Sputtern und Verdampfen sind beides physikalische Aufdampfverfahren (PVD), die zur Herstellung dünner Schichten verwendet werden, sich aber in ihren Mechanismen, Vorteilen und Anwendungen erheblich unterscheiden. Das Sputtern bietet gegenüber dem Verdampfen mehrere Vorteile, darunter eine bessere Haftung, eine höhere Schichtqualität und eine genauere Kontrolle der Schichtzusammensetzung. Während das Aufdampfen einfacher und schneller ist, bietet das Sputtern eine höhere Gleichmäßigkeit, Skalierbarkeit und Kompatibilität mit einer breiteren Palette von Materialien. In dieser Analyse werden die wichtigsten Vorteile des Sputterns gegenüber dem Verdampfen untersucht, wobei der Schwerpunkt auf Faktoren wie Haftung, Filmqualität, Kontrolle der Zusammensetzung und Skalierbarkeit liegt.
Die wichtigsten Punkte werden erklärt:
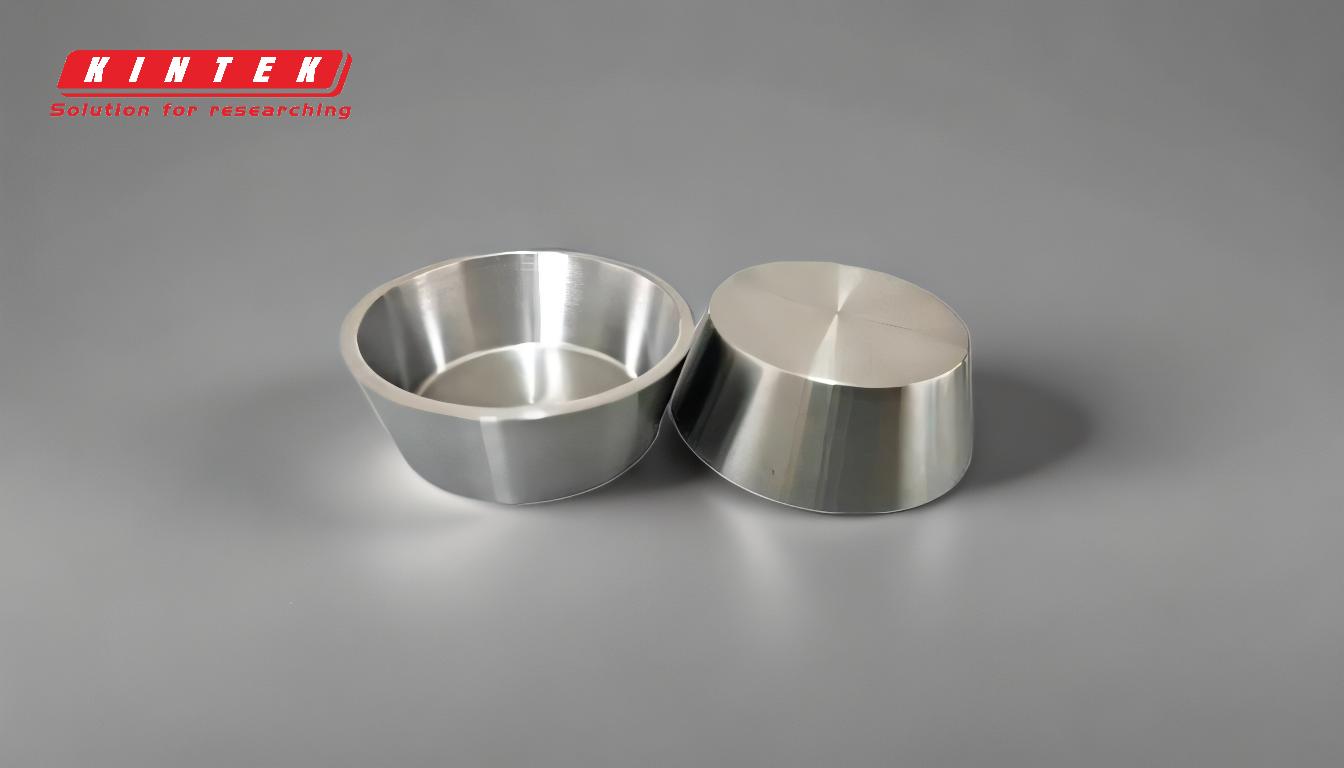
-
Bessere Adhäsion
- Das Sputtern sorgt für eine stärkere Haftung zwischen der abgeschiedenen Schicht und dem Substrat als das Aufdampfen. Dies liegt daran, dass gesputterte Partikel eine höhere kinetische Energie haben, wodurch sie sich besser in die Substratoberfläche einbetten können.
- Bei der Verdampfung kondensiert der Dampfstrom auf dem Substrat mit geringerer Energie, was zu einer schwächeren Bindung und Adhäsion führt.
- Eine starke Haftung ist entscheidend für Anwendungen, die haltbare und langlebige Beschichtungen erfordern, wie z. B. bei Halbleitergeräten oder Schutzbeschichtungen.
-
Hervorragende Filmqualität und Gleichmäßigkeit
- Beim Sputtern entstehen Schichten mit besserer Gleichmäßigkeit und weniger Defekten als beim Aufdampfen. Das Verfahren ermöglicht eine präzise Kontrolle der Schichtdicke und -zusammensetzung, selbst bei komplexen Geometrien.
- Die Verdampfung ist zwar schneller, führt aber aufgrund der Richtungsabhängigkeit des Dampfstroms häufig zu weniger gleichmäßigen Schichten, insbesondere auf nicht ebenen Oberflächen.
- Die höhere Schichtqualität, die durch Sputtern erreicht wird, ist für Anwendungen wie optische Beschichtungen, bei denen es auf Konsistenz und Präzision ankommt, unerlässlich.
-
Kontrolle der Zusammensetzung
- Beim Sputtern bleibt die Zusammensetzung des Ausgangsmaterials in der abgeschiedenen Schicht erhalten, so dass es sich ideal für die Abscheidung von Legierungen und komplexen Materialien eignet. Dies liegt daran, dass beim Sputtern die Atome direkt aus dem Target ausgestoßen werden und ihre Stöchiometrie erhalten bleibt.
- Bei der Verdampfung, insbesondere bei Legierungen, können verschiedene Elemente unterschiedlich schnell verdampfen, was zu Unterschieden in der Zusammensetzung des abgeschiedenen Films führt.
- Dieser Vorteil macht das Sputtern zum bevorzugten Verfahren für die Abscheidung von Mehrkomponenten-Materialien, etwa bei der Herstellung von Dünnschichtsolarzellen oder magnetischen Speichermedien.
-
Abgelagerte Arten mit höherer Energie
- Gesputterte Partikel haben im Vergleich zu aufgedampften Partikeln eine höhere Energie, was die Filmdichte verbessert und die Porosität verringert. Dies führt zu Schichten mit besseren mechanischen und elektrischen Eigenschaften.
- Verdampfte Partikel, die eine geringere Energie haben, neigen dazu, weniger dichte Filme mit größeren Korngrößen zu bilden, was die Leistung bei bestimmten Anwendungen beeinträchtigen kann.
- Die höhere Energie der gesputterten Partikel verbessert auch die Stufenabdeckung, so dass sie sich für die Beschichtung von Gräben und Vias in der Mikroelektronik eignet.
-
Skalierbarkeit und Automatisierung
- Das Sputtern ist in hohem Maße skalierbar und kann für die Produktion in großem Maßstab leicht automatisiert werden. Dadurch eignet es sich für industrielle Anwendungen, die gleichbleibende und hochwertige Beschichtungen erfordern.
- Die Verdampfung ist zwar schneller und kostengünstiger, aber sie ist weniger skalierbar und erfordert häufig manuelle Eingriffe, was ihren Einsatz in der Massenproduktion einschränkt.
- Die Möglichkeit, Sputtering-Prozesse zu automatisieren, senkt die Arbeitskosten und verbessert die Reproduzierbarkeit, was für Branchen wie die Automobil- und Luftfahrtindustrie von entscheidender Bedeutung ist.
-
Kompatibilität mit einer breiteren Palette von Materialien
- Durch Sputtern kann ein breiteres Spektrum von Materialien abgeschieden werden, einschließlich hochschmelzender Metalle, Keramiken und Legierungen, die sich nur schwer verdampfen lassen.
- Die Verdampfung ist auf Materialien beschränkt, die bei relativ niedrigen Temperaturen verdampft werden können, was ihre Anwendbarkeit einschränkt.
- Diese Vielseitigkeit macht das Sputtern zur bevorzugten Methode für fortschrittliche Anwendungen, wie z. B. die Abscheidung von Refraktärmetallen in der Halbleiterfertigung.
-
Geringere Vakuumanforderungen
- Das Sputtern arbeitet im Vergleich zur Verdampfung mit einem niedrigeren Vakuum, was die Komplexität und die Kosten des Vakuumsystems reduziert.
- Die Verdampfung erfordert ein höheres Vakuum, um Verunreinigungen zu vermeiden und eine effiziente Verdampfung zu gewährleisten, was die Betriebskosten erhöht.
- Die geringeren Vakuumanforderungen des Sputterns machen es für kleinere Betriebe und Forschungslabors leichter zugänglich.
-
Vorteile für Umwelt und Sicherheit
- Das Sputtern ist im Allgemeinen sicherer und umweltfreundlicher als das Verdampfen, da die Materialien nicht auf extrem hohe Temperaturen erhitzt werden müssen, wodurch das Risiko einer thermischen Zersetzung oder gefährlicher Emissionen verringert wird.
- Die Verdampfung, insbesondere die Elektronenstrahlverdampfung, erfordert hohe Temperaturen, die Sicherheitsrisiken und Umweltprobleme mit sich bringen können.
Zusammenfassend lässt sich sagen, dass das Sputtern in Bezug auf Haftung, Schichtqualität, Kontrolle der Zusammensetzung und Skalierbarkeit erhebliche Vorteile gegenüber der Verdampfung bietet. Während das Aufdampfen für bestimmte Anwendungen schneller und kostengünstiger ist, ist das Sputtern die bevorzugte Methode für hochpräzise und leistungsstarke Beschichtungen in Branchen von der Mikroelektronik bis zur Optik. Die Fähigkeit, eine breite Palette von Materialien mit hervorragenden Eigenschaften abzuscheiden, macht es zu einer vielseitigen und zuverlässigen Wahl für die moderne Dünnschichtabscheidung.
Zusammenfassende Tabelle:
Aspekt | Sputtern | Verdunstung |
---|---|---|
Haftung | Stärkere Adhäsion aufgrund höherer kinetischer Energie der Teilchen | Schwächere Bindung aufgrund der geringeren Energie des Dampfstroms |
Qualität der Filme | Hervorragende Gleichmäßigkeit, weniger Fehler und präzise Dickenkontrolle | Weniger gleichmäßige Filme, insbesondere auf nicht ebenen Oberflächen |
Kontrolle der Zusammensetzung | Behält die Zusammensetzung des Ausgangsmaterials bei, ideal für Legierungen und komplexe Materialien | Diskrepanzen in der Zusammensetzung aufgrund unterschiedlicher Verdampfungsraten |
Energie der Teilchen | Höhere Energie verbessert die Filmdichte und verringert die Porosität | Geringere Energie führt zu weniger dichten Schichten mit größerer Korngröße |
Skalierbarkeit | Hochgradig skalierbar und leicht automatisierbar für die Produktion in großem Maßstab | Weniger skalierbar, erfordert oft manuelle Eingriffe |
Kompatibilität der Materialien | Ablagerung einer breiten Palette von Materialien, einschließlich hochschmelzender Metalle | Begrenzt auf Materialien, die bei niedrigen Temperaturen verdampft werden können |
Vakuum-Anforderungen | Arbeitet mit niedrigerem Vakuum, was die Systemkomplexität und die Kosten reduziert | Erfordert höheres Vakuum, was die Betriebskosten erhöht |
Umwelt und Sicherheit | Sicherer und umweltfreundlicher, da keine extreme Erhitzung erforderlich ist | Höhere Temperaturen bergen Sicherheits- und Umweltrisiken |
Sind Sie bereit, Ihren Dünnschicht-Beschichtungsprozess zu verbessern? Kontaktieren Sie uns heute um zu erfahren, wie das Sputtern Ihre Anforderungen erfüllen kann!