt.Die Ionen durchlaufen eine zufällige Bewegung, bevor sie das Substrat erreichen, was die Gesamtabscheidungsrate verringern kann.
- Niedrigerer Gasdruck:Bei niedrigerem Druck stoßen die Ionen weniger mit den Gasatomen zusammen, so dass sie auf einem direkteren, ballistischen Weg zum Substrat gelangen.Dies führt zu energiereicheren Stößen und einer schnelleren Sputterrate, kann aber zu einer weniger gleichmäßigen Schichtabscheidung führen.
-
Auswirkungen auf die Filmqualität:
- Höherer Gasdruck:Die Diffusionsbewegung der Ionen bei höherem Druck kann zu einer gleichmäßigeren Schichtabdeckung führen, da sich die Ionen eher gleichmäßig über das Substrat verteilen.Dies kann die Filmqualität in Bezug auf die Gleichmäßigkeit verbessern und Defekte verringern.Die geringere Energie der Ionen kann jedoch zu Folien mit geringerer Dichte und Haftung führen.
- Niedrigerer Gasdruck:Die hochenergetischen ballistischen Stöße bei niedrigerem Druck können zu dichteren Schichten mit besserer Haftung führen, aber die Abscheidung kann weniger gleichmäßig sein, was zu Schwankungen in der Schichtdicke und -qualität auf dem Substrat führen kann.
-
Kompromisse und Optimierung:
- Gleichmäßigkeit vs. Dichte:Bei der Einstellung des Gasdrucks besteht ein Kompromiss zwischen Gleichmäßigkeit und Dichte des Films.Höhere Drücke begünstigen die Gleichmäßigkeit, während niedrigere Drücke die Dichte und Haftung begünstigen.Der optimale Druck muss auf der Grundlage der spezifischen Anforderungen des aufzubringenden Films gewählt werden.
- Prozesskontrolle:Die Einstellung des Hintergrundgasdrucks ermöglicht eine Feinabstimmung des Sputterprozesses und damit die Kontrolle über die Energie und Richtung der gesputterten Ionen.Diese Steuerung ist entscheidend für die Erzielung der gewünschten Schichteigenschaften, wie Mikrostruktur, Spannung und Oberflächenmorphologie.
-
Einfluss von anderen Faktoren:
- Abstand Quelle zu Substrat:Der Abstand zwischen der Sputterquelle und dem Substrat kann sich darauf auswirken, wie der Gasdruck die Schichtqualität beeinflusst.Ein größerer Abstand kann den Ionen mehr Zeit für Kollisionen und Diffusion geben, was die Gleichmäßigkeit bei höheren Drücken verbessert.
- Kathodenwinkel und Target-Substrat-Ausrichtung:Der Winkel der Kathode und die Ausrichtung des Targets auf das Substrat können ebenfalls Einfluss darauf haben, wie die Ionen abgeschieden werden, was sich sowohl auf die Zerstäubungsrate als auch auf die Schichtqualität auswirkt.Eine korrekte Ausrichtung kann dazu beitragen, einige der negativen Auswirkungen niedrigerer Drücke auf die Gleichmäßigkeit abzuschwächen.
-
Praktische Überlegungen:
- Stromquelle:Die Art der Stromquelle (Gleichstrom oder Hochfrequenz), die im Sputterprozess verwendet wird, kann in Wechselwirkung mit dem Gasdruck die Abscheidungsrate und die Schichtqualität beeinflussen.Das HF-Sputtern kann zum Beispiel bei niedrigeren Drücken effektiver sein, da das Plasma unter solchen Bedingungen aufrechterhalten werden kann.
- Material-Kompatibilität:Verschiedene Zielmaterialien können unterschiedlich auf Änderungen des Gasdrucks reagieren.Einige Materialien benötigen möglicherweise einen höheren Druck, um die gewünschten Filmeigenschaften zu erzielen, während andere bei niedrigerem Druck besser funktionieren.
Zusammenfassend lässt sich sagen, dass der Druck des Sputtergases ein kritischer Parameter ist, der sowohl die Sputterrate als auch die Qualität der abgeschiedenen Schicht direkt beeinflusst.Durch eine sorgfältige Einstellung des Gasdrucks und anderer Prozessparameter lässt sich das gewünschte Gleichgewicht zwischen Abscheiderate, Schichtgleichmäßigkeit und Schichtdichte erreichen.Diese Optimierung ist für die Herstellung hochwertiger, auf spezifische Anwendungen zugeschnittener dünner Schichten unerlässlich.
Zusammenfassende Tabelle:
Parameter | Höherer Gasdruck | Niedrigerer Gasdruck |
---|---|---|
Sputtering-Rate | Langsamer aufgrund von Ionenkollisionen und Diffusionsbewegung | Schneller durch hochenergetische ballistische Stöße |
Gleichmäßigkeit des Films | Verbesserte Gleichmäßigkeit und Abdeckung | Weniger einheitlich, mögliche Dickenschwankungen |
Foliendichte und Adhäsion | Geringere Dichte und Adhäsion | Höhere Dichte und bessere Adhäsion |
Abstriche | Begünstigt Gleichmäßigkeit | Begünstigt Dichte und Adhäsion |
Wichtige Überlegungen | Quelle-Substrat-Abstand, Kathodenausrichtung | Stromquellentyp, Materialkompatibilität |
Benötigen Sie Hilfe bei der Optimierung Ihres Sputtering-Prozesses? Kontaktieren Sie noch heute unsere Experten für maßgeschneiderte Lösungen!