Das Lasersintern, insbesondere das selektive Lasersintern (SLS), ist eine vielseitige additive Fertigungstechnik, die einzigartige Vor- und Nachteile bietet.Es ist in der Lage, hochkomplexe und funktionale Formen herzustellen, die mit herkömmlichen Sinterverfahren nur schwer zu erreichen sind.Es ist jedoch mit erheblichen Kosten verbunden, sowohl in Bezug auf die Ausrüstung als auch auf die Materialien, und erfordert qualifiziertes Personal.Andererseits sind alternative Verfahren wie die Pulvermetallurgie für die Großproduktion kostengünstiger, können aber zu ungleichmäßigen Bauteilen führen.Das Hochgeschwindigkeitssintern hat sich als vielversprechend erwiesen, wenn es um die Verbesserung von Dichte und Festigkeit geht, wird aber nicht allgemein befürwortet, was auf mögliche Einschränkungen hinweist.
Die wichtigsten Punkte werden erklärt:
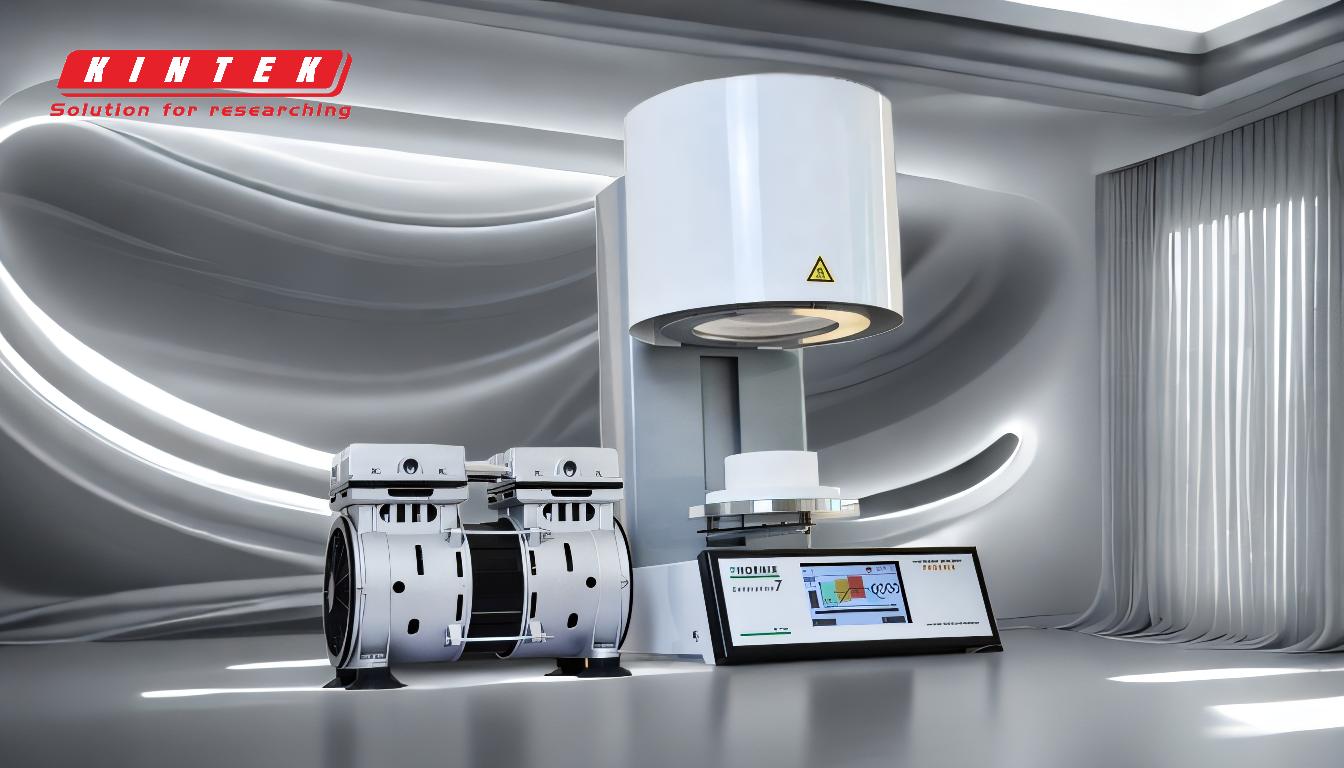
-
Vorteile des Laser-Sinterns:
- Komplexe und funktionelle Formen: Lasersintern, insbesondere SLS, eignet sich hervorragend zur Herstellung komplizierter und funktioneller Geometrien, die mit herkömmlichen Sinterverfahren nur schwer oder gar nicht zu erreichen sind.Dies macht es ideal für Anwendungen, die hohe Präzision und Komplexität erfordern, wie z. B. in der Luft- und Raumfahrt oder bei medizinischen Geräten.
- Vielseitigkeit der Materialien: SLS kann mit einer Vielzahl von Materialien arbeiten, darunter Polymere, Metalle und Keramiken, was vielfältige Anwendungen in verschiedenen Branchen ermöglicht.
- Minimale Nachbearbeitung: Durch SLS hergestellte Teile erfordern im Vergleich zu anderen additiven Fertigungsverfahren oft weniger Nachbearbeitung, da das Verfahren von Natur aus endkonturnahe Komponenten erzeugt.
-
Nachteile des Laser-Sinterns:
- Hohe Kosten: Die Erstinvestition für SLS-Maschinen ist beträchtlich und liegt oft über 250.000 $.Außerdem sind die beim SLS-Verfahren verwendeten Materialien teuer, was die Gesamtkosten weiter erhöht.
- Erfordernis qualifizierter Bediener: SLS erfordert Bediener mit speziellen Fähigkeiten und Schulungen, was die Betriebskosten und die Komplexität erhöht.
- Begrenzte Skalierbarkeit: SLS eignet sich zwar hervorragend für die Herstellung von Prototypen und Kleinserien, ist aber im Vergleich zu Verfahren wie der Pulvermetallurgie weniger effizient für die Großserienfertigung.
-
Vergleich mit der Pulvermetallurgie:
- Kosten-Nutzen-Verhältnis: Die Pulvermetallurgie ist im Allgemeinen kostengünstiger, sowohl in Bezug auf die Ausrüstung als auch auf die Werkstoffe, so dass sie sich besser für die Großserienproduktion eignet.
- Einfacher Betrieb: Im Gegensatz zum SLS erfordert die Pulvermetallurgie keine hochqualifizierten Bediener, was die Arbeitskosten und den Schulungsbedarf reduziert.
- Gleichmäßigkeitsprobleme: Ein Nachteil der Pulvermetallurgie ist das Potenzial für ungleichmäßige Komponenten aufgrund der Reibung zwischen dem Pulver und dem Werkzeug, was die Qualität und Konsistenz des Endprodukts beeinträchtigen kann.
-
Hochgeschwindigkeits-Sintern:
- Verbesserte Dichte und Festigkeit: Einige Studien deuten darauf hin, dass beim Hochgeschwindigkeitssintern Teile mit etwas höherer Dichte und Festigkeit als bei herkömmlichen Sinterverfahren hergestellt werden können.
- Begrenzte Befürwortung: Trotz dieser Vorteile wird das Hochgeschwindigkeitssintern nicht von allen Materiallieferanten befürwortet, insbesondere nicht von denen, die mit Zirkoniumdioxid arbeiten.Dies könnte auf Bedenken hinsichtlich der Materialkompatibilität, der Prozessstabilität oder anderer technischer Einschränkungen zurückzuführen sein.
-
Überlegungen für Einkäufer von Geräten und Verbrauchsmaterialien:
- Anforderungen der Anwendung: Bei der Entscheidung zwischen SLS und anderen Sinterverfahren sollten die Käufer die spezifischen Anforderungen ihrer Anwendung berücksichtigen, z. B. den Bedarf an komplexen Geometrien, die Materialeigenschaften und das Produktionsvolumen.
- Budgetbeschränkungen: Die hohen Kosten, die mit SLS verbunden sind, können für einige Organisationen ein einschränkender Faktor sein, insbesondere für solche mit begrenzten Budgets oder solche, die eine Produktion in großem Maßstab benötigen.
- Fachwissen des Bedieners: Der Bedarf an qualifiziertem Personal sollte bei der Entscheidungsfindung berücksichtigt werden, da er sich sowohl auf die anfänglichen als auch auf die laufenden Betriebskosten auswirken kann.
- Materialkompatibilität: Wer das Hochgeschwindigkeitssintern in Erwägung zieht, muss unbedingt die Materialverträglichkeit prüfen und sich mit den Lieferanten beraten, um sicherzustellen, dass das Verfahren für die geplante Anwendung geeignet ist.
Zusammenfassend lässt sich sagen, dass das Lasersintern, insbesondere das SLS-Verfahren, erhebliche Vorteile in Bezug auf Designflexibilität und Materialvielfalt bietet, aber auch mit hohen Kosten und Betriebskomplexität verbunden ist.Alternative Verfahren wie die Pulvermetallurgie sind für die Großserienproduktion kostengünstiger, können aber Kompromisse bei der Gleichmäßigkeit der Bauteile eingehen.Das Hochgeschwindigkeitssintern hat das Potenzial, die Materialeigenschaften zu verbessern, wird aber nicht allgemein akzeptiert, was darauf hindeutet, dass seine Grenzen sorgfältig geprüft werden müssen.Die Käufer sollten diese Faktoren gegen ihre spezifischen Bedürfnisse und Einschränkungen abwägen, um eine fundierte Entscheidung zu treffen.
Zusammenfassende Tabelle:
Aspekt | Laser-Sintern (SLS) | Pulvermetallurgie | Hochgeschwindigkeits-Sintern |
---|---|---|---|
Komplexe Formen | Hervorragend geeignet für die Erstellung komplizierter und funktionaler Geometrien | Begrenzte Fähigkeit zur Herstellung komplexer Formen | Begrenzte Daten verfügbar |
Vielseitigkeit der Materialien | Geeignet für Polymere, Metalle und Keramik | Begrenzte Materialoptionen | Mögliche Kompatibilitätsprobleme mit Materialien wie Zirkoniumdioxid |
Kosten | Hohe Anfangsinvestitionen (>250.000 $) und teure Materialien | Kosteneffizienter für die Produktion in großem Maßstab | Die Kosten variieren; nicht allgemein befürwortet |
Geschicklichkeit des Bedieners | Erfordert hochqualifizierte Bediener | Einfacher zu bedienen; weniger Fachkräfte erforderlich | Erfordert Spezialwissen |
Skalierbarkeit | Am besten geeignet für Prototyping und Kleinserienproduktion | Geeignet für Großserienproduktion | Begrenzte Skalierbarkeit aufgrund technischer Beschränkungen |
Nachbearbeitung | Minimale Nachbearbeitung erforderlich | Kann mehr Nachbearbeitung erfordern | Minimale Nachbearbeitung |
Gleichmäßigkeit der Komponenten | Hohe Präzision und Konsistenz | Potenzial für uneinheitliche Komponenten | Verbesserte Dichte und Festigkeit, aber eingeschränkte Akzeptanz |
Benötigen Sie Hilfe bei der Auswahl des richtigen Sinterverfahrens für Ihre Anwendung? Kontaktieren Sie noch heute unsere Experten für eine persönliche Beratung!