Das Festkörpersintern ist ein entscheidender Prozess in der Pulvermetallurgie, der zahlreiche Vorteile bietet, die ihn zu einer bevorzugten Methode für die Herstellung von Hochleistungskomponenten machen.Bei diesem Verfahren werden verdichtete Metallpulver unter ihren Schmelzpunkt erhitzt, um die Partikel zu verbinden, was zu verbesserten Materialeigenschaften, Kosteneffizienz und der Möglichkeit zur Herstellung komplexer Formen führt.Diese Methode erhöht die Festigkeit, Haltbarkeit und Präzision und reduziert gleichzeitig den Energieverbrauch und die Umweltbelastung.Außerdem ermöglicht es maßgeschneiderte Materialzusammensetzungen und eine gleichmäßige Produktion, was es für verschiedene Branchen vielseitig einsetzbar macht.
Die wichtigsten Punkte werden erklärt:
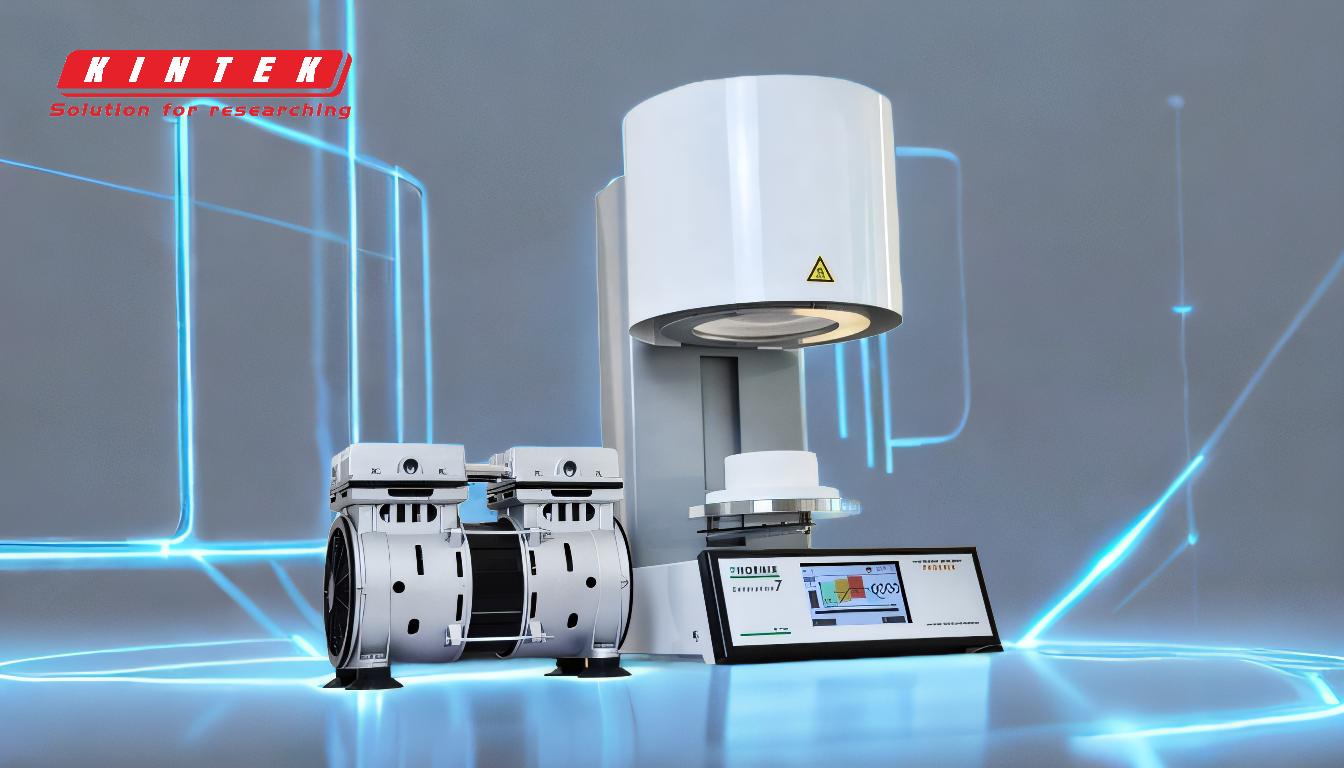
-
Verbesserte mechanische Eigenschaften:
- Das Festkörpersintern verbessert die Festigkeit, Haltbarkeit und Integrität von Materialien, indem es die Porosität verringert und Sinterhälse zwischen den Partikeln bildet.
- Dieser Prozess minimiert den Oberflächensauerstoff und eliminiert Schmiermittel, was zu einer dichteren und einheitlicheren Struktur führt.
- Beispiel:Gesinterte Bauteile wie Turbinenschaufeln weisen aufgrund der verbesserten Bindung zwischen den Partikeln eine hohe Festigkeit und Zuverlässigkeit auf.
-
Komplexe und präzise Formen:
- Das Sintern ermöglicht die Herstellung von Bauteilen mit komplizierten Formen und komplexen Geometrien, sowohl im Außen- als auch im Innenbereich.
- Die Verwendung von Formen und Gesenken, die durch Drahterodieren hergestellt werden, gewährleistet zentimetergenaue Toleranzen und ermöglicht eine hohe Präzision bei der Fertigung.
- Beispiel:Lager, Schmuckstücke und Wärmerohre können mit komplizierten Formen und feinen Details hergestellt werden.
-
Maßgeschneiderte Materialkombinationen:
- Beim Sintern können zusätzliche Elemente wie Nickel, Kupfer und Graphit eingebracht werden, um bestimmte Materialeigenschaften zu erzielen.
- Diese Flexibilität ermöglicht die Herstellung von Materialien mit maßgeschneiderten thermischen, elektrischen und mechanischen Eigenschaften.
- Beispiel:Filter oder Katalysatoren können mit kontrollierter Porosität und verbesserter Gasabsorptionsfähigkeit entwickelt werden.
-
Kosten-Nutzen-Verhältnis:
- Das Sintern erfordert im Vergleich zum Schmelzen von Metallen weniger Energie und ist damit ein umweltfreundliches und kosteneffizientes Verfahren.
- Die Fähigkeit, nahezu netzförmige Objekte herzustellen, verringert den Materialabfall und die Nachbearbeitungsanforderungen.
- Beispiel:Die Massenproduktion von Bauteilen wie Flintenschalen profitiert von einem geringeren Energieverbrauch und geringeren Materialkosten.
-
Vielseitigkeit bei der Materialauswahl:
- Das Sintern kann für eine Vielzahl von Werkstoffen eingesetzt werden, darunter Metalle mit hohem Schmelzpunkt und schwer zu verarbeitende Legierungen.
- Aufgrund dieser Vielseitigkeit eignet sich das Verfahren für Branchen, die spezielle Werkstoffe benötigen, wie z. B. die Luft- und Raumfahrt und die Automobilindustrie.
- Beispiel:Bauteile aus Wolfram oder anderen hochschmelzenden Metallen lassen sich durch Sintern herstellen.
-
Konsistente und wiederholbare Vorgänge:
- Das Verfahren gewährleistet ein hohes Maß an Reinheit und Gleichmäßigkeit der Ausgangsmaterialien, was zu einer konstanten Produktqualität führt.
- Die kontrollierte Korngröße und gleichmäßige Porosität tragen zu einer hohen Wiederholbarkeit der Herstellungsvorgänge bei.
- Beispiel:Gesinterte Teile wie Zahnräder und Buchsen weisen aufgrund der kontrollierten Prozessparameter eine konstante Leistung auf.
-
Verbesserte Funktionseigenschaften:
- Durch das Sintern werden Eigenschaften wie thermische und elektrische Leitfähigkeit, Transparenz und Materialfestigkeit verbessert.
- Es ermöglicht auch die Schaffung spezifischer Porositätsgrade, die für Anwendungen wie Filter und Katalysatoren nützlich sind.
- Beispiel:Wärmerohre und elektrische Kontakte profitieren von einer verbesserten thermischen und elektrischen Leitfähigkeit.
-
Vorteile für die Umwelt:
- Der geringere Energiebedarf des Sinterns im Vergleich zum Schmelzen reduziert den Kohlenstoff-Fußabdruck der Herstellungsverfahren.
- Die Möglichkeit, Metallpulver zu recyceln und wiederzuverwenden, erhöht die Nachhaltigkeit weiter.
- Beispiel:Das Sintern wird aufgrund seiner Umweltfreundlichkeit zunehmend in Initiativen für eine umweltfreundliche Produktion eingesetzt.
Zusammenfassend lässt sich sagen, dass das Festkörpersintern ein äußerst vorteilhaftes Verfahren ist, das Präzision, Vielseitigkeit und Kosteneffizienz mit verbesserten Materialeigenschaften und Umweltvorteilen verbindet.Seine Fähigkeit, komplexe Formen herzustellen, die Materialzusammensetzung anzupassen und eine gleichbleibende Qualität zu gewährleisten, macht es in der modernen Fertigung unverzichtbar.
Zusammenfassende Tabelle:
Vorteil | Wesentliche Vorteile | Beispiele |
---|---|---|
Verbesserte mechanische Eigenschaften | Erhöhte Festigkeit, Haltbarkeit und geringere Porosität. | Turbinenschaufeln, gesinterte Komponenten. |
Komplexe und präzise Formen | Herstellung komplizierter Formen mit hoher Präzision. | Lager, Schmuck, Wärmerohre. |
Maßgeschneiderte Materialzusammensetzungen | Maßgeschneiderte thermische, elektrische und mechanische Eigenschaften. | Filter, Katalysatoren. |
Kosteneffizienz | Geringerer Energieverbrauch und weniger Materialabfall. | Schrotflintenhülsen, serienmäßig hergestellte Komponenten. |
Vielseitigkeit bei der Materialauswahl | Geeignet für hochschmelzende Metalle und Legierungen. | Wolframkomponenten, Materialien für die Luft- und Raumfahrt. |
Konsistente und wiederholbare Prozesse | Hohe Reinheit, Gleichmäßigkeit und Wiederholbarkeit der Produktion. | Zahnräder, Buchsen. |
Verbesserte funktionelle Eigenschaften | Verbesserte thermische/elektrische Leitfähigkeit und Materialfestigkeit. | Wärmerohre, elektrische Kontakte. |
Vorteile für die Umwelt | Geringerer Kohlenstoff-Fußabdruck und recycelbare Materialien. | Initiativen für eine umweltfreundliche Produktion. |
Sind Sie bereit, das Festkörpersintern für Ihre Produktionsanforderungen zu nutzen? Kontaktieren Sie noch heute unsere Experten um mehr zu erfahren!