Das Sintern ist ein entscheidender Prozess in der Materialwissenschaft, der in erster Linie durch die Verringerung der Oberflächenenergie bei der Bindung von Partikeln bei hohen Temperaturen angetrieben wird.Dieser Prozess kann unterhalb des Schmelzpunktes durch Festkörpersintern oder durch die Bildung einer flüssigen Phase erfolgen.Die treibende Kraft hinter der Sinterung ist die Minimierung der Oberflächenenergie, die durch die Verringerung der Dampf-Festkörper-Grenzflächen der Partikel erreicht wird.Zu den Schlüsselfaktoren, die die Sinterung beeinflussen, gehören Temperatur, Heizrate, Druck, Partikelgröße und Zusammensetzung.Diese Faktoren bestimmen zusammen die Kinetik, die Verdichtung und die endgültigen Eigenschaften des gesinterten Materials.Darüber hinaus spielen die Sinteratmosphäre, die Abkühlgeschwindigkeit und Prozessparameter wie Schichtdicke und Maschinengeschwindigkeit eine wichtige Rolle bei der Optimierung des Sinterprozesses für die gewünschten Materialeigenschaften.
Die wichtigsten Punkte werden erklärt:
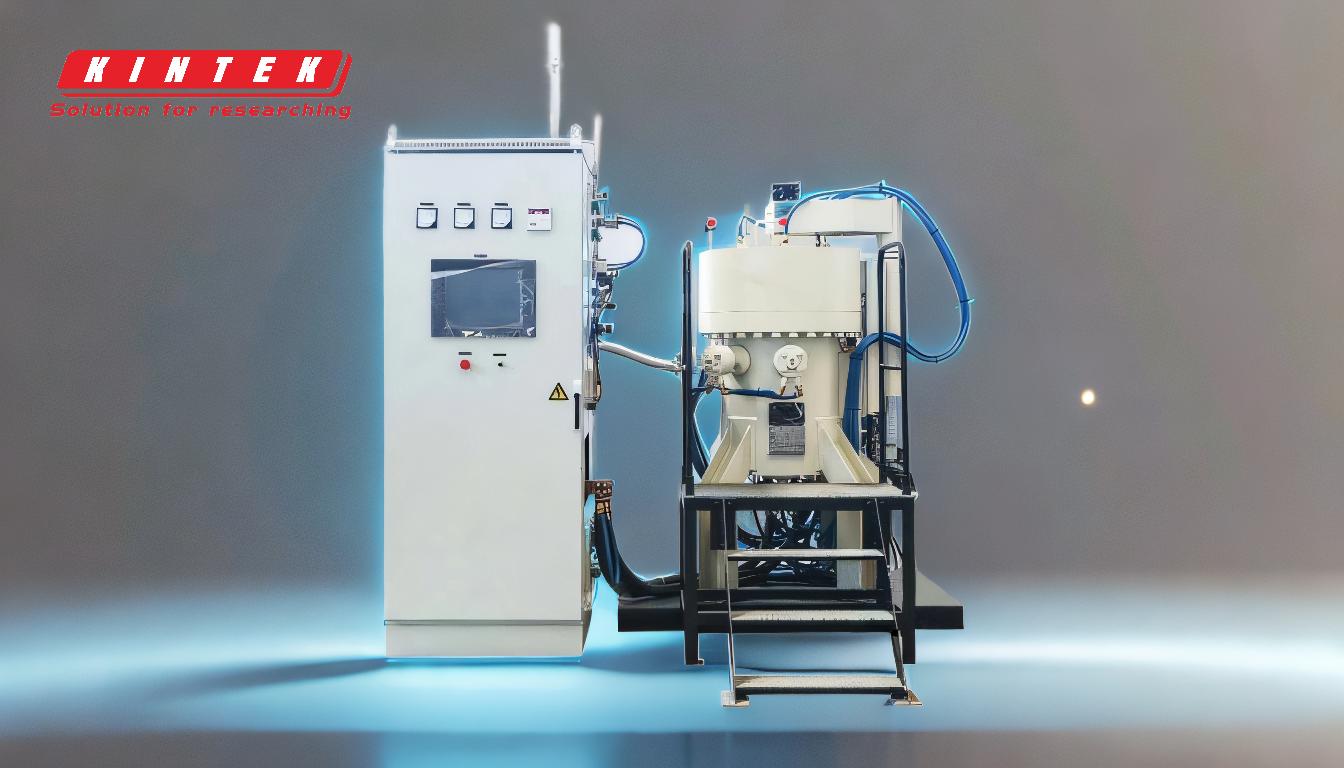
-
Treibende Kraft der Sinterung:
- Die treibende Kraft hinter dem Sintern ist in erster Linie die Verringerung der Oberflächenenergie.Wenn sich Partikel bei hohen Temperaturen verbinden, nimmt die Gesamtoberfläche ab, was zu einer Verringerung der Oberflächenenergie führt.Dies wird durch die Minimierung der Dampf-Festkörper-Grenzflächen der Partikel erreicht.
- Die Sinterung kann unterhalb des Schmelzpunktes (typischerweise 0,7-0,8 der Schmelztemperatur) durch Festkörpersintern erfolgen, bei dem Atome über die Partikelgrenzen diffundieren und Bindungen eingehen.Alternativ kann das Sintern auch die Bildung einer flüssigen Phase beinhalten, die die Partikelbindung verstärkt.
-
Schlüsselfaktoren, die die Sinterung beeinflussen:
- Die Temperatur: Die Temperatur ist ein entscheidender Faktor, der die Kinetik der Sinterung und die endgültigen Materialeigenschaften bestimmt.Höhere Temperaturen erhöhen im Allgemeinen die Diffusionsgeschwindigkeit, was zu einer schnelleren Verdichtung und stärkeren Bindungen zwischen den Partikeln führt.
- Heizrate: Die Geschwindigkeit, mit der das Material erhitzt wird, beeinflusst den Verdichtungsprozess.Eine kontrollierte Heizrate gewährleistet eine gleichmäßige Verdichtung und minimiert Defekte wie Risse oder Verformungen.
- Druck: Der während des Sinterns ausgeübte Druck fördert die Umstrukturierung der Partikel und trägt zur Beseitigung von Porosität bei, was zu einem dichteren und gleichmäßigeren Endprodukt führt.
- Partikelgröße: Kleinere Partikel haben ein größeres Verhältnis von Oberfläche zu Volumen, was eine schnellere Diffusion und bessere Verdichtung fördert.Feine Pulver werden wegen ihres besseren Sinterverhaltens häufig für das Sintern bevorzugt.
- Zusammensetzung: Die chemische Zusammensetzung des Materials wirkt sich auf sein Sinterverhalten aus.Homogene Zusammensetzungen mit gut verteilten Partikeln neigen dazu, gleichmäßiger zu sintern und Materialien mit besseren mechanischen Eigenschaften zu erzeugen.
-
Sinteratmosphäre und Abkühlungsgeschwindigkeit:
- Die Atmosphäre, in der die Sinterung stattfindet (z. B. Luft, Vakuum oder Inertgase wie Argon/Stickstoff), kann den Prozess erheblich beeinflussen.Eine Vakuum- oder Inertgasatmosphäre verhindert zum Beispiel die Oxidation und ermöglicht eine bessere Kontrolle der Sinterumgebung.
- Die Abkühlungsgeschwindigkeit nach dem Sintern wirkt sich auf das Mikrogefüge und die endgültigen Eigenschaften des Werkstoffs aus.Eine schnelle Abkühlung kann zu einem feineren Korngefüge führen, während eine langsamere Abkühlung zu größeren Körnern und anderen mechanischen Eigenschaften führen kann.
-
Prozessparameter:
- Schichtdicke und Maschinengeschwindigkeit: Bei industriellen Sinterprozessen werden die Dicke der Materialschicht und die Geschwindigkeit der Sintermaschine sorgfältig kontrolliert.Typische Schichtdicken liegen zwischen 250 und 500 mm, und die Maschinengeschwindigkeit wird bei 1,5 bis 4 m/min gehalten, um sicherzustellen, dass das Material gleichmäßig gesintert wird und den gewünschten Endpunkt erreicht.
- Luftmenge und Vakuum: Die Luftmenge und die Vakuumbedingungen sind entscheidend für die Steuerung der Sinterumgebung.Die Luftmenge beträgt in der Regel etwa 3200m³ pro Tonne Sintererz, und das Vakuum wird durch Faktoren wie Gebläseleistung, Luftwiderstand und Windleckverluste bestimmt.
-
Sintertechniken:
- Je nach den spezifischen Anforderungen an das Material und den gewünschten Eigenschaften werden verschiedene Sintertechniken eingesetzt.Diese Techniken können den Einsatz von elektrischen Strömen, Druck oder verschiedenen Wärmequellen beinhalten.Die Wahl des Verfahrens hängt von Faktoren wie dem zu sinternden Material, der erforderlichen Dichte und der Endanwendung des Produkts ab.
-
Thermisch aktivierte Festkörperdiffusion:
- Die Sinterung wird im Wesentlichen durch thermisch aktivierte Festkörperdiffusionsmechanismen gesteuert.Diese Mechanismen lassen sich mit Hilfe von Sintermodellen und Werkzeugen wie dem Linseis-Stößeldilatometer quantifizieren, das die Dimensionsänderungen von Werkstoffen während des Sinterns misst.
-
Optimierung des Sinterprozesses:
- Der optimale Sinterprozess wird von Parametern wie der Sintertemperatur, dem angewandten Druck, der durchschnittlichen Korngröße und der Gasatmosphäre beeinflusst.Feinere Pulver und höhere Temperaturen erhöhen im Allgemeinen die Verdichtung, aber die Menge der flüssigen Phase muss sorgfältig kontrolliert werden, um Defekte zu vermeiden.Die Wahl der Prozessparameter hängt von den erwarteten Produkteigenschaften und den begrenzenden Faktoren des Sinterprozesses ab.
Zusammenfassend lässt sich sagen, dass das Sintern ein komplexer Prozess ist, der durch die Verringerung der Oberflächenenergie angetrieben und von einer Vielzahl von Faktoren wie Temperatur, Druck, Partikelgröße und Sinteratmosphäre beeinflusst wird.Das Verständnis und die Kontrolle dieser Faktoren sind entscheidend für die Optimierung des Sinterprozesses, um die gewünschten Materialeigenschaften und Leistungen zu erzielen.
Zusammenfassende Tabelle:
Aspekt | Einzelheiten |
---|---|
Treibende Kraft | Verringerung der Oberflächenenergie durch Partikelbindung bei erhöhten Temperaturen. |
Schlüsselfaktoren | Temperatur, Heizrate, Druck, Partikelgröße und Zusammensetzung. |
Sinteratmosphäre | Luft, Vakuum oder Inertgase (z. B. Argon/Stickstoff). |
Prozess-Parameter | Schichtdicke (250-500mm), Maschinengeschwindigkeit (1,5-4m/min), Luftmenge (3200m³/Tonne). |
Optimierung | Kontrollierte Temperatur, Druck, Korngröße und Gasatmosphäre. |
Optimieren Sie Ihren Sinterprozess für eine bessere Materialleistung - Kontaktieren Sie unsere Experten noch heute !