Dünnfilmbeschichtungen sind in verschiedenen Industriezweigen, darunter Elektronik, Optik und Energie, unverzichtbar, da sie eine präzise Kontrolle der Materialeigenschaften ermöglichen.Diese Beschichtungen lassen sich anhand ihrer Abscheidungsmethoden, Eigenschaften und Anwendungen in verschiedene Kategorien einteilen.Zu den gängigen Beschichtungsverfahren gehören die physikalische Gasphasenabscheidung (PVD), die chemische Gasphasenabscheidung (CVD), die Schleuderbeschichtung und die Atomlagenabscheidung (ALD).Dünne Schichten werden allgemein in optische, elektrische, magnetische, chemische, mechanische und thermische Typen eingeteilt, die jeweils spezifische Funktionen erfüllen, wie z. B. reflektierende Beschichtungen, Halbleitergeräte, Speicherplatten, Korrosionsbeständigkeit und Wärmeisolierung.Darüber hinaus gibt es unterschiedliche Größenordnungen von Dünnschichtbeschichtungsanlagen, von großen Fabrikanlagen für die Massenproduktion bis hin zu kleinen Laborsystemen für Versuchszwecke.
Die wichtigsten Punkte erklärt:
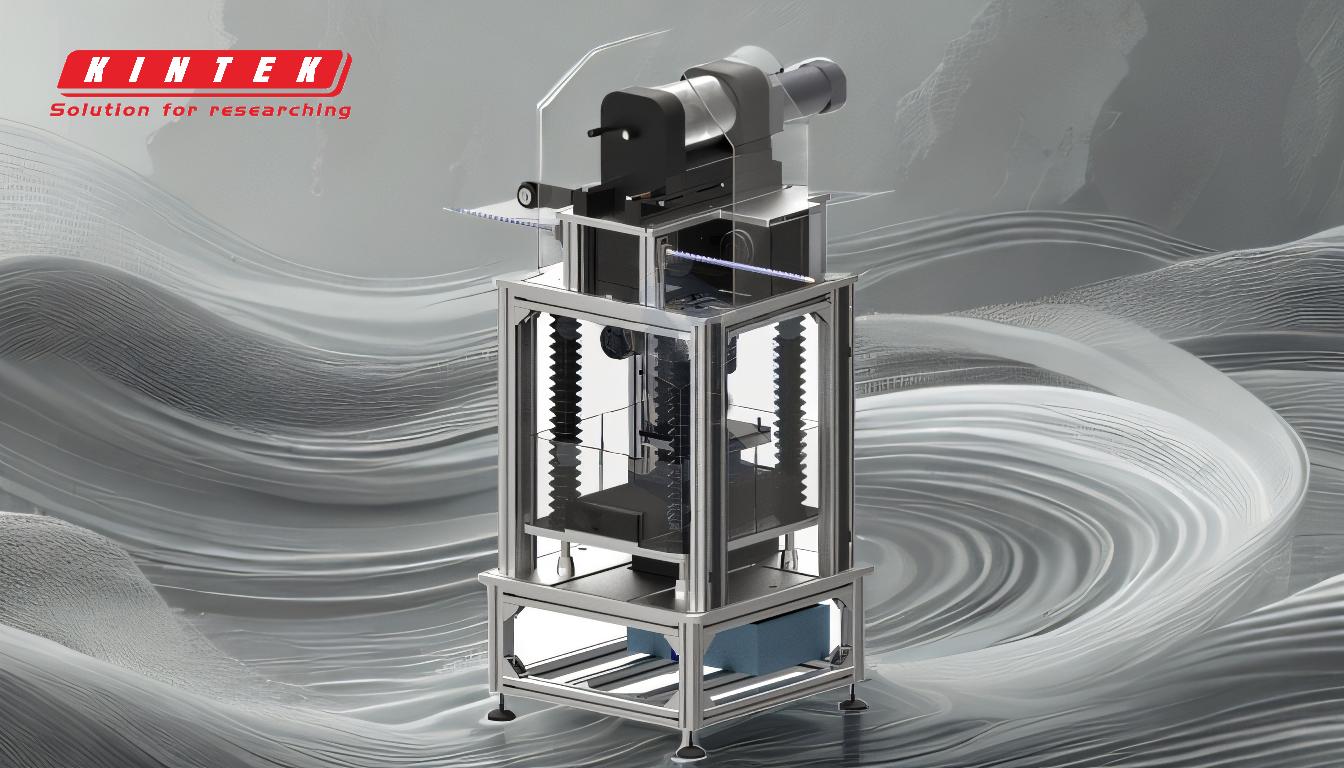
-
Depositionsmethoden:
-
Physikalische Gasphasenabscheidung (PVD):Bei diesem Verfahren wird ein festes Material im Vakuum verdampft und auf ein Substrat aufgebracht.Zu den Techniken gehören:
- Verdampfung:Einsatz von Wärmeenergie (z. B. Elektronenstrahl) zur Verdampfung des Materials.
- Sputtern:Beschuss eines Zielmaterials mit Ionen, um Atome auszustoßen, die sich dann auf dem Substrat ablagern.
- Chemische Gasphasenabscheidung (CVD):Zur Herstellung hochreiner dünner Schichten werden chemische Reaktionen genutzt.Vorläufergase reagieren auf der Substratoberfläche und bilden die Schicht.
- Atomlagenabscheidung (ALD):Ein präzises Verfahren, bei dem eine Schicht nach der anderen aufgebracht wird, was eine hervorragende Kontrolle der Schichtdicke und Gleichmäßigkeit gewährleistet.
- Spin-Beschichtung:Ein flüssiger Vorläufer wird auf ein Substrat aufgetragen, das dann mit hoher Geschwindigkeit geschleudert wird, um einen gleichmäßigen dünnen Film zu erzeugen.
- Tropfengießen und Ölbad:Einfache Verfahren, bei denen eine Lösung auf ein Substrat getropft oder eingetaucht wird, häufig zu Versuchszwecken.
-
Physikalische Gasphasenabscheidung (PVD):Bei diesem Verfahren wird ein festes Material im Vakuum verdampft und auf ein Substrat aufgebracht.Zu den Techniken gehören:
-
Arten von Dünnschichten:
-
Optische Dünnschichten:Wird in Anwendungen verwendet, die eine Lichtmanipulation erfordern, wie z. B.:
- Reflektierende und antireflektierende Beschichtungen.
- Solarzellen und optische Detektorarrays.
- Wellenleiter und Monitore.
-
Elektrische/Elektronische Dünnschichten:Wesentlich für elektronische Geräte, einschließlich:
- Isolatoren, Leiter und Halbleiterbauelemente.
- Integrierte Schaltungen und piezoelektrische Antriebe.
- Magnetische Dünnschichten:Wird bei der Datenspeicherung verwendet, z. B. bei Speicherplatten.
- Chemische Dünnschichten:Sie sind korrosions-, oxidations- und diffusionsbeständig und werden in Gas- und Flüssigkeitssensoren eingesetzt.
-
Mechanische Dünnschichten:Verbesserung der Oberflächeneigenschaften, wie z.B.:
- Tribologische Beschichtungen für Abriebfestigkeit.
- Erhöhte Härte und Adhäsion.
- Mikro-mechanische Anwendungen.
-
Thermische Dünnschichten:Verwendet für das Wärmemanagement, einschließlich:
- Isolierschichten.
- Kühlkörper für die Wärmeableitung.
-
Optische Dünnschichten:Wird in Anwendungen verwendet, die eine Lichtmanipulation erfordern, wie z. B.:
-
Anwendungen von Dünnschichten:
- Optische Anwendungen:Verbessern Sie die Leistung von Linsen, Spiegeln und Displays.
- Elektronische Anwendungen:Ermöglichen die Miniaturisierung und Funktionalität von Geräten wie Transistoren und Sensoren.
- Energie-Anwendungen:Verwendung in Solarzellen und Energiespeichersystemen.
- Industrielle Anwendungen:Schutzbeschichtungen für Werkzeuge und Maschinen.
- Biomedizinische Anwendungen:Aufgrund ihrer Biokompatibilität und Präzision werden sie in Sensoren und Implantaten verwendet.
-
Dünnfilm-Beschichtungssysteme:
- Batch-Systeme:Konzipiert für die Produktion mit hohem Durchsatz, kann es mehrere Wafer gleichzeitig in einer einzigen Kammer bearbeiten.
- Cluster-Werkzeuge:Verwendung mehrerer Kammern für verschiedene Prozesse, die eine sequentielle Bearbeitung einzelner Wafer ermöglichen.
- Fabrik-Systeme:Großsysteme für die Großserienfertigung, oft in Produktionslinien integriert.
- Labor-Systeme:Kompakt und vielseitig, ideal für Forschung und Entwicklung oder experimentelle Arbeiten in kleinen Stückzahlen.
-
Vorteile von Dünnfilmbeschichtungen:
- Präzision:Möglichkeit der Kontrolle von Dicke und Zusammensetzung auf atomarer Ebene.
- Vielseitigkeit:Geeignet für eine breite Palette von Materialien und Anwendungen.
- Kundenspezifische Anpassung:Maßgeschneidert, um spezifische funktionale Anforderungen zu erfüllen, wie z. B. optische, elektrische oder mechanische Eigenschaften.
- Wirkungsgrad:Verbessert die Leistung und Lebensdauer von Bauteilen und senkt die Kosten für Wartung und Austausch.
Wenn man die Arten von Dünnfilmbeschichtungen, ihre Abscheidungsmethoden und ihre Anwendungen versteht, können Käufer fundierte Entscheidungen treffen, um ihre spezifischen Bedürfnisse zu erfüllen, ob für industrielle, elektronische oder experimentelle Zwecke.
Zusammenfassende Tabelle:
Kategorie | Wichtige Informationen |
---|---|
Abscheidungsmethoden | PVD (Verdampfung, Sputtern), CVD, ALD, Spin Coating, Tropfengießen, Ölbad |
Arten von Dünnschichten | Optisch, elektrisch, magnetisch, chemisch, mechanisch, thermisch |
Anwendungen | Optik, Elektronik, Energie, Industrie, Biomedizin |
Beschichtungs-Systeme | Batch-Systeme, Cluster-Tools, Fabrik-Systeme, Labor-Systeme |
Vorteile | Präzision, Vielseitigkeit, Anpassungsfähigkeit, Effizienz |
Entdecken Sie, wie Dünnfilmbeschichtungen Ihre Anwendungen verändern können. Kontaktieren Sie unsere Experten noch heute !