Die thermische Verdampfung und die Elektronenstrahlverdampfung (E-Beam) sind beides physikalische Aufdampfverfahren (PVD), die zur Herstellung dünner Schichten verwendet werden. Sie unterscheiden sich jedoch erheblich in ihren Heizmechanismen, der Materialkompatibilität und den resultierenden Schichteigenschaften. Bei der thermischen Verdampfung wird ein Schmelztiegel durch elektrischen Widerstand erhitzt, wodurch Materialien mit niedrigerem Schmelzpunkt schmelzen und verdampfen. Im Gegensatz dazu werden bei der E-Beam-Verdampfung Materialien mit einem hochenergetischen Elektronenstrahl direkt erhitzt und verdampft, was sie für hochschmelzende Stoffe wie Oxide geeignet macht. Die E-Beam-Verdampfung erzeugt auch dichtere Schichten und bietet im Vergleich zur thermischen Verdampfung höhere Abscheideraten.
Die wichtigsten Punkte werden erklärt:
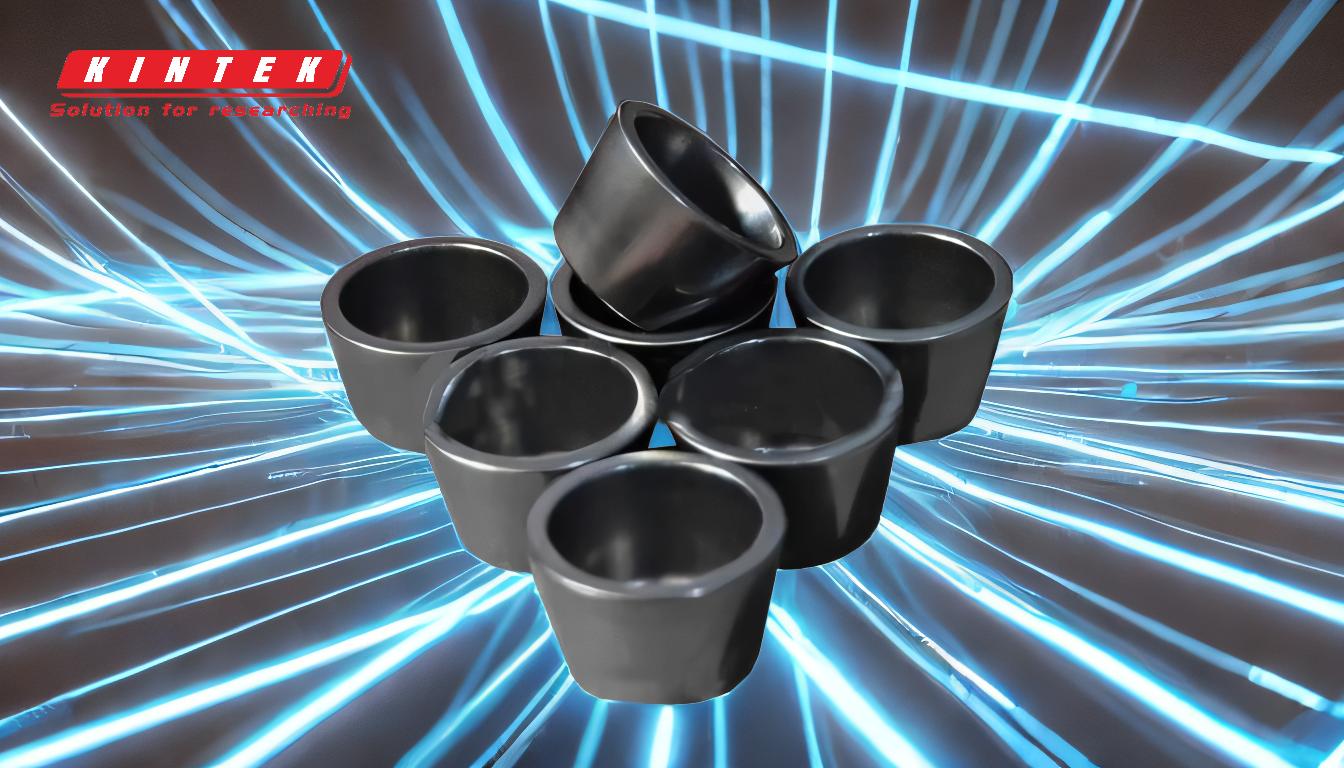
-
Mechanismus der Heizung:
- Thermische Verdampfung: Durch elektrischen Widerstand wird ein Tiegel erhitzt, der seinerseits das Ausgangsmaterial schmilzt und verdampft. Die Erhitzung erfolgt indirekt, da der Tiegel als Vermittler fungiert.
- E-Beam Verdampfung: Nutzt einen fokussierten, hochenergetischen Elektronenstrahl zur direkten Erhitzung und Verdampfung des Ausgangsmaterials. Bei dieser Methode wird die kinetische Energie direkt auf das Material übertragen, was eine effiziente Verdampfung ermöglicht.
-
Kompatibilität der Materialien:
- Thermische Verdampfung: Am besten geeignet für Materialien mit niedrigeren Schmelztemperaturen, wie Aluminium oder organische Verbindungen. Bei Materialien mit hohem Schmelzpunkt, wie Oxiden oder hochschmelzenden Metallen, ist es schwierig.
- E-Beam Verdampfung: Aufgrund der intensiven lokalen Erwärmung durch den Elektronenstrahl können Materialien mit hohem Schmelzpunkt, darunter Oxide, Keramik und hochschmelzende Metalle, bearbeitet werden.
-
Film-Eigenschaften:
- Thermische Verdampfung: Erzeugt Filme, die aufgrund der geringeren Energie, die mit dem Verfahren verbunden ist, weniger dicht sein können. Dies kann zu Folien mit höherer Porosität oder geringerer Adhäsion führen.
- E-Beam Verdampfung: Führt zu dichteren und gleichmäßigeren dünnen Schichten aufgrund der höheren Energie und der präzisen Steuerung des Elektronenstrahls. Dies führt zu einer besseren Schichtqualität und -haftung.
-
Ablagerungsrate:
- Thermische Verdampfung: Die Abscheidungsrate ist im Allgemeinen geringer als bei der Elektronenstrahlverdampfung, was sie für Anwendungen in großem Maßstab oder mit hohem Durchsatz langsamer macht.
- E-Beam Verdampfung: Bietet eine höhere Abscheidungsrate und ist damit effizienter für Anwendungen, die eine schnelle Beschichtung oder dickere Schichten erfordern.
-
Komplexität der Ausrüstung und Kosten:
- Thermische Verdampfung: Einfachere und kostengünstigere Geräte, da sie auf einfachen Widerstandsheizelementen und Tiegeln beruhen.
- E-Beam Verdampfung: Erfordert komplexere und kostspieligere Geräte, einschließlich Elektronenstrahlkanonen, Hochspannungsnetzteile und moderne Kühlsysteme.
-
Anwendungen:
- Thermische Verdampfung: Wird häufig für Anwendungen verwendet, bei denen Kosten und Einfachheit im Vordergrund stehen, z. B. für dekorative Beschichtungen oder einfache optische Schichten.
- E-Beam Verdampfung: Bevorzugt für Hochleistungsanwendungen, z. B. Halbleiterherstellung, moderne Optik und Beschichtungen für Hochtemperaturumgebungen.
-
Umweltbedingungen:
- Thermische Verdampfung: Arbeitet in einer Vakuumkammer, erfordert aber nicht so strenge Bedingungen wie die E-Beam-Verdampfung.
- E-Beam Verdampfung: Erfordert eine Hochvakuumumgebung, damit der Elektronenstrahl effizient arbeiten kann und die dünnen Schichten nicht kontaminiert werden.
-
Skalierbarkeit und Automatisierung:
- Thermische Verdampfung: Weniger skalierbar und schwieriger zu automatisieren, da sie auf Tiegel und Widerstandsheizung angewiesen ist.
- E-Beam Verdampfung: Es ist besser skalierbar und lässt sich leichter in automatisierte Systeme integrieren, wodurch es sich für die industrielle Produktion eignet.
Zusammenfassend lässt sich sagen, dass die Wahl zwischen thermischer Verdampfung und E-Beam-Verdampfung von den spezifischen Anforderungen der Anwendung abhängt, einschließlich der Materialeigenschaften, der gewünschten Schichtqualität, der Abscheidungsrate und der Budgetbeschränkungen. Die thermische Verdampfung ist eine kostengünstige Lösung für einfachere Anwendungen, während die E-Beam-Verdampfung für anspruchsvolle, hochpräzise Aufgaben eine überlegene Leistung bietet.
Zusammenfassende Tabelle:
Aspekt | Thermische Verdampfung | E-Beam Verdampfung |
---|---|---|
Mechanismus der Heizung | Elektrischer Widerstand erhitzt einen Schmelztiegel, um Materialien zu schmelzen und zu verdampfen. | Ein hochenergetischer Elektronenstrahl erhitzt und verdampft Materialien direkt. |
Kompatibilität der Materialien | Am besten geeignet für Materialien mit niedrigem Schmelzpunkt (z. B. Aluminium, organische Stoffe). | Geeignet für Materialien mit hohem Schmelzpunkt (z. B. Oxide, Keramik, hochschmelzende Metalle). |
Film-Eigenschaften | Weniger dichte Filme mit höherer Porosität oder geringerer Adhäsion. | Dichtere, gleichmäßigere Filme mit besserer Haftung. |
Ablagerungsrate | Geringere Abscheidungsrate, langsamer für großflächige Anwendungen. | Höhere Abscheidungsrate, effizient für schnelle Beschichtungen oder dickere Schichten. |
Ausstattung Kosten | Einfachere und billigere Ausrüstung. | Komplexere und kostspieligere Ausrüstung. |
Anwendungen | Dekorative Beschichtungen, grundlegende optische Schichten. | Halbleiterherstellung, moderne Optik, Hochtemperaturbeschichtungen. |
Bedürfnisse der Umwelt | Arbeitet in einer Vakuumkammer mit weniger strengen Bedingungen. | Für einen effizienten Betrieb ist eine Hochvakuumumgebung erforderlich. |
Skalierbarkeit | Weniger skalierbar und schwieriger zu automatisieren. | Sie sind besser skalierbar und lassen sich leichter in automatisierte Systeme integrieren. |
Sind Sie noch unsicher, welches PVD-Verfahren für Ihre Bedürfnisse geeignet ist? Kontaktieren Sie unsere Experten noch heute für persönliche Beratung!