Ein Gleichstromsintersystem (DCS) ist eine fortschrittliche Sintertechnologie, bei der ein kontinuierlicher Gleichstrom zum Erhitzen einer leitfähigen Graphitmatrize verwendet wird, während gleichzeitig Druck ausgeübt wird.Dieses System nutzt die Joule-Erwärmung, bei der der elektrische Widerstand innerhalb der Matrize Wärme erzeugt, was schnelle Aufheizraten (bis zu 600 °C pro Minute) und das Erreichen hoher Temperaturen (über 1500 °C) innerhalb von Minuten ermöglicht.Im Gegensatz zu herkömmlichen Sinterverfahren kombiniert das DCS Wärme und Druck in einem einzigen Schritt und ist damit hocheffizient für die Verdichtung von pulverförmigen Materialien wie Keramik, Metallen und gesinterten Kunststoffen.Das Verfahren vermeidet eine Verflüssigung, indem es unterhalb des Schmelzpunkts des Materials arbeitet und die Partikelbindung durch Festkörperdiffusion gewährleistet.DCS wird vor allem wegen seiner Schnelligkeit, Präzision und Fähigkeit zur Herstellung hochdichter, strukturell robuster Komponenten geschätzt.
Die wichtigsten Punkte werden erklärt:
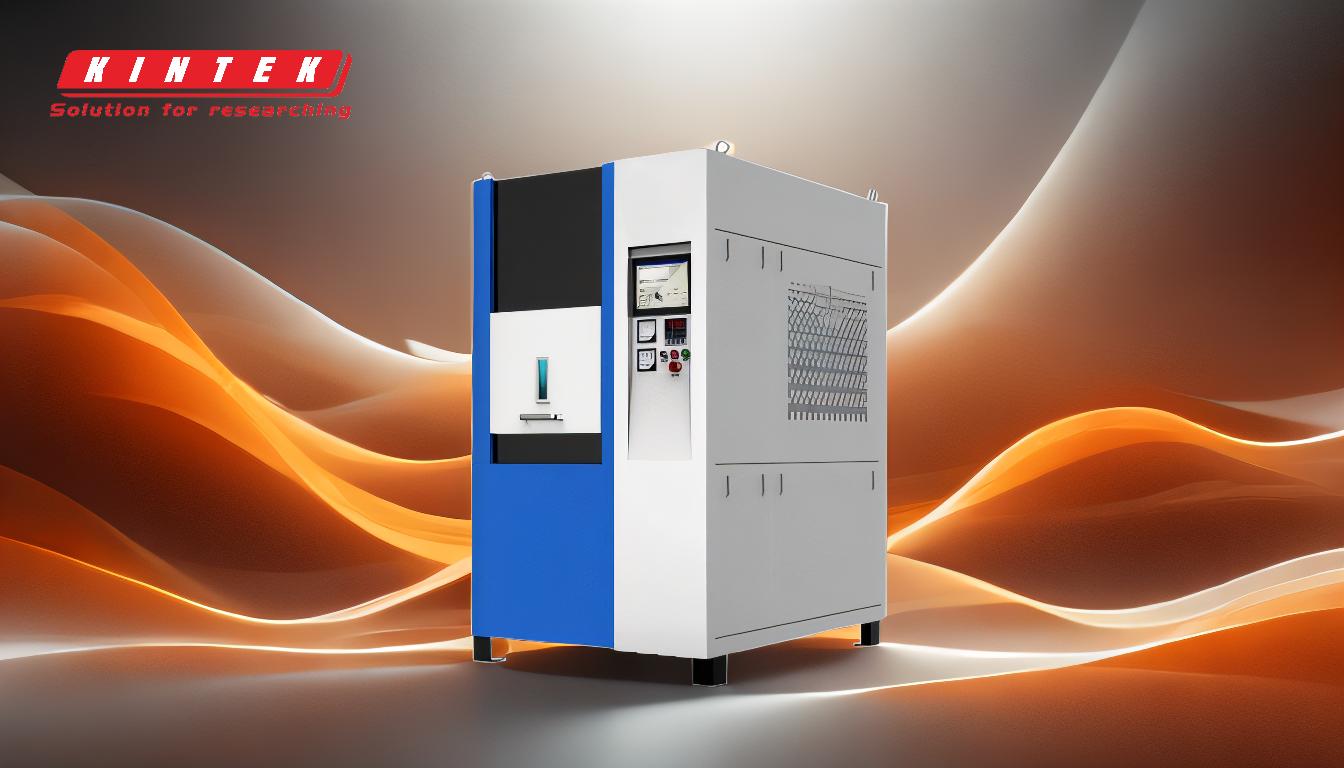
-
Definition des Gleichstromsinterns (DCS):
- DCS ist ein Sinterverfahren, bei dem ein kontinuierlicher Gleichstrom verwendet wird, um eine leitfähige Graphitmatrize zu erhitzen und gleichzeitig Druck auszuüben.Diese einzigartige Kombination von Wärme und Druck ermöglicht eine schnelle Verdichtung von pulverförmigen Materialien.
-
Mechanismus der Erwärmung:
- Das System beruht auf der Jouleschen Erwärmung, bei der der elektrische Widerstand im Graphitstempel Wärme erzeugt.Diese Methode ermöglicht extrem schnelle Heizraten (bis zu 600 °C pro Minute) und kann in wenigen Minuten Temperaturen von über 1500 °C erreichen.
-
Gleichzeitige Anwendung von Wärme und Druck:
- Im Gegensatz zu herkömmlichen Sinterverfahren, bei denen Erhitzen und Pressen in getrennten Schritten erfolgen können, werden bei DCS beide Vorgänge gleichzeitig ausgeführt.Diese Integration steigert die Effizienz und Effektivität des Sinterprozesses.
-
Für DCS geeignete Materialien:
- DCS ist vielseitig und kann für eine breite Palette von Materialien eingesetzt werden, darunter Keramik, Metalle und gesinterte Kunststoffe.Das Verfahren eignet sich besonders gut für Werkstoffe, die strukturell robuste Komponenten mit hoher Dichte erfordern.
-
Vermeidung von Verflüssigung:
- Das Verfahren arbeitet unterhalb des Schmelzpunkts des Materials und gewährleistet, dass sich die Partikel durch Festkörperdiffusion verbinden, ohne sich zu verflüssigen.Dadurch bleiben die Eigenschaften und die strukturelle Integrität des Materials erhalten.
-
Vorteile von DCS:
- Schnelligkeit: Schnelle Aufheizraten reduzieren die Verarbeitungszeit erheblich.
- Präzision: Kontrollierte Erhitzung und Druckanwendung gewährleisten gleichbleibende Ergebnisse.
- Dichte: Erzeugt Komponenten mit hoher Dichte und minimaler Porosität.
- Vielseitigkeit: Geeignet für eine breite Palette von Materialien und Anwendungen.
-
Anwendungen von DCS:
- DCS wird in vielen Branchen eingesetzt, in denen Hochleistungsmaterialien benötigt werden, z. B. in der Luft- und Raumfahrt, der Automobilindustrie und der Elektronik.Es ist besonders vorteilhaft für die Herstellung komplexer Formen und Komponenten mit anspruchsvollen mechanischen und thermischen Eigenschaften.
-
Vergleich mit dem herkömmlichen Sintern:
- Herkömmliche Sinterverfahren umfassen häufig getrennte Heiz- und Pressphasen, die zeitaufwändig und weniger effizient sein können.Das Gleichstromsintern rationalisiert den Prozess durch die Kombination dieser Schritte, was zu schnelleren Produktionszeiten und qualitativ hochwertigeren Ergebnissen führt.
Wenn die Käufer von Anlagen und Verbrauchsmaterialien diese Schlüsselpunkte verstehen, können sie die Vorteile von Gleichstromsinteranlagen besser einschätzen und fundierte Entscheidungen bei der Auswahl von Sintertechnologien für ihre spezifischen Anforderungen treffen.
Zusammenfassende Tabelle:
Hauptmerkmal | Beschreibung |
---|---|
Mechanismus der Erwärmung | Joule-Erwärmung über elektrischen Widerstand in einem Graphitstempel. |
Aufheizgeschwindigkeit | Bis zu 600°C pro Minute. |
Maximale Temperatur | Übersteigt 1500°C in Minuten. |
Unterstützte Materialien | Keramiken, Metalle, gesinterte Kunststoffe. |
Die wichtigsten Vorteile | Geschwindigkeit, Präzision, hohe Ausgabedichte, Vielseitigkeit. |
Anwendungen | Luft- und Raumfahrt, Automobilindustrie, Elektronik und Herstellung von Hochleistungsmaterialien. |
Transformieren Sie Ihre Materialverarbeitung mit einem DCS-System - Kontaktieren Sie uns noch heute um mehr zu erfahren!