Physikalische Gasphasenabscheidung (PVD) ist in verschiedenen Industriezweigen für Beschichtungen und die Abscheidung von Dünnschichten weit verbreitet.Diese Verfahren bieten mehrere Vorteile, z. B. hochwertige Beschichtungen, Umweltfreundlichkeit und die Möglichkeit, eine breite Palette von Materialien abzuscheiden.Sie sind jedoch auch mit Einschränkungen verbunden, z. B. hohen Anlagenkosten, komplexer Prozesssteuerung und begrenzter Schichtdicke.Das Verständnis dieser Vorteile und Einschränkungen ist entscheidend für die Auswahl des geeigneten PVD-Verfahrens für bestimmte Anwendungen.
Die wichtigsten Punkte werden erklärt:
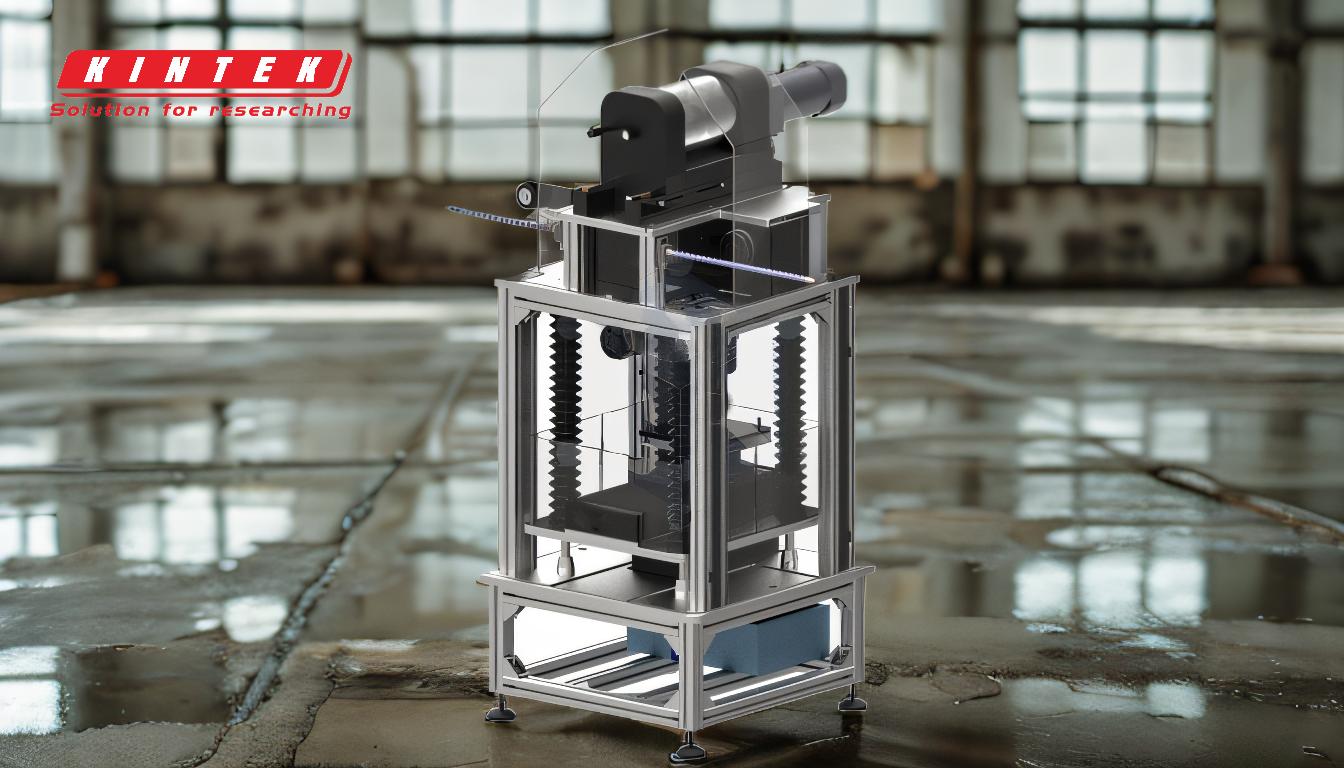
-
Vorteile der PVD-Techniken:
- Hochwertige Beschichtungen: PVD-Verfahren erzeugen Beschichtungen mit hervorragender Haftung, Gleichmäßigkeit und Reinheit.Das Verfahren ermöglicht eine präzise Kontrolle der Beschichtungseigenschaften, wie Dicke, Zusammensetzung und Mikrostruktur, was zu Hochleistungsbeschichtungen führt.
- Umweltfreundlichkeit: PVD gilt als umweltfreundliches Verfahren, da in der Regel keine schädlichen Chemikalien eingesetzt werden oder gefährliche Abfälle entstehen.Dies macht es zu einer bevorzugten Wahl in Branchen, in denen strenge Umweltvorschriften gelten.
- Vielseitigkeit bei der Materialabscheidung: Mit PVD-Verfahren kann eine Vielzahl von Materialien abgeschieden werden, darunter Metalle, Legierungen, Keramiken und Verbundwerkstoffe.Diese Vielseitigkeit ermöglicht die Herstellung von Beschichtungen mit maßgeschneiderten Eigenschaften für bestimmte Anwendungen.
- Verarbeitung bei niedrigen Temperaturen: Viele PVD-Verfahren können bei relativ niedrigen Temperaturen durchgeführt werden, was für die Beschichtung temperaturempfindlicher Substrate von Vorteil ist, ohne thermische Schäden zu verursachen.
-
Grenzen der PVD-Techniken:
- Hohe Ausrüstungskosten: Die Anfangsinvestitionen für PVD-Anlagen können erheblich sein.Der Bedarf an Hochvakuumumgebungen, ausgeklügelten Kontrollsystemen und speziellen Targetmaterialien trägt zu den Gesamtkosten bei.
- Komplexität der Prozesssteuerung: PVD-Prozesse erfordern eine präzise Steuerung verschiedener Parameter, wie Druck, Temperatur und Leistung.Diese Komplexität kann es schwierig machen, konsistente Ergebnisse zu erzielen, vor allem in der Großserienproduktion.
- Beschränkungen bei der Beschichtungsdicke: PVD-Verfahren sind im Allgemeinen eher für Dünnschichtanwendungen geeignet.Das Erzielen dicker Schichten kann schwierig sein und mehrere Abscheidungszyklen erfordern, was den Zeit- und Kostenaufwand des Verfahrens erhöht.
- Sichtlinieneinschränkungen: Bei vielen PVD-Verfahren handelt es sich um Sichtlinienverfahren, d. h. nur die Oberflächen, die dem Dampfstrom direkt ausgesetzt sind, werden beschichtet.Dies kann zu ungleichmäßigen Beschichtungen auf komplexen Geometrien oder Innenflächen führen.
-
Vergleich mit Kurzweg-Vakuumdestillation:
- Während PVD-Techniken in erster Linie für Beschichtungsanwendungen eingesetzt werden, Kurzweg-Vakuumdestillation ist eine Technik zur Trennung und Reinigung von Verbindungen, insbesondere von hitzeempfindlichen Stoffen.Beide Verfahren arbeiten unter Vakuumbedingungen, wodurch die Siedepunkte der Stoffe herabgesetzt werden und die Verarbeitung bei niedrigeren Temperaturen möglich ist.Die Anwendungen und Ziele dieser Techniken sind jedoch recht unterschiedlich, wobei sich PVD auf die Materialabscheidung und die Kurzweg-Vakuumdestillation auf die Trennung von Verbindungen konzentriert.
-
Industrielle Anwendungen:
- PVD in der Fertigung: PVD-Beschichtungen werden häufig bei der Herstellung von Schneidwerkzeugen, medizinischen Geräten und optischen Komponenten eingesetzt.Die Fähigkeit, harte, verschleißfeste Beschichtungen herzustellen, macht PVD zu einem wertvollen Verfahren in Branchen, in denen Haltbarkeit und Leistung entscheidend sind.
- Kurzweg-Vakuumdestillation in der chemischen Verarbeitung: Die Kurzweg-Vakuumdestillation wird in der Pharma-, Lebensmittel- und Chemieindustrie häufig zur Reinigung von ätherischen Ölen, Cannabinoiden und anderen empfindlichen Verbindungen eingesetzt.Da die Technik bei niedrigen Temperaturen arbeiten und hochreine Produkte erzeugen kann, ist sie für diese Anwendungen ideal.
-
Zukünftige Trends:
- Fortschritte in der PVD-Technologie: Die laufende Forschung konzentriert sich auf die Verbesserung der Effizienz und Skalierbarkeit von PVD-Verfahren.Es wird erwartet, dass Innovationen bei den Target-Materialien, den Vakuumsystemen und der Prozesssteuerung die Kosten senken und das Anwendungsspektrum erweitern werden.
- Integration mit anderen Technologien: Die Kombination von PVD mit anderen Abscheidungs- oder Oberflächenbehandlungstechniken wie der chemischen Gasphasenabscheidung (CVD) oder der Plasmabehandlung könnte zur Entwicklung hybrider Verfahren mit erweiterten Möglichkeiten führen.
Zusammenfassend lässt sich sagen, dass PVD-Verfahren erhebliche Vorteile in Bezug auf die Beschichtungsqualität, die Umweltverträglichkeit und die Materialvielfalt bieten.Allerdings stellen sie auch Herausforderungen in Bezug auf Kosten, Prozesskomplexität und Schichtdicke dar.Das Verständnis dieser Faktoren ist wichtig, um fundierte Entscheidungen bei der Auswahl und Anwendung von PVD-Verfahren in verschiedenen industriellen Kontexten zu treffen.
Zusammenfassende Tabelle:
Blickwinkel | Vorteile | Beschränkungen |
---|---|---|
Qualität der Beschichtung | Hohe Adhäsion, Gleichmäßigkeit und Reinheit | Begrenzt auf Dünnschichtanwendungen |
Umweltverträglichkeit | Keine schädlichen Chemikalien oder gefährlichen Abfälle | Hohe Ausrüstungs- und Betriebskosten |
Vielseitigkeit der Materialien | Kann Metalle, Legierungen, Keramik und Verbundwerkstoffe beschichten | Sichtlinienverfahren begrenzt die Beschichtung auf komplexe Geometrien |
Temperatur-Empfindlichkeit | Verarbeitung bei niedrigen Temperaturen, geeignet für empfindliche Substrate | Komplexe Prozesssteuerung für gleichbleibende Ergebnisse erforderlich |
Benötigen Sie Hilfe bei der Auswahl des richtigen PVD-Verfahrens für Ihre Anwendung? Kontaktieren Sie noch heute unsere Experten !