Verdampfen und Sputtern sind beides physikalische Aufdampfverfahren (PVD), die zur Herstellung dünner Schichten verwendet werden, sich aber in ihren Mechanismen, Betriebsbedingungen und Ergebnissen erheblich unterscheiden.Beim Verdampfen wird ein Material erhitzt, bis es verdampft und einen Dampfstrom bildet, der auf einem Substrat kondensiert.Im Gegensatz dazu werden beim Sputtern energiereiche Ionen verwendet, die mit einem Zielmaterial kollidieren und Atome ausstoßen, die sich auf einem Substrat ablagern.Das Sputtern arbeitet mit höheren Gasdrücken und bietet eine bessere Schichthaftung und Homogenität, während das Verdampfen höhere Abscheidungsraten bietet und sich besser für Hochtemperaturmaterialien eignet.Nachfolgend werden die wichtigsten Unterschiede im Detail erläutert.
Die wichtigsten Punkte werden erklärt:
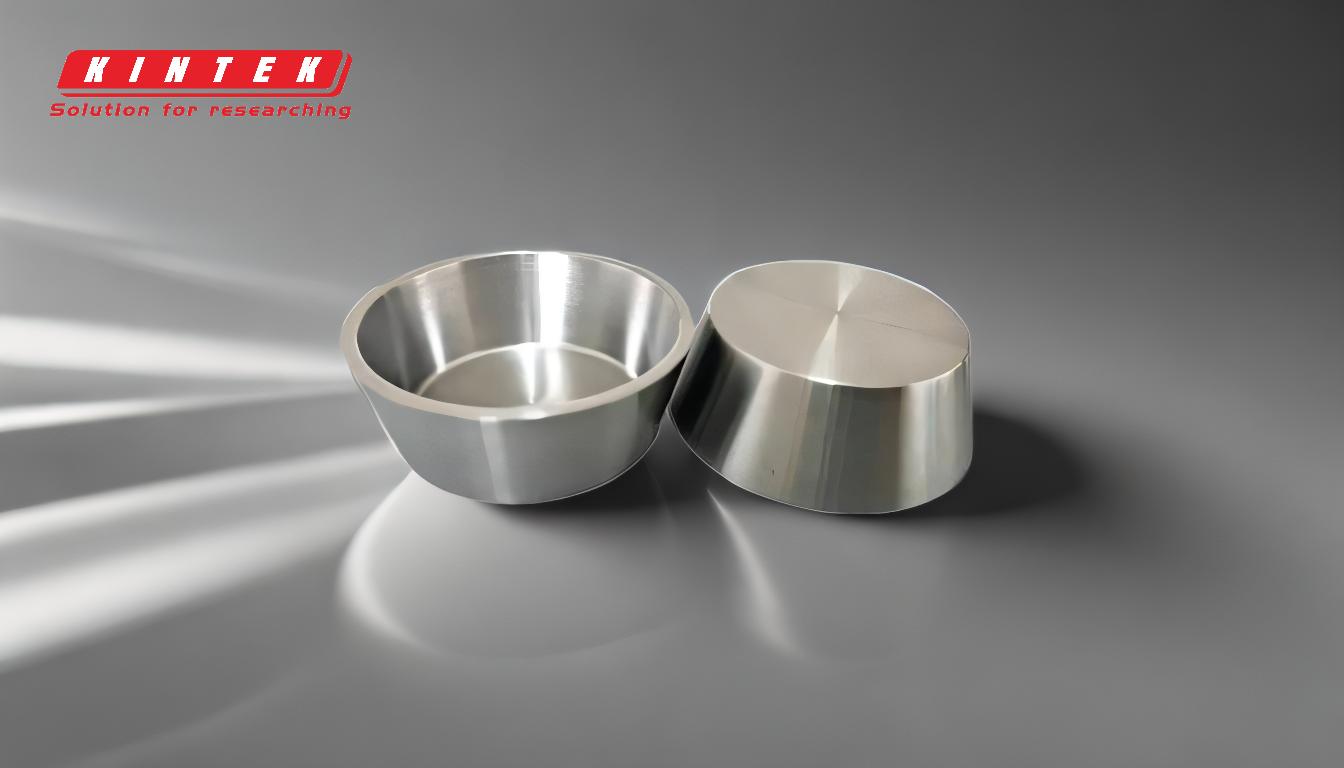
1. Mechanismus der Ablagerung
-
Verdampfung:
- Nutzt thermische Energie zur Verdampfung des Ausgangsmaterials.
- Das Material wird erhitzt (z. B. durch Widerstandsheizung oder Elektronenstrahl), bis es seine Verdampfungstemperatur erreicht, wodurch ein Dampfstrom entsteht.
- Der Dampf kondensiert auf dem Substrat und bildet eine dünne Schicht.
-
Sputtern:
- Beschuss eines Zielmaterials mit energiereichen Ionen (in der Regel Argon-Ionen) in einer Plasmaumgebung.
- Durch die Kollision werden Atome oder Cluster aus dem Target herausgeschleudert, die sich dann auf dem Substrat ablagern.
- Dieser Prozess ist nicht thermisch und beruht eher auf Impulsübertragung als auf Wärme.
2. Betriebliche Bedingungen
-
Verdampfung:
- Erfordert eine Hochvakuumumgebung (sehr niedriger Druck), um Zusammenstöße zwischen den Gasphasen zu minimieren und eine direkte Flugbahn für den Dampf zu gewährleisten.
- Geeignet für Materialien mit hohen Verdampfungstemperaturen.
-
Sputtern:
- Bei höherem Gasdruck (5-15 mTorr) werden die gesputterten Partikel in der Gasphase zusammengestoßen, bevor sie das Substrat erreichen.
- Die Anwesenheit von Gas trägt zur Thermisierung der Partikel bei, was zu einer besseren Schichtqualität führt.
3. Ablagerungsrate
-
Verdampfung:
- Aufgrund des robusten Dampfstroms, der durch die thermische Verdampfung erzeugt wird, ist die Abscheiderate in der Regel höher.
- Kürzere Laufzeiten machen es für bestimmte Anwendungen effizienter.
-
Sputtern:
- Hat im Allgemeinen eine geringere Abscheidungsrate, außer bei reinen Metallen.
- Das Verfahren ist langsamer, weil es einzelne Atome oder kleine Cluster auf einmal ausstößt.
4. Filmqualität und Eigenschaften
-
Verdunstung:
- Erzeugt Filme mit größerer Korngröße und geringerer Homogenität.
- Aufgrund des fehlenden energetischen Partikelbeschusses können die Schichten eine geringere Haftung aufweisen.
-
Sputtern:
- Das Ergebnis sind Schichten mit kleinerer Korngröße, besserer Homogenität und höherer Haftung.
- Die energetische Beschaffenheit der gesputterten Partikel verbessert die Filmdichte und Haftung.
5. Energie der abgelagerten Spezies
-
Verdampfung:
- Die verdampften Partikel haben eine geringe Energie, was zu weniger dichten Filmen führt.
- Dies kann zu einem höheren Anteil an absorbiertem Gas in der Schicht führen.
-
Sputtern:
- Die gesputterten Partikel haben eine höhere Energie, was zu dichteren Schichten mit weniger Defekten führt.
- Die höhere Energie verringert auch die Menge des absorbierten Gases in der Schicht.
6. Skalierbarkeit und Automatisierung
-
Verdampfung:
- Weniger skalierbar für großflächige Beschichtungen aufgrund des Sichtliniencharakters des Prozesses.
- Begrenzte Automatisierungsmöglichkeiten im Vergleich zum Sputtern.
-
Sputtern:
- Hochgradig skalierbar und automatisierbar für die Großserienproduktion.
- Geeignet für die Beschichtung komplexer Geometrien, da das Verfahren nicht auf der Sichtlinie verläuft.
7. Materialverträglichkeit
-
Verdunstung:
- Ideal für Hochtemperaturwerkstoffe, die einer thermischen Verdampfung standhalten können.
- Es können Legierungen durch gemeinsames Verdampfen mehrerer Materialien hergestellt werden.
-
Sputtern:
- Kompatibel mit einer breiten Palette von Materialien, einschließlich Metallen, Legierungen und Keramik.
- Durch sequenzielles Sputtern können mehrlagige Beschichtungen erzeugt werden.
8. Anwendungen
-
Verdampfung:
- Wird häufig bei Anwendungen eingesetzt, die hohe Abscheidungsraten erfordern, z. B. bei optischen Beschichtungen und Metallisierung.
-
Sputtern:
- Bevorzugt für Anwendungen, die hochwertige, dichte Schichten erfordern, wie z. B. die Halbleiterherstellung und Schutzbeschichtungen.
Zusammenfassend lässt sich sagen, dass Verdampfung und Sputtern unterschiedliche PVD-Verfahren mit einzigartigen Vorteilen und Einschränkungen sind.Die Verdampfung zeichnet sich durch hohe Abscheidungsraten und Einfachheit aus und eignet sich daher für bestimmte Hochtemperaturanwendungen.Das Sputtern hingegen bietet eine überlegene Schichtqualität, Skalierbarkeit und Vielseitigkeit und ist damit ideal für fortschrittliche industrielle Anwendungen.Die Wahl zwischen den beiden Verfahren hängt von den spezifischen Anforderungen des Beschichtungsprozesses ab, einschließlich Materialeigenschaften, Schichtqualität und Produktionsmaßstab.
Zusammenfassende Tabelle:
Blickwinkel | Verdampfung | Sputtern |
---|---|---|
Mechanismus | Thermische Energie lässt das Material verdampfen. | Energetische Ionen beschießen das Ziel und stoßen Atome aus. |
Betriebsbedingungen | Hochvakuumumgebung, geeignet für Hochtemperaturmaterialien. | Höhere Gasdrücke (5-15 mTorr), bessere Schichtqualität. |
Abscheiderate | Höhere Abscheidungsraten, kürzere Laufzeiten. | Geringere Abscheideraten, außer bei reinen Metallen. |
Filmqualität | Größere Korngrößen, weniger Homogenität, geringere Haftung. | Kleinere Korngrößen, bessere Homogenität, höhere Adhäsion. |
Energie der abgeschiedenen Spezies | Niederenergetische Teilchen, weniger dichte Schichten. | Hochenergetische Teilchen, dichtere Schichten mit weniger Defekten. |
Skalierbarkeit | Weniger skalierbar, begrenzte Automatisierung. | Hochgradig skalierbar, geeignet für große und komplexe Geometrien. |
Material-Kompatibilität | Ideal für Hochtemperaturwerkstoffe und die Herstellung von Legierungen. | Kompatibel mit Metallen, Legierungen, Keramiken und mehrschichtigen Beschichtungen. |
Anwendungen | Optische Beschichtungen, Metallisierung. | Halbleiterherstellung, Schutzbeschichtungen. |
Benötigen Sie Hilfe bei der Auswahl des richtigen PVD-Verfahrens für Ihr Projekt? Kontaktieren Sie noch heute unsere Experten für eine persönliche Beratung!