Die chemische Gasphasenabscheidung (CVD) ist eine weit verbreitete Technik zur Abscheidung dünner Filme und Beschichtungen, die jedoch mehrere erhebliche Nachteile mit sich bringt. Dazu gehören Herausforderungen bei der Synthese von Mehrkomponentenmaterialien aufgrund von Schwankungen des Dampfdrucks, der Keimbildung und der Wachstumsraten, die zu heterogenen Partikelzusammensetzungen führen. Der Prozess erfordert oft hohe Temperaturen, die zu thermischer Instabilität der Substrate führen und die Art der verwendbaren Materialien einschränken können. Darüber hinaus können die für CVD erforderlichen chemischen Vorläufer hochgiftig, flüchtig und gefährlich sein, und die Nebenprodukte sind oft giftig und ätzend, was die Neutralisierung kostspielig und problematisch macht. Der Prozess ist außerdem durch die Größe der Vakuumkammer begrenzt, was die Beschichtung größerer Flächen erschwert, und er kann nicht vor Ort durchgeführt werden, sodass die Teile zu einem Beschichtungszentrum transportiert werden müssen. Diese Faktoren machen CVD für bestimmte Anwendungen zu einer komplexen und manchmal unpraktischen Methode.
Wichtige Punkte erklärt:
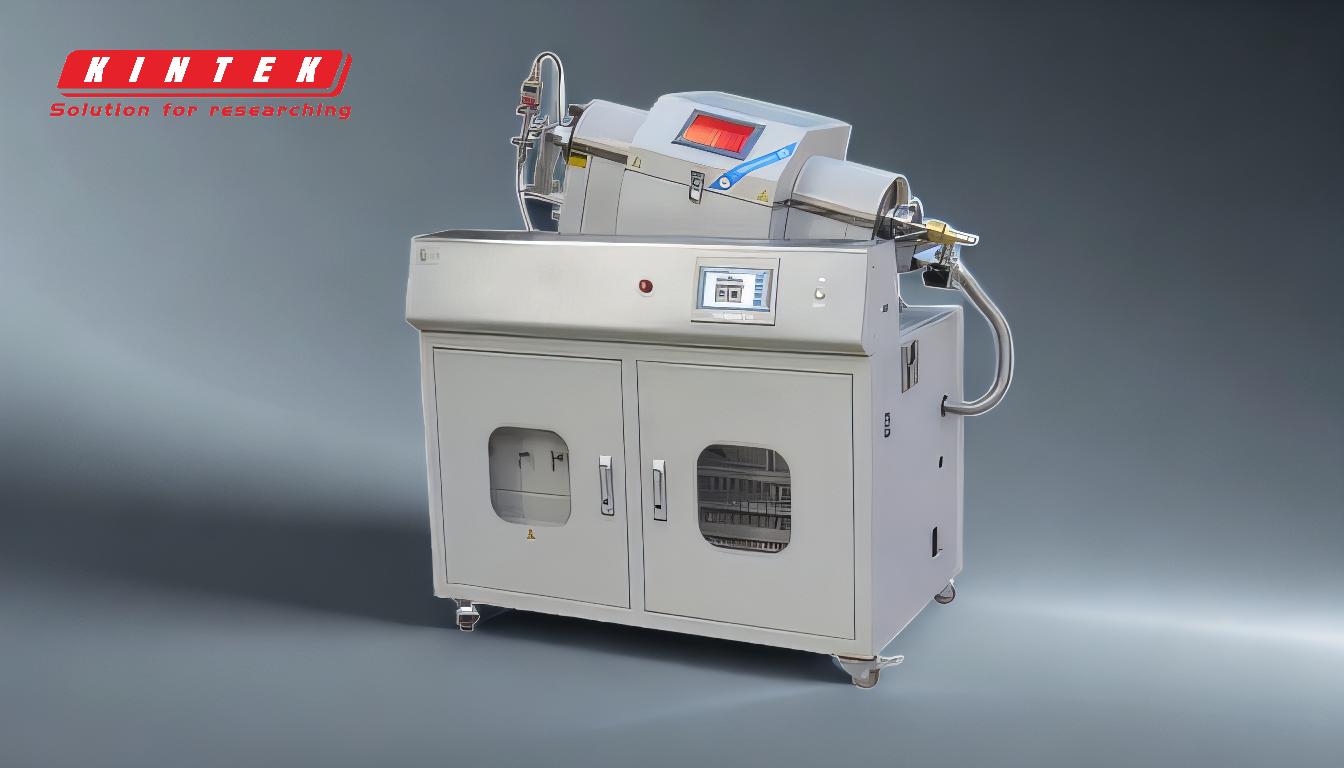
-
Schwierigkeiten bei der Synthese von Mehrkomponentenmaterialien:
- CVD steht bei der Herstellung von Mehrkomponentenmaterialien aufgrund von Schwankungen des Dampfdrucks, der Keimbildung und der Wachstumsraten während der Gas-zu-Partikel-Umwandlung vor Herausforderungen. Diese Variationen führen zu einer heterogenen Zusammensetzung der Partikel, was es schwierig macht, einheitliche Materialeigenschaften zu erreichen. Dies ist besonders problematisch, wenn versucht wird, Materialien mit spezifischen, genau definierten Eigenschaften herzustellen, da der Prozess zu Inkonsistenzen im Endprodukt führen kann.
-
Hohe Betriebstemperaturen:
- CVD arbeitet typischerweise bei hohen Temperaturen, was bei vielen Substraten zu thermischer Instabilität führen kann. Dies schränkt die Art der verwendbaren Materialien ein, da sich einige Substrate unter diesen Bedingungen verschlechtern oder beschädigt werden können. Hohe Temperaturen erhöhen zudem den Energieverbrauch und können den Prozess teurer und weniger umweltfreundlich machen.
-
Giftige und gefährliche Vorläufer:
- Die für die CVD erforderlichen chemischen Vorläufer weisen häufig hohe Dampfdrücke auf und können hochgiftig, flüchtig und gefährlich sein. Der Umgang mit diesen Chemikalien erfordert strenge Sicherheitsmaßnahmen und ihre Verwendung kann erhebliche Gesundheits- und Umweltrisiken mit sich bringen. Darüber hinaus verkompliziert das Fehlen extrem flüchtiger, ungiftiger und nicht pyrophorer Vorläufer das Verfahren zusätzlich und macht es für bestimmte Anwendungen weniger zugänglich.
-
Giftige und ätzende Nebenprodukte:
- Die Nebenprodukte der CVD sind häufig giftig und ätzend und erfordern eine sorgfältige Neutralisierung und Entsorgung. Dies erhöht die Gesamtkosten und die Komplexität des Prozesses, da für den sicheren Umgang mit diesen Nebenprodukten spezielle Geräte und Verfahren erforderlich sind. Auch die Umweltauswirkungen dieser Nebenprodukte geben Anlass zur Sorge, insbesondere in Branchen, in denen Nachhaltigkeit Priorität hat.
-
Einschränkungen bei der Beschichtung großer Flächen:
- Die Größe der beim CVD verwendeten Vakuumkammer begrenzt die Größe der zu beschichtenden Oberflächen. Dies macht es schwierig, CVD-Beschichtungen auf große oder komplexe Strukturen aufzutragen, was den Einsatz in bestimmten Branchen einschränkt. Darüber hinaus geht es bei dem Verfahren oft um „Alles oder Nichts“, was bedeutet, dass es schwierig ist, ein Material teilweise zu beschichten oder in manchen Fällen eine vollständige Abdeckung zu erreichen.
-
Unfähigkeit, vor Ort zu arbeiten:
- CVD kann normalerweise nicht vor Ort durchgeführt werden und erfordert den Transport der Teile zu einem Beschichtungszentrum. Dies erhöht die logistische Komplexität und die Kosten des Prozesses, insbesondere bei großen oder schweren Bauteilen. Die Notwendigkeit, Teile für die Beschichtung in einzelne Komponenten zu zerlegen, verkompliziert den Prozess zusätzlich und macht ihn für bestimmte Anwendungen weniger effizient.
-
Herausforderungen bei der Herstellung von hochwertigem Graphen:
- Die Herstellung von einschichtigem Graphen mittels CVD ist aufgrund der Vielzahl der erforderlichen Wachstumsbedingungen eine Herausforderung. Um qualitativ hochwertige Graphenfilme zu erhalten, sind eine präzise Kontrolle des Wachstumsmechanismus und optimale Bedingungen erforderlich, deren dauerhafte Aufrechterhaltung schwierig sein kann. Dies schränkt die Skalierbarkeit und Reproduzierbarkeit der Graphenproduktion mittels CVD ein.
-
Bildung harter Aggregate:
- Agglomeration in der Gasphase während der CVD kann zur Bildung harter Aggregate führen, was die Synthese hochwertiger Massenmaterialien erschwert. Dieses Problem ist besonders problematisch, wenn versucht wird, Materialien mit spezifischen mechanischen oder strukturellen Eigenschaften herzustellen, da das Vorhandensein von Aggregaten die Integrität des Endprodukts beeinträchtigen kann.
Zusammenfassend lässt sich sagen, dass chemische Gasphasenabscheidung Da es sich um eine leistungsstarke Technik zur Abscheidung dünner Filme und Beschichtungen handelt, weist sie mehrere erhebliche Nachteile auf, die ihre Anwendbarkeit in bestimmten Szenarien einschränken können. Dazu gehören Herausforderungen bei der Materialsynthese, hohe Betriebstemperaturen, die Verwendung toxischer Vorläufer und Einschränkungen bei der Beschichtung großer Oberflächen. Das Verständnis dieser Nachteile ist entscheidend für die Auswahl der geeigneten Abscheidungsmethode für eine bestimmte Anwendung.
Übersichtstabelle:
Nachteil | Beschreibung |
---|---|
Schwierigkeiten bei der Mehrkomponentensynthese | Schwankungen im Dampfdruck und in den Wachstumsraten führen zu inkonsistenten Materialeigenschaften. |
Hohe Betriebstemperaturen | Thermische Instabilität der Substrate und erhöhter Energieverbrauch. |
Giftige und gefährliche Vorläufer | Erfordert strenge Sicherheitsmaßnahmen und birgt Gesundheits-/Umweltrisiken. |
Giftige und ätzende Nebenprodukte | Kostspielige Neutralisierungs- und Entsorgungsprozesse. |
Einschränkungen bei der Beschichtung großer Flächen | Eingeschränkt durch die Größe der Vakuumkammer und die Herausforderungen bei der Teilbeschichtung. |
Unfähigkeit, vor Ort zu arbeiten | Erfordert den Transport zu Beschichtungszentren, was die logistische Komplexität erhöht. |
Herausforderungen bei der Herstellung von hochwertigem Graphen | Es ist schwierig, konsistente Wachstumsbedingungen für einschichtiges Graphen zu erreichen. |
Bildung harter Aggregate | Agglomeration in der Gasphase beeinträchtigt die Materialintegrität. |
Benötigen Sie Hilfe bei der Auswahl der richtigen Abscheidungsmethode? Kontaktieren Sie noch heute unsere Experten für persönliche Beratung!