Physical Vapour Deposition (PVD) und Chemical Vapour Deposition (CVD) sind zwei weit verbreitete Dünnschichtabscheidungstechniken mit unterschiedlichen Prozessen und Anwendungen. Bei der PVD wird ein festes Material im Vakuum verdampft und auf einem Substrat abgeschieden, während bei der CVD chemische Reaktionen gasförmiger Vorläufer zur Bildung eines dünnen Films auf einem Substrat genutzt werden. PVD wird häufig in Branchen wie der Elektronik-, Automobil- und Modeindustrie für Beschichtungen verwendet, die das Reflexionsvermögen, die Haltbarkeit oder die Ästhetik verbessern. CVD hingegen eignet sich hervorragend für Anwendungen, die konforme Beschichtungen erfordern, wie z. B. integrierte Schaltkreise, verschleißfeste Beschichtungen und Gassensoren. Beide Techniken sind in der modernen Fertigung unverzichtbar und bieten je nach Anwendung einzigartige Vorteile.
Wichtige Punkte erklärt:
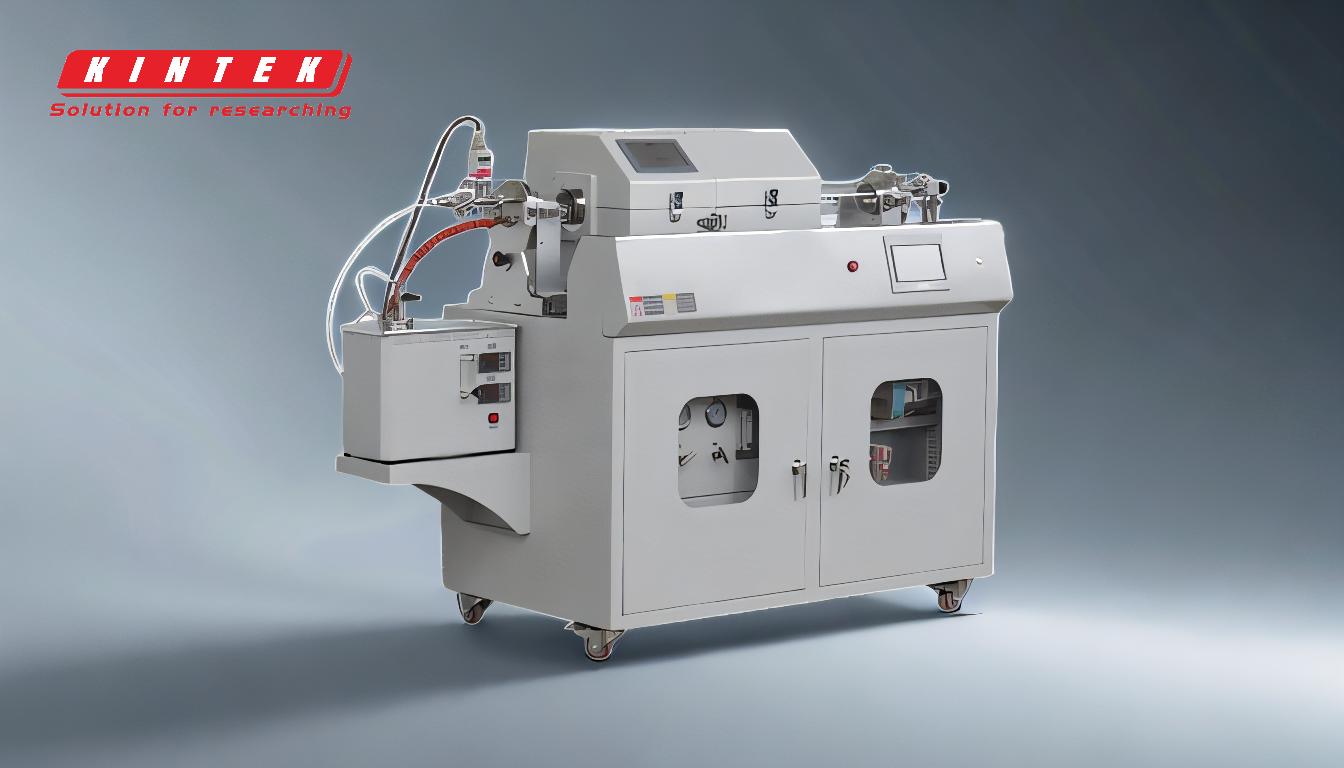
-
Definition und Prozess von PVD und CVD:
- PVD: Dabei wird ein festes Material in einer Vakuumumgebung verdampft und auf einem Substrat abgeschieden. Dieses Verfahren wird typischerweise zur Herstellung dünner Filme verwendet, die Eigenschaften wie Reflexionsvermögen, Härte oder Korrosionsbeständigkeit verbessern.
- CVD: Dabei wird ein gasförmiger Vorläufer erhitzt, der dann auf einem Substrat reagiert und kondensiert, um einen dünnen Film zu bilden. Diese Methode eignet sich ideal zum Aufbringen von Schutzbeschichtungen auf komplexe Geometrien oder unregelmäßige Oberflächen.
-
Beispiele für PVD-Anwendungen:
- Elektronik: Wird für Aluminiumschienen und Keramikwiderstände in elektronischen Schaltkreisen verwendet.
- Optik: Antireflex-Keramikbeschichtungen für Linsen und Spiegel.
- Automobil: Korrosionsbeständige Beschichtungen für Gasturbinenschaufeln und verschleißfeste Beschichtungen für mechanische Werkzeuge.
- Mode und Einrichtungsgegenstände: Dekorative Beschichtungen auf Schmuck, Wasserhähnen und Utensilien.
-
Beispiele für CVD-Anwendungen:
- Integrierte Schaltkreise: Wird zur Abscheidung dünner Schichten in der Halbleiterfertigung verwendet.
- Verschleißfeste Beschichtungen: Wird auf Werkzeuge und Maschinen angewendet, um die Haltbarkeit zu verbessern.
- Gaserkennung: Dünne Filme, die in Sensoren zur Erkennung bestimmter Gase verwendet werden.
- Photovoltaikgeräte: Beschichtungen für Solarmodule zur Effizienzsteigerung.
-
Vorteile von CVD gegenüber PVD:
- Betrieb mit höherem Druck: CVD arbeitet bei höheren Drücken, sodass keine teuren Hochvakuumpumpen erforderlich sind.
- Schutzbeschichtungen: CVD kann aufgrund seiner laminaren Strömungseigenschaften gleichmäßige Filme auf unregelmäßigen Oberflächen oder dicht gepackten Substraten abscheiden.
- Kosteneffizienz: Reduzierte Infrastrukturkosten, wenn kein Management giftiger Gase erforderlich ist.
-
Arten von CVD-Geräten:
- Atmosphärendruck-CVD (APCVD): Arbeitet bei atmosphärischem Druck und eignet sich für die Produktion in großem Maßstab.
- Niederdruck-CVD (LPCVD): Arbeitet bei reduziertem Druck und sorgt so für eine bessere Gleichmäßigkeit des Films.
- Plasmaverstärktes CVD (PECVD): Verwendet Plasma, um chemische Reaktionen zu verstärken und so niedrigere Abscheidungstemperaturen zu ermöglichen.
-
Vergleich von PVD und CVD:
- PVD: Besser für Anwendungen, die hochreine Filme und Sichtlinienabscheidung erfordern.
- CVD: Hervorragend geeignet für Schutzbeschichtungen und Anwendungen mit komplexen Geometrien.
Durch das Verständnis der unterschiedlichen Prozesse, Anwendungen und Vorteile von PVD und CVD können Hersteller die geeignete Technik basierend auf ihren spezifischen Anforderungen auswählen, sei es zur Erhöhung der Haltbarkeit, zur Verbesserung des Reflexionsvermögens oder zur Erzielung einer präzisen Dünnschichtabscheidung.
Übersichtstabelle:
Aspekt | PVD | CVD |
---|---|---|
Verfahren | Verdampft festes Material im Vakuum und lagert es auf einem Substrat ab. | Verwendet chemische Reaktionen gasförmiger Vorläufer, um einen dünnen Film zu bilden. |
Anwendungen | Elektronik, Optik, Automobil, Mode und Heimtextilien. | Integrierte Schaltkreise, verschleißfeste Beschichtungen, Gassensorik, Solarmodule. |
Vorteile | Hochreine Filme, Sichtlinienabscheidung. | Schutzbeschichtungen, gleichmäßige Filme auf komplexen Geometrien, Kosteneffizienz. |
Beispielanwendungen | Aluminiumschienen, Antireflexbeschichtungen, dekorative Schmuckbeschichtungen. | Halbleiterfertigung, Gassensoren, Photovoltaikgeräte. |
Benötigen Sie Hilfe bei der Auswahl zwischen PVD und CVD für Ihre Anwendung? Kontaktieren Sie noch heute unsere Experten für maßgeschneiderte Lösungen!