Die physikalische Gasphasenabscheidung (PVD) ist eine weit verbreitete Technik zur Abscheidung dünner Schichten auf Substraten und wird in zwei Haupttypen eingeteilt: thermische Verdampfung und Sputtern .Diese Methoden unterscheiden sich durch ihre Mechanismen der Materialverdampfung und -abscheidung.Beim thermischen Verdampfen wird ein Material erhitzt, bis es verdampft und auf dem Substrat kondensiert.Beim Sputtern hingegen werden mit Hilfe eines Plasmas Atome aus einem Zielmaterial ausgestoßen, die sich dann auf dem Substrat ablagern.Beide Verfahren werden in einer Vakuumumgebung durchgeführt, um eine hochwertige Schichtabscheidung zu gewährleisten.PVD wird häufig der chemischen Gasphasenabscheidung (CVD) vorgezogen, da es bei niedrigeren Temperaturen arbeiten kann und Schichten mit weniger Verunreinigungen erzeugt.
Die wichtigsten Punkte werden erklärt:
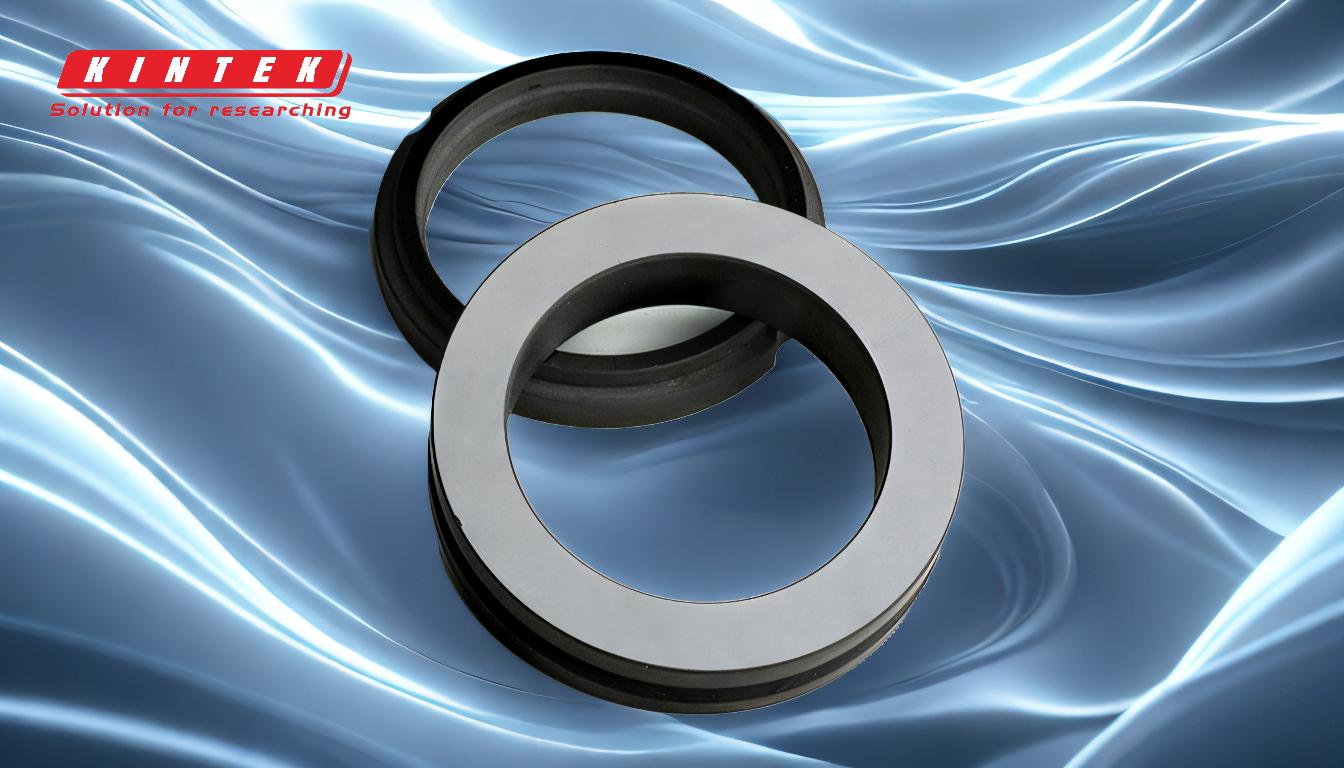
-
Thermische Verdampfung:
- Prozess:Bei der thermischen Verdampfung wird das zu beschichtende Material in einem Vakuum erhitzt, bis es verdampft.Der Dampf wandert dann durch das Vakuum und kondensiert auf dem Substrat, wobei sich ein dünner Film bildet.
- Vorteile:Dieses Verfahren ist relativ einfach und ermöglicht die Abscheidung einer breiten Palette von Materialien, darunter Metalle, Legierungen und einige organische Verbindungen.Sie ist besonders nützlich für Anwendungen, die hochreine Schichten erfordern.
- Beschränkungen:Die thermische Verdampfung ist ein Sichtlinienverfahren, was bedeutet, dass es für die Beschichtung komplexer Geometrien oder Bereiche, die nicht direkt in der Sichtlinie der Dampfquelle liegen, weniger effektiv ist.
-
Sputtern:
- Prozess:Beim Sputtern wird ein Zielmaterial mit hochenergetischen Ionen (in der Regel aus einem Plasma) beschossen, um Atome aus dem Zielmaterial auszustoßen.Diese ausgestoßenen Atome lagern sich dann auf dem Substrat ab.
- Vorteile:Durch Sputtern können sehr gleichmäßige und dichte Schichten erzeugt werden, selbst auf komplexen Geometrien.Außerdem kann eine breite Palette von Materialien abgeschieden werden, darunter Metalle, Halbleiter und Isolatoren.
- Beschränkungen:Das Verfahren kann langsamer sein als die thermische Verdampfung und erfordert unter Umständen eine komplexere Ausrüstung, wie z. B. eine Mikrowellenplasmaanlage zur chemischen Gasphasenabscheidung System zur Erzeugung des erforderlichen Plasmas.
-
Vergleich mit CVD:
- Temperatur:PVD-Verfahren, einschließlich der thermischen Verdampfung und des Sputterns, arbeiten in der Regel bei niedrigeren Temperaturen (250°C~450°C) als CVD-Verfahren, die häufig Temperaturen zwischen 450°C und 1050°C erfordern.
- Zustand des Materials:Beim PVD-Verfahren werden feste Materialien verwendet, die verdampft und dann abgeschieden werden, während beim CVD-Verfahren gasförmige Ausgangsstoffe verwendet werden, die chemisch reagieren, um den Film zu bilden.
- Umweltauswirkungen:PVD gilt allgemein als umweltfreundlicher als CVD, da es keine korrosiven gasförmigen Nebenprodukte erzeugt.
-
Anwendungen:
- Thermische Verdampfung:Wird häufig bei der Herstellung von optischen Beschichtungen, Solarzellen und Dünnschichttransistoren verwendet.
- Sputtern:Weit verbreitet in der Halbleiterindustrie, bei der Herstellung von harten Beschichtungen auf Werkzeugen und bei der Herstellung von dekorativen Beschichtungen.
-
Vakuum Umgebung:
- Sowohl das thermische Verdampfen als auch das Sputtern werden im Vakuum durchgeführt, um die Verunreinigung zu minimieren und die Reinheit der abgeschiedenen Schicht zu gewährleisten.Die Vakuumumgebung hilft auch bei der Kontrolle der Abscheidungsrate und der Schichtqualität.
Zusammenfassend lässt sich sagen, dass die beiden wichtigsten PVD-Verfahren - thermische Verdampfung und Sputtern - unterschiedliche Vorteile bieten und je nach den spezifischen Anforderungen der Anwendung ausgewählt werden.Während die thermische Verdampfung einfacher ist und sich für hochreine Schichten eignet, bietet das Sputtern eine bessere Abdeckung komplexer Geometrien und ist in der High-Tech-Industrie weit verbreitet.Beide Verfahren werden im Vakuum durchgeführt, um eine optimale Schichtqualität zu gewährleisten, und sind im Allgemeinen umweltfreundlicher als die CVD.
Zusammenfassende Tabelle:
Aspekt | Thermische Verdampfung | Sputtern |
---|---|---|
Verfahren | Das Material wird erhitzt, verdampft und kondensiert auf dem Substrat. | Hochenergetische Ionen stoßen Atome aus einem Target aus, die sich auf dem Substrat niederschlagen. |
Vorteile | Einfaches Verfahren, hochreine Schichten, geeignet für Metalle, Legierungen und organische Verbindungen. | Gleichmäßige und dichte Schichten, funktioniert bei komplexen Geometrien, vielseitige Materialverwendung. |
Beschränkungen | Sichtlinienverfahren, weniger effektiv bei komplexen Geometrien. | Langsamerer Prozess, erfordert komplexe Geräte wie Plasmasysteme. |
Anwendungen | Optische Beschichtungen, Solarzellen, Dünnschichttransistoren. | Halbleiterindustrie, harte Beschichtungen, dekorative Beschichtungen. |
Vakuum-Umgebung | Im Vakuum durchgeführt, um eine qualitativ hochwertige Schichtabscheidung zu gewährleisten. | Die Abscheidung erfolgt im Vakuum, um Verunreinigungen zu minimieren und die Abscheidungsrate zu kontrollieren. |
Benötigen Sie Hilfe bei der Auswahl des richtigen PVD-Verfahrens für Ihre Anwendung? Kontaktieren Sie unsere Experten noch heute!